Architectural construction plans, shop plans, and as-built plans are all important for a variety of reasons. These plans have different purposes, address different stakeholders, and have different roles to play during the project cycle. As a contractor, architect, or services company with a focus on these types of services, understanding the differences can simplify project workflows and enhance communication.
Cad Crowd is a standout in the industry when it comes to architectural construction drawings, shop drawings, and as-built services. Cad Crowd will give you proficient experts who will help your company with its next ventures.
🚀 Table of contents
Architectural construction drawings: the blueprint of intent
Architectural construction drawings are the foundation of every construction project since they are the intent of closing the gap between design and build. They represent the architect’s vision, an actualization in the form of the overall intent design that drives every stage of construction. They are not only works of beauty; they are technical plans in the form of detailed information imperative in realizing an idea design into reality.
Most important features of architectural construction drawings
- Focus on design: At the heart of architectural construction drawings is the architect’s creative and functional design. They represent both the aesthetic desire and functional requirements of the project. These comprise spatial planning, with an aim towards efficient utilization of space and adherence to local building codes and standards. The drawings describe how the building is going to look and operate, taking aspects such as lighting, flow, and accessibility into consideration.
- Extent of detailing: These drawings include many details necessary in the construction process. Besides the standard floor plans and elevations, they have structural plans showing load-carrying members, electrical and plumbing plans symbolizing wiring and piping routes, HVAC systems, and even landscapes where applicable. The extensive detail ensures every element of the building is planned and coordinated well.
- Guidance tool: Architectural construction drawings serve as crucial guidance tools for contractors, engineers, project managers, and construction workers. They provide precise instructions on what to build, how different components fit together, and what materials to employ. By providing clear and detailed visual representations, these drawings made by architectural design firms help minimize misunderstandings and errors during construction.
RELATED: How CAD technology is transforming the future of architectural design services companies
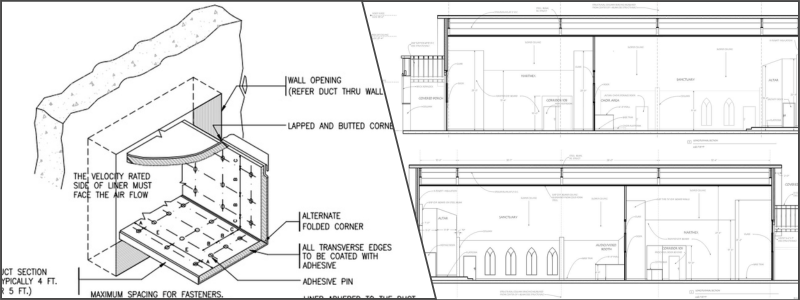
Standard components of architectural construction drawings
- Floor plans and site layouts: Top-down illustrations of how areas within the building are arranged, i.e., room dimensions, where walls, doors, windows, and equipment are located. Site layouts further the view to include where the building is in relation to the surrounding site, including parking lots, access, and landscaping.
- Elevations and cross-sections: Elevations provide a view from the front of each facade, illustrating the exterior look of the building, including materials, textures, and architectural elements. Cross-sections cut through the building to reveal the inside construction, illustrating relations between floors, rooms, and building components.
- Structural, mechanical, and electrical details: These types of building blueprints explore aspects that have to do with the way the building should be assembled. Structural drawings focus on the importance of the body of the building, i.e., beams, columns, and foundations. Mechanical drawings touch upon HVAC systems, while electrical designs cover wiring, outlets, and lighting configurations.
- Specifications of materials: Detailed notes and schedules specify material types to be utilized, as well as quality, finishes, and installation techniques. This assists in ensuring conformity and ease in procurement and estimating costs.
Service firms importance
Construction plans are largely reliant on architectural services companies in an effort to provide accurate and efficient project outcomes. Such plans play a crucial role in:
- Cost estimation: They provide the detailed information needed to create reliable budgets, including material quantities and labor requirements.
- Construction planning: By defining construction sequences and processes, they help schedule tasks, allocate resources, and manage time effectively.
- Regulatory compliance: Building drawings guarantee that the project is in compliance with building codes, zoning regulations, and safety standards, reducing the likelihood of legal disputes or costly changes.
- Contractual basis: They are binding agreements in contracts between clients, architects, and contractors, defining the scope of work and expectations for the delivery of the project.
Ultimately, architectural site plan services are responsible for not just blueprints but the keystone to successful building, bridging an architect’s vision to a buildable, structured entity.
RELATED: Techniques for 3D architectural visualizations and tips for your services firm
Shop Drawings: the fabrication blueprint
While building plans provide a general design overview, shop drawings focus on the minute details needed for fabrication and installation. Drafted by contractors, subcontractors, manufacturers, or specialized drafting companies, shop drawings are the critical link between architectural concepts and real construction. They translate the architect’s intent into actionable plans for specific building components so that every detail is accurately captured before it’s delivered to the job site.
Key features of shop drawings
- Exact specifications: Shop drawings focus on detailed details that may not be given importance by construction drawings. They give exact dimensions, manufacturing specifications, material specifications, and installation procedures for components like structural steel beams, HVAC units, cabinetry, electrical panels, and piping. These specifications allow manufacturers to create items accurately and with little scope for interpretation or error.
- Technical accuracy: Shop drawings differ from general design plans in that they contain very technical information. They specify fabrication methods, welding details, screw and bolt locations, assembly procedures, and tolerable deviation. This degree of accuracy guarantees that parts fit together perfectly when installed, ensuring the integrity of the overall design.
- Review and approval process: Shop drawings are strictly reviewed and approved by architects, engineers, and project managers. The tiered review process checks that the drawings meet the original construction documents and project specifications. Differences are identified and adjusted before fabrication to prevent on-site mistakes and delays, which are extremely expensive.
