Prototyping is an important aspect of product design and manufacturing. Without effective prototypes, companies may create products that are unsuitable and do not meet design requirements. Moreover, in a mass-manufacturing environment, a lack of using a prototyping design service could cause issues with production. We have created a detailed guide below for prototype design in a mass-manufacturing environment that fortune 500 companies may follow:
The Prototype – Why Is It Used in Mass-Manufacturing?
First, it is important to define prototypes and their functionality in mass-manufacturing environments.
What Is a Prototype?
The basic definition of a prototype is:
“A first or preliminary version of a device or vehicle from which other forms are developed.”
In a typical product design lifecycle, the product design freelancers create a product concept. This is developed using detailed research and design techniques. Once a concept is established, the basic shape, form, and parameters of the product are then created, often using CAD and 3D modeling software.
On completion, a prototype is then required. This is usually the first physical manifestation of the product—something that is tangible and can be tested. Prototypes are usually not suitable for manufacturing, but they are quite close to the finished product.
Why are Prototypes Required for Mass-Manufacturing?
In a mass-manufacturing environment, thousands of products are made—for example, light bulbs, electrical components, and household furniture components. It is not a personalized or hand-made service—the important factor is volume and efficiency.
Therefore, the product design must be perfect. Product flaws result in manufacturing defects. Moreover, design errors could cause manufacturing bottlenecks or a waste of raw material and resources.
To that end, we can see why an effective prototype is vital in a mass-manufacturing environment. A well-designed prototype can be translated into a manufacturable product. It can then be produced without issue and allow for a cost-effective mass-manufacturing process.
What are the Different Types of Prototype?
To effectively design a prototype for mass-manufacturing you must understand the different types of prototype. There are two clear distinctions—proof of concept and production quality:
Proof-of-concept prototype—This is not a prototype suitable for mass-manufacturing. A proof of concept prototype is typically created during early design stages. It is a rough idea that cannot easily be translated into a working product. This type of prototype is used to further refine product designs.
Production quality prototype—This is a prototype suitable for mass-manufacturing. It is a design that is virtually ready to be produced. Production-quality prototypes have greater detail and are as close to the finished product as you can get. These are suitable for mass-manufacturing as the production team can quickly translate into a workable item that can be manufactured in their facilities.
Examples of Industries Prototypes are Used
This type of prototyping is used readily by fortune 500 companies. It is a tried and tested method that helps the efficient development and production of products. Manufacturing companies will have entire teams and sections devoted to product development and the effective design of prototypes. We have listed some example industries where mass-manufacturing prototyping is used below:
- Aerospace
- Automobile
- Medical Equipment
- Electronics
- Household goods
- Children’s toys
In the aerospace industry, for example, fortune 500 companies like Boeing and United Technologies will employ prototyping for airplane components. Alternatively, electrical companies like Whirlpool and Honeywell International will use prototyping to effectively design new electrical components for their devices. Hire a freelance aerospace engineer!
A Prototype Design Guide for Mass-Manufacturing Products
The prototype design process follows a set pattern. This could vary depending on the industry, but the basics remain constant. We have listed this basic process below:
- Analyze Information and Requirements from the Designers
Ideally, you have information presented from the design team. Indeed, you may have worked with the design team during the initial concept phases. To create an effective prototype, full disclosure from the designers is necessary. This includes the following information:
- 3D model representation of the product
- All measurements and dimensions
- Preferred materials and components
- Product goals and usage
This information allows you to create an accurate prototype that reflects the original design concepts. Furthermore, the more information you have, the more complete the prototype is. This means it translates quicker and easier into a manufacturable item.
