As a textile engineer with a concentration in polymer chemistry, the concept of plastics in manufacturing and design thrills me. While many people will say you should always err on the side of “paper” in the “paper or plastic” debate, I can’t help but espouse the benefits of plastics and polymers, especially in manufacturing and prototyping.
When you’re working with a prototype design service, you will likely interact heavily with plastics of some sort. Polymers and plastics are particularly common with 3D printing, but they are useful for every area of prototype and small-batch manufacturing. Let’s try and demystify the types of plastic you’ll run into and how they’re used.
Types of Plastics – A Primer

The first thing to understand when working with plastics for manufacturing and prototyping is that there are many different types, and the wide variety comes with many properties. Polymer science has created such a wide array of plastics that it is almost dizzying to try and find the appropriate one for each project.
For example, common plastics like polypropylene are used in plastic bottles, but then there are other types as different from them as high-density polyurethane foam that can be made into structural components while also acting as flexible memory foam. And the same formulation can have completely different properties – like polyethylene.
Ultra-low-density polyethylene is used for artificial candle wax, low-density polyethylene is common in shopping bags, and ultra-high-density polyethylene is used in professional-grade hockey sticks and aerospace parts. The chemical formula is the same, the density is different. So, plastic products vary greatly. This is the world you’re diving into when you look at plastics for a rapid prototyping service.
Rigid Plastics or Thermosets

Rigid plastics are just what the name implies – rigid. Typically, they are made from what’s called thermosets, which mean they have undergone a chemical change in the manufacturing process so they are “set” thermodynamically and will not melt or change state. Instead, they’ll combust or degrade.
These are great plastics for making structural material, protective items, and anything that needs to be hard. They do not have the flexible capabilities that elastomers have, so they will not bend or twist easily. This is beneficial since you typically want to use them for structures or safety equipment, like hard hats and sports helmets or electrical enclosures and even some lightweight rigid automotive structures.
In general, higher density polymers make more rigid plastics, so high-density polyethylene will form a strong rigid plastic, as will high-density nylon. Additionally, polycarbonate is a very common rigid plastic. It starts as a standard polymer molecule with large amounts of carbon creating a more rigid structure in the internal molecule, which produces a much sturdier end result for the plastic piece.
Elastomers or Thermoplastics

Elastomers are what a lot of people think of when they think of “rubber.” These are stretchy and flexible plastics, and they can bend and be molded even after they are finally set. There are many obvious benefits to flexible plastics: they’re commonly used for gaskets, rubber bands, and disposable items.
Imagine if we used thermoset materials for the plastic rings on a six-pack of canned soda – it would be a lot more difficult to get out of the packaging. Or a thermoset plastic for the “disposable” grocery bags, that would be quite heavy, and definitely would have me choosing paper. The flexible, lightweight nature of these plastics make them the best option for a number of end-uses in the real world.
Silicone is a common elastomer, particularly for gaskets, as well as polynitrile, which is common in medical gloves and similar items, and urethane rubber. These are all valued for their low weight and flexible properties, without which those end products would not function or would offer a poor user experience. A stiff medical glove would snap as soon as you tried to put it on, and a rigid gasket would be unable to properly seal the enclosure that it’s surrounding because it can’t be maneuvered into the tight spaces as needed. Usability issues arise when the material is chosen poorly.
Reinforced or Composite Plastics
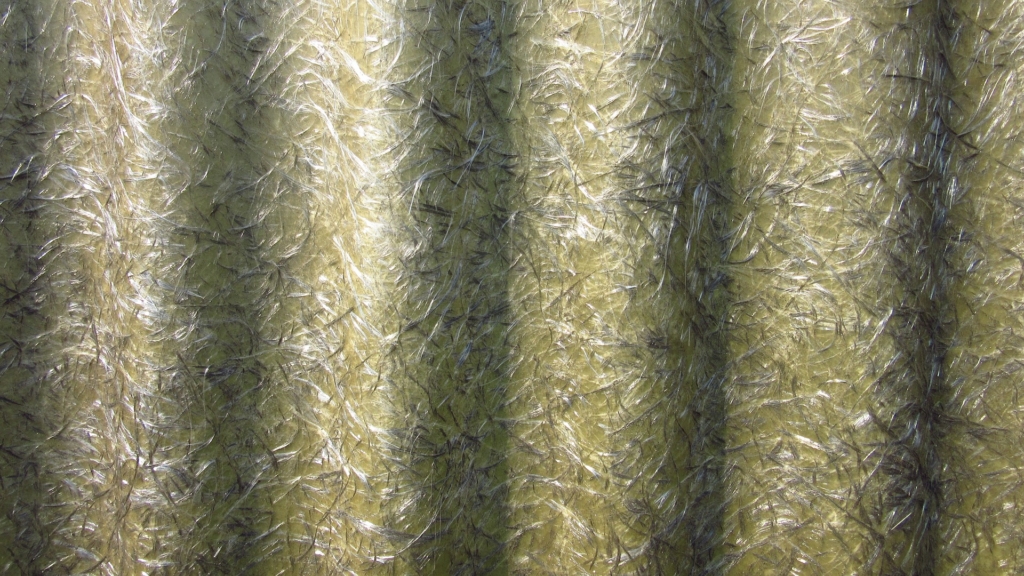
Reinforced plastics and composite plastics are especially interesting. You can take a standard plastic piece and augment whatever property you want to by adding in fiber or other materials. Fiber can be added to a number of plastics to create a stronger part overall.
