There are approximately 254,000 manufacturing companies in the United States alone. They range from minuscule, small-batch manufacturing operations to titans of industry like GE and Northrop Grumman, and these are only the ones in America. The number of products they manufacture on a daily basis is staggering, both in overall sheer volume and differentiation. These manufacturing companies form one of the earliest links in an integral chain of businesses around the world.
The products these companies spit out are used in other industries—some of them manufacturing, some service, and some straight to consumers. At the heart of it is a manufacturing company producing a unique part that will eventually lead to a finished good. Without all of this, the economy would come to a screeching halt because even freelance engineering design service need their phones and computers. Telecommunications giants need cabling and microprocessors to transmit data and set up their infrastructure.
Working at the very front end of this process is a manufacturing engineer service. This individual will work alongside designers to sculpt the mold for their product before ever sending it through the processing plant. Without this key cog in the process, parts would be clunky, inefficient, and take time to produce accurately.
Unfortunately, when the design first comes to them in its primary iteration, it is nowhere near ready to put into a manufacturing facility. It needs to be edited and reconstructed to take advantage of the manufacturing process and remove the dross that will gum up the assembly line.
Table of Contents
Introduction to engineering for manufacturing
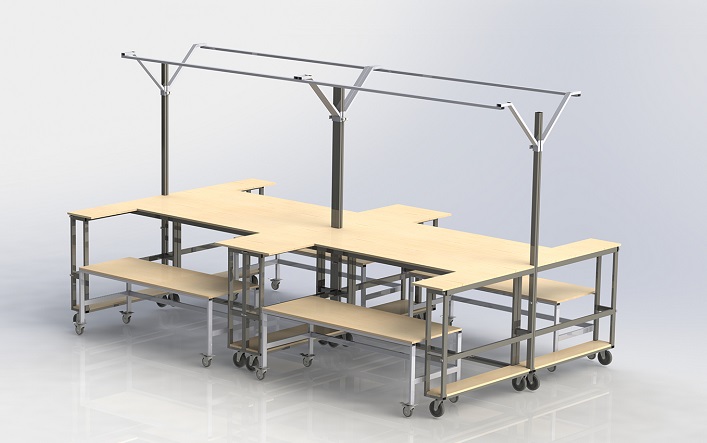
This is called engineering for manufacturing or design for manufacturing. Engineering for manufacturing is a commonly-discussed principle in the world of Six Sigma and efficiency design because it requires a lot of process knowledge to execute. This process is a major requirement for getting something off the page and onto the plant floor.
To put it into a positive light, traditional product design services can be idealists and dreamers. Their designs and plans tend to try and solve every problem at once or be overly complicated or ornate. These are great things in theory, but they do not translate well into the practical realm of manufacturing, especially when it comes to detail or complexity.
We’ve discussed some common ways manufacturing companies produce their parts—most notably with molds, presses, or lathes and machining. With all of these processes, there is a finite amount of complexity they can incorporate. Because of this, it’s difficult for them to make more detailed parts, especially if they involve lots of small pieces or design elements.
In order to make these designs more practical, the manufacturing engineer needs to reduce the complexity and plan for certain things to happen in the manufacturing process. This process is different for every plant and every machine used, so that makes this effort more complicated, but completing this will allow the product to be manufactured much more smoothly.
