Indeed, in the competitive market of today, product design goes beyond creativity and functionality but also involves how something can be made more efficiently. A deep understanding of manufacturing processes, materials, and supply chains informs designing easy-to-manufacture products at low cost, and scalable designs – Design for Manufacturing (DFM) comes into the scene here. By incorporating DFM principles early in the design process, companies can streamline development, reduce costs, and improve the overall efficiency of their product lifecycle.
In this article we will outline the need for DFM, the guiding principles driving it forward, and practical strategies to help your firm gear up product designs for manufacture. Whether you are a startup or have an existing business, the adoption of DFM practices will yield significant pay-offs for your firm.
Table of contents
What is design for manufacturing (DFM)?
Design for Manufacturing actually becomes a practice of designing the product with manufacturing processes in mind, making the product easier, cheaper, and quicker in production. DFM focuses on simplification of the product design to reduce its complexity, to improve the manufacturability of the product and at the same time minimize costs in the course of production. It requires a collaborative approach between the design, engineering and manufacturing teams as the specifications of the product have to be compatible with the capability of the selected manufacturing process.
The ultimate intent of DFM is that the design-to-production gap is as low as achievable without the costs being too high and production time too long. Done right, DFM can be an effective means to minimize waste, utilize material resources more efficiently, improve the quality of products, and better the overall manufacturing process.
RELATED: Contract manufacturing services vs. manufacturing services

Why is DFM important?
Introducing DFM in the design process provides your company with immediate benefits, especially when it comes to costs, savings, and a whole lot of efficiency.
1. Better collaboration
DFM encourages cross-functional collaboration between design engineers, manufacturing experts, and procurement teams to ensure all stakeholders understand the potential issues and constraints during the production process. More efficient designs, therefore, are achieved.
2. Cost minimization
Design with manufacturing in mind may result in unnecessary costly revisions and complex processes. Substreamlining of the design process reduces costs produced in assembly time, labor, and raw materials. Much simpler designs are composed of fewer parts that can be simpler to manufacture; hence lower aggregate costs.
3. Speed to market
A product designed to be more manufacturable moves quicker from the design stage to the production one. It helps a company shorten its development process and avoid a long time taken between design stage and production, thereby launching products in the market much faster with fewer changes in the design that could be brought about.
4. Better quality products
DFM ensures that designs are manufactured within the specified tolerances and materials, which makes for better quality consistency in products. It becomes possible to ensure that products designed with manufacturing constraints in mind have fewer defects, higher precision, and better durability when produced.
5. Scalability
Products that are designed for manufacturing efficiency are easier to scale up. Whether you produce hundreds or millions of units, a well-optimized design can facilitate a smooth transition to large-scale production.
RELATED: 8 tips companies use to simplify design manufacturing or design for manufacturing
Key principles of design for manufacturing
For optimal product design for manufacturing, an understanding of the principles that form the foundation of DFM is essential. These principles focus on reducing complexity while promoting an optimal material consumption that is also aligned with manufacturing capabilities. Explore the following set of critical core principles of DFM:
1. Take into consideration material cost and availability
Material selection becomes another critical aspect of manufacturability and, therefore, cost. DFM encourages designers to use materials that are more readily available, less costly, and easier to process. Of course, the exotic materials may have some unique properties because they could be much more costly than others, with longer lead times and more complex processing.
Selection of materials commonly used in the industry can limit the production time hence the cost of manufacturing. An example can be choosing such metals, plastics, or composites which are more commonly used in the industry to bring down the material costs and ease the procurement.
2. DFA: Design for assembly
Design for assembly centers attention on reducing time to assemble a product, making the manufacture more economical. To guide the process, principles of DFA require you reduce the number of parts and eliminate features that complicate assembly.
For example, you might design parts to self-align easily at assembly (by exploiting symmetry or self-locating features) or select fasteners that are less labor-intensive to install. Reducing the steps and complexity of the assembly process reduces labor cost and opportunities for error.
3. Design for testability
Testability at the design stage will ensure that a product can be tested for quality and performance to quite an extent before and during its production. Testability is the designing of products to where they can be inspected for fault or disparities in the manufacturing process.
Manufacturers can, therefore, include clear points of inspection, accessible test features, or even functionalities with built-in tests in their designs to ensure fewer faults in the manufacturing process and thus an even more coherent production line.
4. Focus on tolerances
Tolerances are the allowable dimensions variations that a part can have at some level of production. Tight tolerances can raise the difficulty level as well as cost of manufacturing. DFM recommends designing parts with tolerances achievable and needed for the function of the product.
By making careful evaluations on the tolerances required, designers will avoid overengineering and extra costs that may come with precision manufacturing. It may also help in avoiding delays due to quality control issues or parts that do not comply with the specified requirement.
5. Reduce manufacturing processes
Every manufacturing process adds to the cost and the complexity of the production cycle. DFM encourages designers to consider the least number of different manufacturing processes that will be required to create a product. For example, instead of designing a part that needs to be cast, machined, and then assembled, design it to be made by one single, more efficient process.
This reduces the number of processes involved, so, therefore, manufacturing cost is reduced and the possibility of errors or defects. It also pushes the designers to think of how much more of the product can be produced in the same process that brings down the setting up cost and improves efficiency.