Fiber increases the yield strength and tensile strength of a material by dispersing the load across these more rigid fibers. It also improves tear strength and cut resistance, making these polymers extremely durable. There are many plastics that use glass particles or fiberglass to impart these same properties and create a much more durable product. You can even add something like carbon to a polymer prior to processing to improve its strength and raise the melting point.
Carbon could also impart electrical conductivity, but depending on the process, you may want to avoid that (such as with electrical connectors or enclosures, or really anything that will be used around high voltage processes). Composites are similar to reinforced plastics, but instead of mixing another material throughout the polymer, you are adding it as a separate layer or in very specific and intentional locations to increase the heat resistance, tensile strength, or some other property. Often times, a ceramic backing will be applied to some polymers to make them frictionless or more durable.
Modified Plastics

Finally, you can modify certain plastics with exotic additives. Obviously, if you want plastic with a unique color, you can always include pigments and dyes to create that but there are a wide range of property-enhancing additives you can incorporate.
Zeolite crystals can be added to improve antimicrobial properties, and these are commonly used in toilet handles that are made of plastic for just that purpose. Flame retardant additives are often incorporated to prevent against fire.
There are even additives for lightfastness to ensure the color doesn’t fade; UV stabilizers to prevent from ultraviolet damage, or if it’s clear plastic, to ensure ultraviolet light doesn’t permeate the plastic; and antistatic additives to prevent against static or electric discharge. The benefit of using polymers in prototyping is that, because they come in a compounded form, you can mix formulations and create different things. These additives allow you to tweak the properties of your product and create a unique material that won’t act like anything before it.
Chemical and Mechanical Properties of Plastics and How to Select Them
Tensile Strength

I’m sure you’ve all seen a tensile testing machine. You place a sample into clamps between two vertical pulleys that separate slowly, eventually tearing the sample apart. This test gives a lot of information about a material, particularly textiles, because they have very unique properties.
Yield Strength
The yield strength is a property specific to plastics and, in some cases, metals. We’ll discuss Young’s Modulus and Hook’s Law in a little while to understand the physics behind deformation of these materials, but obviously, when you pull on a piece of plastic, it changes shape.
The greater the force you apply, the more it deforms. With plastics, there are two important things to note. First, a plastic will start to deform at much lower forces than metal or ceramic. This point is obvious. It’s not common for people to be able to tear apart a piece of copper with their bare hands, but a plastic bag is an entirely different story.
The second point is that they can regain their shape after quite a bit of deformation. Many plastics can undergo stretching and deformation of 50% of their length or more before they fail. The yield strength is the point at which, when pulled, it will not regain its original shape. This is essentially a measure of “stretchiness” and will give you an idea of how much stress you can force onto this material and it will remain useable once returned to its original state.
Fail Strength or Ultimate Strength
Ultimate strength, sometimes called fail strength, is the final state of plastics. If you put it in a tensile tester until it legitimately snaps, then you have found the fail strength. Because plastic can deform and regain its shape, its fail strength is significantly higher than the yield strength.
If you can imagine the molecules inside the plastic, you’ll be able to understand what’s going on a lot better. The polymers that make up plastic are very long chains of molecules, essentially like threads that are all tangled up. When you pull a piece of plastic, these molecules stretch and are pulled in the direction of the force, but they rebound because of the intermolecular forces at work between them all.
Industrial designers have found that if you pull enough, you will eventually overcome those forces and get the long-chain molecules to line up and slide past one another. That is the yield strength because you have forced the molecules to give up their randomized orientation and align in one direction. However, the plastic is still intact. If you continue pulling, though, the molecules will be separated, and you’ll break the plastic. This is the fail strength.
