Depending on the process you’re using, your parts can come off the the 3D printer looking more or less sharp. Usually, though, there’s at least some amount of post-processing required to get your piece presentation-ready — especially if you’re printing consumer goods. This is what surface finishing is all about, a technique that turns a raw 3D part into a finished product.
Finishing should be a design consideration from the start. Why is this so important? Parts can be made of different materials, come in different shapes, and are also processed differently – these will factor into the kind of finishing operation to be used. As such, it’s important to know what techniques are possible for different processes.
Fused Deposition Modeling (FDM) uses engineering-grade thermoplastics when building 3D parts. This kind of material can be put through the same post-processing process used for injection molding such as drilling, painting, priming, and sanding. Laser sintering often requires a fair amount of post-processing, and in the case of metal sintering, it requires a significant degree of skill and expertise.
3D objects created using PolyJet already have smooth surfaces after printing is done. As such, they don’t need any post-processing. Depending upon their intended use, though, but they can benefit from some coating or paint.
The Need for Finishing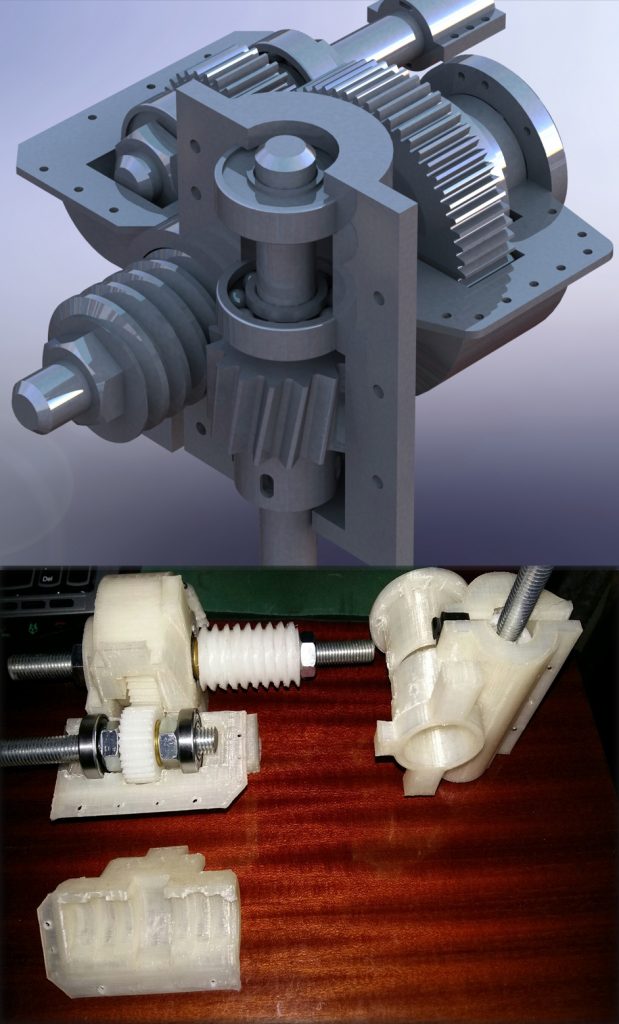
While a 3D-printed part often comes out pretty close to a finished state, it’s still a raw product. We haven’t quite reached the futuristic world of instant fabricators. While there typically isn’t any assembly required, it can still be improved, most especially in aesthetic terms. Products produced through 3D printing will be used in different situations and they need to look good and function as planned.
1. To Improve the Appearance of a 3D Part
3D printing has opened up so many doors for creative products to be made. From simple objects to intricate geometries, there is a world of possibility when it comes to 3D products. But these products don’t come out of the machine looking like a real finished product – they still have to go through the finishing process.
Finishing improves the look of a product; it makes it look more appealing. After all, this item will need to catch the attention of buyers. Which means it needs to be presentable. Layer lines are still visible once a 3D object comes out of the machine. This can usually be taken car of with a bit of sanding, resulting in a much more visually appealing product.
2. To Reshape an Object to Meet Certain Dimensions
There is an ever-increasing range of different available for 3D printing and each of those materials has a specific print dimension. Different printing methods also have different resolutions, or degrees of accuracy, that they can produce right off the bed. What this means is that, for objects that must conform to highly specific tolerances, a bit of post-processing is often required to smooth a part down to just the right shape and size. The degree to which this kind of finishing is required will depend entirely on the technology and material used, as well as the intended use of the printed part.
3. To Enhance Functionality
3D-printed parts have a purpose and need to be improved after coming out of the machine so they can function as planned. This is what the finishing process is for as it can increase strength, improve electrical conductivity and even enhance chemical resistance. Usually this will involve coating or plating the printed part in additional materials in order to provide it with the required characteristics.