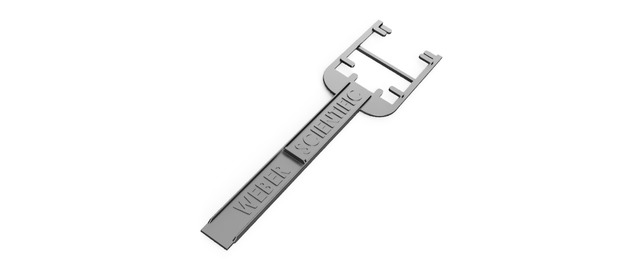
It is important to continually refer to information from the designers. If you don’t, you may lose focus and create a prototype that is ineffective.
- Create Clear Goals and Benchmarks
Before starting the design, you must assign clear goals and benchmarks. Oftentimes, benchmarks and KPIs are assigned by management or those overseeing the product development. Regardless, you should have something to work towards. Simple goals include:
- End date for the completed prototype
- Maximum budget
- Tolerances for design accuracy
Benchmarks and progress points are also important. For example, you may set daily tasks that you must achieve. Essentially you must plan the prototype design process to give yourself achievable milestones, and a clear plan of action.
- Design the Prototype
Once a clear plan of action is created, the prototype design and production process can begin. This stage varies greatly depending on the software, machines, and tools available. Moreover, how the designs have been presented will determine how a prototype is created/designed too.
For example, if 3D models have been presented from the design team, they could be quickly translated into CAD/CAM to produce a physical prototype with ease. Alternatively, if paper designs and blueprints are given, these designs would need to be translated into digital plans first.
During the design stage, you create a working prototype and physically produce it.
- Refine if Necessary
In an ideal scenario, a prototype is created, and it is perfect first time. It can then be signed-off and transferred to the production department. Oftentimes changes are required, however.
What works well as a 3D model, may not ultimately transfer into a workable physical product. This is the main point of prototyping – to assess the viability of a product and ensure it can be produced. Therefore, you may have to refine the designs. Furthermore, you may have to send the 3D and concepts back to the design team for changes.
Small “bumps” like this could happen several times. Furthermore, you may have to re-submit concepts to the design team repeatedly. Eventually, a usable prototype is developed that meets the designer’s specifications.
- Test the Prototype
To ensure viability, prototypes are often tested. Examples of testing include:
- Strength tests
- Pressure tests
- Usability tests
- Resistance tests
A mixture of physical tests and usability tests are essential. For example, a prototype of an airplane part is placed under different physical tests to ensure its durability. Alternatively, items like furniture and household goods could be tested for usability to ensure they are fit for purpose. The different tests required should be discussed and formalized during the initial planning stages.
Depending on the results, the prototype may have to be refined by the rapid prototyping team. For example, if that airplane part did not meet minimum durability requirements, it would have to be completely re-designed.
- Submit to Manufacturing
Finally, once you have completed the prototype, it must be submitted to the production/manufacturing department. Throughout the process, it is likely that production is involved – making suggestions and ensuring the product can be made.
The manufacturing department makes an arrangement to produce the finalized design. Before this happens, checks and authorization may be required. For example, the product may have to pass health & safety checks. Furthermore, it may have to be authorized by a board of directors, shareholders, or even regulatory bodies within the industry.
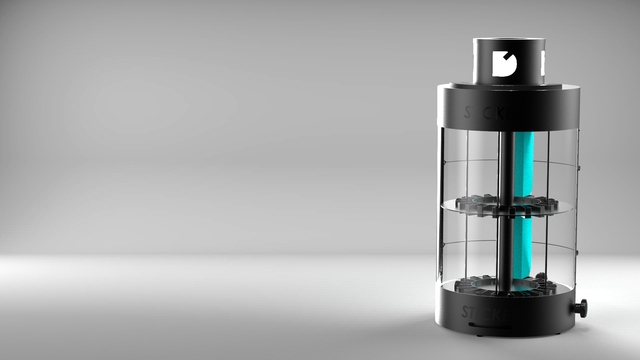
Regardless, the prototype team will now have minimal input. Manufacturing may seek further advice. Moreover, they may ask for a re-design of the prototype if circumstances change. However, in most instances, the project is complete from a prototyping perspective.
