There’s no shortage of factors to consider when designing a new product to manufacture. Each factor can have a significant impact on the quality of the product, the efficiency of the manufacturing process behind it, and the profitability of the product.
With so many factors to consider and their significance to the project, how can a new product be designed efficiently by a manufacturing service? Luckily, there are systems far more advanced than the old ways of trial and error or just focusing on making each component as easy to produce as possible.
This is where Design for Manufacturing and Assembly (DFMA) comes in. It provides a comprehensive approach to design that considers factors that will be encountered during manufacturing and assembly.
What Is Design for Manufacturing and Assembly and How Does It Work?
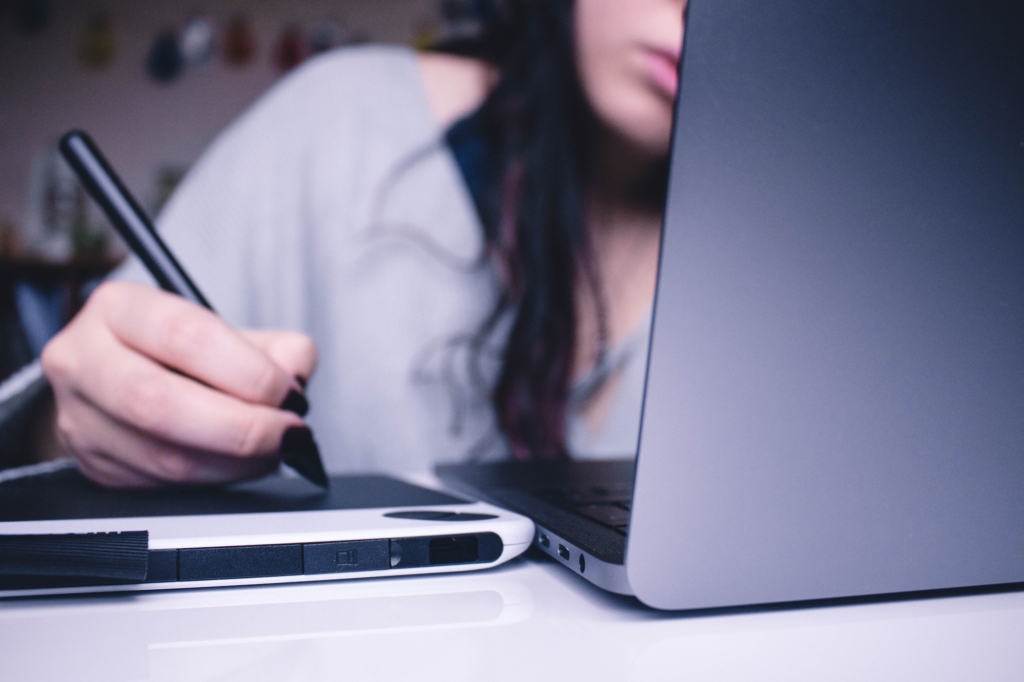
Design for Manufacturing and Assembly (DFMA) is a system of methods that aims to make the manufacturing of a product as simple and cost-efficient as possible. The primary goal of this system is to cut costs by identifying and resolving difficulties and inefficiencies that will be encountered in manufacturing. This work is done during the design stage to avoid costly mistakes such as retooling and redesigning processes.
This type of design method has been used in a variety of industries and more industries are turning to it as its benefits become more well-known. Essentially, Design for Manufacturing and Assembly combines the concepts of Design for Manufacturing with the methods of Design for Assembly. These design styles have been used by huge corporations to successfully create significant savings in the manufacturing process.
Since Design for Manufacturing and Assembly can be called a system of methods, there are numerous factors that are normally considered when it is applied to a new product. While each manufacturing situation is different, this type of design offers an intelligent and organized approach to creating the most efficient design for a new product. It is an appropriate choice for Lean Manufacturing, and it can bring numerous benefits to a company.
It has been documented that the most significant opportunity for cost-savings in the creation of a new product is in the design stage. When a product and its components are being designed is the most advantageous time to make changes. It is far simpler and less costly to make a change when everything still exists only as a drawing or a file.
In some situations, a change can be made to a master geometry file by an engineer in a matter of minutes. Compare that to finding out that a design change of a single component is warranted during the completion of the first batch of products. The further away from the design stage that a problem is noticed, the more costly it can be to correct, in addition to the cost already incurred by inefficiencies that could have been avoided from the start.
