Reverse engineering is a process where a product, structure, or mechanism is disassembled or deconstructed to gather information about how the design works. As the name suggests, the design process is the opposite of a typical product engineering process. Instead of assembling a product or design part by part, with reverse engineering services, it is disassembled in a backward sequence. Some companies use reverse engineering to improve their products, reduce production costs, or make legacy replacement parts. Other firms may use reverse engineering to understand how competitors build their designs and launch competing products.
Table of Contents
RELATED: How reverse engineering services use 3D laser scanning for design
The cost of reverse engineering
In the United States, a reverse engineer charges anywhere from $50 to $145 per hour. Engineers very rarely charge on a per-project basis because there is a probability of discovering “unknowns” during the process, especially when the objective is to determine faulty parts in an existing product. Since it is difficult to determine if the job will be easy or difficult, reverse engineers tend to charge a higher rate in the range. The cost of reverse engineering is affected by various factors, such as locations, desired output, and timeframe.
Most design engineering firms suggest that the clientship the product to their facility. The engineers will outline requirements when the project requires on-site inspections. In this instance, the client will compensate for travel costs. An in-house project completed in the firm’s facility can run from a few hundred dollars for a simple product to thousands of dollars for complex machinery with electrical and mechanical parts.
RELATED: What are industrial design rates & costs at product design services firms?
Product complexity increases the difficulty level, and so does the desired output. If a client wants a detailed report of each component in a complex product, the price can go up considerably from the introductory rate. The typical time frame for reverse engineering work on a simple product is around two weeks. An expedited project takes about one week from delivery and will add up to 30 percent of the standard pricing.
Reverse Engineering Process
The most critical requirement for reverse engineering a product is obtaining a physical sample. Engineers will need tools and equipment to take effect apart and do the examination. The process of reverse engineering always involves disassembly. Once the outer shell of the product is removed, the internal mechanisms, including electronic components and mechanical parts, can be closely inspected. All product parts and components are documented in detail, including information about dimension, color, assembly sequence, function, specification, manufacturers, and price. Such a method allows engineers to figure out the blueprint of a product.
RELATED: How do engineers evaluate different design ideas?
Regardless of the product size, engineers start by analyzing the product dimension. It does not matter if the product is a massive commercial airliner or something as tiny as a microchip. In most cases, a large electronic product comprises thousands of smaller parts. Engineers take measurements of every component’s height, width, and depth during the process because dimensions affect performance and features.
When a mere fraction of a millimeter is considered consequential on the assembly or overall product function, 3D scanning technology comes in handy. A single component is scanned multiple times, each from a different angle, to provide a view from every possible direction. The scanner collects the component’s geometric data to redraw a realistic 3D model. Some 3D scanners used for reverse engineering purposes include CMM (coordinate measuring machines) and structured light digitizers. Industrial CT scanners, the same technology employed in medical imaging, can also be used.
RELATED: How to find an electronic design company for outsourcing new product engineering
CT scanners use X-ray equipment to display the scanned object’s internal and external 3D representations. The automatically reconstructed 3D asset may not be perfect, but the most important thing is that all the essential geometric data are successfully collected and compiled. An experienced AutoCAD drafting and design specialist can further refine the image in CAD software by removing visual imperfections. Refinements should not be a problem if they don’t alter component specifications. Scanning, taking measurements, and final retouching are repeated as many times as necessary to cover all the components used in the product.
The exact process applies when the project involves a PCB for reverse engineering. The electronic prototype and design expert will examine, identify, and uninstall various circuit board components. A typical board contains resistors, capacitors, transistors, inductors, transformers, sensors, diodes, and sometimes LEDs. Each component has a unique specification, which determines features and affects performance. Before deconstruction starts, engineers take close-up pictures of both sides of the board to document the layout and composition.
RELATED: What are electronic manufacturing services (EMS) for new products & prototype design?
All parts are removed in a predetermined sequence and stored in safe places in an organized manner to ensure easy re-assembly if required. Engineers record the dimension of each part and identify the specifications. The step gives a better understanding of how the PCB works and an insight into what every component does. If the purpose is to make a copy of the board, technicians can test their skills by replicating the design after the deconstruction.
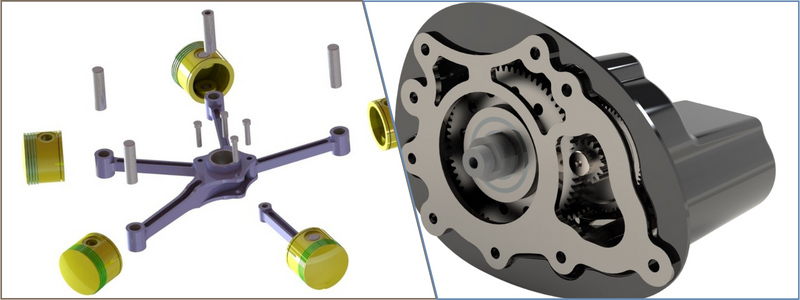
For reverse engineering, it is necessary to take note of the board’s technical details, including but not limited to the materials, trace patterns, wire/lead insulation gap, trace width, and safety certifications. PCB can be recreated as a digital (simulated) file to test the performance and capacity without building a physical board. Most designs can be modified in a simulated environment to test different components and usage scenarios.