Engineering for manufacturing process
1. Review the Design
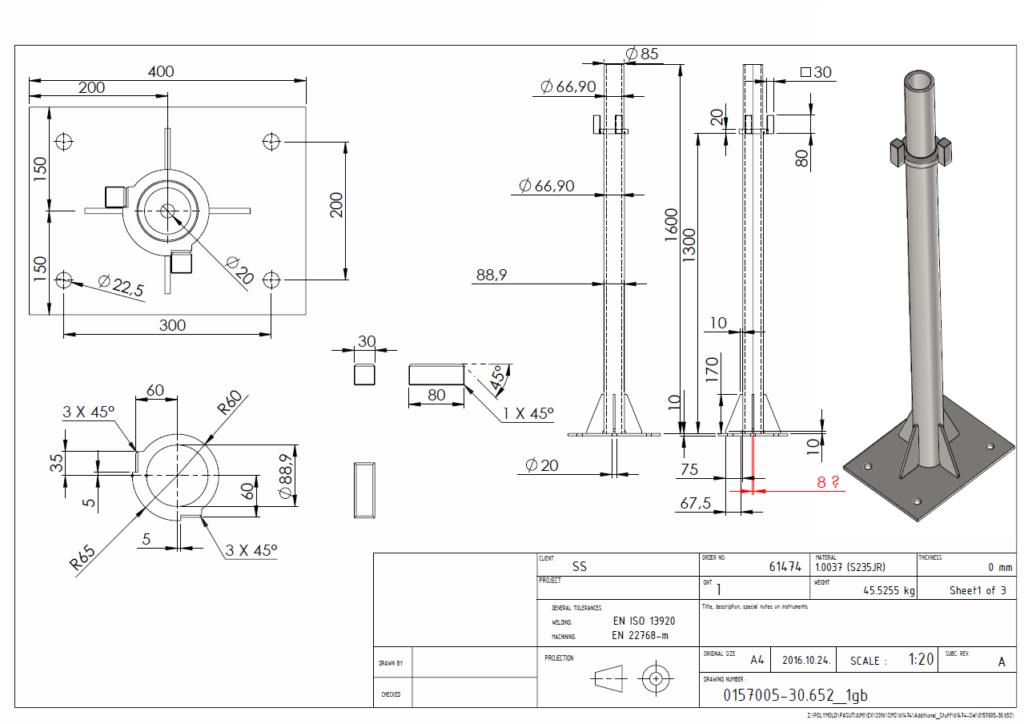
The obvious first step is to review the design. A designer or product engineering service will give you a CAD file detailing their grandiose ideas for the product. Often, they will boldly state that the design is already engineered for manufacturing, and just as often, they are wildly incorrect. It’s not their fault though. You, as the manufacturing engineer, are far more familiar with the process than they, and because of this, you will be able to design it appropriately for manufacturing.
When reviewing this design, there are important things to consider. First of all, look at the complexity of the part. If there is a high level of detail or minute pieces incorporated into the design, that should be addressed. Additionally, take a look at draft angles for extruded or molded parts.
There should not be any sudden, sharp turns in the design, particularly if they are perpendicular to the longest dimension of the part. Simple changes can be made in the preliminary evaluation as you notice them. As you get further along, however, changes will be more difficult to make, so catching them early is crucial.
2. Examine the manufacturing process
The next stage involves using a manufacturing service. Assess what machines you will typically run this sort of product on and what those machines’ requirements are.
The examination should inform more changes to the product. As you take a look through the plant to see where this product will travel and with what it will interact, you will get a feel for all of the different aspects that will make an impact. Essentially, you are walking the process virtually and doing a risk assessment of all the issues that could occur when producing this part.
RELATED: 9 design and engineering tips for reducing manufacturing costs on new product designs and prototypes
Make a list of every crucial item and return to the product. The more details you examine initially, the better the redesign will be. It is certainly a tedious process, but you will be able to ensure that the product will travel successfully through your manufacturing plant without issue.
The goal is to create a usable product, so even if the designer crafted the most state-of-the-art piece they could imagine, if it fails on the assembly line, it won’t be useful.