Finishing Techniques
Geometry and the material used determine what kind of finishing technique can be used for a specific 3D part. Different textures, as well as appearances, can be achieved depending on the technique you will use. However, the kind of material and its size, and of course the intended use, will be major factors in deciding what kind of finishing process is applicable.
Why should the size and material of a 3D object be top factors in determining the kind of finishing technique to be used? There are methods better suited for objects that will serve as prototypes while other techniques are best used for display models.
Here are some of the different finishing techniques available for 3D-printed objects:
1. Bead Blasting
This is the second most used finishing process next to sanding. It’s easier to reach internal channels using this method (since you don’t have to twist your arm up in crazy directions to fit into strange places). As the name suggests, little beads are blasted against the part to smooth out the appearance
Bead blasting is done using a spray gun and plastic media, which will be used to remove layer lines from a 3D part. The entire process takes about five to ten minutes to complete, varying depending upon the size of the part. Once an object has undergone the process, it will bear a smooth matte surface appearance.
A big advantage of bead blasting for 3D printed parts is its flexibility. This method can be performed whether a product is still in the prototyping stage or the production stage. Bead blasting is also appropriate for parts produced through FDM, which is a very common and accessible method of 3D printing.
Objects that have gone through vapor smoothing have a sheen and bead blasting can get rid of that if a matte finish is preferred. This method is not suggested for PolyJet parts because those objects already have a smooth finish.
A limitation arises with bead blasting when the size of the object is concerned. Since this process is performed inside a chamber, the object’s size must not be more than 24x32x32 inches. Another drawback is that only one object can be worked on at a time.
2. Sanding
3D objects are still raw when they come out of a printer. In particular, they still bear layer lines which throws off the aesthetic. This is especially problematic for consumer-grade parts or for parts meant as display models or sample products. Sanding can solve that problem and is the most popular kind of finishing technique.
This is the same kind of process we’re all familiar with from woodworking, except here the point is to get rid of the layer lines from the additive process. This can be done by hand or by using belt sanders. Sanding is simple, inexpensive, and pretty flexible. Anyone can do it and it’s hard to really mess it up, which is also nice.
Sanding is also important whenever any kind of coating is to be added. Before any coat is added, the object has to be sanded. It’s also a good idea to sand between coats, should multiple coats be required. This is done to ensure that the surface being worked on is smooth and will take an even coat.
While sanding is a tried and tested finishing technique, it does run into trouble with certain objects, particularly those with small undercuts and holes. To reach those areas, a different smoothing technique will be needed (like bead blasting).
PolyJet objects don’t need to go through the sanding process given that they already come out of the machine with a smooth look (PolyJet has an extremely high degree of accuracy).
3. Tumbling
This method is mostly used to process and polish metals, but the process can be applied to many plastics. This is done with some material that is softer that the part, such as ceramic, corn cob, plastic or some synthetic.
Tumbling works like this: the object to be finished is put into a vibrating unit containing a soft media. The unit is rotated by a machine for a number of hours until the media polishes the surface.
This method is best used on strong FDM materials, such as ULTEM and polycarbonate. One of the advantages of this method is that parts don’t need to be worked on one at a time; many parts can be put into a unit and processed at once.
With advantages comes certain drawbacks as tumbling is best suited for objects that are round as they don’t have a lot of sharp edges and corners which could be damaged during the tumbling.
4. Vapor Smoothing
This method works by melting the surface of a 3D part using a solvent. The part is exposed to a vapor chamber for a number of seconds resulting in liquefied plastic. Once that is achieved, the part is then immediately placed in a cooling chamber to halt liquefaction. This process results in an object that is not only smooth but shiny as well. The resulting object can be further finished by bead blasting to remove the shine, if desired.
Dimensions are preserved with vapor smoothing. Porosity, particularly those with FDM parts, is eliminated with this method which is good news for items that will be used to hold gas or liquid.
The vapor smoothing method is mostly used for finishing items that will serve as holders, like bottles. Some materials, such as polycarbonate, ULTEM 1010, ULTEM 9085 and PPSF, can’t be finished with this method as the solvents might cause harmful chemical reactions.
Another disadvantage of this method is its size restrictions. Since the object needs to be put inside a tank, it shouldn’t exceed a certain size (3x2x3 feet). That said, most people aren’t printing parts larger than that.
Conclusion
Those are some of the most common techniques used to process 3D printed parts. Of course, there is more to it than that. Objects produced through Direct Metal Laser Sintering will often require more substantial post-processing to get rid of leftover support structures. Because those support structures are themselves made of metal, this often involves machining or grinding, and should be undertaken by professionals.
Speaking of professionals, do you need professionals? We have them. Whether you’re looking for experienced professional CAD design freelancers or expert contract manufacturers to 3D print and process your parts for you, Cad Crowd has got you covered. With thousands of designers on hand, we’ve got the expertise you need.
Get in touch with us now to receive a free quote. We’ll connect you with pre-qualified, reliable designers, engineers, and manufacturers.