Factors Commonly Considered in DFMA
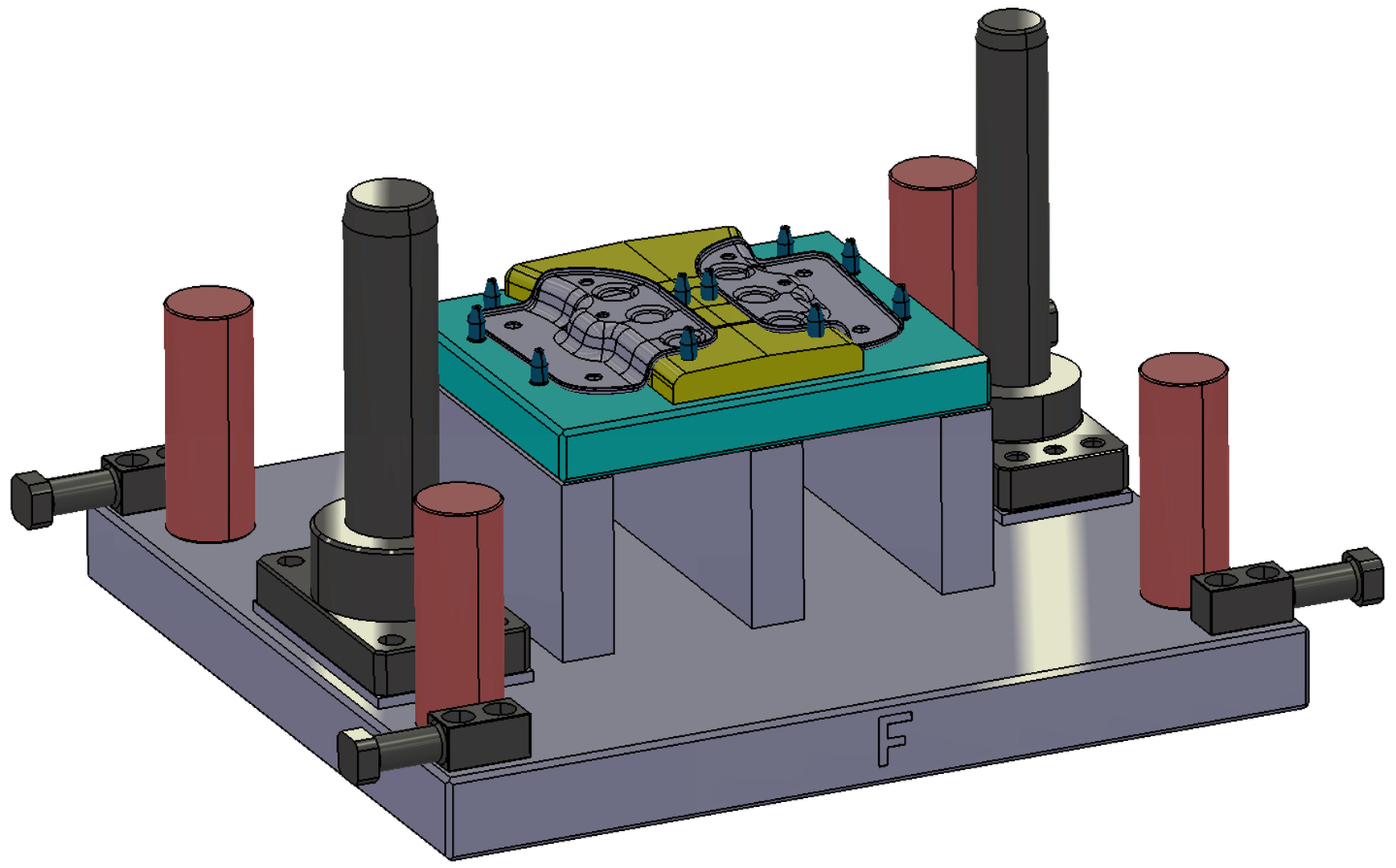
Once the initial concept has been created, it can be optimized using DFMA. When DFMA is applied to a product, it will be examined in a logical sequence to identify and eliminate as many inefficiencies as possible before production begins.
Fasteners
If a new product requires any type of fastener, this is one area that should be examined. While all varieties of fastener can be very useful in the right situation and they all have their place, they can also quickly increase the manufacturing cost of a product. In fact, in many cases, the cost of simply installing a given fastener during manufacturing can be far higher than the material cost of the fastener itself. Fasteners such as clips and screws appear to be very low in cost on paper, but the cost of installing them can negate any potential savings or worse depending on the situation.
DFMA commonly seeks to eliminate fasteners as much as possible for these reasons. Snap-fit components are favored with DFMA. Since the product is still in the design stage at this point, the designs of components can be changed to give them snap-fit functionality where possible. However, this is just one of many areas that are frequently targeted for optimization with DFMA.
Number of Components
The total number of parts in a product is another factor often examined with DFMA. It may be necessary for many specific parts in the product to remain as they were originally drawn. However, in a number of situations, it may be more beneficial to eliminate some individual parts or even combine them with adjacent parts.
For example, let’s say that within the product, there are two stationary parts in the product that are to be made from the same material. It’s possible that redesigning those two individual components into a single solid part may be more efficient and cost-effective.
