Product development and 3D modeling can be challenging. Contrary to popular belief, you don’t just think of a product idea one day and bring it to life the next. It is a long and arduous process that requires meticulous planning from start to finish ensuring that your product will succeed the moment it hits the market. A product manufacturer must see a visualization of their concepts first as they work on their product design. They need to order prototypes they can experiment with to make it possible.
Unfortunately, prototyping doesn’t come cheap, especially during the initial process of creative development, where ideas flow continuously one after another. The good news is that 3D design and 3D product modeling designers can offer companies numerous benefits, including that they help lower the number of intermediate prototypes required. More importantly, these 3D techniques can make the entire product development process risk-free and more cost-effective. It is also equally critical for product manufacturers to identify any flaws in design sooner than later.
Table of contents
- 3D design and 3D modeling defined
- 3D modeling and 3D design offer adjustibility
- Speed up the product design and development process
- Better and easier communication among development teams
- Simplify the prototyping process
- Fix errors before finalizing the product design
- An unlimited number of corrections are possible
- Get approval for intermediate product design and development stages
- Impeccably accurate and detailed 3D product models
- How Cad Crowd can help
RELATED: Accessible design: better products for everyone
Flaw identification helps manufacturers finalize the design of their products before production. And through the CGI services of a professional 3D modeling company, product manufacturers can come up with a 3D design that is attractive, safe, and user-friendly at the same time. 3D design and 3D modeling may differ but are complementary aspects of the product development process. 3D design refers to developing a 3D representation of an object or product.
3D modeling, on the other hand, is the actual creation of the virtual model of that product or object. Continue reading below to learn how companies can use 3D design services and 3D modeling for better product development:
3D design and 3D modeling defined
As mentioned earlier, 3D design and 3D modeling processes are critical stages of product development. While these two may be very similar, they have some significant differences. 3D design refers to the process where a 3D design of a product is developed. It often involves making a sketch of the product, designing this sketch on a computer, and fabricating it. The 3D design process entails product design based on ideas, sketches, documentation, drawings, and plans. It involves 3D visualization of a model and transforming ideas into 3D structures.
RELATED: 5 Tips for successful product design
3D designers stay up to date with the newest trends in design, can give the model a sense of style, and are adept in volume-spatial thinking. On the other hand, 3D modeling involves developing a 3D model of a product that already exists. Product designers can do it with the help of CAD software or by scanning the product to produce a digital model. After the 3D product model is created, the designer can alter and manipulate it for developing a brand-new product design.
3D modeling has very subtle differences from 3D design, focusing more on developing visual models. It means that a 3D designer can assist a 3D modeler with creative ideas and a framework for shaping a –project. The 3D modeler will then work on fine details such as roughness, dimensions, and others to transform the 3D designs into actual 3D models.
Remember, 3D modeling and 3D design are critical tools in product development. Companies can use them together or separately to develop better products. Now that you know more about 3D design and 3D modeling, it’s time to discover how your company can use these tools to improve your product development process.
RELATED: 10 Simple products that made millions for inventors
3D modeling and 3D design offer adjustibility
One of the key advantages of 3D concept design services and 3D modeling in the field of product design is none other than adjustability. With the help of specialized 3D software, professional CG artists can easily tweak and update any feature of a 3D item without breaking a sweat. For instance, the artist can adjust the product’s proportions, materials, textures, proportions, and geometry. They can also add or remove design elements as and when needed.
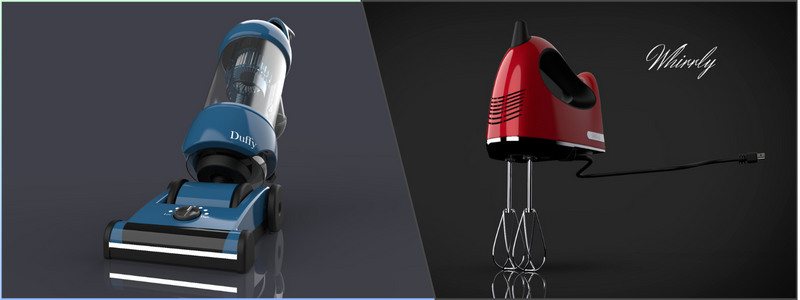
Speed up the product design and development process
In the past, product design development took up too much time. Developing a product design involves a vicious cycle of updating the design, placing an order for a new prototype whenever a significant change is made, and waiting for the delivery of the prototype. This cycle continues until the product design is perfected. But with the rise of CGI technology, things have changed dramatically for the product design process.