Purposes of reverse engineering
Product concept designers or manufacturers utilize reverse engineering to gain in-depth knowledge about how something works. If done correctly, the information gathered during the operation helps create a digital copy of every part, mechanism, and assembly process. It is like having a blueprint of a product. Some of the most common purposes or benefits of reverse engineering are as follows:
Failure analysis
Reverse engineering is most commonly associated with failure analysis. If or when a product fails, the easiest and most comprehensive way to determine the issue is by taking it apart. Once the parts are disassembled and examined, it becomes easier to determine where the problem is, how it happens, and why the issue arises. To repair a faulty product, you must know what’s wrong with the design in the first place.
RELATED: New product design with freelance CAD experts
When reverse engineering is done using CAD software, it is possible to test product performance through a simulation program. A simulation analyzes how a product performs under various conditions, such as extreme heat or cold, careless handling, exposure to water, or normal usage. Performance reports based on simulated runs help inform how to fix the underlying problem.
Legacy parts replacement
Industrial machinery tends to be overbuilt in terms of durability. The machine will perform without a glitch for years, if not decades, before any sign of wear and tear becomes apparent and affects performance. When efficiency decreases noticeably, it may require legacy parts replacements. For example, a food factory has been using a heavy-duty machine to keep the conveyor system running daily for many years. The machine is old now, and one of the components inside is no longer working to its full potential, rendering the production inefficient.
RELATED: The best PCB design software for electrical engineering professionals in 2022
The problem is that the manufacturer no longer produces the component; it has been discontinued, so a custom-made job is in order. Custom manufacturing is not complex when performed by the right professionals with the right equipment, assuming you know which part is faulty. Otherwise, the machine has to be taken apart to determine the issue and pinpoint the culprit. In short, you need reverse engineering.
The machine may have to be deconstructed or 3D scanned to see the internal mechanism. As long as qualified professionals do the work, for example, a team of mechanical and industrial engineers, it shouldn’t take excessively long to determine the problem and find the solution. A CAD designer can create a digital replica of the machine along with all its parts and components, and the defective component is custom-manufactured and installed during re-assembly.
RELATED: Hiring the best electrical engineers & freelance PCB designers
The reverse engineering cost can be more expensive than purchasing a whole new machine, depending on the machine’s size and complexity. The real value of the undertaking is the documentation. Once reverse-engineered, the factory can use the information indefinitely and build replacements for other components as often as necessary. In this situation, it is best to work with a reverse engineering company that can custom-build mechanical components.
Product design improvement
A key driver for reverse engineering is product design improvement. For any company in the manufacturing industry, constant development is the nature of the business. Some companies are willing to reverse-engineer competitors’ products to look into their unique designs. Ultimately, the methods are improved or altered to build alternative variants.
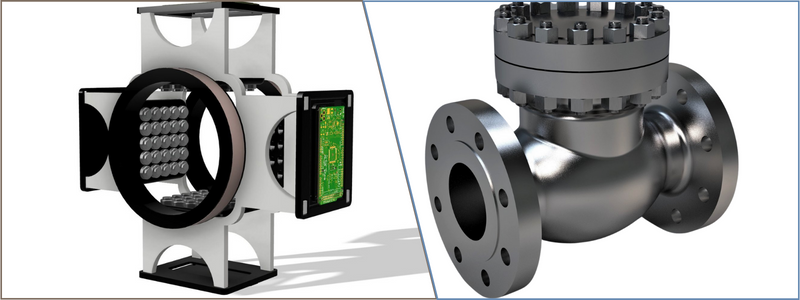
RELATED: How to reduce painful product development costs for your company
Reverse engineering for design improvement does not merely aim to create better components or find product faults. The exact process is employed to simplify the assembly process, reduce any excess by removing unnecessary parts, and ultimately reduce manufacturing costs without sacrificing usability and features. This is where DFM services come in very handy.
System diagnostics
On a much larger scale, reverse engineering helps determine whether an entire system comprised of multiple independent machines—such as in an industrial process—is working at its best. The flow of a manufacturing operation in a factory depends on how well each machine runs. When equipment underperforms, efficiency will suffer, and an excessive load is placed on the interconnected system.
RELATED: Business tips for new product design & development
Large-scale reverse engineering treats and examines the system as a single unit. It is much more complex, time-consuming, and costly than machine disassembly, but the virtual copy can help a company prevent unexpected loss or extensive damage due to one weak link in the chain.
How Cad Crowd can assist
Cad Crowd’s freelance specialists carry the knowledge and experience to help you with 3D modeling and help you connect with the 3D printing, rapid prototyping, and manufacturing services you need to bring your product to market. Save time by reaching out to us! to take to your preferred manufacturer. Check out how it works, or get a quote.