It is a broad question with no single correct answer. Combining a functional PCB with a hardware product design is practically building an electronic product. And just like the question in the beginning, it is a broad category of products, from a simple everyday device like a USB drive to a state-of-the-art avalanche probe.
Developing a USB thumb drive design takes little more than purchasing ready-made flash drive boards and connectors. Then, you can get creative with the enclosure design using CAD software and a consumer-grade 3D printer. Since you don’t need to hire an experienced mechanical engineer to lead the project and partner with a custom prototype maker, the overall development cost for the new enclosure will not exceed several hundred dollars.
The latter is at an entirely different level of sophistication. Take the AvaTech SP1 Smartprobe as an example; the GPS-enabled device connects to a user’s smartphone via Bluetooth and is equipped with an accelerometer and an inclinometer as well as a ranger finder – all in addition to a whole bunch of optical depth sensors and a custom digital force sensor. It collects data from the surrounding environment and sends them to the smartphone to help the user avoid triggering an avalanche when skiing. It probably took the company around a million dollars to have it developed, tested, and certified. In general, simple consumer electronic products are less expensive to build and bring to market than complex, specialized, high-tech solutions.
Table of contents
Hardware design cost and PCB prototyping rates
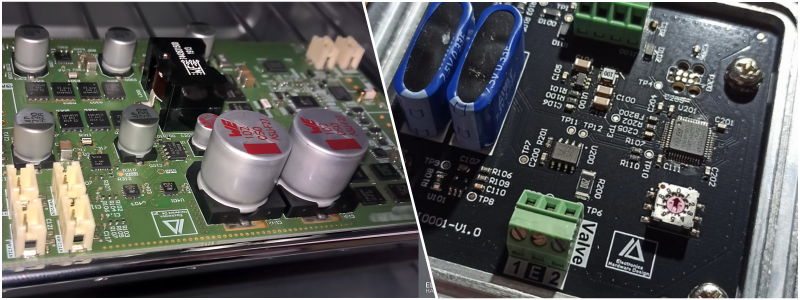
The scope of the term “hardware product design” must be clearly defined as well. Building an electronic product with a 3D printer and a prototype platform, such as an actuator kit, should not require more than $50,000 upfront investment. However, you may need anywhere between $200,000 and $300,000 to make the product at least presentable to potential buyers. The development requires a thorough product design process and plenty of engineering input, so much money goes to hiring mechanical and electronics engineers. If the plan is to prepare the design for mass production, you may need an even more significant investment.
Design complexity is among the most significant factors affecting development costs. While a large company can afford to have a few failures during market readiness, a small startup should focus on keeping things simple to avoid costly mistakes.
RELATED: How to develop a new electronic hardware prototype & products for your company
Design studios
A complete range of product development services from a small design studio can cost up to $60,000 for concept creation, 3D modeling, physical prototyping, and testing. An electronic product with a user interface via screen or mobile app requires software development, which can easily double the investment requirement.
Freelance engineers
Hiring freelance engineers is more expensive than partnering with a design studio regarding electronic product development. To build a quality product design, you need a dedicated team of at least a mechanical, electronics, and software engineer. A project manager is also necessary to oversee the process and collaboration. A software engineer is required when the product is supposed to work with a computer or smartphone; otherwise, it is a permissible omission.
PCB prototyping requires firmware integration, a task best left to the electronics engineer. Firmware is low-level software embedded in PCB hardware components, whereas an app is high-level programming typically handled by computer scientists or software engineers. For most electronic products, app/software development is only necessary after going through PCB prototyping and firmware integration stages.
In other words, a small design team of mechanical engineers and electronics engineers alone should be enough to get the job done up until the point of PCB prototyping. Hardware/enclosure development occurs after PCB prototyping because both parts must be fitted to each other. If the PCB layout features USB ports, audio jack, buttons, and knobs, the enclosure needs to accommodate the parts. According to the BLS, the typical rates for electronics and mechanical engineers are as follows:
Hourly rates
Occupation | Lowest 10% | Median | Highest 10% |
Mechanical Engineers | $29.80 | $46.30 | $72.72 |
Electronics / Electrical Engineers | $36.00 | $52.00 | $82.42 |
Since the data is based only on the pay rate of mechanical and electronics engineers in the United States, the most significant factor between the hourly rate gaps is the experience level instead of location.
