Today, we are discussing the cost of designing a new electronic product and developing PCB hardware prototype rates at firms. Every inventor and designer needs to know every single factor in making a product. It is true to all product categories, and even more so to electronics, not only because of the sheer number of small components assembled into a circuit, the certifications, and the actual manufacturing. The total cost accumulates in a typical electronic product development process due to the expenditures explained below.
Table of contents
- PCB Design, estimated cost: $10,000+
- Prototyping, estimated cost: $1,000+ per iteration
- Software, estimated cost: $5,000+
- Plastic Enclosure Design, estimated cost: $5,000+
- Plastic Enclosure Prototype, estimated cost: $500+ per iteration
- Retail Package Design and Prototype, estimated cost: $3,000+
- Certifications, estimated cost: $10,000+
- Federal Communications Commission (FCC)
- Intentional Radiator
- Non-intentional Radiator
- UL (Underwriters Laboratories)
- CE (Conformité Européenne)
- CEC (California Energy Commission)
- RoHS Certification
- WEEE (Waste Electrical & Electronic Equipment)
- ESD (Electrostatic Discharge) Immunity
- Bluetooth SIG
- Other certifications
- Manufacturing, estimated cost: $40,000+
- How can Cad Crowd help
PCB Design, estimated cost: $10,000+
The electronics hardware and the engineering design costs consume the most considerable portion of the overall budget. Bear in mind that “hardware” in this case refers to the essential electronic components, excluding the enclosure. Most engineers charge by the hour; according to the latest data (May 2020) by the US Bureau of Labor Statistics, the national average hourly rate for electronics engineers in the country is $54.
It is impossible to determine the exact timeframe when developing new electronic products. Any slight deviation from the original plan or technical difficulties will push the completion date back, significantly increasing the overall engineering cost. Printed Circuit Board (PCB) design software can help prevent unexpected product development challenges. Cadence Allegro, Proteus, Autodesk Eagle, Altium Designer, and DesignSpark are some of the most popular.
RELATED: What are electronic manufacturing services (EMS) for new products & prototype design?
Computerized design mitigates the risk of mistakes, both in the design itself and cost estimation, thanks to integrated component libraries with which engineers and vendors can verify inventories and real-time prices. Every software program has its own set of unique features, but in general, engineers will be able to take advantage of the following capabilities:
- Component performance comparison in terms of power loss and resistance
- Identification of critical component
- Prediction of component failure rates
- Simulation tools for cost-benefit analysis.
Design for Assembly (DFA) and Design for Analysis (DFA) tools are available in most software packages, along with data reports such as Bill of Materials and cost estimation. DFA focuses on reducing the cost of assembly, whereas DFM emphasizes efficient manufacturing. We are achieving both means better cost-efficiency regarding material labor and overhead while ensuring a quick time-to-market process.
PCB design software facilitates collaboration between design teams and component suppliers, specifically its DFM and DFA functionalities. Such features also encourage standardized parts and minimize component count (whenever possible) without sacrificing quality.
RELATED: Hiring the best electrical engineers & freelance PCB designers
Prototyping, estimated cost: $1,000+ per iteration
Once the design is ready, prototyping is the next step in the development process. It involves two steps:
Blank PCB
The cost to produce a blank PCB is mainly affected by the number of routing layers and size. At a bare minimum, two routing layers (top and bottom) are necessary. Most designs require four to six layers, but a complex product may require Tat least eight layers. PCB size tends to shrink as the number of layers increases.
PCB assembly
The primary factors in determining the cost of PCB design assembly (soldering down the components) include the total number of features used, the use of leadless packages, minimum pin pitch distance, and whether the parts are welded on both sides of the board. The total estimated cost mentioned above already covers both steps. If calculated on a per-unit basis, a production run of a large number of units is almost definitely compared to prototyping.
As the volume increases, production cost per unit decreases. Building more than a dozen prototypes is never a good idea, and five to ten should be good enough for a preliminary internal test. Once the functionality is confirmed and major bugs fixed, you can then increase the quantity and start distributing the samples to potential customers or investors.