To conclude, a review and assessment are prudent. Review the design process – what could have been improved? What worked well? You can use this assessment for future projects as a form of continual improvement.
Simple Tips to Improve the Prototype Design Process for Mass-Manufacturing
Aside from the basic prototype design process, we can offer advice too. When creating a prototype for mass-manufacturing, there are things you can remember to help:
Understand the Available Manufacturing Setup
This type of prototype is created specifically for large manufacturing operations. In most instances, the facilities will not be radically altered to produce a new product. The opposite must occur – the product (and prototype), must be designed for the available manufacturing setup.
Therefore, you must consider the production facilities available. What manufacturing equipment will be used to create the product? What constraints are there? Are there any health and safety regulations that must be adhered too? Ensure you have an in-depth understanding of the available facilities. This ensures you won’t develop a prototype that can’t be translated into a manufacturable item.
Communicate Frequently with the Design and Production Teams
In this scenario, designing a prototype should no be an isolated process. Communication is important. Indeed, you may enlist the services of other 3D product modeling services during the design. Designers can provide valuable input. They understand the purpose and intent of the product. Moreover, they can assess your prototype to ensure it meets the original design requirements.
The production team can analyze the prototype to ensure it is appropriate for their facilities. Moreover, they can start taking details from the product design. These details are used to prep manufacturing facilities. Moreover, the production department can look at materials and start planning with suppliers, etc.
Effective communication makes the process smoother. Moreover, it ensures that errors and potential design flaws are quickly addressed.
Don’t Lose Sight of Your Goals
As a prototype designer, you must have goals. In any aspect of the product development cycle, goals are important to keep focus and stay on track. Without goals, the design process becomes convoluted, disorganized, and inefficient. Furthermore, what should be an easy process, could take much longer than anticipated.
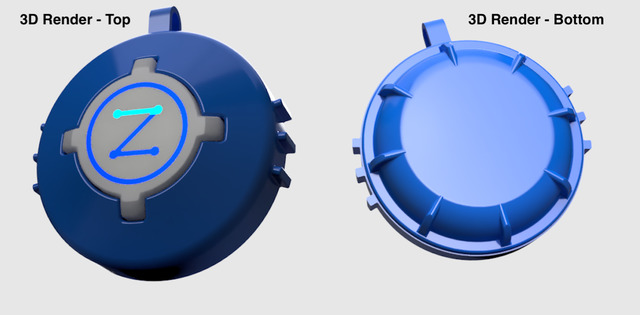
Examples of prototype design goals include:
- Timeframe for prototype completion
- Allowed budget
- Desired outcome
- Adherence to design and company ethos
Set simple goals like these to focus your work. Check regularly that you are achieving your goals – review sessions can help measure your progress.
Utilize Digital Technologies to Improve Efficiency and Speed
Finally, in modern manufacturing, utilizing the latest technology is vital. Designers have an array of advanced software and systems for prototype creation. For example, the use of CAD systems and 3D modeling software greatly reduces prototype development times. Furthermore, it allows for greater flexibility and creativity.
In addition to 3D modeling and CAD, consider additive design and the use of 3D printers. 3D printing technology enables the quick and accurate creation of prototypes. Particularly for simple designs with few parts often used in mass-manufacturing industries. Utilizing these technologies is important to maintain an efficient prototype development process.
We hope you have found this article beneficial. It is important to understand all aspects of the product design cycle including prototyping. For mass-manufacturing businesses, an effective prototype design process helps greatly.
Firstly, it speeds up the “idea to product” timeframe. Secondly, it ensures product designs transition smoothly into a manufacturing environment. Ultimately, it means a business can create and produce new products for reduced cost and time. If you need prototype design services, give Cad Crowd a shout. We facilitate the services of professional designers for manufacturing industries. Get a free quote today.