Young’s Modulus

Young’s Modulus is a way to measure both of the aforementioned properties, but it also gives us a working model for what happens below the yield strength. Like we said earlier, many plastics can be deformed to 50% or more of their length in a certain direction and rebound to their original shape with no lasting issues.
The Young’s Modulus will help you predict how well something deforms and returns to its resting state, and can also be used to extrapolate how many cycles of stretching (or compression) and returning it can undergo before failure. Young’s Modulus is related directly with Hook’s Spring Law, which means that any force applied to a spring will deform it in direct proportion to the spring constant of the material, which in the case of polymers is Young’s Modulus.
The corollary to this is that any change in one-dimension results in a proportional, opposite change in the other dimensions, i.e. if you stretch it lengthwise, it will contract its footprint. Young’s Modulus can help explain this and will allow you to plan out how you will use the plastic because you can take into consideration any potential shrinkage or stretching that may occur.
Hardness

Hardness is a pretty obvious trait. Typically, with plastics, the tool and measurement method used to analyze hardness is durometer. A durometer refers both to the testing device and the value or scale that is attributed to a material.
A durometer measures the hardness of the material in a very specific way. The tool applies pressure to the plastic, or other material, using a standard-sized ball foot, and then measures how much force must be applied to achieve a certain depth of penetration by this foot. This gives a standard data point for how hard one must press to leave an indentation.
The shore durometer scale is used to identify each of these values, and is broken down into three categories – Shore 00, Shore A, and Shore D. Shore 00 measures rubbers and gels that are easily penetrable, Shore A measures soft and flexible rubbers, and Shore D measures semi-rigid to tough plastics. These measurements are very useful in choosing a product that needs rigidity and strength, and you can very quickly analyze whether or not a plastic will work for your end product by looking at the Shore Hardness Scale.
Elongation
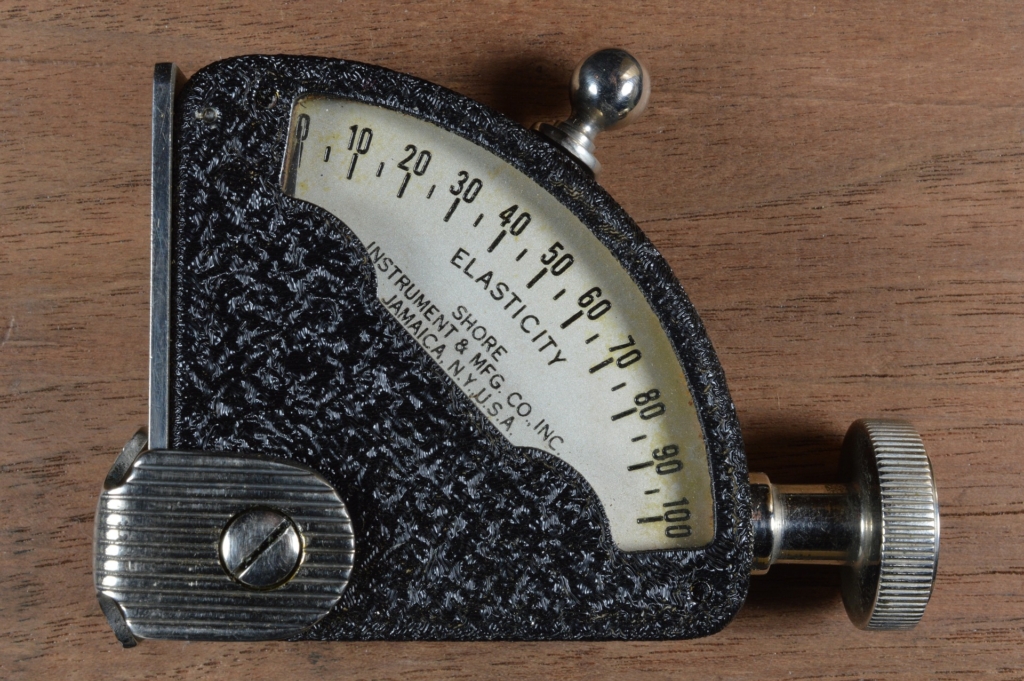
Jumping back to the discussion on Young’s Modulus, yield strength, and fail strength, let’s take a look at elongation. Elongation is essentially how far something can stretch right up until it reaches the yield point. Elongation is a very useful measurement for any product that is required to stretch, like rubber bands, compression clothing, gaskets, or similar products.
Like we discussed before, if it is stretched below the yield point, it will be able to deform but return to its original shape and size once the stress is removed. A material with good elongation can even maintain a stretched shape for long periods of time and rebound exactly as they were initially.