Component Geometry
During the concept phase, the main emphasis is creating a working product. The original design may be inefficient for manufacturing in a number of ways, but that’s alright because of the optimization the DFMA can provide.
In addition to the number of components and the use of fasteners, the geometry of the product’s components should be examined as well. When looking at the shape of each part, things like symmetry should be considered. Is it possible to give the necessary parts symmetrical designs? If so, that might just be the way to go.
Symmetry is one component of a part’s shape, but sometimes making a part intentionally asymmetrical can offer advantages. This might be the addition of a large chamfer on a single corner, or the placement of a single smaller or larger corner radius on an otherwise uniform component. This particular type of modification is often colloquially referred to as “idiot-proofing” in design firms and job shops around the world.
On the subject of component geometry, another way to potentially optimize parts is to use identical parts. This may be possible in situations where a left and right version are already designed. Combining or modifying them into a single part that fits both locations could bring significant savings.
Manufacturing Process of Individual Components
During DFMA optimization, the means of manufacturing individual components of the product is another factor that needs to be examined. In the case of metal parts, should they be machined or fabricated? Perhaps they could be cast.
The best answer will always depend on the specifics of the situation. In the case of machining, more choices may emerge. Would wire EDM or conventional EDM be the most appropriate choice or is it more of a simple machine and grind type of part?
Shop floor workers are often a goldmine of information on this topic. Many of them will be more than happy to share their knowledge and perspective with you. The best process to create a specific component may be something that you aren’t familiar with, but shop floor workers see it all.
Of course, plastic components come with a similar range of process options when it comes to production. Does it need to be machined with high precision? Is it something that could be made with a mold instead? Is the best answer another process or perhaps another material entirely? Questions like these should be investigated by engineers, but shop floor worker and material supplier input could be quite valuable as well.
Materials Used for Parts
There are plenty of materials available and pricey specialty materials abound. However, the desired material for each component should certainly not be overlooked.
Even in simple scenarios, it may be possible to use a significantly less costly material for a given component that will still allow the part to perform its function. Different types of steel can easily be substituted in simple scenarios, sometimes the difference in price per pound can be drastic. In other cases, it may be more appropriate to switch the material from metal to plastic or vice-versa.
Tolerances
Tolerances can be tricky during the design process. Many have dreamed of a perfect world where parts are the perfect size each and every production run without fail. When this desire is unnecessarily reflected in the expected tolerances of components, the result can be a significant increase in production costs.
