Not all 3D models are created equal. Some never seem to lose quality even when compressed or changed in other ways, while others end up looking distorted after just a few changes. The quality of a 3D modeling service greatly determines whether this will happen and how bad the distortions will be if they do occur. There are a lot of reasons why this can happen. Distortions can occur due to openings in the mesh, multi-stacked polygons, or other errors. The wrong measurements can also play a big part. If the measurements are inaccurate, it can make the model look strange even if the mesh is otherwise correct.
If the model is usable after these changes, it will require post-processing to make it look right for the intended user. This can eat up a lot more time than simply improving the model’s quality, especially if the model is low quality. Unfortunately, measuring the quality of a 3D model is not as easy as simply looking it over. To truly evaluate the quality of a 3D model, you need to treat a model’s evaluation as a process.
By checking your model in as many ways as possible, you can get a good measure of whether it is a high-quality model or will need some work before it can be better. Many great tools and 3D design services are out there to help you during this process, and a little knowledge can also be useful here. Let’s start by looking at why you might need a model and how that impacts the rest of the creation process.
Table of Contents
What will the model be used for?
Before any evaluation can begin, an excellent question to consider is what the model will be used for. What makes a 3D model high quality depends on what the product will be used for. If the 3D model is for a video game, high poly count and a believable figure matter most. Animation, however, requires an accurate bone structure and realistic joint movement.
Even if the texture, color, and size are accurate, if a model moves oddly during the animation process, it will reduce the model’s quality. These details are essential, but what matters most changes entirely for the manufacturing industry. There, visual details on the model are less important than showing how to build the product as perfect as possible.
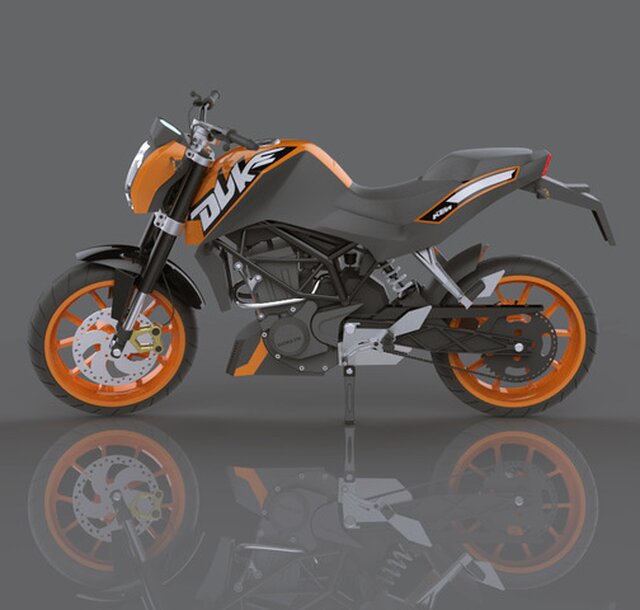
No matter what you’re modeling, however, the end goal is realism. While what point makes the model most believable changes depending on what the model is to be used for, realism is a good measure for quality. If a manufacturing service can see precisely where screws need to go in a model and can use it as a reference point for creating the real product, the model can be considered a success. On the other hand, even if a cute squirrel or other characters in a game are anatomically correct, this model wouldn’t be considered successful if they move oddly.
Perform a laser scan
A laser scan is a great way to compare your render to the original. Laser scans throw out beams of light to accurately measure objects without damaging them. Laser scanning can create a digital copy of a building or other object and can be used to compare your model to a physical object to check for accuracy. A laser scan can give you a picture-perfect understanding of how the model’s actual structure should look. Photo references can help guide you from there by showing what textures and colors are needed to make the model look as realistic as possible.
Take measurements
If you’re not able to do a laser scan, taking measurements yourself can help you get a rough idea of how close you are to accuracy. This is not as good as a laser scan, but it can help give you reference points to see how your mesh model holds up to the original item you’re trying to recreate. When other data is not available, getting as much information as possible through measurements or photo references can still help you make an accurate model. The less information you have about the original, the harder it is to recreate accurately, but it is still possible to improve this way.