The manufacturing firm needs to develop product designs; an expert 3D artist will create digital visualizations of these ideas. Thanks to this, product makers no longer need to order several prototypes, often adding to their expenses. Instead, they can quickly test several concepts one after the next without any unwanted delays. Some CG specialists can even develop 3D product models regardless of the complexity in just a few days.
RELATED: 12 Unique product design ideas
Better and easier communication among development teams
3D design and 3D modeling can benefit every project member as these tools can simplify communication between the stakeholders and the product design team. Since all project members get identical 3D files and visualizations, all professionals will be aligned. In addition, since 3D designs and 3D models can be saved in universal file formats, all the specialists involved can work on them without switching from one software to the next.
Simplify the prototyping process
With the help of 3D design and 3D modeling, product designers will no longer require numerous intermediate prototypes. Working hand in hand with the CG experts, they can update and alter a 3D model as often as necessary and see the results immediately. 3D designs also allow them to experiment until they achieve their intended product. Once everything looks perfect, the product manufacturer will only need a final prototype that their target audience can use for testing.
RELATED: 12 Brands using crowdsourcing for product design ideas
Fix errors before finalizing the product design
One significant advantage of 3D design and 3D modeling is that they help manufacturers spot design mistakes or errors sooner, even without a prototype. Any 3D object can be optimized for CAD software. It will help automatically check if it complies with the drawings and report errors if there are any. 3D simulation is another notable benefit that a CG modeling professional can provide.
Regarding products with complex mechanisms, CG experts will be able to perform 3D simulations that can help pinpoint malfunctions and address any safety concerns. The whole process can be done using special software that only needs the CAD model of the object. Once a 3D object is ready, the CG artists can optimize and export it to the specific file format that best suits and works with the CAD software in use.
An unlimited number of corrections are possible
The most obvious advantage of 3D design and 3D modeling for product development is that the manufacturer can make unlimited necessary adjustments. It is possible to edit any 3D model until the manufacturer is happy and satisfied with the result. Most 3D product rendering and design studios include a certain percentage of corrections in the total project cost. It means that once the adjustments go beyond the set limit, resulting in significant changes in the 3D model, you can expect it to be considered a new and different project.
RELATED: 10 Steps for freelance designers to create and manufacture a new product
Get approval for intermediate product design and development stages
Both the manufacturer and the marketing team must approve and give a signal to any change made to the product design. It is not effective to use old-school freehand sketches for this particular purpose since these cannot showcase the details of the design in full splendor. Receiving high-quality 3D renderings of the different stages of the product design process is one of the significant advantages of CGI. Expert 3D product engineering specialists will be able to render several variations of the design of a single item. All there is left to do for the manufacturer is to pick the best choice, thus speeding up the decision-making process.
Impeccably accurate and detailed 3D product models
Meticulous and thorough accuracy is a substantial benefit of 3D design and 3D modeling. 3D objects are the only ones that can ultimately showcase every design feature, not only the external but also the internal ones. If necessary, CG experts can slice a cross-section of a 3D model to present every detail of the design better.
RELATED: How a product design service can handle tough new product development deadlines
Alternatively, 2D drawings or freehand sketches cannot showcase the design and all its benefits, typically highlighting just a few aspects that might not help much in the decision-making. With the help of 3D design services or 3D modeling services, companies can look forward to better and more efficient product development.
How Cad Crowd can help
One of the best ways to succeed in your design project is to work with a talented product designer. Cad Crowd connects you with the best CAD designers and 3D modeling services in the business. Get a free quote today.