What it really comes down to is that parts with tighter tolerances take more time and workers with a higher level of skill to create. This is reflected in the prices that are paid for parts with tight tolerances whether those tolerances are actually warranted or not. If the tolerances of a part can be increased from +/-.0005” to +/-.001” without compromising function, then a substantial savings in the production costs of that component can be expected.
Benefits of Utilizing DFMA
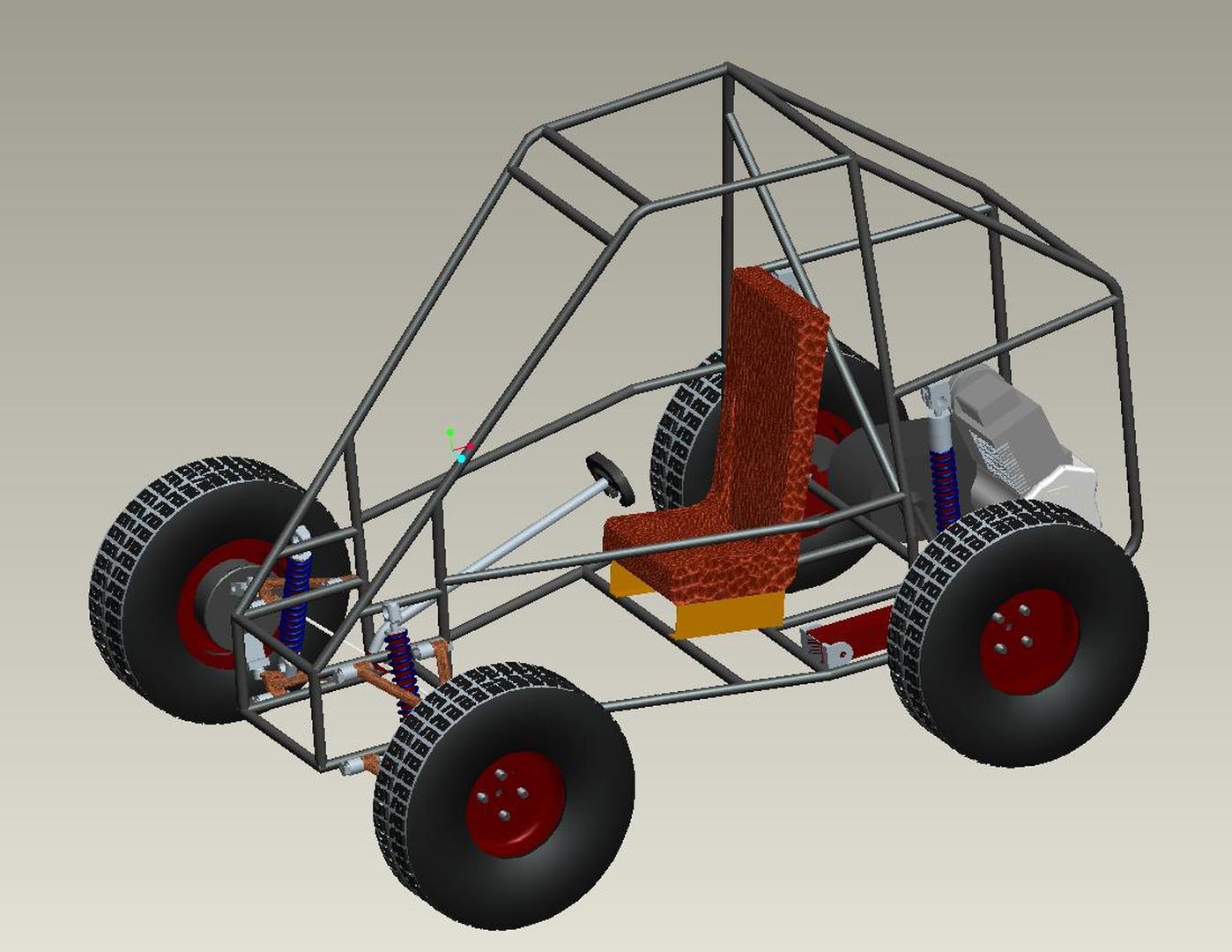
Benefit 1. Cost Savings
Given the comprehensive nature of DFMA methods, it should come as no surprise that the benefits can be quite far-reaching. The primary goal of DFMA is to cut manufacturing costs, and it can be used to do this quite well. However, it does it in such a way that it actually reduces or eliminates a number of the most painful problems that are typically associated with the creation of a new product.
So, DFMA initially cuts the total cost of manufacturing a product. Since work with DFMA ideally begins during the design stage, there are immediate savings in cost via minimizing wasted material, wasted labor, and unnecessary assembly time. However, as production goes on, these savings grow.
Sure, in some cases, it may involve a bit more upfront cost, but once the volume reaches a certain number, production is and will continue to be less costly. It’s also worth noting again that the largest opportunity for savings in the manufacturing process is during the design stage. The design stage offers the opportunity to get things right the first time and avoid as many inefficiencies as possible.
Benefit 2. Ease of Production
This is a direct result of the type of optimization that DFMA aims for. Since the principles of DFMA lead to more efficient production and processes, it has the potential to eliminate numerous design and engineering related headaches before they ever become a problem. It’s far faster and easier for everyone in the manufacturing process when inefficiencies are addressed and avoided before production begins as opposed to finding them, working around them for a period of time, and then eventually paying to correct them. Discovering difficulties in the manufacturing or assembly process that could have been avoided creates waste and headaches for everyone involved.
Benefit 3. Minimizing Mistakes and Tooling Redesign
This benefit ties in closely with the point just above. While DFMA can be applied to a product that is already in production, it has the greatest potential for benefits in the design stage. Very costly mistakes such as those leading to retooling and tooling redesign can often be avoided.
The potential savings of minimizing or avoiding each inefficiency only increases with production volume. Just imagine the cost of redesigning and retooling an entire production line compared to the cost of a few more hours spent on the design.
Benefit 4. Simplifying Assembly
Assembly can be a very costly part of the manufacturing process depending on the methods used. Turning to fasteners again as an example, it typically costs more to have the fastener installed during assembly than the unit price of the fastener itself. This is not the only scenario where this point holds true. Another appealing benefit of simplifying the assembly process is that it can result in faster production times.
Benefit 5. Reduced Lead Times
While a lot of the emphasis with DFMA concepts is applied to cost reduction, it is possible that many modifications will ultimately result in shorter lead times and production times. Considering the sizes and shapes of readily available stock materials is a prime example. It’s great to minimize manufacturing costs, but additional production speed without a loss in quality also has plenty of its own appeal.
