How can you elevate your business using CAD product design services for product development? First things first, a good preface for the discussion that follows calls for a basic understanding of two terms:
Product development
Product development is all the processes involved in bringing a product from being a concept to materialization. A product may refer to physical items, digital goods, or services. Although the development phase technically ends when the product reaches the market, any good company constantly scrutinizes the finished design and implements improvements whenever possible. From the company’s business (monetization) perspective, the development arrives at a complete stop when the product becomes inevitably obsolete. It happens if a significant improvement results in a new design, distinctive from the latest iteration, or a new technology offers a better solution.
Table of Contents
RELATED: Product design guide for freelancers developing an invention
CAD
CAD (computer-aided design) is an umbrella term for various product design activities utilizing specialized computer software. Examples of prominent CAD software include Autodesk AutoCAD, SketchUp, SolidWorks, and Blender. Design activities cover everything from free-form sketching to technical drafting (e.g., architectural and construction plans), from concept drawing to virtual prototyping. CAD is a computerized approach to design, encompassing not only formulation and visualization of ideas in a digital realm but also problem-solving applications. It is both software and a platform for design task collaboration.
Based on the definition above, proper product development must incorporate its entire journey, starting as a mere abstraction to the point of obsolescence. In the old days, when computers were not as prevalent in the design and manufacturing industry as they are today, nearly every new product design began as a conventional sketch drawn on paper. A series of complex 2D annotated drawings provided detailed views of the design from multiple angles. Several physical prototypes were used as proof of concept and for design or performance evaluations. Manufacturing prototyping companies can guide you through the entire product development process.
RELATED: How-to guide: new product design, engineering and prototyping your idea for mass manufacturing
CAD design services
The product development process has remained similar throughout the ages. It begins with a brainstorming session that runs concurrently with market research, followed by design optimization and internal analysis. Every considerable progress typically requires a physical mock-up until the all-approved version is manifested in a final prototype. At this point, the product is ready for mass manufacturing and market launch.
Refinements and updates are mandatory to maintain the product’s competitiveness. Computerization of a product development process also follows the same progression, but it taps into the next level of sophistication with CAD. The “computerization” process used by CAD design firms here refers to two major categories of CAD design services:
- Digitization: a transformation from paper-based information into digital format. For example, an architect converts a traditional blueprint into a PDF or vectorized floorplan image file. Among the obvious benefits include easy modifiability and file sharing.
RELATED: New product development and design: should your company work with a product design team?
Incorporating CAD digitization services enhances digitalization by leveraging specialized software and expertise to convert physical designs and drawings into digital formats. This enables seamless integration with CAD systems, allowing for more efficient collaboration, improved accuracy, and faster iterations during the product development lifecycle.
- Digitalization: the practice of using digital technology to streamline the development process. Implementing digitalization in product design means using advanced digital devices to facilitate every development phase, including ideation, visualization, prototyping, and analysis.
Although some product designs are digitally developed in flat 2D image formats, such as electronic schematics and shop drawings, the most significant advantage of CAD comes with 3D visualization services.
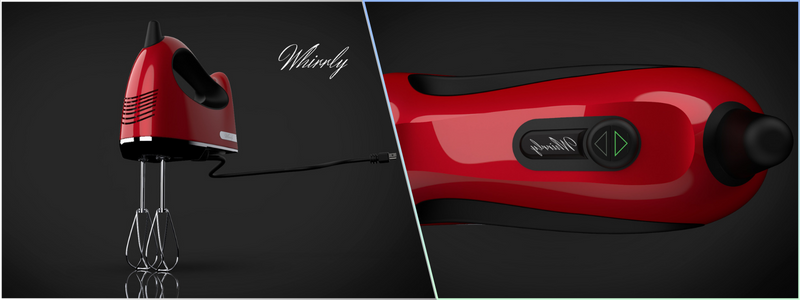
RELATED: Accessible design: better products for everyone
New product development: model-based definition
New product development is not always an easy process. Once the designer identifies an unaddressed demand in the market or a lack of a solution to a longstanding problem, the complex part of the undertaking begins. One of the main reasons is that simply providing a solution will never be enough. Customers also want a user-friendly design wrapped in a durable, practical, easy-to-maintain, and reasonably-priced product. It is safe to say that experimentation with the help of a prototype design engineering expert makes for the most reliable, time-tested, and accurate method to engineer a new design.
However, developing a commercial product through potentially innumerable physical exploratory prototypes does not make much financial sense to any company. Conventional 2D engineering drawings help minimize design mistakes, but they will never reach the level of efficacy as 3D CAD does. Within the general framework of product development, CAD design services heavily emphasize digital product definition (DPD)—more commonly referred to as model-based definition (MBD). Almost all CAD design services in product development revolve around exercising MBD.
RELATED: Do you know the three major types of 3D models?
A model-based definition is extensively utilizing 3D models to determine product design specifications. The 3D models, created and exploited within CAD software, function not only as a visualization tool but also contain metadata associated with the engineering configuration of the design. The attached metadata (or information) defines the specifications for individual product components and assemblies. Also included are bills of materials, design intent, and geometric dimensioning and tolerancing (GD&T).
