There have been minimal improvements when it comes to construction practices used and enforced in the industry. These techniques, which seem to be the standard since the Jurassic era, have produced houses and buildings that have been criticized as inefficient in terms of cost, design, and overall aesthetic. Many houses even fail to cater to the current market demand.
But of course, if you want to stay ahead of the curve and achieve success in the progressive residential construction industry, you need to think outside the box and explore more modern solutions. Catering to the ever-evolving market, the demand cannot be fulfilled by simply generating more and more houses. The solution should be as innovative and new as the continuously improving technology and practices. One key methodology gaining traction in today’s construction industry is DFMA or design for manufacturing and assembly services.
DFMA is a methodological approach that optimizes the design process to allow a more efficient and seamless assembly and manufacturing. It ultimately leads to standardization, which will give you and your company faster construction timelines and cost savings. This article will share with you how building design and construction companies can take advantage of DFMA to design affordable homes.
🚀 Table of contents
DFMA at a glance
DFMA, or Design for Manufacturing and Assembly, is a framework focusing primarily on designing products that can be manufactured and assembled easily. This design process is not something that is new in the industry; it has been used since the 1980s to minimize the overall costs of computer hardware, consumer appliances, automobiles, and even airplanes.
These products are designed and crafted by DFM design professionals using individual components and parts that are aligned to be built and assembled in a factory setting. The buildings that will be worked on are considered products that can be split into several modules that can be built step by step and part by part. These modules which can consist of different parts and workings, are repeatable, interchangeable, and standardized.
Benefits of DFMA homes
Houses built using DFMA aim to lessen a large chunk of lifecycle costs, including build cost, construction and design time, carbon intensity, and household energy consumption while improving construction productivity.
RELATED: 5 Reasons to hire a CAD design specialist to bring your company’s concept to market
Expected economic benefits of DFMA housing projects
- It allows other registered providers and 3D designers to reproduce the business model in partnership with the rest of the group to achieve a multiplier effect.
- It reduces labor requirements per house, improving the industry’s resilience to a labor shortage, an existing concern that might only worsen over time.
- It creates new business opportunities for suppliers.
- It cuts down regional construction costs and speeds up delivery time to meet the targeted deadlines.
- It decreases the energy bills of homeowners.
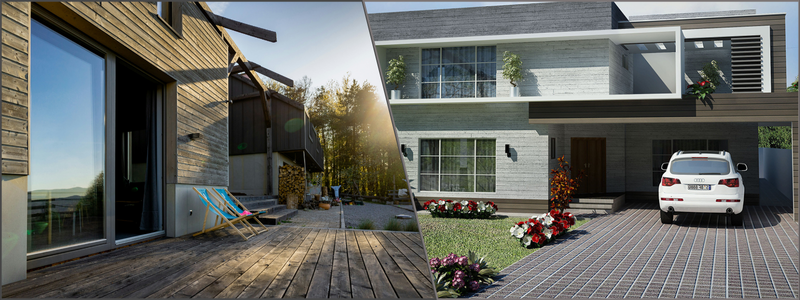
- It creates a safer work environment for the production process compared to traditional onsite production.
- It creates new skills and roles for future use.
- It improves quality of life by creating a more comfortable living environment and disposable income.
- It provides faster access to affordable or social housing.
RELATED: Smart manufacturing using CAD design is the future for OEM’s
Reasons why the modern construction industry moves towards DFMA
- The ultimate outcome of 3D construction rendering services and design is to create reasonably priced buildings within an accepted timeframe. DFMA or prefabrication is a good example since it uses modular construction drawings and already manufactured construction drawings. Once combined, these techniques and modules simplify the manufacturing part by outsourcing different offsite components which will give you a balanced performance, quality, and a more acceptable cost.
- In DFMA drawings and models, assembly and manufacturing are elegantly intertwined together to have a simple, efficient, and error-free construction. However, just like other combined processes, DFMA might present complications and challenges at one point. However, the perks of reducing materials, overheads, and labor costs offer the ultimate solution to achieving success with minimal wastage and higher profit margins.
- During product assembly, DFMA follows a meticulous design review process. It identifies optimal part design of products as well as cost-effective and efficient production methods that cater to the requirements of the designers and the rest of the team members.
- Entire units or parts of the building’s construction are crafted in a factory setting or an actual factory away from the construction site before being transported to be installed on the site. Prefabricated construction modeling and DFMA encourage seamless collaboration between project design and production, making the products more cost-effective and reliable.