One point of consideration for elongation, yield strength, and fail strength is the weather. Because plastics fall into a middle area with a relatively low melting point, as well as their own separate transition called the glass transition temperature, the temperature can severely affect them.
For instance, the main reason behind one of the worst space shuttle disasters in United States history was that one of the gaskets had not been assessed for its glass transition temperature accurately, and it became brittle when exposed to the cold of the high atmosphere, failing and destroying the shuttle. So, elongation is a very important metric, and it’s necessary to take everything into consideration.
Miscellaneous
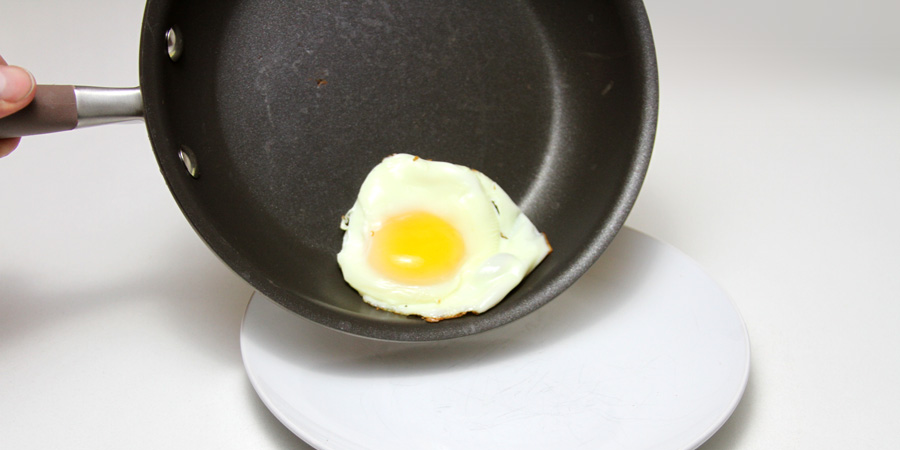
We haven’t even begun to address all the different properties associated with plastics. Beyond their physical internal properties, you have to consider the specific heat of each material, which will impact thermal transfer through it – especially if you want it to act as an insulator, for which some plastics work very well.
The coefficient of friction is also an important factor. Some materials and products are intended to be exceptionally slippery, such as Teflon, and they work very well in lubrication or bearings applications. Others need to maintain a very static position without adhesives or locks, and therefore need a high coefficient of friction to prevent motion.
Additionally, density is a major factor to consider. The density will impact the rest of the properties listed above, but each material can be manufactured in different densities, which is one of the wonderful benefits of polymer science. You can create a polyethylene formulation with molecules that are as small as several hundred atoms long to tens of thousands of atoms long (which is the main difference between low-density polyethylene used in candle making and ultra-high-molecular-weight polyethylene used in hockey sticks). You can customize the density, which will change all the other properties as well.
Additional Properties
Not only do plastics have intrinsic, beneficial properties that must be taken into consideration, there are also chemical and additional properties that are inherent or can be included to improve the final product. Let’s look at some of these additional properties that should be considered as well.
Biocompatibility
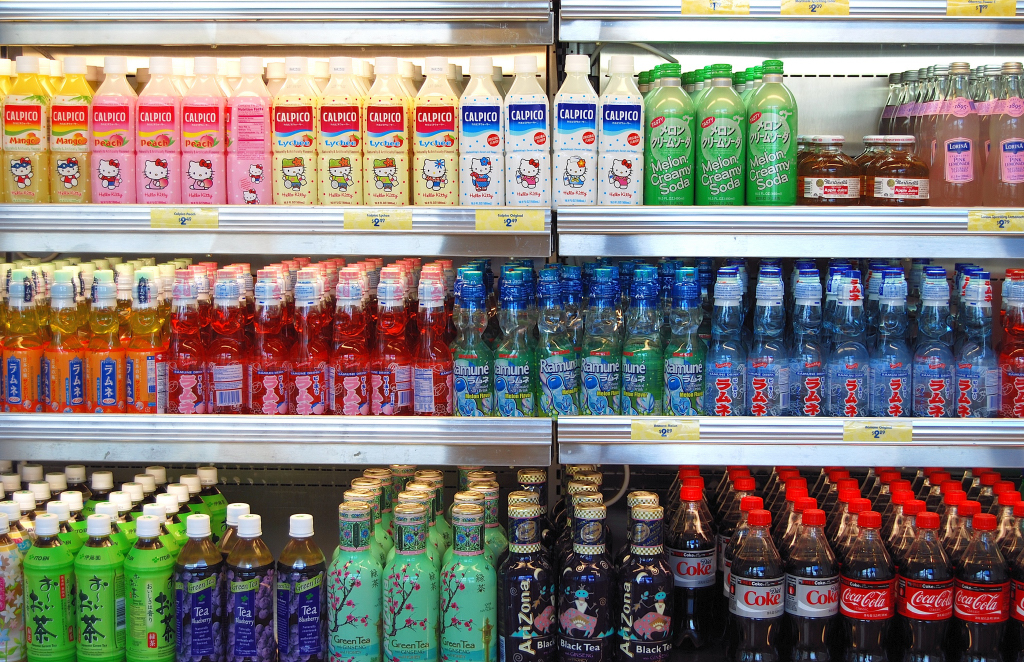
Plastics are used all the time in medical operations as well as with food treatment and other functions that come into close biological contact with humans and other species. The appropriate plastic should have no adverse effects on the person with whom it’s interacting.