RELATED: Learn about electrical engineering consulting costs, services, and pricing in firms
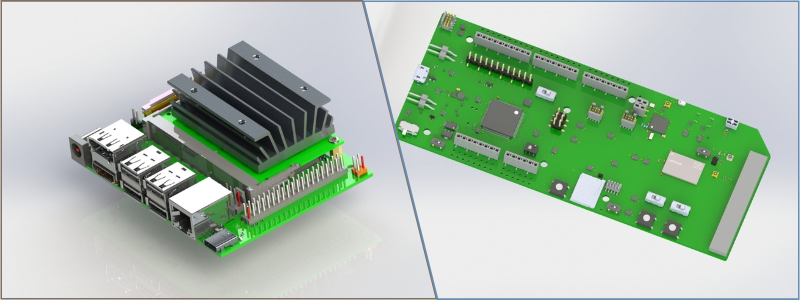
Software, estimated cost: $5,000+
Even the most straightforward electronic product comes with embedded software. Every electronic product has a microprocessor or microcontroller that requires firmware (or programming) to operate correctly. Assuming the product works with a smartphone app, there needs to be a separate development budget for the app. Since a prototype design aims to confirm whether the method works as intended, you must consider the cost of software (and app development).
The same team does not constantly develop hardware and software simultaneously. The budgets to build the two aspects can be similar, but this is an over-generalization. Each product is unique, meaning some can be hardware-complex while others are software-heavy or perhaps both; the development cost follows accordingly. The more sophisticated an electronic product is, the more money it takes to prototype.
RELATED: The best PCB design software for electrical engineering professionals in 2022
Plastic Enclosure Design, estimated cost: $5,000+
Designing the plastic enclosure for your electronic design is best left to a 3D modeler or industrial designer. Most will opt for the former simply because modelers usually charge less than the latter. However, there is a big difference in how each does the job. Some electronic products require additional components to be attached to the plastic enclosure, such as moving mechanical pieces and metal (magnetic) parts, which increase the level of complexity in both engineering and design works.
Most 3D modelers will focus heavily on the aesthetic side of the design, and the result is more like a work of art rather than a mass-produced item. Industrial designers also consider the artistic value, but more importantly, they create a design from a marketer’s standpoint. From an industrial designer’s perspective, a product enclosure must be a selling point. Aesthetic alone is not enough because it also has to encourage people to buy the product.
RELATED: 3D Models of electronic enclosures by freelancer designers on Cad Crowd
Plastic Enclosure Prototype, estimated cost: $500+ per iteration
Like the PCB design, the plastic enclosure design must also undergo prototyping. In recent years, additive manufacturing (3D printing) has become the method for building an enclosure prototype. The technology works by stacking layer after layer of molten plastic on a printing bed to form a shape.
A 3D printing process is unlike injection molding, where you must build the mold first. Any design (drawn and saved in a compatible file format) can be printed. You use a 3D printer filament as the material, and plenty of types are available in the market these days. It may take just about a few hours to print a shape, but it all depends on the complexity of the design. Some 3D printers are made for home use, although it is best to refrain from non-professional users when creating a prototype. It is quick and affordable for a low-volume prototyping design.
RELATED: Different kinds of prototypes and how to use them for your design project
The alternative is CNC machining, a subtractive manufacturing method. It is a computerized sculpting process in which a plastic block is carved to shape, and any unnecessary materials are removed from the block to build the final design. A significant advantage of CNC is that you can use production injection-molded plastic as the base material, creating a prototype identical to the method in shape, texture, and strength.
With a plastic enclosure, sometimes the prototype cannot be manufactured, at least not in an efficient way. It is especially true with 3D printing design, a method with limitless capabilities for creating a shape. Mass production can be a real challenge if the enclosure is too intricate, with many cavities, curves, and varying thickness levels. Most plastic parts used in mass-produced goods are manufactured using the injection molding technique, thanks to its speed and affordability.
Whether you are hiring a 3D modeling or industrial designer, make sure the professional understands the capabilities and limitations of injection molding. You do not want to end up with a pricey prototype that cannot be manufactured in bulk without a significant redesign.
RELATED: What are industrial design rates & costs at product design services firms?
Retail Package Design and Prototype, estimated cost: $3,000+
Packaging must be functional because it protects the product from the elements from when it leaves the manufacturing facility until it gets to the hands of a buyer. Some products sold only online do not need retail packaging at all, and Online sellers can use plain reinforced cardboard because consumers can see the product photos on the website. In a retail environment, the packaging design is almost as important as the product itself. For packaging design, in addition to providing protection, it must also be appealing enough to help sell the product.
Standard packaging designs for electronic products include clamshells and boxes. You may want illustrations, a logo, or a 3D product rendering regardless of the type. You don’t want to slap a product photo on it and call it a job well done. The packaging material is probably not that expensive, but the original artwork printed on the package can cost hundreds of dollars if done by a professional.
