Today’s post covers 3D design services and how to design prototypes for inventors and companies. It is important to evaluate whether there is enough demand and whether you’re reaching for the right customers when reassessing the potential of your products. Does your product resolve problems or at least provide answers to real questions? Are your products intentionally aligned with the audience that you have in mind? These are the questions you should first address in order to make sure that your design and products resonate with the market.
Understanding both demand and target audience helps increase your chances of success. But inventors who make it big take things a little bit further. They know and understand that actual feedback about the product is more essential than the insights you can get from simply researching about your market alone. They’ve realized that they need to do so much more and go above and beyond to get these questions answered correctly.
This is where prototyping becomes your indispensable best friend. Prototype design experts design a shrunk, tangible version of your products that lets your customers hold in their hands. Prototypes give you the flexibility to add tweaks and updates and materialize them without the full cost breaking your bank.
Table of contents
RELATED: What is industrial design prototyping, and what are the main prototypes used by companies?
More about prototypes
Prototypes are your designs after drinking the shrinking potion from Alice in Wonderland. It can be shrunk version, but still incorporated with all the details and even the functionalities that the actual product is expected to embody. Prototypes can also be in the form of either low-quality or high-quality sketches. The “personalities” engraved in these prototypes help stakeholders get a better glimpse and understanding of your final products.
Types of prototyping
Prototyping has two major types: high-fidelity and low-fidelity prototyping.
High-fidelity prototyping has the same exact external appearance and function as the actual product is intended to possess. This type of working model is worked on by product teams when the designers know what exactly they want to build. This prototype covers the user interface or UI of the product like the visuals, aesthetics, and UX or user experiences. It is also usually incorporated along with the user flow and behavior and caters to interactions between the products and your clients.
The primary purpose when it comes to low-fidelity prototyping is to check and test the functionality of a product rather than its visual appearance and aesthetic. It is a cost-saving, fast, and easy method of turning high-level design concepts into tangible items that serve as a representation of the future product. While the process allows a quick overview of the product, it doesn’t allow the user to perform any testing.
RELATED: Different kinds of prototypes and how to use them for your design project
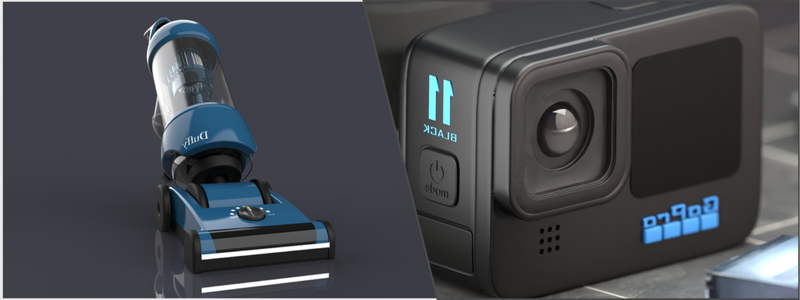
Examples of prototyping
The following are some of the most widely used examples of prototyping in the market:
Rapid models and 3D printing
Rapid models and 3D printing services allow designers to come up with a realistic and functional product model using advanced and high-tech computers and printing machines. It is a prototype that lets businesses switch from the design to the production stage faster because the 3D models can help them pinpoint specific areas that need adjustments and identify flaws. It also takes just a few minutes to adjust those little digital changes to a 3D-printed model.
Sketches and diagrams
Sketches and diagrams are two of the most basic examples of prototyping because they require the least effort and don’t even need any artistic or drawing skills. It starts with the use of sketches to conceptualize and develop a new product. The interface of the product can be drawn on paper together with the front-end design of the product or application. This paper prototype is useful in the conceptualization and design of a new application or product.
Feasibility prototypes
3D designers or businesses may add and use feasibility working models to test specific features that they can add later on in the process of product development. After the initial prototype is developed, the designer can implement changes to the design. Feasibility prototypes can be used for digital and physical models alike. Designers can also use these prototypes for testing and adopting a new idea if they wish to add a critical website or product feature.
RELATED: Freelance rapid prototyping costs, pricing, and rates for companies and inventors
Horizontal prototypes
Horizontal prototypes are used by companies to understand a project’s human interface. This prototype shows screens, windows, and menus on a computer to determine how users interact with a website or product. A horizontal prototype also shows the user interface of the product and offers a broader view of it as a whole.
Role-playing prototypes
Experiential or role-playing prototypes are simulation techniques that help improve the user experience of a service or a product. Some designs can take advantage of visualization techniques such as augmented or virtual reality. For example, when testing the first design of a new theme park or circus, the users can walk through the area with the help of augmented and virtual reality.
Storyboards
Storyboards are excellent ways to tell stories and guide customers through seamless user experiences. These are interactive and iterative design methods that use a series of pictures, sketches, and drawings to show the solution to a problem or concern of a user. Drawing the user’s experience helps them understand their issues better. Designers can also use storyboards during the initial stage of prototyping to gather feedback during the early steps in the design process.
RELATED: 10 Tips on how to find the best prototype engineering firm services
Vertical prototypes
Vertical prototypes are technical prototypes designed by prototype design engineers that add details regarding the functions of a particular business process. A vertical prototype expands on some elements of the horizontal prototype and explains the inner functions of the sub-systems in the overall interface. Vertical prototypes are used by companies in the later stages of the design process to elaborate on specific functions or features of a website or product. Vertical prototypes also test essential tasks of an application or software before they proceed to the subsequent design process.
