When you’re defining a new idea or trying to come up with one, there are a tremendous number of factors to consider. What’s the goal? What do we have to work with? Should we hire a freelance concept design service?
Fortunately, there are great solutions for all of those questions and more. Here, we’ll take a closer look at a handy tool for developing new products: design thinking.
What Is Design Thinking?
Design thinking is a specialized school of thought that is used to develop new products by product design services. One of the most significant differences between design thinking and other approaches is that this method focuses on the way that the product will be used and perceived by the end-user. This is a primary consideration the whole way through the process, from concept creation to prototyping and testing.
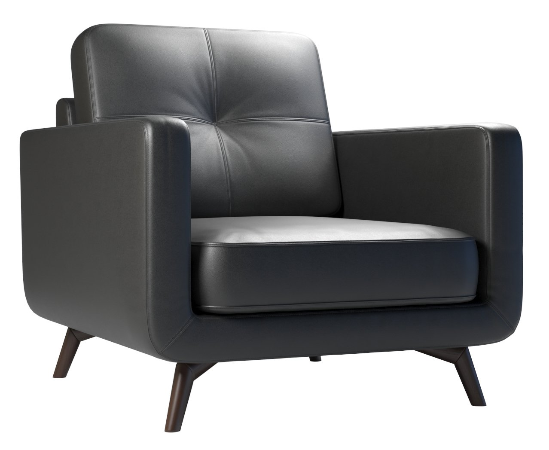
Many ways of thinking in the design field are focused on specific laws of physics, mechanical functions, and even factors like manufacturing cost. Since design thinking prioritizes the experience of the end-user over all else, it can lead to some very different choices during the development process. It is an appropriate course of action when you want to develop something that is going to be loved by the end-user.
RELATED: What Is Design Thinking and Why Is It Important for New Product Design?
Design thinking can be used for the development of any product or idea. It is regularly used by leaders in various industries and it is also taught at leading universities. However, for the purposes of this guide, we will only be focusing on the way design thinking is applied to the development of physical products.
The Stages of Design Thinking
In addition to focusing on the perspective and experience of the end-user, another defining characteristic of design thinking is that it is divided into clear stages. Depending on the circumstances, some stages may be repeated multiple times before reaching a final design that is ready for production.
Some stages may be repeated by industrial design services, and others may occur in a different order than what is outlined here. It all depends on what makes sense for your specific circumstances.
This is quite likely and is something that is just a part of new product development. You may be familiar with the prototyping process in general, but design thinking goes beyond prototyping. That being said, let’s take a look at the stages of design thinking and how they all work together.
Stage 1 – Empathize
Traditionally, the design thinking process begins with the empathize stage. One of the most critical things to do at this stage is to leave your assumptions at the door. This stage of the process is not about what you know; it’s about what you don’t know and what end-users experience.
If you’re working on a product that is relevant to an activity you’re familiar with, then it’s great to have that background, but remember to be open to the experiences of others.
Research during this stage is of paramount importance. Experts in the field should be consulted. Try to get as much insight as possible from relevant new invention design services. That being said, don’t overlook the average user. Their feedback is critical as well.
If you can, spend some time doing things that the end-user would do with the product. This kind of experience is as close to walking a mile in their shoes as you’re going to get.
Stage 2 – Define
The second stage of the design thinking process is the define stage. At this point, the goal is to take all of the experience and research that was compiled during the empathize stage and find a significant problem. It’s essential to keep these problems focused on the experience of the end-user.
In some cases, multiple problems may be identified. It’s possible that more than one problem may be solved by one innovative solution. Situations like this are rare but can lead to the creation of something that is truly revolutionary for a field. Working with a freelance product engineer will help.
However, it can be simpler if all of the research is boiled down to a single problem instead. This will allow for the creation of a solution that is as specialized as possible later.
Stage 3 – Ideate
During the ideate stage of design thinking is when you start generating potential solutions. However, there is another difference between design thinking and some other approaches that become visible here. When utilizing design thinking, you’re actively trying to look at the problem that you defined previously from new perspectives.