Both clamshell and box are comprised of two parts: a custom-cut plastic to keep the product in place and a cardboard piece with printed artwork or a sales message. Much like the actual enclosure, packaging design is best developed using a 3D CAD drafting service, especially if the artwork is product rendering, and the custom-cut plastic must be injection molded to fit the product perfectly. With clamshell, the artwork is printed on the blister card; use thicker card and stamp printing for the best result. If you have to build multiple packaging prototypes with different images, they can cost a reasonable amount of money.
RELATED: New product packaging design & why it’s essential for product designers
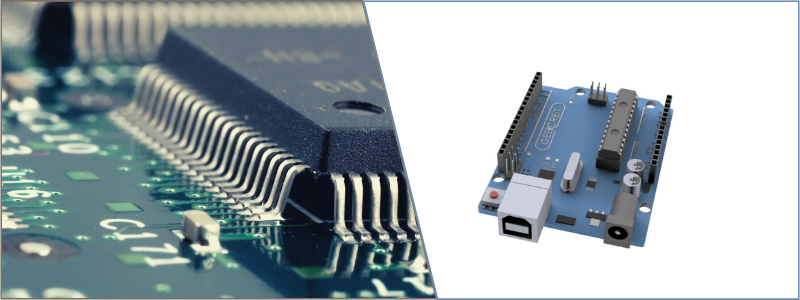
Certifications, estimated cost: $10,000+
Most products, especially electronics—wireless or not—require several certifications before officially being introduced to markets. Estimating the cost of certificates to around $10,000 is, in some cases, a gross understatement. It may take the most considerable portion of the budget when developing a new electronic product design. Among the most common certifications required are:
Federal Communications Commission (FCC)
All electronic products to be used or sold in the United States that oscillate at 9 kHz or higher must be FCC certified. The purpose is to limit electromagnetic radiations below the point where the product interferes with wireless communication. FCC classifies electronic products into two types:
Intentional Radiator
Any electronic product designed to deliberately transmit (RF) radio frequency waves (more commonly referred to as electromagnetic radiation). Cellular phones and internet-enabled devices are typical examples of intentional radiators.
Non-intentional Radiator
Any electronic product that unintentionally, albeit inevitably, emits some level of RF wave during operation. Some examples include TV receivers and computers. The certification requirement for the intentional type is much more involved and expensive than its unintentional counterpart. The equipment is a direct cost for obtaining the certification; the testing chambers’ rental fee is around $1,000 per hour. Most startups hire a third-party testing service to perform the necessary procedures.
RELATED: Tips for PCB design services creating new products
The FCC may also require SAR (Specific Absorption Rate) testing to determine how electromagnetic radiations interact with the human body. SAR is applied to devices equipped with high-power radio transmitters, such as smartphones and tablets. A device is only considered safe for human use if the SAR rate does not exceed 1.6 watts per kilogram. Most phones sold today are safe.
UL (Underwriters Laboratories)
Every electronic product plugs directly into an AC outlet must pass UL certification requirements before being introduced to the US and European markets. The primary purpose of the certification is to ensure the product’s safety in the sense that it will not trigger an electrical fire or cause other safety risks. UL’s primary concern is standardization; the organization promotes plenty of safety standards, each set to diverse types of electronic products and their intended use.
In the United States, UL certification is not technically necessary; however, neglecting to obtain accreditation can hurt the product in the market. If your product causes an electrical fire, you are held liable. The UL certification falls on the charger if your product does not plug directly into the AC outlet but uses a portable charger. An alternative to UL certification applicable to electronic products sold in Canada and the United States is known as CSA (Canadian Standard Association).
RELATED: A product designer’s guide to design for manufacturability
CE (Conformité Européenne)
Any electronic product design with a “CE” marking is officially regarded as compliant with European health, safety, and environmental requirements. You can almost say that CE is the equivalent of both UL and FCC certifications combined.
CEC (California Energy Commission)
All electronic products that contain battery chargers and are to be sold in the State of California, United States, must meet the efficiency requirements enforced by the CEC. In short, the AC adapter used to recharge the product requires certification of Level IV energy efficiency issued by the Department of Energy.
RoHS Certification
Electronic products to be sold in Europe and the State of California must be RoHS certified. The procedure verifies that the products contain no harmful substances like mercury or cadmium. RoHS certification is not a hassle, and inur factory partner may be willing to obtain it on your behalf.