3. Redesign the product
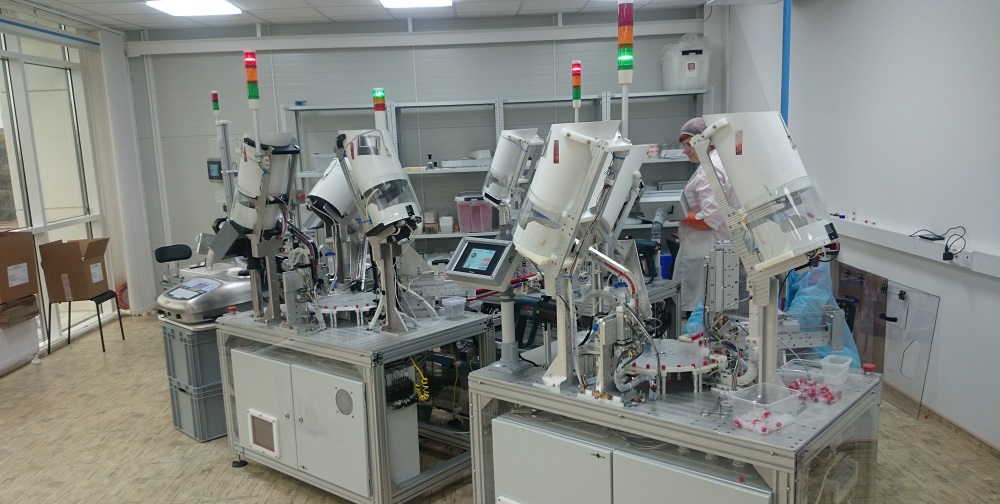
The key here is remembering that you are creating a product. Just as the concept design service was initially trying to create a product that solves every issue, you need to be careful of doing the opposite. There is a risk of deconstructing the product too much, ending up with a part that doesn’t perform its intended function, regardless of how straightforward it was to produce.
Think of it this way, when designing a metal connector for an electrical outlet, the easiest design for a manufacturing facility to produce is a cylindrical piece of bar stock. That won’t function for the product’s purpose at all, though. Because of this, you need to ensure that the product still accomplishes the intended task, while also being as simple to produce as possible.
This requires knowing the specified purpose of the product as well as the key performance indicators. You need to know what the most important criteria for its function are so that you can judge whether or not the product accomplishes the intended goal. Maybe the CAD drawing service made the drawing so that it would perform the intended function but also solve five other problems that are less important.
You, as the manufacturing engineer, can reduce the complexity and remove three of those additional five functions while maintaining the intended function and creating a marketable product.
4. Test and review
The next step is to test and review your changes. This is a never-ending cycle of redesign, test, and review. Well, maybe not never-ending, but certainly long and cyclical. Like we stated earlier, the more attention you pay in the initial phases of the process, the easier production will be. At this point, the majority of the design changes should be made. If not, fix the major errors and test to see how well it travels through the machinery and plant.
You will always run into issues with testing a new invention idea. Your goal is to determine if the issues you encounter are vital to the process or are simple nuisances and perform a risk analysis. You need to determine whether it will be less efficient to adjust the design or live with the pesky issues you found during the test.
There are many situations where that is the case. For example, you may not have the perfect machine to manufacture a part so that it does its intended function. But, with a little added trimming or buffing, you can get the job done on a machine you already have. That may be good enough.
5. Make adjustments in process
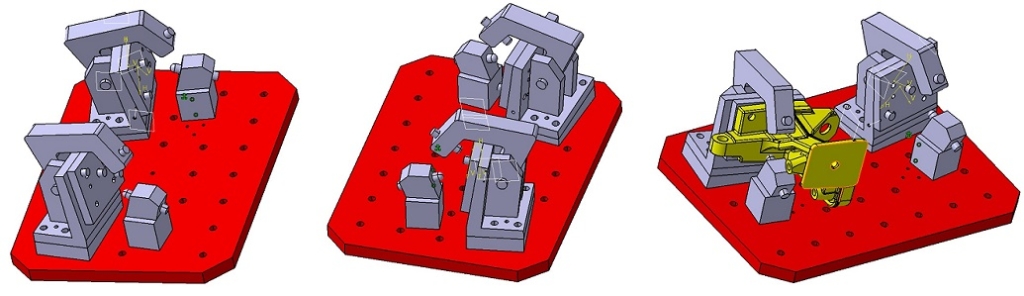
After you’ve performed an assessment of the issues with the design, and redesigned as much as you can without throwing out the intended function of the product, you have one final step. Make adjustments in your process if necessary. This is the other half of the engineering for manufacturing coin—you may need to adjust the manufacturing process.
To do this, though, you need to understand what the critical elements are and what things absolutely cannot be changed.
For instance, you shouldn’t go so far as retooling a machine or changing up the entire process for the sake of one part, unless you truly intend to mold your business around that piece. Every change you make to established processes will affect existing product lines, so you have to be careful what steps you take. A mechanical engineering service can help.