6. Reduce design complexity
One of the simplest tenets of DFM is simplification. The more complex the design is, the harder and more expensive it is to manufacture. A design may become simpler if it eliminates features that have no meaning, reduces the number of parts, or makes use of standard parts. A design should be functional but easy to produce.
For example, rather than combining the same function into various small components that require assembly, designers can opt for one component that encompasses the exact functionalities. This reduces the time for assemblage and lowers labor cost and the probable errors of the time of production.
7. Standardized components
The use of standard parts and materials significantly reduces the cost of a firm’s production since custom fabrications are no longer needed. Standard components can be sourced easily, are cheaper, and are usually proven to work under the constraints of most manufacturing processes. They also make it easier to manage inventories and lead times.
Designers should opt for the off-the-shelf components and those that can be produced by more prevalent processes, rather than designing special components that might need specific tools or machines. This not only saves material and tooling expense but also reduces the time-to-production end.
RELATED: DFM for new product design excellence: complete guide for company success
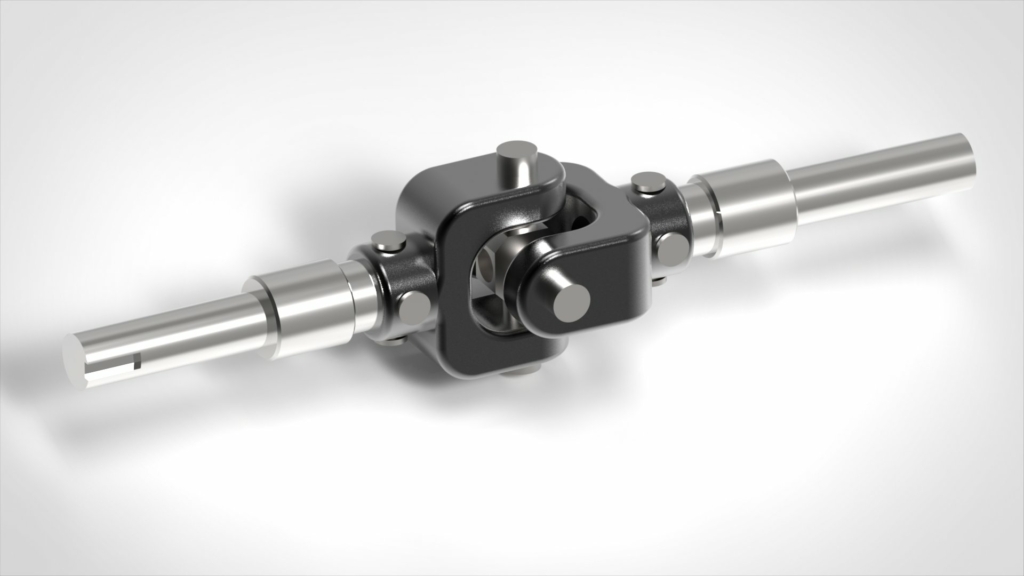
Practical approaches for implementing DFM in your organization
Having now outlined the main tenets of DFM, let’s review some practical steps your company can take to implement the principles outlined above in its product development process.
1. Conduct a DFM analysis
After completing the preliminary design, do a detailed DFM review. Through this review, assess whether the product is complex or not; whether it can be manufactured; material selections and methods of assembly. A cross-functional team of engineers, designers and manufacturing experts can examine the design if it accommodates the principles of DFM and make necessary adjustments.
2. Engage manufacturing at an early stage in design
Good DFM practice requires close collaboration between design and manufacturing teams. Involve the manufacturing team as early as possible to ensure the product design meets available processes and equipment. Collaboration on product design can lead to early identification of potential manufacturing challenges, giving the design team the opportunity to modify the product to make it easier and less expensive to manufacture.
3. Iterate based on feedback
Design is a repetitive process. Once feedback from manufacturing, testing, and quality assurance is received, keep modifying the design to become more manufacturable. Constant improvement allows your product to remain affordable, functional, and of high quality throughout the transition from concept to production.
4. Prototype and Test
Once the product design is optimized for manufacturability, think of building a prototype. Compiling and testing by various means will be a great way to verify your design and assess if it can be scaled up into production levels without the occurrence of problems. This helps bring out unforeseen problems that possibly might not have been seen in the design stage.
5. Leverage DFM software and tools
Use software-specific tools that aid DFM analysis. More and more software-based platforms permit the simulation of manufacturing processes and let experts assess the feasibility of a product. Such tools can be very helpful in pointing out potential flaws in design before the stage of production, saving much time and money in the process. This also enables them to identify certain areas where material use or manufacturing processes may be optimized.
RELATED: What are new product development costs, design services rates, and pricing for your company?
Wrap up
Preparing your firm’s product design for manufacturing is essential for cost-effective and efficient production. Embracing Design for Manufacturing principles will help you streamline the development process, reduce the production cost, improve product quality, and accelerate time-to-market. The main ideas are to simplify designs, use standardized components, avoid manufacturing processes, and integrate the right teams at an early stage.
How Cad Crowd can help
When done right, DFM improves the manufacturing process of your business and, by extension, your business performance as a whole. With proper planning and collaboration, you would optimize your designs for functionality and manufacturability for long-term success in a competitive market. Count on the name Cad Crowd. Request your quote today.