WEEE (Waste Electrical & Electronic Equipment)
It is a directive or regulation enforced in the European Union to make clear that all electronic products sold in the region meet the safety and environmental standards for the collection, recycling, and recovery procedures. WEEE regulation works in tandem with RoHS certification, and the latter addresses the harmful materials used, while the former regulates the safe disposal method for the product and its materials.
RELATED: How industrial designers and engineering services have influenced the product design world
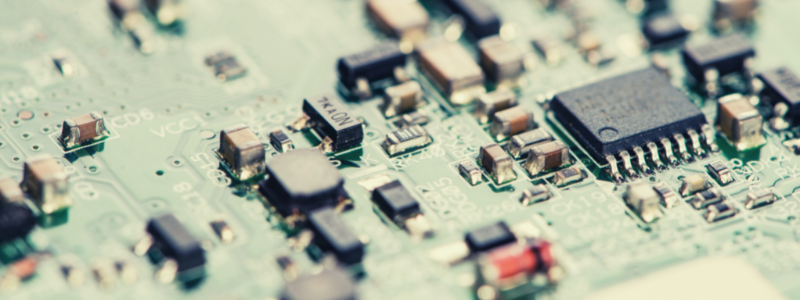
ESD (Electrostatic Discharge) Immunity
The point of this test is to figure out whether an electronic product can withstand exposure to ESD. Sensitive electronic equipment can go haywire if exposed to a reasonable level of static electricity. It is not necessarily a safety issue, but a test to determine the effect is recommended. In some products, ESD failure is instantly noticeable, although there are exceptions where the results are not immediately apparent.
ESD immunity tests prevent your product from encountering severe problems down the road, especially when customers store or use it near other electronics. If (or when) ESD causes severe damage after sales, the product and brand’s reputation will take a massive blow. Considering the risks, having the effect tested beforehand is a small price.
RELATED: Product simulation and analysis: why it’s worthwhile
Bluetooth SIG
The official organization oversees the standard and licensing of Bluetooth technologies is the Bluetooth SIG (Special Interest Group). Although the group is not-for-profit, the promoter members are all massive private corporations, including Microsoft, Lenovo, Intel, Apple, Ericsson, Nokia, and Toshiba. Bluetooth SIG is not technically a certification, but a licensing fee is in order if your electronic product uses Bluetooth Classic or the Low-Energy version. In addition, you also pay the organization for using the Bluetooth trademark, which costs around $8,000 for the licensing fee.
Other certifications
Products for children usually have to go through a more comprehensive list of certifications to ensure everything is safe. Certificates from the FDA are necessary when the products are used in a way that brings them in contact with food items.
Manufacturing, estimated cost: $40,000+
You have covered all the procedures and the minimum cost required to develop a new electronic product before manufacturing. Thus far, the estimate is:
Development stages | Estimated price (USD) |
PCB Design | 10,000 |
Prototyping | 1,000 |
Software | 5,000 |
Plastic Enclosure Design | 5,000 |
Plastic Enclosure Prototype (per unit) | 500 |
Retail Packaging (Design and Prototype) | 3,000 |
Certifications | 10,000 |
Manufacturing | 40,000 |
Total cost | 74,500 |
Many people underestimate the cost factors between prototyping and product design manufacturing stages. An electronic change from a mere design to a prototype still requires many development phases such as the enclosure, package, and most importantly, certifications. Opt for a local factory partner to minimize the chances of something going wrong. Collaboration with local business entities means both parties work under the same regulation, safety requirements, and quality standards. Communication is also more accessible because everyone speaks the same language.
RELATED: Top tips to create impactful prototype designs for company products
The nature of product development is that there can be a lot of unknowns in the process, so there is no standard pricing anywhere. The estimate given above should be treated as a mere approximation. In an ideal world, you must have double or more of the amount specified as a contingency plan. For a complex product, the total cost of development is easily in the range of millions of dollars, although simpler ones should be viable for much less.
How can Cad Crowd help
Whether you’re still in the concept phase or are ready to start production, our 3D modeling design team will provide you with the experience you need to complete any project. Our services are available for inventors and entrepreneurs who need to hire 3D design talent for their new products. Contact us for a free quote.
Hi Jai, yes, we can help. Please use our quote form for a personalized estimate. Thanks!
Hi, My name is Jai Yadav; I want to develop an embedded electronic prototype product for the oil and gas industry. Can you guys help me in this regard?
Hi Jai, send your project summary via our quote form, and we’ll get back to you with an estimate asap.