Industries Utilizing DFMA
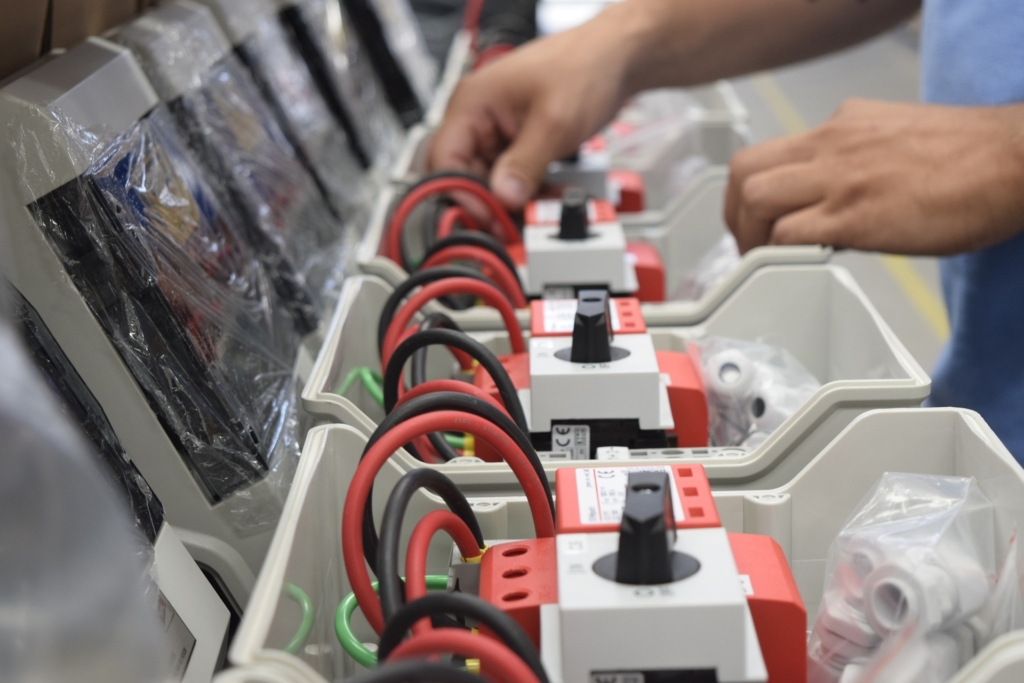
One of the earliest major successes of DFMA application on a large scale was experienced by Ford with the Taurus. This occurred during the 1980s and according to Ford, the company had saved a billion dollars. That is a tremendous figure and it’s illustrated by a household name, one that had its place in pioneering manufacturing at that. DFMA is a very valuable tool not only for the automotive industry.
As DFMA and its value have become more well-known over the years, its use has spread to numerous other industries. Perhaps most notably, it has been used in the design of numerous medical products, particularly medical device design services. In addition to being utilized in the medical industry, DFMA has also been applied to products in the oil and gas industry where both production cost and speed are significant factors. Interestingly enough, in some cases, a DFMA approach has found that re-shoring is a more efficient and less costly decision than continuing overseas production.
The examples mentioned here are mainly high volume production. Automotive, medical devices, and oil and gas all frequently require tremendous numbers of parts and products.
So where does that leave lower volume products? DFMA has successfully been utilized for much lower production levels as well. In some cases, only a few thousand units were required to reach the point where savings were achieved. The most likely small volume products to benefit from DFMA tend to be complex rather than simple.
Specific DFMA Tips to Consider
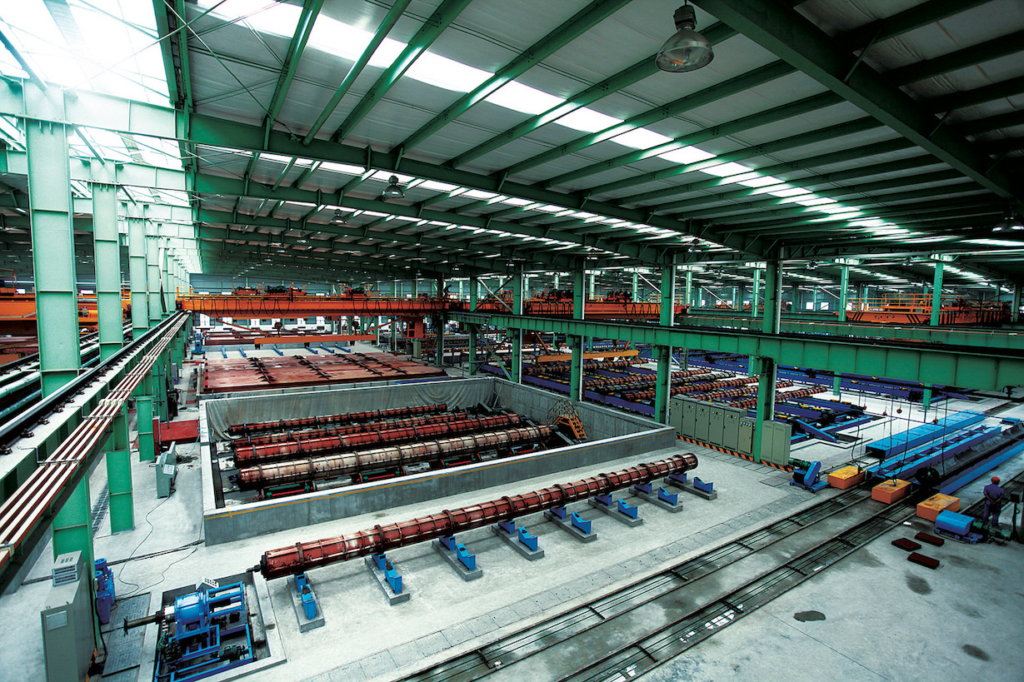
- Take advantage of larger tolerances when possible – The amount of tolerance that is labeled as acceptable on a given part will have a direct effect on the cost of producing it. Significant reductions in cost can be had by making tolerances no smaller than +/-.001”. This keeps a wider range of production methods available as well. For example, there are a larger number of ways to make a part with a +/-.005” tolerance than there are to make a part with a tolerance of just +/-.0005”.