The best adjustments at this stage are simple ones that involve small human actions. Trimming the burrs off of a plastic part or spraying a chemical sealant on top of a metal part are fine options. Repurposing a lathe or other large machine strictly for one part is typically not a great decision. Eventually, if the product line is successful and stable enough, those would be things to consider.
If you get through these steps and still have difficulty manufacturing the product, you need to return to the freelance design service and start from scratch.
Keys to good engineering for manufacturing
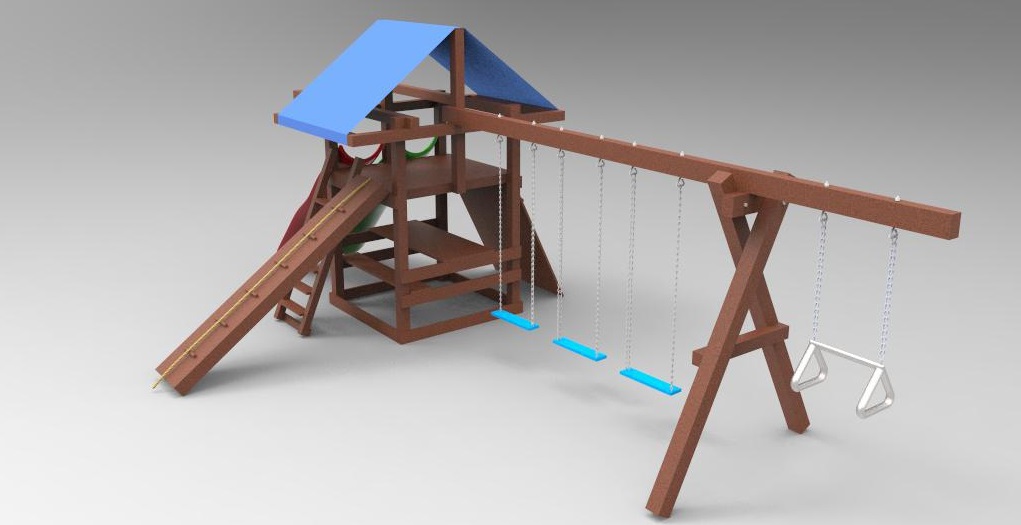
There are a few things you need to make this process effective. The first thing is a good designer who knows the process and has experience with engineering for manufacturing. If you can start off with a somewhat functional design, your experience in the redesign will be much smoother. They will also be able to help you along the way so that you can successfully fix the design.
An understanding of the manufacturing process is also vital. Hopefully, as an engineer in the manufacturing facility, you will have had lots of exposure to it and it will be very familiar with it. If not, it is beneficial to find someone with a high degree of familiarity. The operators who work in the plant on a daily basis are a great resource. They can walk you through the steps they take to produce the parts and see what needs to change to make their lives easier.
An understanding of the materials you use to manufacture these products is beneficial as well. The more you know about the different plastics, metal design and fabrication, or components used in these products, the more you can incorporate them into a holistic design view. The tensile properties of a material will affect machining and molding, and the size of internal components is critical to getting appropriate dimensions. Know your process and know your parts.
Finally, a solid understanding of the end-use of the product will be key to this process. Like we said before, if you know the end purpose and the main goals of the product design, you will be a lot better off with fixing the process. This is because you know the crucial areas in which you cannot compromise. Start from the end-use of the product and then remove things that are not necessary until you get to a point where manufacturing is smooth, and you will have all you need.
How can engineering for manufacturing help your business?
Do you need engineering for manufacturing to help your business? Especially for companies that are just starting on the journey towards manufacturing their own products, this process can be extremely beneficial, and there really is no better time.
If your company is just beginning to create products, you have the liberty to design your process in the most commonsense way possible. Therefore, engineering for manufacturing serves a dual purpose, helping you design your products appropriately for the process and also helping you set up and establish the process for long-term success.