Some of them are naturally biocompatible and need no improvement to be used with the human body, such as medical-grade PVC, Polyethylene, Polypropylene, and Teflon (PTFE). Additionally, you can use additives or sanitizing processes to ensure that some others are biocompatible. Nylon is one that is commonly adjusted to use in biomedical applications.
More often than not, freelance design engineers use 3D printed materials are not biocompatible without adjustment, so these are produced through extrusion, thermoforming, or molding in some way. There are many options for biocompatible polymers, however, whether intrinsically or adjusted, so if those are your needs, you can certainly find something that will work.
Antimicrobial

An antimicrobial material will specifically prevent microorganisms from growing on or within the material. There are obvious benefits to an antimicrobial product, and these are typically useful in biomedical applications where you don’t want any bacteria or viral organisms. Many polymers are naturally antimicrobial, but they’re not always the easiest to process. Because of this, it is more common to find plastics made with antimicrobial additives for production.
Polyethylene, Polypropylene, and Acrylonitrile are commonly used because they mix well with additives of any type. Zeolite crystals are the most common antimicrobial additive, and they are made silver particles that trap and kill microbes and bacteria, making the surface safe. Because of increasing disease and a greater understanding of health and sanitation, more and more products are being manufactured to have some form of antimicrobial nature.
There is additional research being done into nano-etched polymers that have a surface configuration that is inhospitable to most forms of bacteria and viruses, so they won’t need any additives. But these treatments are still in their infancy and are very difficult and expensive to produce, so most people stick with chemical additives.
Processability
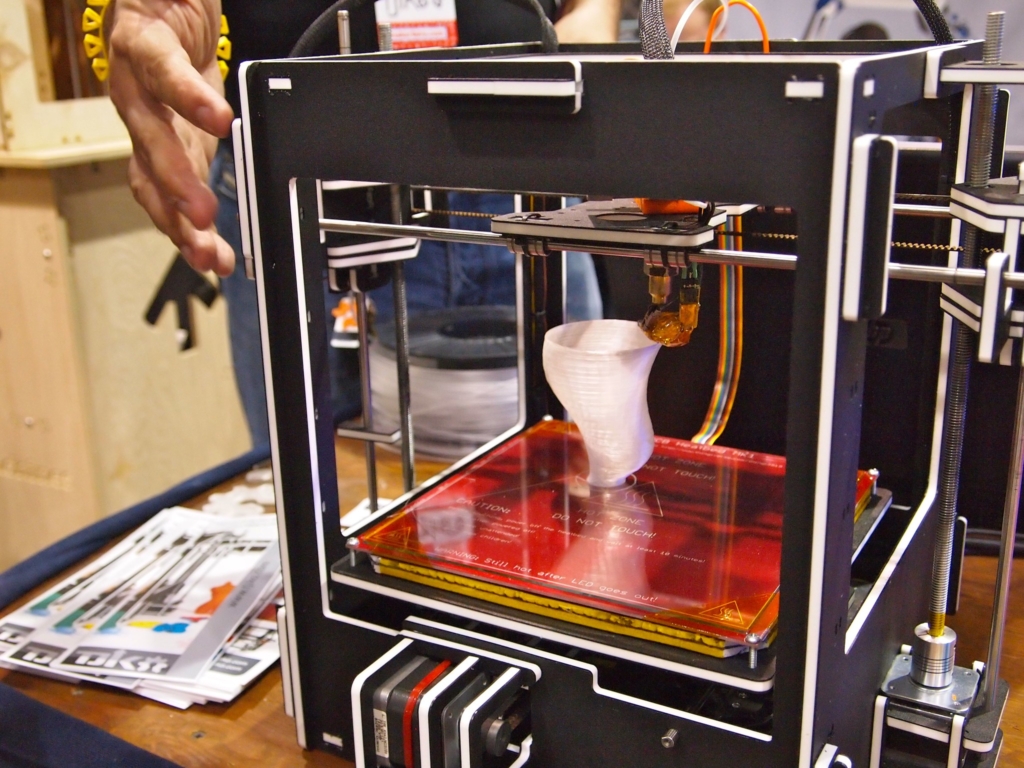
How are you planning to manufacture or prototype this material? Will you hire a manufacturing service? That will drastically affect the choices you have for what material you want. The first consideration, especially for someone working with a prototype design service, is will you be able to 3D print this material?