- Material shapes and sizes – Both the standard shapes and sizes of the desired materials should be considered. Parts that are close to a standard, readily available size of stock material can be produced faster and with less waste than those with more challenging shapes or dimensions that are very different from most standard stock sizes. Most material suppliers will happily supply a list of their standard sizes that are kept on the shelf. Aiming to use standard material sizes also helps to cut lead times on production.
- Pay attention to dimension ratios in pockets – If a part requires a machined pocket, be careful when designing it. The size of the corner radius will determine the size of the tool it can be cut with. If a pocket has small corner radii, keep it shallow if at all possible. Be generous with the size of all corner radii if it’s feasible. If the pocket has dimensions that would make it particularly challenging for a mill, then conventional EDM can offer a possible alternative.
- Hole style, depth, and threaded holes – Blind holes can be challenging to add to a part, especially in the case of harder materials. Use through holes whenever possible. In the case of tapped holes, larger tolerances can help to reduce costs. When the thread depth is given a tight tolerance, this adds to production cost and overall component price.
- Consider setup times – If a part is to be produced by machining, then the number of setups required to make that part can be a critical factor. Designing a part that requires multiple setups will result in a more costly part as opposed to something that can be created in a single setup.
- Thin, fragile, and narrow features – All of these features can increase the production costs of a part quite quickly. Features that are thin, fragile, narrow, or some combination of the three are often very challenging to make. They will require more time, more skilled workers, and will likely result in an appreciable amount of waste. In addition to that, such features often do not fare well during the assembly process. This may lead to additional waste on top of already high prices.
- Chamfers and fillets – It’s good practice to use chamfers to break outside corners when necessary. In the case of internal corners where clearance is needed, opt for a radius if possible. Breaking edges and creating clearance this way is often the most cost-efficient. On the other hand, opting for external corner radii on a part can quickly increase the cost without offering any additional benefit over a chamfer in many situations.
- Straight edges have their place – In addition to minimizing the number of necessary setups for making a part, some things can also be done to make the setups that are necessary as simple as possible. For example, leave the outside edges of parts straight and parallel when possible, especially when it is a part that will be made from bar stock. This will help to allow them to be set up quickly and easily during production.
- Reduce adjustments when possible – Parts that offer adjustment are often both complicated and costly to produce. Some types of adjustments can be built into the design without moving features, such as extra clearance on slots and bolt holes. Try to reduce or remove moving features if at all possible.
- Simplify the assembly process – This goes hand in hand with a number of the previous tips and concepts, such as opting for snap-fit parts over those that require fasteners and reducing the number of parts where possible. When simplifying the assembly process, consider things such as the way parts fit together, the amount of handling that will be necessary, and the total number of setups that will be required to complete the assembly process. The less setups that are required and the less handling that there is, the lower the cost of assembly will be.
- Be open to feedback and seek it out – Once the product and its components are being produced, take some time periodically to check in with personnel at all stages of the manufacturing process. From shop floor workers and assembly to suppliers, each may be able to provide insight from their unique point of view about ways to make production more efficient.
- Choose finishes and secondary operations carefully – Coatings, very fine finishes, and secondary operations can all increase the cost of a part or product very quickly. For many internal components, lower quality finishes can be acceptable. They will not be seen by the customer, and as long as a reduction in finish quality does not impede function, it’s a prime opportunity to cut costs.
