Product development is expensive, time-consuming, and, most of the time, unpredictable. No matter if you’re a small start-up or developed enterprise, managing cost while ensuring quality and efficiency means so much to a company’s success. One practice that can help many companies save massive amounts of money in developing products is pre-production prototyping, an important offshoot of prototype design services.
Pre-production prototyping refers to the process by which a working model of the product is made before it is actually launched to the public. The designers, engineers, and all the other interested parties take a prototype that enables them to conceptualize and experiment with the product idea in the most realistic way possible. It allows for problematic areas to be identified and solved early on at a non-high-quality manufacturing investment. Fewer revisions may be expected, and risks will be considerably reduced with huge savings over time.
This article explores many ways your company can use pre-production prototyping to save on product development. It can make both your product quality and your bottom line better, too.
🚀 Table of contents
What is pre-production prototyping?
Pre-production prototyping is the first version designed to check the functionalities and capabilities of the product before releasing it to the market. For pre-production, there can be several prototypes involved, such as 3D printed models, mock-ups, and a small batch of functional prototypes. Testing the functionalities of a product is helpful in identifying the possible design faults and optimization needed before the actual launch. In this way, the final product will be able to satisfy the company’s standards and target the customer’s requirements.
RELATED: Benefits of AutoCAD for electrical drawings with freelance engineering services & companies
How pre-production prototyping saves money in product development
Early detection of design flaws
Flaws in the design during the early stage can lead to a serious, costly problem in product development. There will also be a possibility to multiply once the product is placed under mass production, resulting in costly recalls, wasted materials, and even slight damage to a brand’s reputation. Companies can detect design flaws through pre-production prototyping prior to mass production.
The prototype is the first actual model of the product, where the designer and engineer will test if it would work, how it will look, and if it is ergonomic. They would then recognize which issues were perhaps a poor fit and finish, durability problems, or user interface issues. That way, errors can be caught at the prototype phase before costly changes later on.
Example: Consider a consumer electronics company launching a new product. A prototypical version created before actual production may provide engineers with the idea that the button placement for this device is impossible to use when held in one hand. Correction at the prototype saves the firm from redesigning at the production phase, which would cost that much money.
Reduced possibility of manufacturing defects
Manufacturing defects can be very expensive if discovered after producing hundreds or thousands of units. Prototyping pre-production tests the product’s manufacturability, hence determining if the design is scalable enough to meet mass production requirements. Companies can discover possible bottlenecks in manufacturing, inconsistencies in materials, or problems in assembling.
The earlier the problems are detected, the sooner they can adjust the design or the manufacturing process before full-scale production has begun and a large-scale defect is discovered that would cost much to rectify.
For example, in inventing a novel form of wearables, this company can ensure beforehand whether the material chosen is mouldable or leads to problems upon mass assembly through prototype pre-production. Thus, if this prototype shows issues arising, it is possible to amend the material type itself or the product design without wasting money on reworks and delays for wearable design services.
Cost-effective iterations
The process of product development often requires a few iterations, whereby designs are reviewed and changed based on testing and feedback. Pre-production prototypes can achieve this through iterations that don’t cost much since the prototype can be modified and adjusted according to early-stage feedback without investing in costly tooling or production changeovers at scale.
The actual cost of modifying a prototype is usually much lower than that of reworking a product into mass production. This is because the prototype is usually produced in small quantities, so you can easily make adjustments without incurring the significant costs associated with a production run.
For instance, a furniture house with a new product line may use this pre-production model to try many different materials or finishes. That facility can quickly prove multiple iterations on a design but not commit to a large volume of production. All this helps save the company that much more over time before getting into large productions through furniture design services.
RELATED: Essential product design checklist when working with freelance experts & services companies
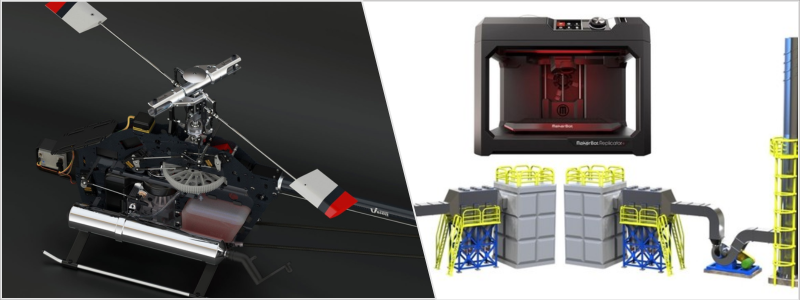
Better communication
Effective communication between stakeholders is important for product development professionals. Pre-production prototyping provides a tangible representation of the product, which can be used in meetings with investors, customers, or suppliers. This helps stakeholders better understand the product’s features, functionality, and potential for success.