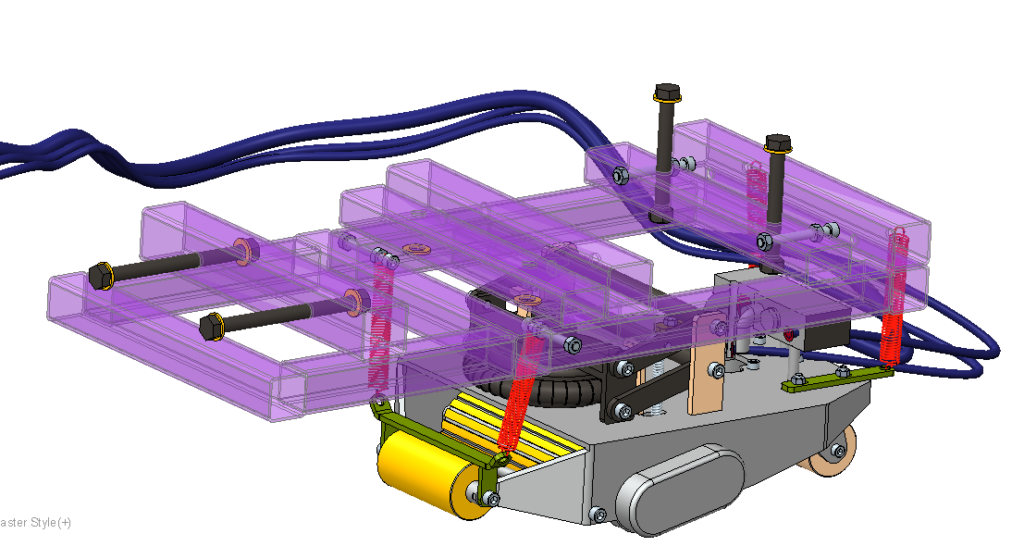
The main thing to remember is that your company is trying to make a profit. As idealistic as you are about creating a product that changes the world, in order to reach the point where you can make something that truly impacts people’s lives, you need to make enough profit to keep yourself in business.
The best way to do this is to make the manufacturing process as efficient as possible. Engineering for manufacturing will help you reduce cost and lead times so that your product can be on the market as quickly as possible, and also will make you as much money as possible.
Even the more established businesses can benefit from this process. Particularly if you are trying to squeeze a new product line into an existing structure, it is almost impossible to be successful without design for manufacturing.
You can take advantage of existing assembly lines and machinery to design your product and ensure you create the most efficient plan possible for the finished product. With design for manufacturing, you enable yourself to get as much out of what is available as possible, as long as you have a little bit of creativity and flexibility.
Frequently asked questions
What other benefits does engineering for manufacturing offer?
Engineering for manufacturing is an excellent practice that helps with efficiency. Not only does it help you successfully create products, but it also makes sure they fit within the overall scheme of the manufacturing plant. For instance, your company may benefit from a more diversified product offering. Without this process, it may be difficult or impossible to squeeze different products into the same footprint by nature of how they’re made.
RELATED: Which manufacturing technology is right for your new invention?
With its aid, however, you can make sure the processes complement one another, utilizing both the space in the plant and the same machinery so that you don’t have any redundant processes, and all production time is maximized to create marketable products as much as possible.
This process also accounts for time and energy savings. You want to make things efficiently and ensure that they can be produced within a reasonable time frame. As such, you will try to balance minimizing operator working time while also making the product as standardized as possible for the manufacturing processes you’re using.
What are some useful tools for design for manufacturing?
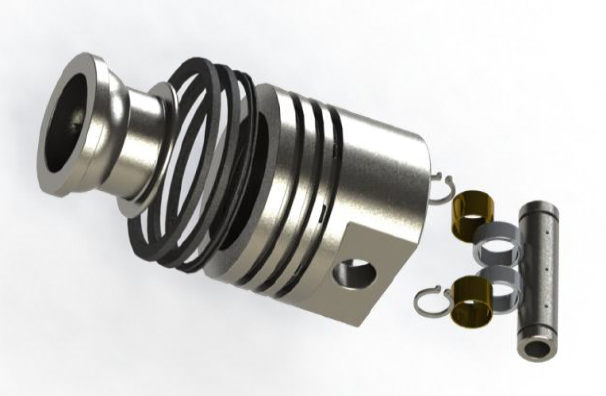
Design software is obviously extremely useful for design for manufacturing. You will need to see and manipulate product designs so they can be optimized for the process at hand. Without access to something like SolidWorks or AutoCAD, you will have a difficult time making your vision a reality, simply because you will need to go back to the industrial design service to make changes continually. Being able to draft things on your own or make the necessary adjustments is vital in the process, if only for your own documentation.