Q&A
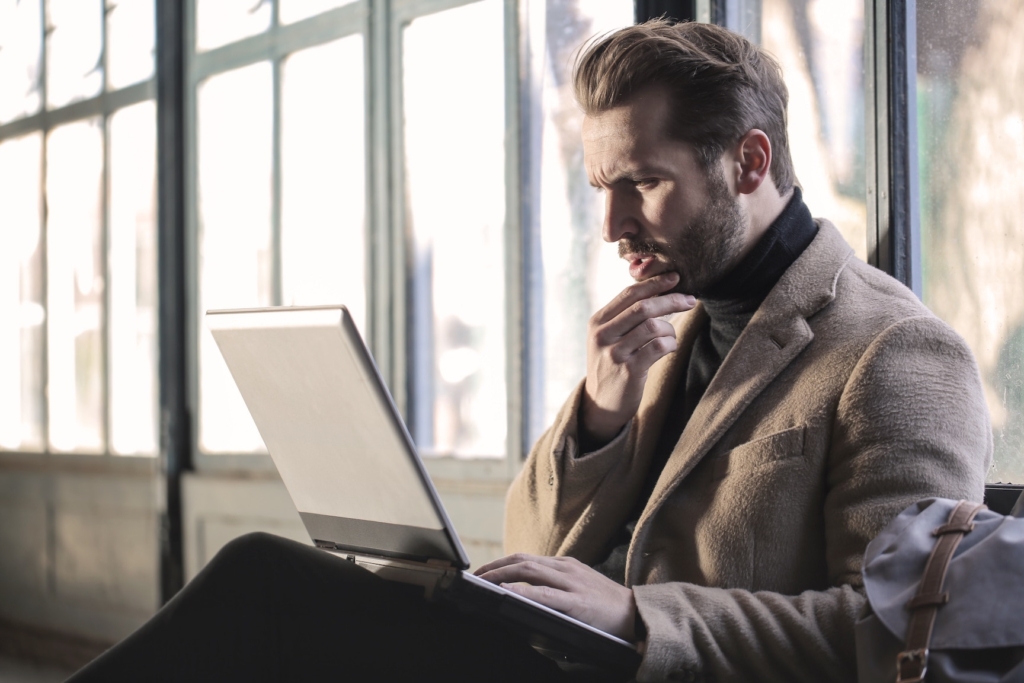
How much can DFMA cut production costs?
Of course, this varies from one situation to another and is directly tied to the specific circumstances involved. That being said, Design for Assembly alone can often create a reduction of approximately 25% in manufacturing costs. When combined with Design for Manufacturing and using the full DFMA toolbox, it is reasonable to strive for an even larger reduction in manufacturing costs.
How was DFMA created? What is the history of DFMA?
The research that led to the creation of Design for Manufacturing, Design for Assembly, and ultimately Design for Manufacturing and Assembly began decades ago. Much of it was conducted in the United States by University of Massachusetts Professor Geoffrey Boothroyd.
He was later joined by Dr. Peter Dewhurst and the duo formed Boothroyd Dewhurst Inc. It was around this time that they released their first software package for the Apple II, which was soon followed by a PC version. The DFMA methods have saved major corporations billions of dollars since implementation. Boothroyd and Dewhurst were also recognized for their contributions to manufacturing by President George H.W. Bush. They were awarded the National Medal of Technology.
Definitions
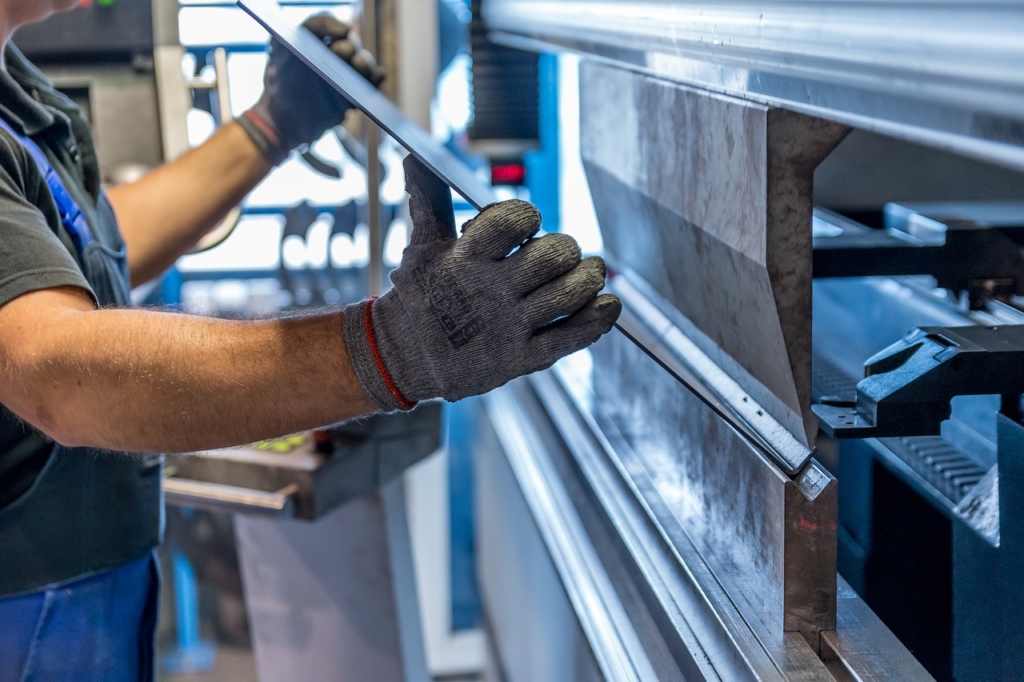
Design for Manufacturing – Designing parts to make the manufacturing of the product’s components as efficient as possible.