You want to see it from new angles so you can come up with solutions that are unlike what’s already been done before. Coming up with as many ideas as possible during this stage is ideal. You know all of them aren’t going to play out, especially when working from new perspectives, so you want to start with plenty of ideas.
Stage 4 – Prototype
The prototype stage of design thinking is much like the prototyping stage of other approaches. The most significant difference remains in the perspective. This is where the physical prototypes come into the picture. Physical prototypes will always be a necessity when developing a new product, but prototype design services who make virtual prototypes are very valuable as well.
Depending on the specifics of your situation, it may be better to get several prototypes with small differences instead of several identical prototypes. This just depends on your circumstances and any other parties or individuals that may be involved in the decision-making process.
Stage 5 – Test
Once you have your prototype, you have to test it. Now, from a design thinking approach, this may take several forms. Perhaps you’ll test it yourself. Maybe you’ll test it with some other decision-makers. Since we’re talking about design thinking, you’ll probably want to get some prototypes in the hands of end-users so you can get feedback directly from them.
What usually happens is that some additional problems are identified during testing. These may warrant a design change or perhaps even going in a different direction entirely. Either way, the knowledge gained from testing the prototypes is incredibly important for the success of the design, especially when it comes to getting a positive reception for the product and avoiding costly mistakes and revisions during full-scale production.
Repeating the Steps
Since design thinking is a human-centered approach to product development, new ideas and realizations could happen at any stage of the process. This is why it’s rather common to skip around and repeat various stages.
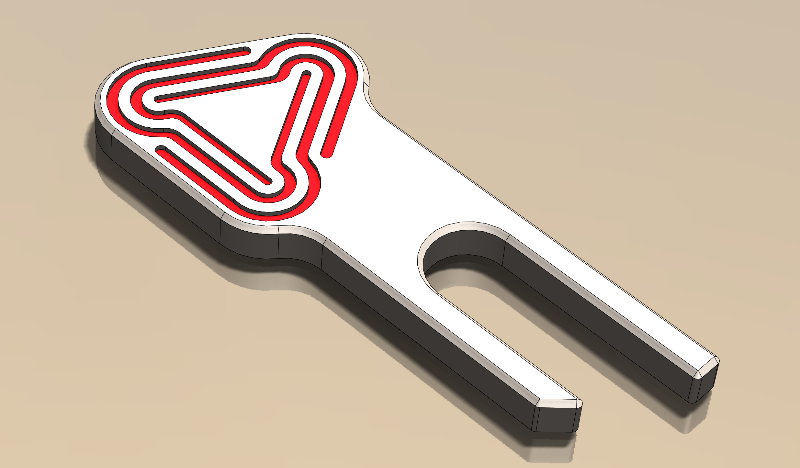
The five stages of design thinking are laid out neatly here, but in practice, it’s not always so organized, nor is it necessarily advantageous to strictly adhere to the textbook order. A human-centered approach by nature requires a bit of room for changes and flexibility.
If it makes sense to go back a step or two, then, by all means, do it. It’s likely to help you make the final product even better than it would have been.
Why Utilize Design Thinking?
There are many benefits that can be gained by using the design thinking approach. While it can be applied to the development of any new product, it has the most significant potential for creating new products for the consumer market. This is why 3D furniture design services practice this.
It’s no secret that in some markets, the experience of the end-user is the most significant factor in their purchase decisions. It can be even more important than cost, company reputation, or even visual quality. If the product provides the best experience of any choice on the market, then consumers in specific markets will gladly choose it over competing products.
If your company or idea relies on getting a great reception from a huge market or existing customer base, then design thinking is an excellent tool. It should absolutely be something that you take advantage of when developing new products. When well-executed, the research and ideas from the earlier stages of design thinking actually set a great foundation for marketing as well.
RELATED: How Cad Crowd Helps Inventors Design Innovative Products
Take the problems that the product solves and emphasize those points in marketing collateral. These benefits are likely to be what really set the product apart from everything else on the market anyway. Don’t be shy about these benefits of the product. If potential customers don’t know about the product’s unique benefits, then you can’t expect them to choose it for those benefits.