The hourly rates are manageable. You must consider the expected development timeline until a functional PCB is prototyped and a hardware enclosure is built. An electronics engineer must complete a series of procedures before a layout is ready for prototyping. Such methods include producing a Bill of Materials based on preliminary evaluation, drawing schematics, and designing the PCB layout. The whole process can take several months. After the PCB prototyping, the electronics engineer performs the firmware integration; these tasks need another month to complete.
A mechanical designer begins the work by drawing a 3D model of the enclosure based on the dimensions and specifications of the PCB prototype. You will have to wait at least a month for a simple enclosure design and up to 6 months for a complex one. Access to a 3D printer can speed up the enclosure prototyping work, which should not take more than a week. Preparing the design for mass production, usually with injection molding technique, can be a tedious 4-week process.
RELATED: New concept design costs, engineering prices & product development services rates
Professional product design services
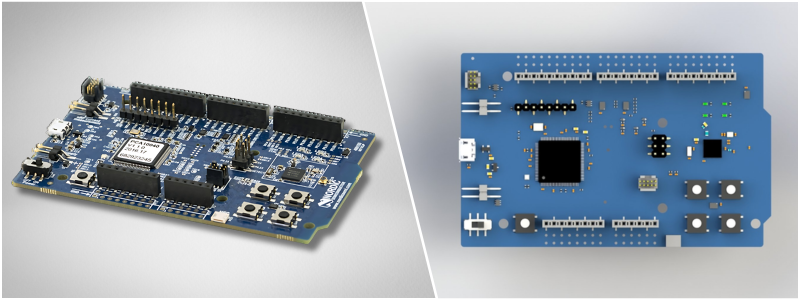
Most product development firms offer a complete range of services, including PCB prototyping, encompassing the typical step-by-step progression of a hardware design creation.
- Concept evaluation: At the end of a concept evaluation phase, a design firm should develop several design iterations based on your original idea. The point is to revise your idea and improve a rough design into its best possible refined version. Good communication is the key to ensuring that you and the firm are on the same page so the project may progress quickly.
- Product schematics: the design firm produces a Bill of Materials based on the product schematic drawn on a computer. BoM lists all electrical components and materials required to build the product. It is the part where you get a clear idea of how much it would cost to develop an enclosure design and build a PCB inside it.
- PCB layout and enclosure model: an electronics engineer creates a digital PCB layout. The software will verify the design at the end of the process to see whether the configuration is correct and by the schematic. At the same time, a mechanical engineer produces 3D models of the enclosure design. Development for the enclosure goes slowly during the early stages, but it picks up the pace once the PCB prototype is ready. The 3D models function only as visualizations. You can also order a lifelike render if needed.
- PCB prototyping: The PCB prototype takes about a week to complete. Generally, be prepared to have 3 – 5 PCB layout prototypes for the first run. You need another prototyping run after some tests, evaluations, and revisions to fix potential functionality issues. Increase the order quantity to have enough product samples for different experiments.
- Embedded firmware: an electronics engineer starts the hardware/firmware integration to establish connection and communication among the components.
- Enclosure prototyping: The 3D models are revised according to the PCB specification and dimensions. A mechanical engineer builds the design on CAD software and sends the file to a 3D printer. If your enclosure is supposed to have metal parts, the prototyping process needs to involve a CNC machine.
- Certifications: The design firm can help you apply for the certification process through recognized bodies such as FCC, CSA, and UL. Most certifications are voluntary.
- Documentation: if packaging is not needed, the design firm can go directly to the documentation work to produce various documents such as instruction manuals, warnings, and maintenance recommendations.
RELATED: Consumer electronic product design services: costs, rates, and prices for freelancers
A product design firm does not usually provide mass-production services. However, it will be willing to help you find a potential factory partner to manufacture the product in large volumes. Depending on the design, some additional work might be required before you can proceed to the manufacturing step. For example, a plastic enclosure requires an injection molding technique. The design firm will design the mold and have it fabricated.
End note
Product development is not something to take lightly. The development cost will be your biggest obstacle, but it won’t be your only challenge. There is a long road from a design concept to a tangible product. For a small company, developing a new hardware product can be a considerable investment, especially when the product is an electronic device with embedded firmware or mobile app integration. Having an experienced design firm or a team of mechanical and electronics engineers on your side can make the difference between the efficient development of a feasible design and a significant money drain.