Design for Assembly – Designing the product and its components to cut assembly costs by focusing on efficiency and ease of assembly.
Design for Manufacturing and Assembly – A proven set of methods that is a combination of Design for Manufacturing and Design for Assembly. The goal is to lower the production cost of a product as much as possible by considering both the way the components are created and the way that they will element in the final product.
Tolerance – The acceptable range in finished dimensions of a part. In relation to DFMA, tolerances are examined as another potential way to reduce manufacturing cost. Parts that must be made to smaller tolerances generally cost more than those with more generous tolerances.
Conclusion and Next Steps
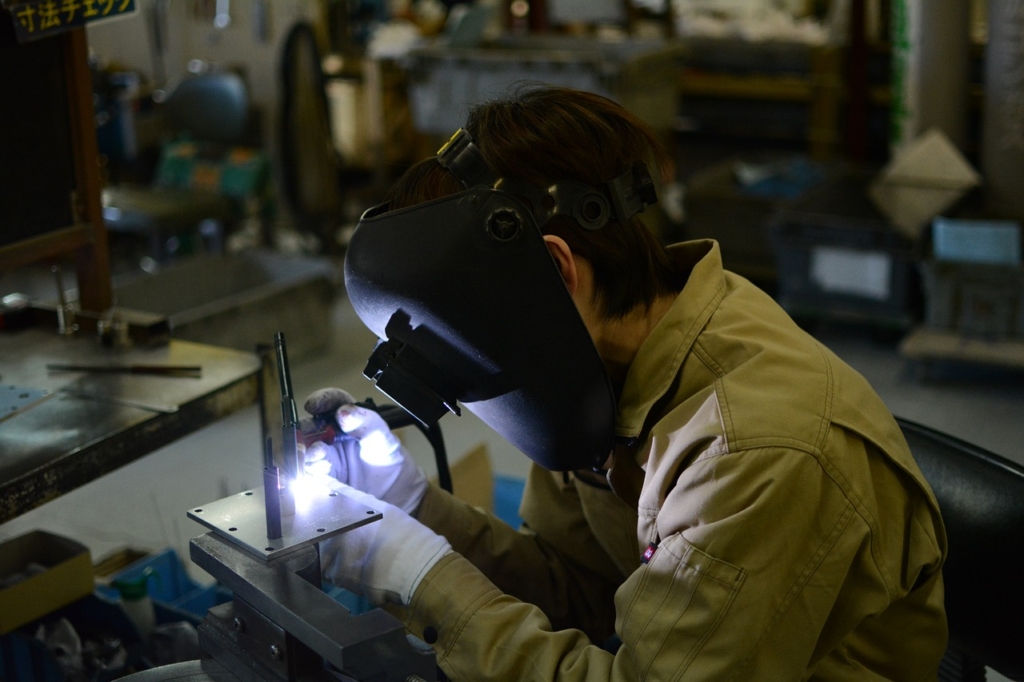
DFMA design and its concepts are a fascinating topic with plenty of reach and very valuable real-world application. The core ideas that drive it are rather simple though, and that’s a great thing. This alone makes it very easy to see if DFMA is something that can be of use to you and your business or not.
Are you designing or contemplating a product that will be manufactured? If so, then DFMA services are certainly worth investigating at minimum. Depending on the circumstances and intended scale of production, it could be an excellent decision—one that could bring immediate and lasting benefits.
Feel free to research DFMA further. In fact, the more research that you do, the more likely you’ll be to make the most appropriate decision for your circumstances.
Cad Crowd Has DFMA Talent

However, if you already know that DFMA services are something that will be beneficial, Cad Crowd can help. Here at Cad Crowd, we are always keeping an eye on engineers and designers that consistently do great work. If you need a DFMA freelance engineer to help with your project, we can help you find the one that’s best suited to your specific needs.
Of course, we aren’t watching everything that these engineers do. That’s their business, and we respect privacy. We regularly hold contests to see who displays the most design talent. In addition to contests, freelancers must be vetted to be added to our talent pool. If you browse through the available freelance engineers at Cad Crowd, you will only find those who are experienced, proven, and trusted.
When you bring your design project to Cad Crowd for professional manufacturing services, you can be sure that your project will be protected and you will receive expert assistance. It’s standard procedure to use NDAs for projects brought to Cad Crowd and the intellectual property rights go to you.
You don’t have to wonder or negotiate about rights and privacy—find the professional that looks like the best fit for the project and let them get to work. If you’re ready to confidentially see what DFMA can do for your project, then get a free quote today.