Plant layouts are also very beneficial. When doing a cell layout design or working on an efficiency project, you will want to know how the material flows through the workspace. This is equally important to the design for manufacturing process because motion and human actions will affect the product. By understanding the layout, you can minimize the movement between machines so that parts are manufactured efficiently.
A mold or dye manufacturer or designer will be very useful for this process as well. If you have someone you know that can go ahead and make a design for a mold (assuming you are using a hydraulic press or similar machine), you will be able to test the design more quickly and effectively.
What are the drawbacks of design for manufacturing?
The biggest drawback of this process is simply the time it takes. Time is money, so any period spent on something other than manufacturing is frustrating. However, you can recoup this time lost throughout the process because you are making the product significantly more efficient.
A skilled engineering design service will need to complete this process, and it is basically a necessary evil. Without performing thorough engineering for manufacturing analysis, you will set yourself up for difficulties and failures throughout the remainder of the process.
Not so much a drawback, but certainly a potential issue is the possibility of realizing that you can’t produce the part as planned. There are certainly times when a highly desired piece simply will not work within the confines of the plant as it stands. You will either have to scrap the idea altogether, which is highly undesirable or suggest financial investment.
Perhaps getting new machinery will help you towards successfully crafting the product or hiring more operators to perform the necessary steps. Either way, it’s a potential pitfall, and you should be prepared for it.
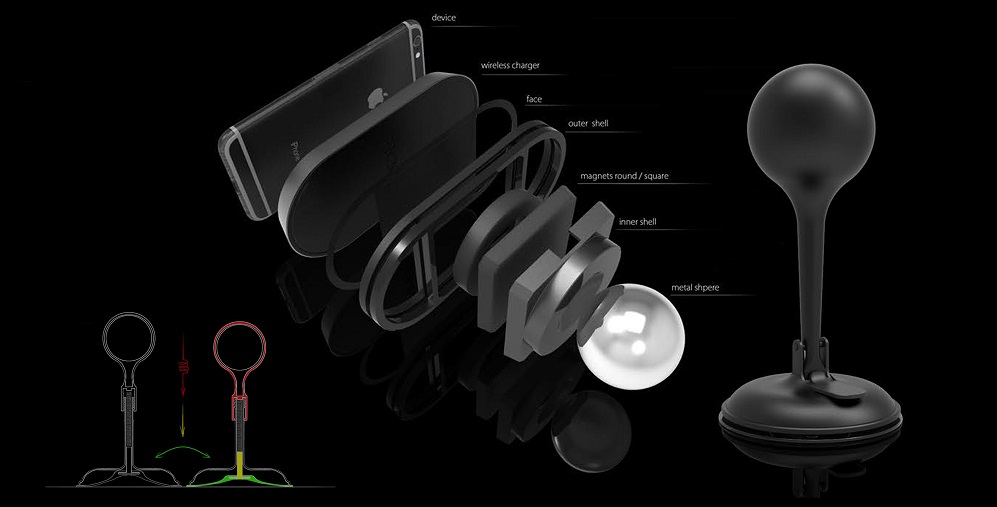
Conclusion
Design for manufacturing can be a tedious and time-consuming process, but it is certainly worth it. All of those “necessary evil” type things really are worth it in the end when manufacturing is concerned. Without taking the necessary steps and performing due diligence, a company can quickly dig themselves into a hole they can’t easily escape.
It requires learning and it requires diligence, but it will pay off. Design for manufacturing will allow you to create a better product that will garner you more profit in the long run because it will fit efficiently into your plant and product portfolio.
You may even be able to help serve the voice of the customer with these actions, creating a more efficient product for their use. This is a very creative form of analytical engineering and should be treated as a way to prevent headaches and loss in the future.
Cad Crowd offers a comprehensive network of engineers for companies in every industry. For more information on how Cad Crowd can help you, contact one of our team members today.