If you’re planning to use a 3D printer for your project, you are limited to the current capabilities. Only a few common plastics can be used on a standard 3D printer, like Poly-vinyl acetate. If you are planning to use a more intense, industrial 3D printer, you may have fewer restrictions, but you can broaden your scope if you’re willing to use a CNC or extrusion method to produce the product.
Extrusion and thermoforming work very well for materials with lower melting points, but a freelance CNC programmer can give precision and rapid manufacturing for products that are a bit more resilient. A plastic-like Polyester ester ketone, or PEEK, is acceptable in a wide array of manufacturing processes, like CNC cutting, extrusion, or thermoforming. Silicone rubber, however, is much more unstable and responds poorly to various manufacturing processes, and therefore is much more limited to injection or compression molding.
Dimensional Stability
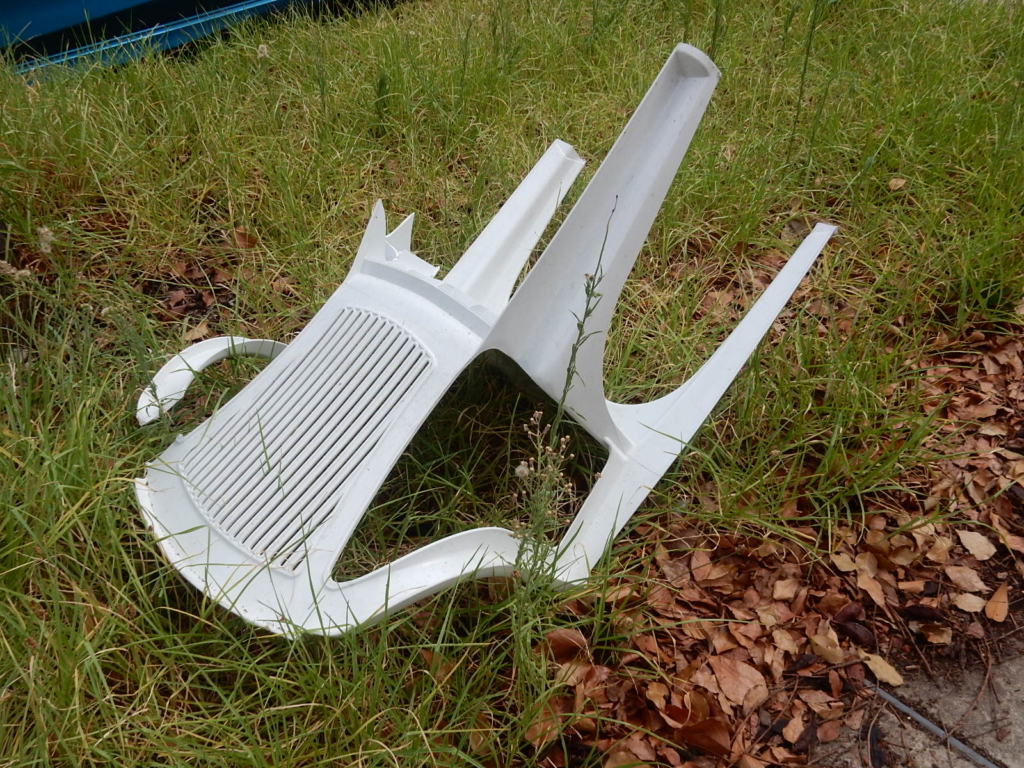
When working with polymers, the dimensions are always a major consideration. Typically, with ceramics, metals, or composites, there will not be any dynamic movement in their size and shape. Unfortunately, with plastics, one of their more marketable features can also be their undoing.
The ability to bend, stretch, and compress also makes plastics dimensionally unstable. When you are creating your product, you need to consider how stable it needs to be – which relies greatly on the forces applied to it. If you are going to be applying a large load to a plastic, it is more likely to deform and lose its dimensional stability, so you will need a more rigid material in that situation. You can use the properties discussed earlier to determine the necessary dimensional stability.
