With additive manufacturings rise to prominence over the last decade came a slew of benefits for product designers as well as consumers. Companies are turning toward additive manufacturing to simplify and excel their manufacturing processes.
What once was reserved for the wealthy is now being used by everyone, including solopreneurs. The cost of an entry-level 3D printing machine is quite low – you can get one for as little as $500.
This is allowing more people to get their ideas out into the world. It’s an efficient and affordable way for start-ups and large companies to test out new product ideas with little investment.
With that said, let’s take a look at the benefits of additive manufacturing for product design in more detail.
Realizing Design Concepts
Additive manufacturing allows everyone from entrepreneurs to large-scale companies realize new design concepts. From concept ideation to prototyping, additive manufacturing quickens each process and allows product designers to fully achieve their concepts. In fact, prototype design services almost solely use additive manufacturing.
All products, regardless of their complexity, can be created using a 3D printer. Where additive manufacturing shines is its ability to create intricate designs and parts. Designs filled with complex geometry and many parts would typically be expensive to prototype, posing as a huge barrier to entry for small companies. Thankfully, this is no longer a problem.
Small companies who would be limited to virtual prototyping and product visualization due to financial limitations can now create real-life prototypes. They can fully realize their product designs, viewing it in the real world as opposed to the guess-work involved in a CAD model.
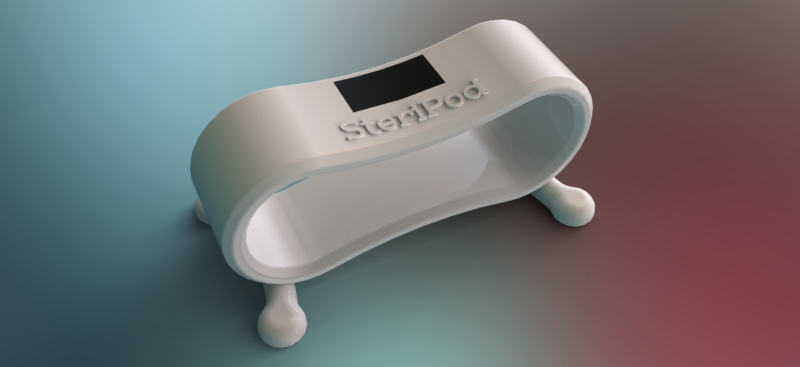
Designers can more easily create prototypes without a substantial financial investment. In fact, they can even recreate prototypes with little to no cost, as the process is quite affordable. Thanks to this, product designers can take advantage of being able to physically examine the product to determine if improvements should be made.
It’s also worth mentioning that a physical prototype can serve other purposes aside from aiding in design. Marketing and sales departments can use a physical prototype for their advertisements and sales pitches. They can also be used to demonstrate a product’s effectiveness to potential investors who otherwise may not get the gist through a 3D CAD model alone.
Minimizing Design Flaws
With additive manufacturing, product design companies are able to work out the kinks in a product’s design before it hits the market. This is invaluable in retaining customers and being successful – as they say, a first impression means everything.
Products designed with CAD would once only be analyzed virtually, and if you were lucky, you could create a prototype or two through traditional methods. This was not the best testing process and resulted in many products hitting the market before they were ready.
3D printing gives designers the opportunity to print countless models to test a design’s function and aesthetic appeal. And when you make changes, it’s simple just to reprint the model and look over it again for little cost and effort.
Additive manufacturing makes prototyping more affordable for not only wealthy companies but for small businesses and entrepreneurs who would otherwise not be able to test their products generously.
It also allows you to test multiple colors, materials, and other aesthetic functions of a product in real life. While virtually, you could test these things, getting an in-person view of the product is priceless and allows you to get personal with the product.
Incorporating Design Changes Instantly
With a virtual prototype, identifying problem areas that need more attention is more difficult. While CAD designs are increasingly becoming more complex and high quality, nothing beats getting a physical prototype into your hands.
With your physical prototype, you can identify product flaws more easily. A physical prototype lends itself to feedback in that you can show it off to potential customers and ask for feedback. They’re the ones buying, so it’s essential to get their opinion before launch.
Aside from the function, a physical model can also be critiqued on its aesthetic. Seeing how parts fit together and how colors look in real life can make a world of difference in the final product. It’s highly recommended to test a few aesthetic choices before finalizing.
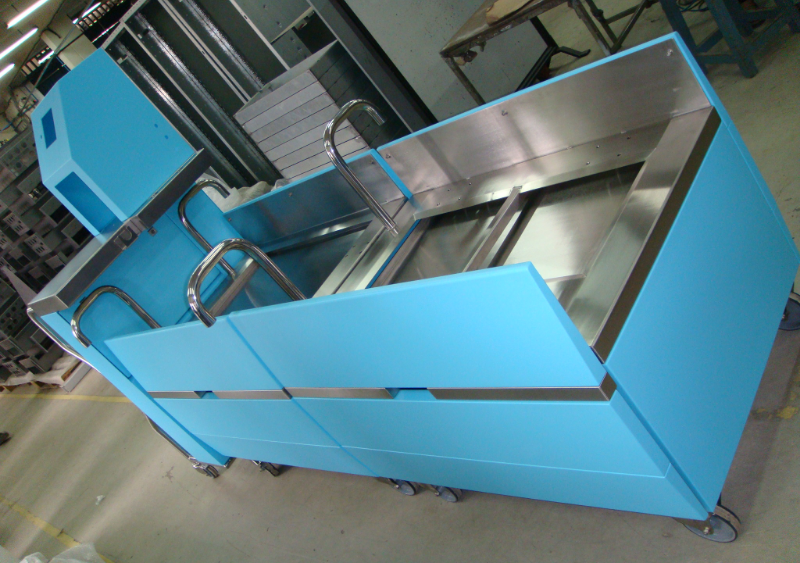
And with a physical prototype, you can immediately respond to feedback. Each time you receive a piece of criticism, you can directly go into your CAD file, input the change, and reprint the model for another look.
