Any product designer with a great and new idea wants to realize it as soon as possible in any way. Unfortunately, an idea will only be great if a manufacturer can use materials and machines to turn it into reality. This is where DFM companies or Design for Manufacturing enters the picture. For some designers, the manufacturing stage is only a speck in the entire process. It’s often one of their most minor concerns. However, this kind of approach can be hazardous regarding product design.
Manufacturing and design will always be together, whatever happens. This is why this neglectful approach will eventually result in an inferior end and low-quality product. This article guides the company’s success in designing new products for manufacturing excellence.
Table of contents
RELATED: 5 Reasons to hire a CAD design specialist to bring your company’s concept to market
What is DFM?
DFM, or design for manufacturing, refers to designing products, components, or parts for easy manufacturing to produce a better product at a reduced cost. The product’s design is simplified, optimized, and refined to do this. DFMA (design for manufacturing and assembly services), is often interchangeably used with DFM.
There are five principles assessed during a DFM. These include:
- Compliance/Testing
- Design
- Environment
- Material
- Process
DFM design services for your company should ideally take place early on during the design process, way before the start of tooling. Aside from this, properly executed DFM must involve all stakeholders, from engineers to designers, material suppliers, mold builders, and contract manufacturers. The purpose of cross-functional DFM is to challenge the product design. The new product design is scrutinized at every level, including holistic, component, system, and sub-system levels, to ensure the optimization of the design without unnecessary cost.
RELATED: Why prototype DFM services are useful for product design at companies and firms
Changes will get more expensive and tricky as the product design moves through the product’s lifecycle. With early DFM, you can execute changes in design faster at the most affordable location. Pulling stakeholders together early on during the new product development design process is easier. However, even when you already have an established product design, one necessary element of a systematic DFM is challenging the original product design.
Product design errors are often repeated by copying an earlier design. Make sure you question every aspect and element of your new product design.
- Check the original drawings.
- Disassemble the product.
- Study the near-neighbor and competitive products together with the lead users.
- Sit down with the contract manufacturer, who might have already solved the issue with another client.
- Is there someone else who solved the issue in another way?
- Can you make it better in any way?
RELATED: 8 tips companies use to simplify design manufacturing or design for manufacturing
There is a lot of effort, time, and thought to go into prototype DFM services, making it a meticulous process you can’t take for granted. That’s why you need the help of experienced design for manufacturability experts.
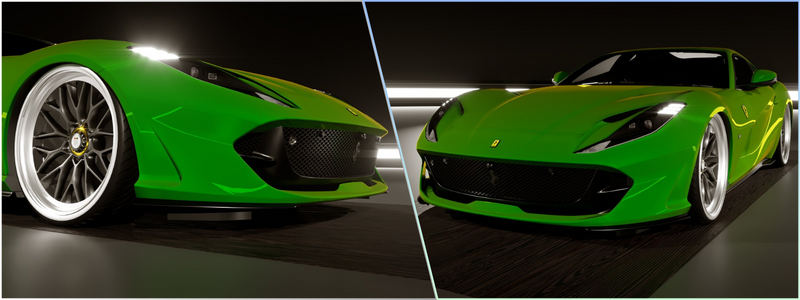
Five key principles of DFM
Testing or compliance
Every product should adhere to quality and safety standards. These are sometimes industry standards; some are third-party standards, and the rest are internal standards specific to a company. The manufacturer you choose must have testing facilities certified by the ISO. This is also when you should learn who will perform the ETL, UL, and other similar third-party testing and where the testing will take place.
Design for manufacturing
Product design companies play a critical part in DFM. The actual drawing of a product design or part must conform to sound principles for manufacturing for your chosen manufacturing process. Ensure that you discuss the product design with the product development expert, who will confirm that your product design will adhere to the excellent manufacturing principles for the chosen process.
RELATED: How to save money on injection molding: 10 tips from an engineering design firm
Environment
Your product or component should be engineered to withstand the specific environmental conditions and challenges it will encounter. Even the best forms worldwide will only be helpful if the part can function correctly under normal operating conditions. A design engineering professional can help your company develop a product for the environment in which it will be used.
Material
You must also choose the suitable material for your new product or part. Several criteria should go into this decision. The following are some of the material properties you should consider throughout the DFM or DFMA process:
- Color – What is the specific color of the part?
- Electrical properties – Should the material be a dielectric or insulator instead of a conductor?
- Flammability – How burn or flame-resistant should the material be?
- Mechanical properties – What is the preferred strength level of the material?
