Methodologies that will allow you to cut costs and optimize your current processes are truly godsend lifesavers, especially in this fast-paced and dynamic manufacturing landscape. This is where Design for Assembly, or simply DFA, comes in and truly enhances the processes in place.
DFA represents a significant change in how companies approach and apply modifications in the process of creating products, from the drawing board to the assembly line. By applying different methods to implement assembly practicalities and design insights, DFA brings about a bunch of benefits to improve both your manufacturing process and final products.
Table of contents
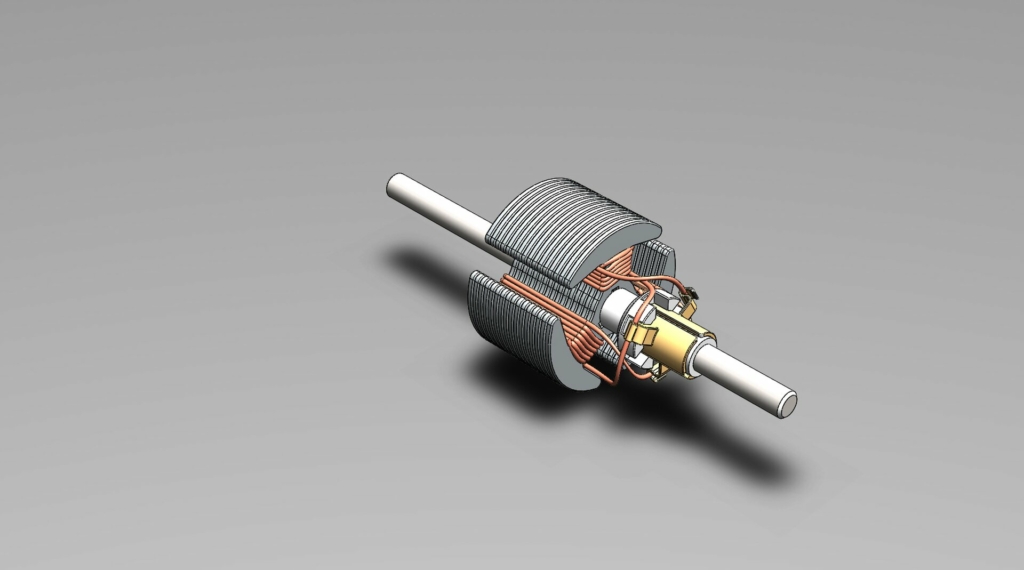
RELATED: How to design effective assembly drawings for consumer products and manufacturing companies
What is design for assembly?
Design for assembly, or DFA, is an engineering approach that simplifies product design to make the assembly process faster, easier, and more affordable. Its main objective is to reduce the complexity of the assembly process, minimize operation errors, and ensure an accurate and error-free assembly process.
Primary DFA principles
Design for assembly principles are founded on the objective of creating an error-free, cost-effective, and efficient assembly process. The following is a comprehensive breakdown of these DFA principles.
- Design for ease of access
The main objective of this principle is to ensure easy access to the parts and a seamless assembly of the components. It reduces the risk of errors that may be due to restricted visibility or access to each part and overall view of the whole mechanism. It also minimizes potential damage to adjacent parts during the assembly and thrives on eliminating the need for specialized equipment to have a more customer or client-friendly end product.
- Define multifunctional parts
Having parts that can serve more than one purpose incredibly enhances even the tiniest aspects and details of your product. Reduced parts can also minimize the size and weight, for example, which can be beneficial for products or projects in industries such as automotive or aerospace, where both factors greatly impact performance. It reduces the number of parts and saves money by removing the need for many specialized parts.
- Guarantee self-locating parts
The objective is to design parts so that they can all fit together in a single orientation, making the assembly process intuitive. This minimizes the possibility of wrong assembly, which may result in product failures or faults. It also decreases the need for complex fixtures or jigs. Because of the intuitive fitting of parts together, it can also streamline the training process for the assembly workers.
- Aid self-fastening
This principle aims to design parts whenever possible that can be joined together without using additional tools, adhesives, or fasteners. Techniques such as interlocking designs and snap-fits are often used.
This eliminates the cost and time often associated with securing and inserting different fasteners. It also lessens the risk of missing or loose fasteners, which helps enhance the product’s reliability. This can also simplify disassembly for recycling or repair.
- Minimize handling
The purpose is to make parts easy to place, pick up, and orient during assembly. This decreases the odds of damage or errors caused by improper or excessive handling. It also improves the efficiency of the automated assembly process while reducing effort and time.
- Trim down the number of parts
The main concept here is to minimize the number of different parts in the product. A reduced number of parts can lead to several key benefits:
- Faster assembly times because of fewer parts to handle and join
- Lesser potential points of faults or failure to improve product reliability
- Reduced manufacturing costs because of the lesser need for processing and materials
- Simplified process of procurement and inventory
- Standardized parts
The aim here is to ensure standardization of parts across multiple product ranges or products. It helps achieve economies of scale in the production of parts. It makes production more flexible because standard parts can cater to different product lines. It simplifies inventory management as it reduces the variety of parts that should be stocked.

Benefits of design for assembly in product manufacturing
There is more to DFA than being a mere set of guidelines. This philosophy profoundly impacts the conceptualization, design, and assembly of products. Proper integration of DFA can offer numerous benefits both to the actual process of manufacturing and the finished product.
