After design for additive manufacturing services or 3D printing was first used, among its earliest commercial adopters was none other than the aerospace industry. You might not even realize or notice it. Still, the truth is that numerous government agencies, suppliers, and OEMs have already been using 3D printing for years, with the newest commercial airplane generation now flying with more than 1,000 3D-printed spare parts. Continue to read below to learn the different applications of 3D printing for companies that belong to the aerospace industry:
Table of contents
Applications of 3D printing in the development of aerospace products
1. Functional testing of rockets
Jet suits that seem like they are taken out of a sci-fi film are under development with Gravity Industries. These are meant for applications in search and rescue inaccessible or not feasible for safe landing of helicopters. Different types of 3D printing technologies have sped up the process involved with prototype design firms and testing, including specific tests where the best option available was thermoset photopolymer resin. The lead designer and test pilot, Sam Rogers, used parts on Form 3’s Clear Resin to come up with the design for the rocket engine igniter that is vortex-cooled.
RELATED: How the aerospace industry is using CAD design services: drafting, modeling, and prototyping
This transparent material is ideal for the environment for testing, allowing Rogers to observe the combustion patterns on the test rig’s interior. It would have been notably expensive for Rogers to use metal to get several design iterations. However, due to the short tests and low cost of materials used for the parts, he opted for a high-performance design with more down lead time and expenditure.
2. Development of complex rocket parts
Specializing in vertical landing rocketry and takeoff, Masten Space Systems started to 3D print rocket engines back in 2014. They developed small test thrusters at first and soon scaled up to a thrust broadsword engine weighing 25,000 pounds in 2016. The additive experience of the company includes metals and plastics alike.
Masten’s test and research engineer, Kimberley Devore, stated that the company has used 3D printing services and traditional machining for rocket engine production. Although Masten continues to use several traditional manufacturing for their older engines, the company has already welcomed 3D printing for faster production and more flexible designs. Thanks to 3D printing, it costs them little to add complexity to enhance performance or take risks.
RELATED: Freelance aerospace engineering services, cost, rates, and pricing for companies
3. Aerospace tool prototypes
It takes both time and skill to program CNC machines. 3D printing is a practical tool to create production costs or prototypes at a lower price at a faster speed, as long as the part isn’t metal. A&M Tool and Design develops custom machines and parts for optics, robotics, and aerospace. The shop became more modern to launch new equipment, such as 3D printing, retrofitted solutions, and reliable traditional technology.
The shop started using 3D prints for prototyping to test function and fit. 3D printing makes it possible for the team to produce parts much faster, use the entire day, set up prints to run through the night and use features the following day. It’s beneficial to use printing for geometries that are time-consuming and costly to produce using CNC machines.
RELATED: Benefits of outsourcing CNC machining services for your company’s prototype design
Applications of 3D printing in aerospace manufacturing
4. Electroplating and 3D printing end-use aerospace parts
Elliptika now enjoys faster creation of novel antenna designs and saves cash thanks to 3D printing end-use parts. The company specializes in developing and designing RF or radio frequency and microwave solutions and products. The company creates custom antennas and filters for development and research in education, medicine, defense, and automotive. As radio frequency designers, Alexandre Manchec and Gwendal Cochet wanted to minimize costs, deliver their designs faster, and achieve more complex geometries.
They have realized the importance of looking beyond traditional manufacturing techniques to meet these demanding parameters. The team at Elliptika has worked with several processes for additive manufacturing and discovered that SLA or stereolithography design for 3D printing is the most suitable match for electroplating, thanks to the printed parts’ smooth surfaces.
RELATED: Why businesses should consider 3D printing services and prototyping for product design
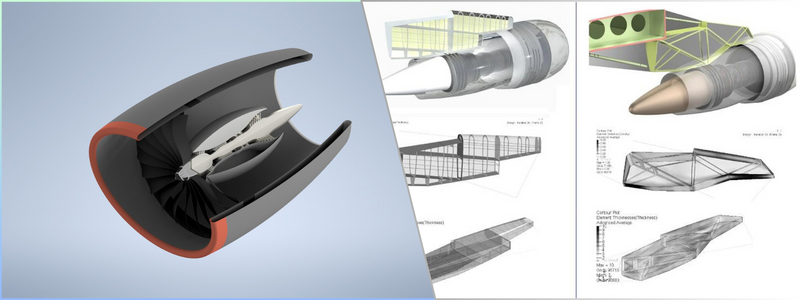
5. 3D printing of custom tools for aircraft parts
Lufthansa Technik is among the biggest aviation suppliers in the world that also provides MRO or maintenance, repair, and overhaul. The company’s proprietary Guide U escape route markings are developed to be installed in the aircraft cabins aftermarket. The ground-breaking floor markings are photoluminescent. It means they feature self-luminous color pigments that charge using the normal cabin light and remain glowing in the dark if an electrical emergency occurs.