- Optical properties – Should the material be transparent or reflective?
- Thermal properties – How heat resistant should the material be?
Consider talking about the material with the contract manufacturer because they might have access to the existing materials in their portfolio, which will let you score a lower price.
RELATED: 10 key factors for managing manufacturing costs for your company’s new products
Process
You should choose the appropriate manufacturing process for the product or part. The last thing you want is to use a highly-capitalized process, for instance, mold and die design services involving the development of dies and tools to produce a low-volume part that could have been otherwise made using a method with a lower capital, such as thermoforming.
To determine the suitable manufacturing process for you, the DFM should consider how many parts will be made, the specific material that will be used, the required tolerances, the intricacy of the surfaces, and whether there is a need for secondary processes.
What factors affect DFM?
DFM’s ultimate goal is to lower manufacturing costs without making any compromises in terms of performance. Aside from the main DFM principles stated above, the following are equally important factors that may significantly impact the design and manufacturing of assembly.
RELATED: New product development and design: should your company work with a product design team?
Come up with modular assemblies
Using modular assemblies or non-customized modules in your product design will allow you to tweak the product without the risk of losing its functionality in general. An excellent example of this is automotive design firms creating a primary automobile that will let you integrate extras by including a modular upgrade.
Identify surface finishes that are considered acceptable
Try to strive for function instead of flashy for the surface finish, except if it is intended for a trade show grade.
RELATED: New concept design costs, engineering prices & product development services rates
Design for an efficient joining
Is it possible to clip or interlock the parts together? Discover different ways to join the parts without using adhesives, fasteners, or screws. Below are a few helpful tips if you need to use fasteners:
- Try to minimize the variation, size, and number of fasteners.
- Avoid screws that are too short or too long, flatheads, round heads, tapped holes, and separate washers.
- Use chamfered and self-tapping screws to ensure better placement.
- Stick with standard fasters as much as possible.
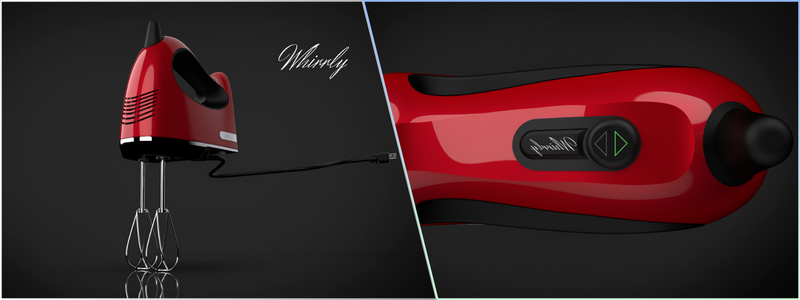
Minimize the number of parts
Lowering the part count in a new product design is the fastest and easiest way to lower the cost since you are also reducing the quantity of the required material, the labor involved, production, the amount of engineering, and the shipping costs.
RELATED: Tips for engineering your company’s new product concept to be manufacturer-friendly
Reduce reorientation of parts during machining and assembly
Designing the components to minimize the need for manual intervention during assembly and production is crucial. In this regard, leveraging DFMA (design for manufacturability and assembly) designers can prove highly beneficial.
Standardise materials and parts
Customization and personalization are time-consuming and expensive. Quality standardized parts can reduce production time because these parts are often available. It also gives you more assurance of their consistency. The material should be based on the new product’s intended use and planned function. You have to consider how it should feel, whether soft or hard. It’s also important to check if it needs to endure pressure. Finally, you must also determine if your product or part needs to conduct electricity or heat.
Streamline the number of manufacturing processes or operations
When making your product involves a more complex process, it will also introduce more variables for errors. Always remember that every process will always have its own set of capabilities and limitations. Only include operations critical to the new product’s design and its function.
RELATED: A product designer’s guide to design for manufacturability
How Cad Crowd can help
DFM can work wonders to guarantee operational efficiency and inspire collaboration among international suppliers across vendors and departments. With industries across different sectors expanding and creating more intricate product designs, companies can use DFM services or DFMA services to achieve their goals for launching. Companies require effective methods to lower costs, eliminate delays, increase quality, and simplify processes.
DFM can expedite product development timelines by identifying and rectifying design flaws, thereby preempting costly design revisions and issues. Cad Crowd can help you find product design experts who assist with the DFM process. As a trusted platform for professionals, you will never have to look hard to meet the perfect partner for your product manufacturing and ensure your company’s success! Contact us for a free quote.