Tips for Designing
Focusing on the user’s experience as well as their problems and perspectives is central to design thinking. That being said, once an innovative solution has been identified, solid design concepts should not be ignored.
Instead, they should be implemented from a secondary perspective. Utilize them where they fit, but not at the cost of compromising the core function or idea.
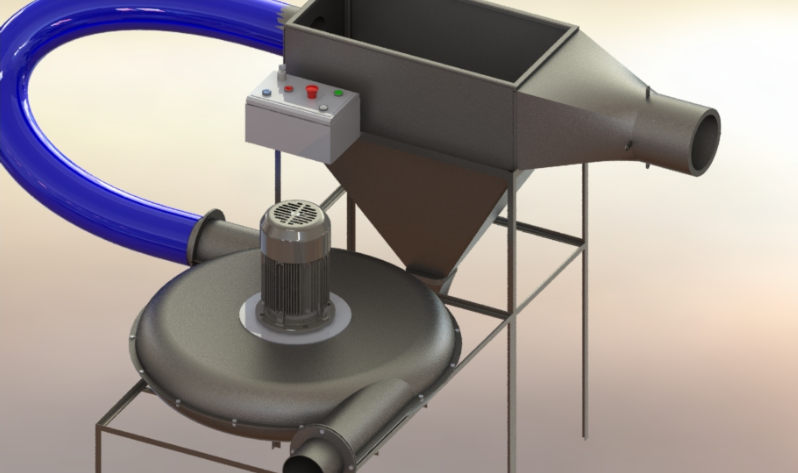
3D modeling design services are a terrific tool for product development regardless of the school of thought driving the concept. It allows for much quicker design changes than earlier technologies.
For example, if interference is found between two parts in the design, the size of one or both components can typically be changed in a matter of minutes. The parts can then be assembled in the model again with their new sizes.
A more basic example would be manipulating the 3D model and its parts to see where geometry can be altered to make the components less costly to manufacture without taking away from the unique benefits of the product.
Some common practices, such as design for manufacturing and assembly, can directly oppose design thinking if both are applied to the same design. That’s not to say that both can’t contribute to the design, but one needs to be the primary school of thought and the other can simply be a source of additional improvements.
Tips for Prototyping
Prototyping is a very broad subject all on its own. Without adequate effort during the prototyping process, full-scale production can be a mess and the final product may be poorly received. While prototyping can be a time consuming and costly process, when done correctly, it is well worth the investment.
Today, advances in both design and manufacturing technologies have created options that make the prototyping process faster, more efficient, and quite often more affordable. Rapid prototyping design engineering is at the helm.
Let’s say that you have an idea for a new product that will attach to any lawnmower and allows the user to trim the yard with incredible precision. Perhaps it even allows them to make custom patterns and it keeps them on track while mowing.
So, now you have your new product idea, and the device relies on a unique mechanism as opposed to electronic technology for guiding the user and the mower. At this point, you also decide to take advantage of all the modern tools that are available during the prototyping process.
With this approach, you begin by creating a 3D model yourself or having a professional 3D product modeling service make one for you. This 3D model is true to scale and even allows you to test the way that the parts will fit and move together.
To save time and money building the prototype, you find some companies offering 3D printing. After carefully reviewing their backgrounds and getting a few quotes, you send them a copy of your 3D model to print.
After a short wait, mostly depending on the 3D printer’s workload, your first physical prototype is ready. You take it home, attach it to your lawnmower, and decide on a unique pattern to cut. Your new product works!
However, connecting it to the lawnmower was a bit of a challenge and there are some exposed sharp edges that were overlooked in the initial design. You go back to the 3D model, change a few things, and now you’re ready to get the next iteration 3D printed for testing.
Tips for Testing and Adjusting
Testing and refining can be a little more involved in design thinking. The core concept demands focusing on the experience of the end-user. So, unlike some prototyping methods, testing by potential customers or a focus group should be prioritized.