MBD represents every bit of a modern product development process. The idea behind MBD is to create a rich technical data package (TDP) using 3D product modeling services to contain and deliver product design information. Throughout every development phase, the TDP might receive countless modifications because it is the single source of information used and communicated by the entire design team. For example, when an engineer proposes a design change and updates the model, everyone else can analyze the alteration and improve upon the original suggestion.
RELATED: Why is 3D modeling important for product manufacturing companies?
The same routine is repeated as many times as necessary until the cummulation of ideas and refinements translates into real progress. In other words, the 3D models serve as the authoritative source of information that drives all design and engineering activities. At the end of the process, the final 3D models are true digital representations of a technically viable and financially feasible new product. Suppliers, manufacturers, and regulatory bodies may share the same data package further downstream if needed. There is no need to create multiple data packages.
Using a CAD digitization studio —within the scope of MBD practice—can facilitate a “near completion” product development process using 3D models. With the exception of physical prototyping and manufacturing, MBD is an adequate replacement for the traditional approach to product development. The range of data generated in the 3D models helps reduce the time spent on design documentation.
RELATED: Crowdsourcing new product design and 3D modeling
More importantly, it eliminates unnecessary complexities in engineering and manufacturing validation. In addition, the spatial construct of a 3D model is easier to understand as humans naturally see every object with both eyes in 3D. With detailed technical annotations, the visualization minimizes the chances of misinterpretations and leads to well-informed, efficient design-related decision-making.
Automation with design intent
A massive advantage of MBD with 3D modeling over traditional 2D drawings is the accurate, automated, clear visualization of design intent. During the early days of CAD (pre-1990s), mainstream computer software was mostly replacements for conventional drawing boards. Productivity was increased as engineer companies could produce accurate technical 2D drawings in digital formats. CAD software could display design geometry, but the model did not contain much information other than dimensions.
Thanks to the advent of 3D CAD, the models are realistic virtual representations of a design. CAD software can generate a greater amount of data contained within the model file itself. In addition to geometric information, the model contains technical specifications such as material, density, and location of every part and component. Furthermore, the data covers the parametric relationships between the features.
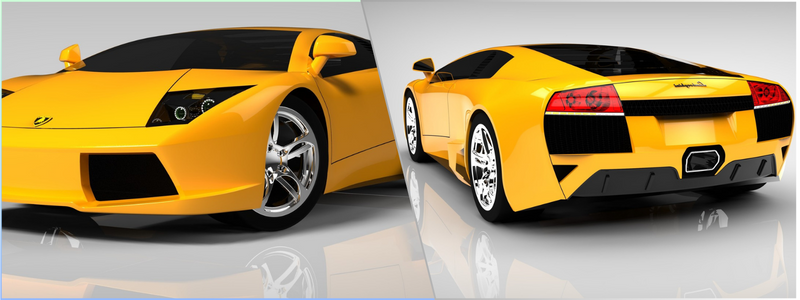
RELATED: How to design 3D models for 3D printing & new prototypes
The software allows for easy modification or removal of any of the data. When a data point is modified, the entire model updates itself accordingly. Engineers can use the parametric relationships and determine the design intent early in the 3D modeling work. The purpose is to simplify alterations without decimating earlier progress.
Efficient collaboration
Using only a single set of 3D models that contain all the necessary information, a company in the middle of a product development process can do away with less redundancy; hence, more free resources at the invention design team’s disposal to spend on the primary task at hand. Regarding design documentation and communication, using paper-based drawings often adds an unnecessary burden to the development cycle. A simple modification or update to the 3D model doesn’t have to necessitate changes to paper documentation. The time it takes to maintain the documentation and communicate the changes hampers progress.
RELATED: From idea to reality: turning your invention into a product
At the same time, MBD does not mean going completely paperless. There will always be some paperwork involved but much less than the conventional method. A centralized digital data center allows for efficient collaboration among the stakeholders. It improves the company’s ability to maintain quality standards, both in the development process and the final product. Subsequent design improvement after the market launch can reuse the same 3D models as reference points to speed up progress.
Physical prototype
Every new product materializes as a prototype before becoming the ready-to-market version. Once again, with the assistance of prototype design engineering, CAD design services transform the otherwise time-consuming and resource-intensive physical prototyping into an efficient undertaking. Instead of turning to injection molding techniques, the company can use the same digital models for 3D printing.
RELATED: 10 Tips on how to find the best prototype engineering firm services
Additive manufacturing services has reached a point where it can print complex parts with metal materials. Once the digital models are approved, engineers can proceed to the final prototyping phase. The models must be converted into a print-friendly file format, and the printing process itself can take almost a full day, depending on the product’s complexity. It is faster and more practical than injection molding or CNC machining.
How Cad Crowd can assist
Cad Crowd is simply the best place to get invention design help, whether it’s product design, drafting, patent services, engineering, 3D rendering services, or prototyping. Learn how it works or get a quote to start working with us today.