You can even print multiple versions of one design to compare and contrast them, speeding up the production process. And with each iteration, your product design will improve – and this is all before your launch!
It’s the best way to determine how your market will respond to the product. The worst-case scenario is that there’s little interest in your design. It’s better to find that out before launching though, right?
Saving Cost and Time
With additive manufacturing, you can save money creating your product design. Prototypes using additive manufacturing are notoriously cheaper than traditional manufacturing methods. They require less material and can be made quicker.
Additive manufacturing requires fewer materials and less energy to create a fleshed-out prototype. It significantly reduces the manufacturing processes environmental footprint. This is not only good for the environment but also saves you money in the long run.
This not only applies to prototypes, but also to products and parts in general. Many manufacturing services are turning to 3D printing to create pieces that would otherwise take more material, money, and time to make. 3D printing can completely eliminate the need to create molds, special tools, and patterns to design machine parts.
Conventional manufacturing methods like CNC machining produce tons of waste. Additive manufacturing only uses material required to create a part of the product, and at a much faster pace too.
A report by GE has an excellent example of this. Their LEAP jet engine uses a fuel nozzle that are laser printed. With additive manufacturing, they create a single nozzle made of one piece that is more durable, lighter, and reduces fuel burn by up to 15 percent. If they were to use traditional manufacturing, they would need to create 20 different parts and weld them together to create the same nozzle at a lesser quality.
This is also why industries are turning toward 3D printing for large scale products. For example, 3D printing can be utilized to create low-cost housing. India has plans to create 3D printed homes on a larger scale within the next year or two, a solution to their deficit in housing and transportation.
Customizing Designs
A benefit of additive manufacturing is being able to customize the product to the customer’s desire. That is, because rapid manufacturing allows products to be created on-demand, certain products lend themselves to customization.
To customize a product that will be 3D printed, all that’s required is a change in the CAD design. Manufacturers don’t need to create a whole new product using new tools and processes – all they have to do is reprint the design after the CAD file is changed.
This is a benefit to manufacturers, as it allows them to provide more options to consumers. When a consumer can customize their product, they feel more connected to the brand and item as a whole. It encourages them to come back and engage with the brand, as they’ll care more about their product than if it was a generic item.
Manual customization would require a lot of physical labor and increasing costs. To take advantage of the trend of mass customization, additive manufacturing must be used. No one really wants the same generic item as their friend – they want something customized that they can be proud to show off.
Some companies, like Nike ID, already take advantage of this. They allow customers to change the color and design of their shoes online, directly altering their own 3D file. This creates a sense of brand loyalty and gives them an edge in the marketplace.
Fully-Managed Print Jobs
Once you actually get your product out there, you can use additive manufacturing to begin creating the parts of your design (or maybe even the entire product itself) that lend themselves to 3D printing. Choosing the right manufacturing materials can be tough. Nowadays, you’re able to print all sorts of things, and it’s the best to way to create complex items. Metal 3D printing has even come a long way.
Whether you’ll be 3D printing your entire product design or just a few parts, you can set up fully-automated print jobs. That means fewer employees, less tedious manufacturing work, and more accurate models.
With traditional manufacturing, you’d have someone stuck doing repetitive work on a product line or something similar. This lends itself to human error and potentially costly mistakes. Having the ability to automate your design process puts a machine in control, keeping design consistent, efficient, and affordable.
Potential for More Sustainable Designs
Additive manufacturing is the opposite of subtractive manufacturing. The former involves adding only the material required to create a product, while the latter entails stripping away elements from a large block until you have just your product left.
It’s obvious which of the techniques is more wasteful. Subtractive manufacturing involves more material than required, and the leftover is often not recycled or reused.
Unlike subtractive manufacturing, additive manufacturing only uses the materials required to create a product. This translates to less waste.
RELATED: Sustainable Product Design Tips for a Healthy World
In addition, additive manufacturing is quicker. There’s a significant amount of time required to remove unwanted material in the subtractive manufacturing process. So, with 3D printing, you’re not only saving on materials, but you’re saving time and energy.
Another way additive manufacturing is more sustainable is in the quality of the design. While quality is itself subjective, you can’t argue that a personalized item is inherently higher quality to the user. With 3D printing, manufacturers and freelance product designers are able to create items for their users exactly.
Old manufacturing methods use a one-size-fits-all approach, which in reality is usually one-size-fits-none. This leads to more product turnover and less satisfied customers. More products are thrown in the trash, and their lifespan is reduced.
Custom products made specifically for their users are more valued. They function better, in ways that the user expects, and are more likely to be kept and used in the long run.
If you’re looking for 3D printing services to manufacture your next product design. let us help. Cad Crowd not only has a network of product designers ready to help, but we are also connected to manufacturers around the world. Shoot us a message and we’ll help get your prototype or manufacuring run going.