RELATED: DFM For new product design excellence: complete guide for company success
Other perks of DFMA
Here are other reasons to take advantage of DFMA for designing affordable homes:
Ability to test
It’s possible to consider offsite solutions early on in the planning stage with the help of building information modeling experts or the BIM process. BIM aids in delivering prototype specifications to allow extensive testing. Models can also undergo virtual testing before companies invest finances in their actual prototypes.
Cost
Fewer parts are used in DFMA, which eliminates unique parts and cuts down the labor count for assembly. It also uses standard hardware and parts, reducing the need for assembly tools and thus further decreasing the costs involved. The DFMA process offsite is predictable and not prone to delays and material damage due to weather, helping save overall costs. It’s also possible to use the same parts interchangeably for product manufacturing, decreasing the number of parts and costs.
The application of total quality or operational management tools can help fulfill future volume needs. Projects involving repetitive structure elements, such as supermarkets, malls, colleges, schools, hospitals, and hotels, can also significantly benefit from DFMA, as it easily replicates elements in larger quantities after choosing the design.
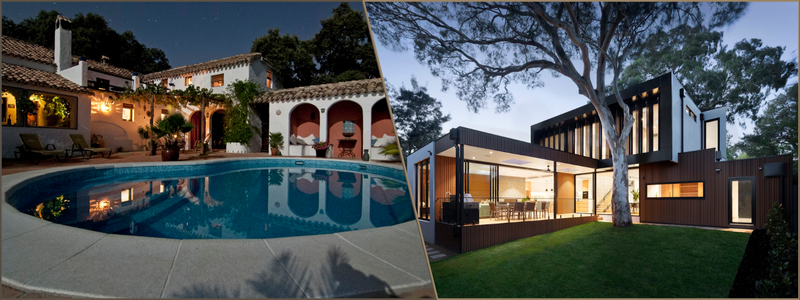
Availability of resources
Construction in a different environment requires less onsite labor to relieve shortages in skills. Onsite resources are necessary only for the final installation of assembly instead of the design, manufacture, and complex assembly of parts and components.
Safety
Entire buildings or components can be reconfigured and transferred to different sites to ensure improved safety of future deconstruction of buildings. Prefabrication work in controlled factory settings is done following controlled and safe protocols for health and safety. The site also has more spaces and fewer external factors for various trades taking place within the same space.
RELATED: 8 Tips companies use to simplify design manufacturing or design for manufacturing
Simplified manufacturing activities
DFM experts help optimize and simplify the manufacturing process, particularly through modules. The modules in the product design resulting from prefabrication can simplify testing, inspection, redesign, purchasing, assembly, service, maintenance, and the rest. Assembly is also simplified through self-locating and self-aligning parts, including molded keyways, chamfers, indentations, and projections. DFMA also reduces elements for interconnections.
The interconnected parts are flexible and can be used to connect two more parts. The harnesses guarantee unique connectors prevent misalignment. It also simplifies inventory and improves servicing and maintenance processes. Modules can make the redesign process more versatile to help with testing before the final assembly and allow the use of standard elements to cut down product variations.
DFMA also avoids multiple cleaning and solder steps. Prefabrication also simplifies the identification of problems and the assembly process’s operations. Self-contained and separate modules also require fewer tools with reduced disassembly and overall repair time. Using multifunctional parts also allows the execution of several constructions by just a single part, thus making the procedure less complex.
Site space
DFMA also offers huge benefits to sites with limited access, limited space, and complex logistics ,such as city center locations and airports. Even sites that don’t have house storage and those that can handle the delivery of semi-prepared or raw materials can also benefit from DFMA. Offsite prefabrication also results in less labor and material onsite, thus opening up more onsite space.
RELATED: Leading home design & modeling 3D technology for builders, companies, and firms
Speed
DFMA helps eliminate or reduce interfaces, which decreases assembly time. The use of standard assembly practices like self-aligning parts and vertical assembly cuts down assembly time as well. Products made through DFMA can also smoothly and quickly transition to the production stage. This reduces the time required for the product to travel from the conception phase to its ready-for-market phase.
Stack or vertical assembly also requires less reorientation of parts to speed up the process. Self-aligning parts like roller bearings, ball bearings, and washers don’t require additional reorientation or adjustment to save time. Remedial or snagging works also take less time. It also regulates and controls the reworking and sequencing of trades to cut down some of the more common onsite delays.
The manufacturing process can also be designed to pay close attention to the smooth flow of materials, reduced number of material moves, reduced brazing and welding, use of easy-to-control processes, separation of mechanized and manual operations, and simultaneous performance of similar operations.
How Cad Crowd can help
Needless to say, the use of DFMA for home building design and construction companies offers a long list of benefits. Ultimately, the best DFMA solution will only be possible with the help of experts. Contact Cad Crowd, and we will help you find the right experts for your DFMA projects!