Startups frequently fail because they misunderstand market needs. This article shares design and engineering techniques for creating a desirable and viable product with design firms. Developing a product that nobody needs or wants doesn’t make sense, and a new product idea may be envisioned differently than implemented. Therefore, you must identify market demand and test the product to determine if it will satisfy people’s needs. Given a limited budget, the last thing you want is to stretch your budget too thin to the point that it runs out before you are ready for market. One desirable option is to turn to a 3D product concept design firm that can help you create a viable product.
RELATED: 3D modeling: an overview of history & industry applications
Common types of 3D modeling
Design firms use various 3D models with different techniques and approaches. These different 3D modeling types offer a unique set of pros and cons that a design firm can use to create a viable product.
NURBS modeling
Non-uniform rational basis spline or NURBs modeling refers to developing a model using a dedicated mathematic model to create realistic elements. It is a popular form of modeling since it is versatile and has many applications (i.e., creating simulations of cars, animals, people, etc.).
RELATED: 12 Must-know 3D modeling terms
Polygonal modeling
Coordinates X, Y, and Z are used in polygonal modeling to create surfaces and shapes. This type of 3D product modeling service is called polygonal due to the use of the polygonal mesh theory that might not be beginner friendly. It manipulates the wired mesh to the desired shape to develop the preferred model. The gaming, animation, and film industries often use polygonal models.
Primitive modeling
In product design, primitive 3D modeling is characterized by using spheres, cubes, and similar variations of shapes to develop a new element. Good 3D modeling experts should be familiar with this technique since this is essential. Primitive is a term that represents the simplicity of the use of two shapes to form something exciting and new. Using Boolean processors that allow the creation of shapes and outlines is the most common method of doing primitive modeling. Physics simulations are an excellent example of using primitive modeling.
RELATED: 3D modeling vs. 3D rendering services
Rational B-spline modeling
Rational B-spline modeling is one of the most widely and commonly used types of 3D prototype design engineering services. This type of modeling is similar to primitive modeling and uses various geometric shapes to form a new structure. However, what makes it different from primitive modeling is that it is more versatile while offering a more extensive selection of elements you can play around with and choose from. Unlike polygonal modeling, this type of modeling is not as difficult to perfect. The designer only needs to conjoin different shapes to create basic structures and then twist and curve them until the desired final product is achieved. For example, this model can create textured and interesting surfaces such as shoe soles.
Solid modeling
Basic shapes such as spheres and prisms are used in solid modeling to form different models. For example, you can create 2D sketches, and you will scale them to come up with a 3D element. You can also add solid elements to other solid elements to develop more detailed shapes and figures. Previously, solid modeling was used by the assembly and machining industry for verification and planning. Today, it is already being used in 3D printing and interior design.
RELATED: How much do engineering design services cost for company design R&D?
Wireframe modeling
The shapes in wireframe modeling are considered multiple networks of vertices. A minimum of three vertices are required to develop a single geometrical shape. The size can be easily altered by dragging the vertex in any preferred direction. Designers use wireframe modeling to develop complex surfaces. However, mastering it is more complicated since formal training is required. Wireframe modeling can create numerous complex elements and design items, including appliances, shoes, and even people’s faces.
The role of 3D modeling in designing a viable product
3D visualization is the best and easiest way to design a viable product. When it comes to product design, 3D modeling technology has an almost endless list of benefits, including the following:
1. Create high-quality prototypes with 3D modeling
Design firms use 3D visualization technology to develop lifelike models of various products that are more realistic than traditional photographs. 3D modeling allows you to design prototypes featuring vivid details like different lighting conditions, textures, and other peculiarities. These prototypes can then be 3D printed, or you can also use them for marketing purposes.
RELATED: 20+ Free 3D models and downloadable CAD files of mechanical and engineering designs
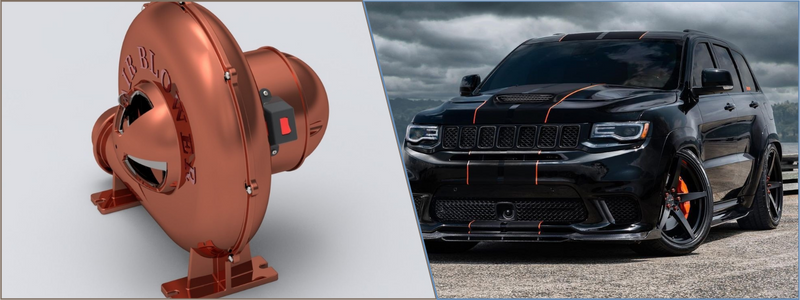
2. Speed up your time to market
This next benefit is straightforward to understand. Going to the market faster with a quality product increases your chances of succeeding and taking over market share. 3D modeling allows you to design and manufacture your product more quickly than other methods, which will shorten your time to market so you can surpass your competitors.
3. Simpler and easier display of the physical properties of a product model
One of the best things about using 3D models for product design is that it is realistic and can depict objects that other techniques cannot. 3D models are great for showcasing products in various environments. The 3D modeling designer can easily modify the model (i.e., turned and repositioned) so you can see and check how it will fit in different places and angles.
RELATED: Accessible design: better products for everyone
Several major brands, such as IKEA, now use this technology to guide their customers in choosing the furniture they need. The company’s website feature 3D models that customers can use to check if the specific product would fit well in their spaces. The models can also be tested in different virtual areas and rooms to make the entire process easier and more convenient.
4. Identify the best materials technologies for your needs
Thanks to the flexibility and versatility of 3D modeling techniques, you can experiment and identify the best elements that suit your product. The product can be viewed from a 360-degree angle, and you can also apply different textures, finishes, and other changes and observe them from different angles. It will allow you to quickly identify the best materials to proceed to production.
RELATED: How-to guide: new product design, engineering and prototyping your idea for mass manufacturing
5. Iterate tooling and prototypes to maximize refinement and testing opportunities
A rapid prototyping company that creates prototypes is an inevitable aspect of any product design process. Not too long ago, prototypes had to be manually created from various materials to portray an idea. Even though it worked fine, there were apparent shortcomings. You must remake the model from scratch to make a few slight changes.
However, this means you will be wasting plenty of materials on physical production, not to mention that it will also be more expensive. But with realistic 3D product rendering, endless versions of prototypes can be made, and changes can also be done in real-time to fit your needs or those of your client. These designs are cheaper, don’t produce additional waste, and are very flexible.
RELATED: A product designer’s guide to design for manufacturability
6. Production optimization and seamless transition to manufacturing
Product design from concept to manufacturing will be quicker and easier if you take advantage of the existing 3D technologies. It is possible to design and perfect several product models fast, and you can send these to manufacturing in just a few minutes. Edits and tweaks can be made on the spot to improve and simplify your entire design and make it ready for the manufacturing process.
7. Simplify supply chains
Mass production is time-consuming and complex, with plenty of small actions required before launching your finished product in the market. It depends on different parts and departments to create a codependent environment, and the construction will be ruined even if one aspect falls apart. 3D modeling can simplify this process by conjoining manufacturing and design activities into an easy and quick setup. Creating a viable product with design firms is now possible with 3D modeling.
How Cad Crowd can help
At Cad Crowd, pre-vetted CAD professionals from around the world can help you with product design services for cost-effective production. All work is handled confidentially between you and your chosen designer. Get in touch to get a free quote on your project.