Elements of shop drawings in common
- Accurate illustrations of prefabricated components: These plans show individual elements and assemblies, illustrating how every element is integral to the complete structure.
- Material grades and finishes: Shop drawings services clearly indicate the materials to be utilized, including grades, coatings, and surface finishes, to meet functional and aesthetic requirements.
- Installation instructions and connection details: They give sequential instructions for the assembly and installation of elements, including connection techniques, anchor locations, and interface information with other structural components.
Significance to service firms
Shop drawing service firms are essential in bridging the gap between design and construction. Their experts ensure each part is manufactured with accuracy, minimizing errors and conserving materials. With precise instructions, these drawings optimize on-site productivity, allowing construction crews to work faster and more effectively.
Besides, accurate shop drawings can reduce project costs significantly. They allow problems that might arise during construction to be established from the start, saving costly time and effort on rework. In complex projects such as high-rise buildings or factories, the significance of accurate shop drawings cannot be overstated—they are crucial in the maintenance of project schedules and the structural stability of the build.
Short of being mere technical documents, shop drawings are the foundation on which successful fabrication and installation rest. By their capacity to interpret architectural imaginations and translate them into accurate, actionable plans, they ensure all components fit hand in glove, function as designed, and serve to enhance the quality of the finished building.
RELATED: Top tips you need to know for choosing a BIM company for architectural design & CAD services firms
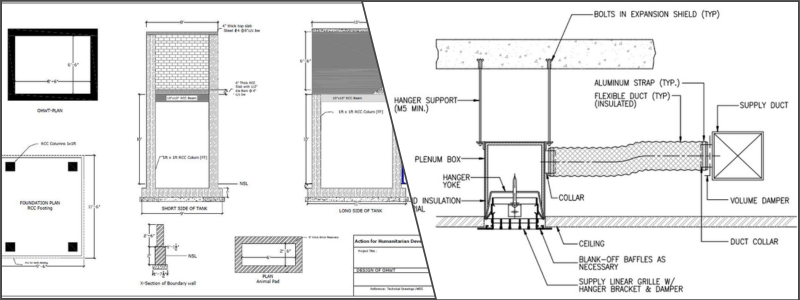
As-built drawings: the record of reality
When the dust has settled, and the construction phase is nearing completion, as-built drawings are an integral part of the project records. These important documents record the “as-is” condition of the completed building, including all the changes and variations from the original building plans. Unlike design blueprints, which are the hoped-for vision, as-built drawings services depict factual and detailed descriptions of what has been built.
Key features
- Recording changes: One of the primary reasons as-built drawings are employed is to record all changes that take place during the construction process. These changes can include dimension changes, material changes, location changes of mechanical, electrical, and plumbing systems, and unforeseen adjustments required because of site conditions or design changes. Construction projects have real-world conditions that demand decisions to be made on the spot, and as-built drawings assist in recording these decisions in detail.
- Detailed records: As-built drawings are not sketches. They include detailed annotations, redlines, and comments showing deviations from the original plan. These records form a middle link between original plans and final results, giving a comprehensive overview of how the project went. The fine detailing is such that all changes, however small or big, are captured for posterity.
- Facility management tool: As-built drawings are a treasure trove for facility management, being a major tool for future repairs, renovations, and maintenance. They provide an accurate record of the built environment, allowing property managers, maintenance personnel, and contractors to understand the conditions as they exist without guesswork. From locating hidden utilities to designing new installations or resolving issues, as-built drawings serve as a point of reference certainty.
Common components
- Final floor plans, elevations, and sections: These are the final layout and any modifications from the original design. 3D floor plan design services provide a clear image of the spatial relationship and structural details.
- Final locations of structural, mechanical, and electrical systems: The accurate location of these systems is crucial for future building. As-built drawings indicate where pipes, ducts, wiring, and support structures are actually located, which may vary from the initial plans.
- Deviation notes from original specifications: Comprehensive notes describe why some changes were implemented, giving context that can be useful for future projects or legal purposes.
Significance for service companies:
As-built services companies specialize in creating these detailed reports, offering documentation that makes facility management, legal compliance, and future project planning easier. They are a treasure to property owners, maintenance staff, and renovation contractors.
Accurate as-built drawings can make renovation projects run more smoothly, save money by preventing surprises, and ensure that any changes comply with safety and building codes. Furthermore, they can serve as legal documents, attesting that construction was in accordance with contractual requirements and regulatory requirements.
In brief, as-built drawings are greater than end-of-construction blueprints; they are the ultimate snapshot of a project’s existence. Their accuracy and detail make them a treasured resource for anyone involved in a building’s life cycle, from construction and management to renovation and even demolition.
RELATED: Marketing real estate: top real estate 3D rendering trends for companies and firms
How service companies address these differences
Service companies that specialize in architectural drawings, shop drawings, and as-built documentation must be sensitive to the specific demands of each. This is how they effectively obtain these differences:
- Specialized expertise: Each of these kinds of drawings typically has its own dedicated personnel at firms so that employees with the right expertise perform specific work.
- Workflow integration: Seamless workflow between design, fabrication, and construction documentation teams reduces errors and ensures consistency across project phases.
- Technology utilization: Advanced CAD design experts, BIM software, and cloud-based tools allow for efficient drawing-making, checking, and managing.
- Quality check: In-depth checking procedures confirm cross-checking of drawings against project requirements, building codes, and site conditions.
Cad Crowd is here to help
Understanding the distinctions between architectural construction drawings, shop drawings, and as-built drawings is not merely an intellectual exercise—it’s a necessity for anyone who works with construction projects.
Cad Crowd has worked with tons of architectural, real estate, and design companies to find the best-outsourced talent as an industry-leading platform. Contact us at Cad Crowd today for a quick and easy free quote.