While plenty of quality work and effort may have gone into the empathize, define, and ideate stages of the process, the real answers come during prototype engineering. Getting some prototypes into the hands of potential customers is going to yield highly valuable information very quickly.
The downside of human-focused methods is that sometimes the unique perspectives that are encouraged simply miss the mark when the idea is presented to the target audience. By presenting real users with physical prototypes, you’ll know what the market as a whole is likely to think of the product. For better or worse, this feedback is indispensable.
Now, realizing or being told that the design needs some changes is not a challenge or cause for concern. It’s merely an opportunity to make the final product even better. Great products often require several prototype iterations before reaching the final market-ready version of the design.
Working with a Freelancer
If you or your company are used to working on projects in-house from start to finish, then realizing that a project requires some outside talent tends to cause a bit of uncertainty. However, calling in a freelance engineering design service or designer is nothing to be afraid of if you need their skills. Successful businesses of all sizes work with freelance professionals every day. That being said, there are a few points to consider that will make the process as smooth as possible.
First of all, don’t expect to find top-tier skills for a bargain price. All costs considered, it is usually less costly to bring in a freelance designer or engineer as opposed to hiring one. If you decide to let cost be the number one factor when you’re seeking the help of a freelance professional, you aren’t going to like the end result.
If possible, compile a list of potential candidates for the project. Ideally, these are experienced professionals with a vetted track record who are both skilled and reliable.
Also, make sure that there are clear terms about the privacy of your project and the rights to the design. You want to be sure that the intellectual property rights will remain yours fully. It’s good practice to use non-disclosure agreements in situations like this as well.
As for actually working with your chosen freelance civil engineering service, be clear about your expectations. Inform them of any significant dates or milestones for the project, as well as how often you would like them to check in if you don’t plan to interact on a daily basis.
While it’s imperative to make your expectations clear, it’s equally critical to give the designer or engineer some creative flexibility so you can make the most of their background and experience. They’re likely to know more than you about specific points and subjects, so let that work for you rather than seeing it as a conflict.
Don’t forget the basics either. Give them the same degree of respect that you would give to any other professional in the field. Many freelance designers and engineers will eagerly reciprocate, and this will only help to move the project along smoothly.
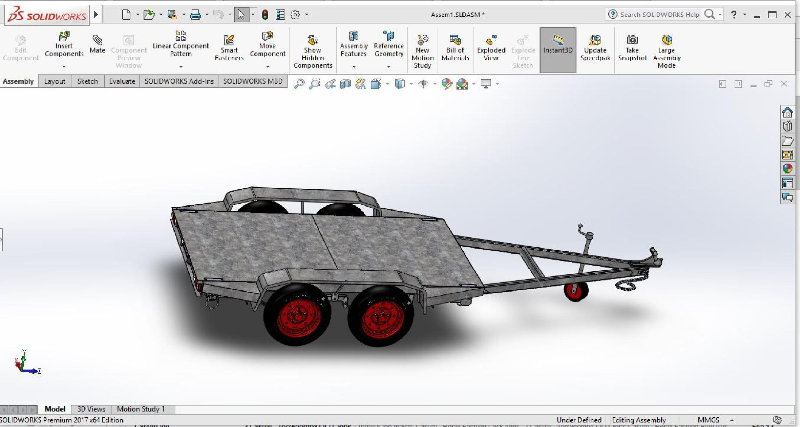
Manufacturing Your Product
When it’s time to choose a way to manufacture your new product, there’s no shortage of choices there either. Each method offers its own advantages and disadvantages.
Among the more traditional methods, we have options like CNC machining and injection molding. CNC machining can be used for both small and large scale production, but the cost can make it unappealing in some scenarios.
CNC machining really shines when precision is a top priority. Holding tolerances of +/-.005” is a snap with this method. In fact, you can even hold tolerances of +/-.001” this way, although this tends to increase the cost.
Injection molding is better suited for large scale production. That’s because this method comes with a higher initial investment. However, with enough production volume it doesn’t take long to recover the initial investment in molds.