Using a prototype also aligns all the parties on what the product design and goals should be, thus lowering the chances of misunderstandings or disagreements. It can prevent delays or misaligned expectations that would cost much more later in the development cycle.
For example, when making a new tech gadget, a pre-production prototype developed during this process can be used to pitch the idea to a potential investor. It has been viewed as instilling confidence in the product as well as its feasibility, thus creating funding support for development costs.
Production process optimization
Prototyping before the shift from the prototype stage to the mass production stage is done in order to test the actual manufacturing process. The effort will find problems in tooling, efficiency of the assembly line, and logistics for manufacturing design services. These issues can be smoothed out well before the full production run so that the business will not experience delays or unnecessary costs during the transition from development to mass production.
Another use of pre-production prototypes is in testing packaging and shipping methods to ascertain that products get to their destination safely and incur minimal transportation costs. Packaging failures may be corrected before many products leave the manufacturing station.
For instance, a new developing company for a kitchen appliance can use the prototype before production to test their assembly line to make sure that it is not only efficient but cost-effective. They might even test the packaging to make sure that the products will reach the retailers without any damage and thus save on return costs or on damaged goods.
Validating market demand
Pre-production prototyping enables validation of market demand before large-scale investments in production. A company might use the prototype to develop marketing materials early or pilot small-scale programs, as well as undertake user testing as a means of understanding the direction of interest that customers will exhibit.
This allows firms to avoid overproduction and decreases the likelihood of investing in a product that would not be sold. It means that knowing what exactly the market requires, the production quantities will be optimized to prevent waste from being spent on unsold inventories.
Example: A fashion brand can use fashion design services to make a prototype pre-production of a new clothing line and display it to a small group of consumers. This pilot run will enable the company to gauge interest, ensuring that only products most likely to sell are produced, thus eliminating more risk of excess inventory.
RELATED: How much does PCB assembly cost? 5 expert tips to reduce rates and pricing for design companies
Improved time-to-market
One of the prime advantages is reducing the time to market for a product. Prototyping before the actual start of production gives companies the opportunity to identify problems at an early juncture. At this stage, this will help bring fewer delays in the latter portion of the product development cycle. A smoother product development cycle has a faster time-to-market value, which, in turn, can be cashed into profit.
Early testing and validation of the product also means that any necessary adjustments are made before they become time-consuming and expensive. Your company will move from concept to production more efficiently by getting it right the first time, keeping costs down and ahead of competitors.

Better product quality
Thus, through prototype development and testing prior to full production, this method of prototyping in pre-production ensures an end product is better. A quality product would not have too many returns or need to be repaired or be dissatisfied with customers, thereby proving costly in the long term.
Investment in the pre-production prototype and refinement based on real-life feedback ensures that it meets the customer’s needs and industry benchmarks, thus avoiding problems that can affect the performance or reputation of a product.
Example: A company manufacturing new medical devices can use prototyping pre-production from medical device design services if they want assurance that the device is safe and complies with whatever regulatory requirements are available. This avoids costly delays and fines that might be incurred due to non-compliance or faulty products.
Conclusion
It can save time and money for a company in the long run by incorporating pre-production prototyping into the product development process. Pre-production prototyping is a powerful tool for organizations because it helps to improve communication with various stakeholders and facilitates the reduction of manufacturing process cycles.
Catching problems early, testing the design in real-life conditions, and assuring efficient production is possible through this process. Companies are saving costs but improving product quality and speed to market.
How Cad Crowd can assist
Using prototypes as a central part of your product development strategy will allow your company to get better-quality products and a smoother transition into mass production. The end result is a product that satisfies customer expectations while meeting business goals, all within reasonable costs. Ask for a quote from Cad Crowd today, and let us walk you through the process of finding the top experts for all your prototyping needs.