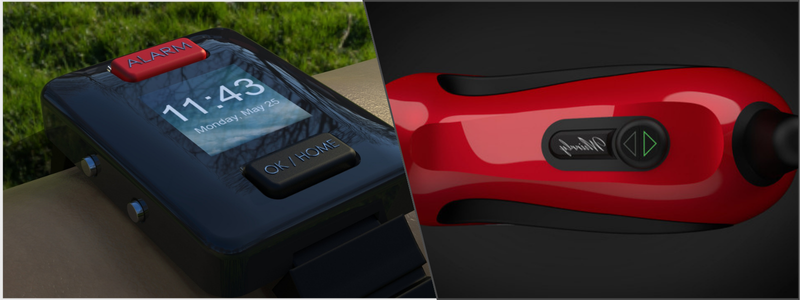
Video prototypes
Businesses use video prototypes to present products in graphic simulations or animated videos that explain a project’s concept. Video prototyping shows speculative and new ideas, products, and designs to prospective customers. Presenting a view gives a good idea of how customers might perceive concepts that might have been otherwise challenging to prototype because of limited resources.
Wireframes
Wireframes serve as the digital diagram or layout of a product. These can be used to produce prototypes of digital tools, software, and websites. A wireframe is a flowchart of a website or software that presents all website pages or software applications and their interconnection with each other. This gives designers and developers a general idea of the appearance of a website and helps them understand its core functionalities. Anyone can use wireframes, from developers to copywriters, to navigate the placement and structure of different content.
RELATED: Key differences between prototyping and prototype engineering for companies & firms
Benefits of designing prototypes
Prototypes are now considered valuable tools in the manufacturing industry for many good reasons. The following are some of the critical benefits of designing prototypes:
Design validation
A prototype provides a tangible demonstration of the functionality and design of the final product. Rapid prototype services allow clients to assess the aesthetics, user experience, and ergonomics of the prototype. This will then help them reach better decisions when it comes to possible improvements or changes to the design.
Feasibility testing
Prototyping allows investors and businesses to test the feasibility of the product concepts and ideas they have in mind. They can determine potential issues in the design, feasibility concerns, and technical problems early on in the development phase. This results in lower costs and saves more time than is required for retooling and redesigning.
Intellectual property protection
Designing a prototype offers a proof of concept or POC development. It can also prove ownership of an intellectual property. This can be very valuable when it comes to the protection of your innovations and ideas.
RELATED: Understanding trademark law: intellectual property tips for inventors
Seamless communication between investors and stakeholders
Prototypes are vital as they help communicate and demonstrate the concept of the product to potential stakeholders, clients, and investors. A functional prototype can increase interest, enhance credibility, and even help secure more partnerships or funding for the future production and development of the product.
Iterative improvement
Designing a prototype also makes way for fine-tuning and iterative enhancements of the product according to testing and user feedback. The iterative approach also guarantees the market suitability of the final product for its target audience.
Presales and marketing
A fully functional and visually appealing prototype can also be used for activities related to presales and marketing. The sales team and marketers can use and present something tangible that will help secure pre-orders, spike interest, and attract more prospective customers.
RELATED: 6 Ways you can use 3D Printing services to create a new prototype design
Market testing
Using prototype design experts allows businesses to perform market testing and acquire valuable feedback from future customers. The input can then be used to improve the product further and ensure that it aligns with the preferences and demands of the target market.
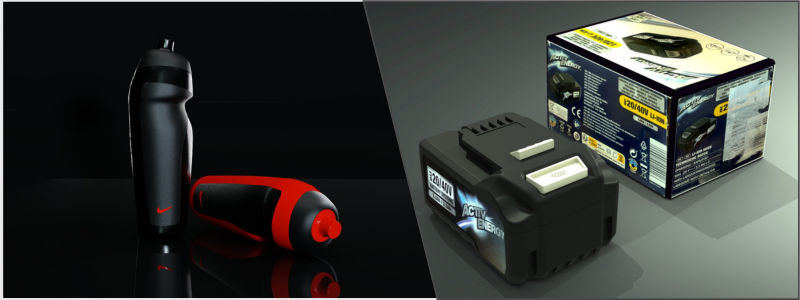
Reduced risk
The validation of the design and functionality of the product through prototyping can help businesses cut down the risks often linked with full-scale manufacturing. The identification of problems and addressing them accordingly in the prototype phase reduces the possibility of costly setbacks and errors in mass production.
Streamlined collaboration
Prototypes can make way for streamlined collaboration among the different teams with different functions, including the designers, manufacturers, and engineers. The product’s physical representation can lead to better alignment and communication during the development phase.
Cost and time savings
Prototyping makes it easier for DFMA companies to carry out quick modifications and iterations, which can lower the costs and time involved in the development process. The ability to identify room for improvement or flaws in the existing design early on in the process can help prevent costly tooling changes or rework later on in the production. This optimizes the timelines and overall costs of the project.
RELATED: How to design the best prototype for your new product
Tips for prototype creation and usage
Below are some helpful tips for developing and using prototypes:
- Build the prototype with team members right from the start. Team members can pinpoint room for improvement and then work together to find a solution.
- During the development of a prototype, pay attention to solving flaws and move back to the earlier design if a design error is found. The existing one can either be changed, or a new prototype can be made without any problems.
- Prototypes can help ensure a design’s safety. For digital products, this means protecting the business and customers from cybercriminals and hackers.
- It is critical to promote and endorse the usability of your product when developing a prototype and considering the product’s primary purpose. You should come up with a working model that presents the inspiration that sparked the design.
- Never build a flawless working model, as it might delay the actual product’s development. Focus instead of making a prototype of what you need and what is necessary.
RELATED: Advantages of using rapid prototyping services for your business
How Cad Crowd can help
Cad Crowd connects you with the best prototype design services that can help your company or firm design the best prototypes for your new concept.