Somewhat related to dimensional stability is moisture absorption and regain. Not every plastic absorbs moisture, but some of them do. Polyurethane and nylon, common in clothing, will absorb moisture. This changes the rigidity and dimensional stability in the product, and should be considered when manufacturing a product. In many situations, this will not affect anything adversely, but if the product is intended to be used in water or in humid situations, it may have an impact.
Temperature Resistance

There are too many considerations to list them all, but one final one to discuss is temperature resistance. Plastics are more fickle than many other materials. While ceramics and metals have a range of useable temperatures from well below freezing to potentially over 1,000 degrees Fahrenheit, plastics tend to melt not far above boiling temperature, and brittleness is imparted at low temperatures.
Because of this, you must select a plastic that has a suitable temperature resistance for the operations your product will be placed in. Select a higher temperature option for products that will go into an engine that generates heat, or a lower temperature option that will be used on an Arctic fishing vessel.
As we discussed earlier, thermosets do not melt because of the chemical changes they have undergone, but they do combust or break down in other ways. Consider the temperature range it will be used in, and think about what may happen if that product fails. Would it be less dangerous for a gasket to potentially melt or to combust? As always, the end-use dictates the selection of material.
Manufacturing Considerations
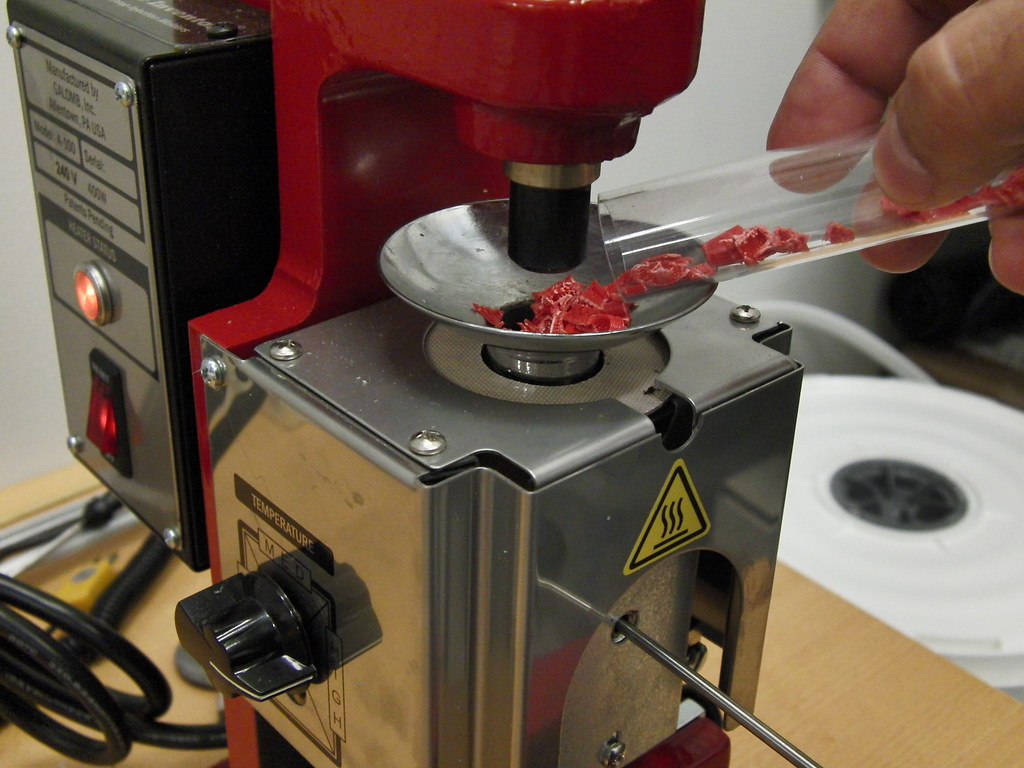
Now, when you’re selecting the material to create your prototype, you need to ask yourself how will this product be manufactured? If you’re only concerned with early-stage rapid prototyping, a 3D printed piece may work just fine for your design process. But if you’re thinking ahead to the long-term state of production, you may want to select something that can be used in a standard production system. The plastics that are used in 3D printing are not ubiquitous in everything, and vice versa. It is more common to be unable to use the same plastic in a 3D printer as you are using in, say, an extrusion or thermoforming process.
For the prototype, using a CNC machined manufacturing method may offer more of the flexibility you need to create a product that can be easily replicated in the final manufacturing process. Injection mold design is a similar option, but you will need to create a mold or dye, which you may not want to do unless you are certain this product will go into production and will be replicated. If that’s the case, having a mold or dye that’s been cast already will make your life easier, but if you’re still waiting on customer approval of the product, then you may want to hold off on casting one until the product design is finalized.