Take advantage of STL checks and other tools
Many types of 3D modeling software already have methods to check for quality in the program itself. 3ds Max, for example, has an STL checker that helps spot problems in the model. This tool is mainly designed to check and see if problems will occur when the model is changed or rendered, but it’s still a valuable way to check for potential problems that could lower the project’s value.
STL checks are important because they focus on major problems that might prevent the model from being 3D printed or used in other ways. 3D printing often uses mesh conversion to change a model from perfect geometry with round curves into triangles and vertices. This process is surprisingly complex and a little like smashing a vase and then reassembling it. If the model is not made correctly, the result can be several errors that make it impossible to print the model.
Luckily, an STL checker can help find these problems and solve them. Most STL checkers have an auto-repair that handles as many fixes as possible and alert you to the issues that the checker can’t solve. The STL checker mainly looks for problems such as multiple-stacked polygons and open edges, so you will need to use something else to check the model’s quality.
Use software to help
Laser scans give you a clear look at how the 3D model should appear, but small details may be overlooked when recreating it with your own model. There are lots of different programs available to help you in these situations. Programs like Geomagic’s 3D take your data and compare it against the references from laser scans. They can then tell you if minor details or even significant flaws are different from the scans.
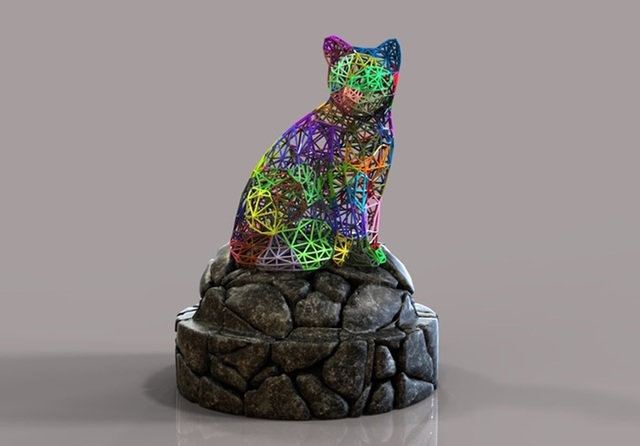
This can help you avoid embarrassing mistakes in buildings such as too many or too few windows or help you notice other details you might have missed during the creation process. It also gives you basic statistical data, so you have a good idea of what to change to make your model as accurate as possible.It is exceedingly difficult to get everything right through visual examination alone.
We tend to skim over details when making a quick comparison, making it easy to miss changes that need to be made. Software can help you in the process of making your model as accurate as possible. There are several different types of software available, so if you find one difficult to use, don’t be afraid to try another. Having software on hand can help you improve the quality of a model quickly and easily, so you don’t have to waste time visually examining the model for problems.
How Do You Know If Your Model Is High Quality?
While all these tools will help you improve the model’s quality, the question remains: what makes a model high quality? In general, you know your model is of good quality when it is as accurate and has as few errors as possible. A model that does not have any holes in the mesh, is as close as possible to the same measurements as the real object being recreated, and moves in a realistic function are signs that a model is high quality. On the other hand, if the STL checker finds many errors, it distorts badly when changes are made, or does not fit the measurements closely, these are signs it is a low-quality model.
RELATED: 3D Modeling Techniques Used in Video Games
No matter what you are creating, striving for the highest quality model every time is a good practice to keep. You never know when an old model will be needed, and having suitable bases in your library that do not need a lot of post-processing can save a lot of effort over time. 3D models frequently need to have changes made to them for future work. This may be an upgrade on an old model phone or a new outfit on a game character. Even small changes to a 3D model that isn’t well designed can create noticeable distortions.
By taking care to make sure that the model is as high quality as possible in the beginning, you can cut down on how much post-processing the model will need and how hard you must work to make the changes you need. It is worth the extra effort to take measurements, look for errors, and make any new model as strong as possible.
Cad Crowd’s 3D Modeling Experts at Your Disposal
At Cad Crowd, we have the privilege of working with a network of 3D modeling professionals who can help with any project. Whether you need a model made of a house or a product, let us help. Get a free quote today.