Cost savings
There are several areas where DFA can help save on costs during product manufacturing:
- Inventory management
Fewer distinct parts mean more streamlined management of inventory, resulting in reduced warehousing and holding costs.
- Labor costs
Simplified assembly procedures will result in fewer man-hours required for assembly. Decreased assembly errors can also reduce wastage and rework.
- Material costs
DFA can dramatically reduce the required raw materials by reducing the number of parts and using multifunctional parts.
Eco-friendly manufacturing
- Simplified disassembly for recycling
Products made using DFA principles are usually easier to disassemble at the end of their lifecycle, which facilitates component reuse or recycling.
- Efficient resource use
Fewer resources such as auxiliary materials or energy are used up during the production process when the design for ease of assembly is optimized.
- Reduced waste
Lesser quantities of components and reduced assembly errors may result in reduced wastage in terms of defective products or raw materials.
Improved customer satisfaction
- Cost benefits
The savings made possible by DFA usually allow manufacturers to provide competitive pricing that translates to value for money for consumers.
- Topnotch products
The benefit for end users of the product is not just a premium look and feel, as it also boasts excellent reliability.
Enhanced reliability and quality of products
- Better finish and fit
Parts designed with assembly in mind often have a more seamless fit, resulting in a refined appearance for the final product.
- Lesser failure points
A product with fewer parts naturally has fewer potential failure points, making it more reliable.
- Reduced errors in assembly
Since parts are designed for intuitive and easy assembly, the chances of errors during the assembly process are reduced.
RELATED: Key differences between prototyping and prototype engineering for companies & firms
Faster time-to-market
- Efficient assembly
A faster assembly process means a shorter timeframe for manufacturing products ready for the market.
- Less rework
Decreased assembly errors will result in fewer units sent back for corrections, which can speed up the overall production timeline.
Enhanced training and worker morale
- Ease of assembly
Workers will experience less frustration and a better sense of achievement when products are easier to assemble.
- Streamlined training
Temporary or new staff members can be quickly onboarded because the intuitive design can simplify the learning curve.
Increased productive flexibility
- Modular design
Most principles of DFA lean towards a modular design to allow easy variations or upgrades of products without the need to revamp the entire assembly process.
- Scalability
With the changing market demands, manufacturers can easily scale production down or up with the help of efficient assembly and standardized parts.
Modern manufacturing and DFA
Modern manufacturing is characterized by shrinking product lifecycles, a pressing need for sustainable practices, and rapid innovation. DFA has emerged as a key strategy to guide the product manufacturing and design processes amidst all these dynamics.
Here are the different ways that DFA can integrate and interact with the landscape of modern manufacturing:
- Adaptability to changes in the market
Integrating DFA principles with modern methods such as 3D printing and 3D modeling solutions can pave the way for quick prototyping. Rapid iteration can speed up product development and ensure timely entry into the market.
Alignment with Industry 4.0
In today’s Big Data era, DFA allows manufacturers to acquire insights from the assembly data that help optimize the design for predictive maintenance and better assembly outcomes.
Smart integration
With the rise of Industry 4.0, the world of manufacturing is becoming increasingly interwoven with different digital technologies. DFA can complement this trend by streamlining assembly processes, making them more conducive to robotic assembly and automation.
Eco-conscious manufacturing
- Facilitated recycling
Since it’s easier to disassemble products designed using DFA principles, they can support the circular economy model by allowing effective components to be reused and recycled.
- Sustainable practices
Today’s consumers have become more eco-conscious than ever, prompting manufacturers to switch to more sustainable practices. Since DFA focuses on the efficient use of resources and reduced wastage, it perfectly aligns with mandates on green manufacturing.
- Improved consumer experience
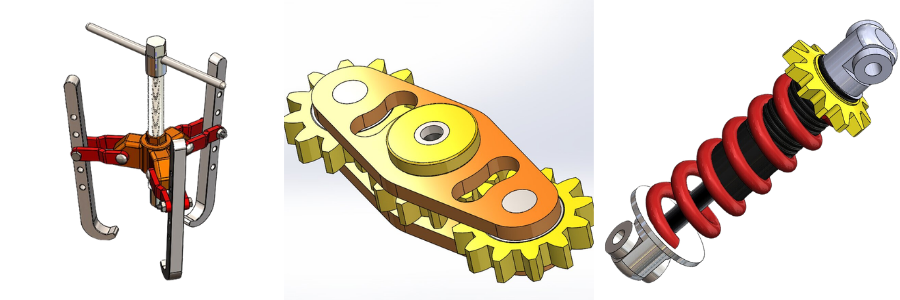
RELATED: 4 tips to improve cabinet shop drawings for manufacturing efficiency at companies
The Bottom Line
Seeing DFA as just a cost-cutting tool will only undercut its holistic effects on the manufacturing landscape. This reshapes the mindset on design, fosters a balanced relationship between manufacturers and designers, and guarantees a stand-out end product in terms of performance and quality.
With more and more industries dealing with challenges such as rapid technological advancements, sustainability concerns, and changing consumer needs, taking advantage of DFA principles offers a more proactive approach to dealing with these challenges.
How Cad Crowd can help
Embracing design-for-assemblement services for product manufacturing is no longer a mere strategic move; it is a key investment in quality manufacturing in the future. Cad Crowd will connect you with the best services that can turn your products into reality.