In the case that you are set on using a 3D printer to create your design prototype, it would behoove you to select a similar material that can be produced using a 3D printer and creating the product so that its properties would be nearly identical for testing and demonstration purposes. This way, you can still use an efficient prototyping method and demonstrate the capabilities of the product without having to commit to something costly or cumbersome like creating a mold or using a more expensive CNC machine. If you can substitute various forms of Nylon and Poly-lactic acid for materials like Polycarbonate or High-density polyethylene, you can utilize a 3D printer to create a similar version.
The easiest way to do this is to find the necessary properties that we discussed in earlier sections, like yield strength, Young’s Modulus, elongation, or durometer and what values you will need them to meet in the final product. Select a common 3D printable material, such as Nylon 12 or Vero Clear, and then compare it to the material that will likely be used in the final production application. If you are working with an injection or thermoforming molding process, compare it to something like EPDM or forms of Acrylonitrile. If your customer works primarily with extrusion, compare it to Polycarbonate, Silicone, or urethane rubber. This will help you decide what you can use for prototyping and how to properly translate it to final production, making your life a lot easier.
Final Thoughts
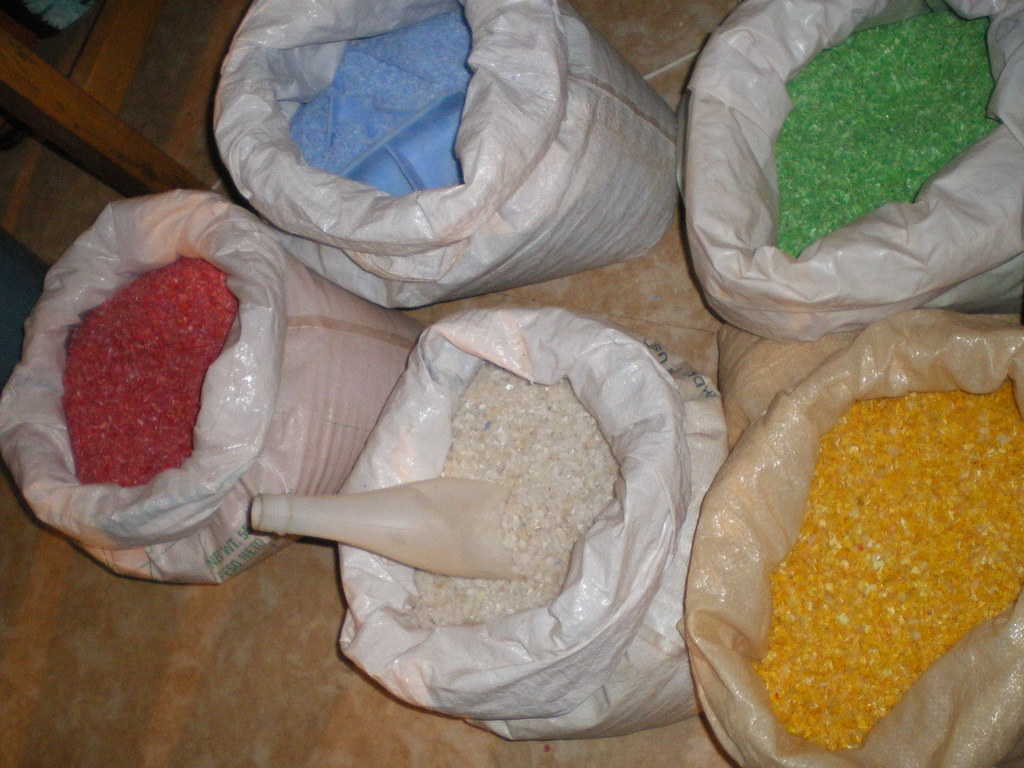
Obviously, freelance mechanical engineers make significant design considerations when using plastics in a prototype. At this point, you may simply think it’s easier to select something like ceramic or metal, but the benefits offered by plastics will far outweigh the effort you must expend on the front end. The main problem with plastics is that there are so many options.
The diversity in the plastics industry affords you every opportunity to find the perfect fit for your product, and, in fact, if you want to create a specialty material designed exclusively for your product, plastics give you that chance. Any prototype design service could benefit from selecting unique plastics to work with because you have flexibility and options that other materials don’t offer you.
Whether you’re working to design a single product or you want to create high-fidelity prototypes for future production, polymer science has created an array that can suit any need you encounter. Hopefully, this article can help you analyze and select the correct formulation for your next product. You can even start the development process with a simple SolidWorks design from a CAD design service and start 3D printing products at your leisure if you want to. Whatever your end goal is, however, Cad Crowd can help. Find out how it works today.