Several fabrication processes and tooling materials were tested before production. 3D printing custom extrusion nozzles were discovered as the most flexible and cost-effective manufacturing method. The project engineer of Guide U, Ulrich Zarth, stated that theoretically, they could also injection mold their parts. However, they wouldn’t be too flexible in the nozzle’s adjustment and shape, which is where 3D printing comes in handy.
6. 3D printed masking jigs
AMRC Integrated Manufacturing Group works hand in hand with its industrial partners to come up with advanced technologies and create integrated systems. The company’s research group works on an Airbus project, Europe’s most significant aerospace manufacturer. This involved the high-tolerance machining and drilling titanium, aluminum, and carbon fiber components.
RELATED: Selecting materials for 3D printing your new product or prototype
After one hole is drilled to proceed with the next hole, the first one should be covered so that the generated scrap won’t cross-contaminate the second hole. The team initially tried using an aluminum piece with a tiny rubber O-ring, although it wasn’t enough to solve the issue. Two wrinkles were also added, with the caps required in various sizes. The team had just ten days to source 500 caps to beat their deadline.
Applications of 3D printing in aerospace education and research
7. Wind tunnel testing
Wind tunnel testing is conducted by the Texas A&M Oran W. Nicks Low-Speed Wind Tunnel for various projects. The engineer and manager of the company, Lisa Brown, assists researchers in developing their test plans, designing the models, and creating the code that allows them to accumulate relevant data. The team used 3D printing to build scale models for testing various objects.
The KIT or Karlsruhe Institute of Technology on the other side of the Atlantic Ocean also uses 3D-printed parts for wind tunnel testing. Lars von Deyn, a doctoral student, looked into methods of forecasting turbulent flows. Deyn’s work has the potential to inform the design and material options to lessen friction in mobility.
8. Space testing
Researchers at NASA are now studying the performance of electroplated SLA parts in space. The engineers at the Goddard Space Flight Center of NASA developed 3D printed brackets that were electroplated and then sent over to play on board a summer 2022 mission of SpaceX commercial resupply services (CRS-25) to the ISS or International Space Station.
RELATED: Additive manufacturing materials: 3D printing
Using Materials International Space Station Experiment (MISSE-16), the test platform of the International Space Station of Alpha Space, the samples will receive exposure to the space station’s external environment. They will be brought back for additional testing on Earth. The results can give a glimpse of how NASA, as well as other manufacturers in the aerospace industry, may integrate additive manufacturing and electroplating into their prospective product plans in the future.
9. Training of next-generation engineers
The United States Naval Academy hires young men and women who will become the U.S. Navy and Marine Corps’ professional officers. USNA’s Associate Professor, Captain Brad Baker, realized that the iterative process of his engineering students and their learning pace was affected by the absence of access to manufacturing abilities. Despite having a machine shop that caters to the student’s capstone projects, every team or individual could not create over three or four iterations within a year.
RELATED: 6 Ways 3D printing will change the world
The captain was one of many campus professors to provide his students with 3D printers for their coursework. However, he brought the manufacturing and design capabilities under a single centralized location when he launched MakerSpaceUSNA. He began integrating the machines into the mechanical engineering curriculum with only a couple of FDM or fused deposition modeling printers.
He made the devices accessible to students finishing their capstone projects. Upon entering the engineering curriculum, students first discover using CAD software, operating FDM printers followed by stereolithography (SLA), and working their way to SLS or selective laser sintering 3D printers.
They also discover more about 3D scanning services, allowing them to complete reverse engineering projects using their learned tools. MakerSpaceUSNA provides all USNA students the experience they need thanks to the reliable and high-quality printers that use SLS, SLA, and FDM technologies with a selection of technologies on additive manufacturing.
RELATED: 3D Printed threads and screws: innovative product design options for companies
How Cad Crowd can help
As 3D printing becomes more accessible and powerful, there’s no denying that the aerospace industry is now ready to welcome more contributions from other contributors. Cad Crowd keeps up with these developments as the platform grows with more selections of 3D printing professionals specializing in aerospace.