If more traditional methods don’t appeal to you or offer a good fit for your project, then 3D printing may be something to consider. 3D printing isn’t often thought of as a viable method of full-scale production, but this technology is advancing rapidly and it is an appropriate production method in some scenarios.
Regardless of which manufacturing service you choose, there are some common factors that you will need to consider. First of all, it’s imperative to get multiple quotes. Shop rates vary, sometimes by wide margins, and this is true whether you’re dealing with machine shops, mold shops, or other service providers.
If your project has special considerations, then you should look for a company that has a relevant specialty. Some examples include tiny tolerances, specific machining methods, and unique materials.
Aside from getting multiple quotes and looking for a specialized provider, you should also look into the background and reputation of companies you are considering. Be sure to familiarize yourself with their payment terms as well. You don’t want production to be held up because you thought they expected a payment in 90 days, but they actually expected it in 30 days.
Presenting and Selling Your New Product
If you’ve opted for the design thinking approach and utilized 3D modeling during development, then you’re already ahead when it’s time to start creating marketing materials.
3D models can easily be used to make a wide range of marketing materials. They can be used as a base for high-quality 3D renderings, 3D animations, and more. Materials like these are excellent for e-commerce and online advertising. Some animations and renderings even allow the user to interact with them. In some situations, this allows the potential customer to get an even better look at the product than if they were examining it in person.
Don’t forget classic print collateral though. Inserts can be included in the packaging of your product to promote your other products if you have them.
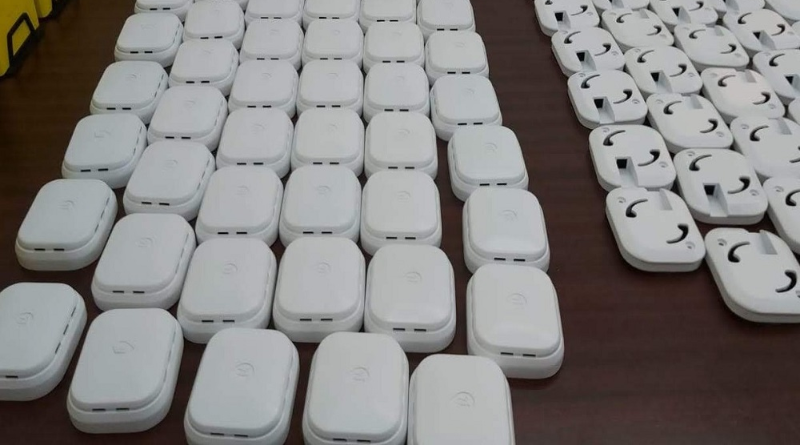
Things to Look Out For
Overall, design thinking is a solid and generally efficient approach to developing new products. However, there are two main problems that are commonly encountered when utilizing this approach.
Neither of these problems is unique to design thinking. The first is something that can be encountered with any type of iterative design. Of course, this problem is chasing perfection.
RELATED: 6 Ways to Use 3D Printing Services to Create a New Prototype Design
While the goal is to create the best product possible, you have to be ready to make a call about when good enough really is good enough. Otherwise, you can end up going through endless iterations and design changes without a final production-ready design in sight because of unrealistic standards.
Don’t sell yourself short. If others are telling you that the design or product is already great, they’re probably right.
The other problem that is frequently encountered with design thinking sometimes isn’t visible until you start looking into production costs. It’s easy to lose sight of good design practices while creating something that embodies a new ideal. However, this can easily be avoided by working with a designer or engineer who is familiar with both design thinking and design for manufacturing.
Summary
Design thinking is an excellent approach for new product development, especially when creating something for the consumer market. Like other methods, it does have some weaknesses, but these can be avoided by working with a professional who has the right kind of experience.
If your project involves creating a new product for the consumer market, then design thinking may be an ideal approach. This approach can be utilized by yourself, but getting help from an experienced freelance designer or engineer is an option as well.
If you’re considering the help of a freelance engineer, you can easily get a quote at your convenience. Contact Cad Crowd today to get a free quote for your project.