Finite Element Analysis (FEA) services offer a platform of virtual simulations used for analyzing the effects of predictable forces on a design. The mathematical-based analysis visualizes when or how a design can fail, materials will deform, assemblies might disintegrate, and a structure can collapse. FEA is ideally implemented during the design phase of a fabricated product to discover rooms for improvement and modify it as necessary. While different industries resort to FEA for various specific purposes, they share the same goals of finding the perfect combination of performance, build quality, and cost.
Table of contents
Consumer goods
Product design companies and engineers in the consumer goods industry utilize FEA to predict components’ future performance and structural behavior before developing physical prototypes. Consumer goods might be built from various materials, such as aluminum, cast iron, steel, metal alloy, thermoplastics, fabrics, and leather, to name a few. FEA works for all materials as long as the user understands their physical properties and characteristics.
RELATED: Sustainable product design and product development principles for firms to consider
Many consumer products can be subjected to FEA simulation. For example, electronics need thorough analysis to determine waterproofing and thermal qualities; furniture pieces require repeated tests to see the load-bearing capacity; shoes and wearable items must meet ergonomic requirements; and children’s toys must be checked for durability and shock-resistance properties. Regardless of the products, FEA can determine whether their designs can withstand physical damage under regular use.
The design for additive manufacturing firms can make well-informed changes if the analysis demonstrates product failures under non-extraordinary loads. Virtual modeling and analysis processes help companies reduce production costs, shorten design cycles, and boost productivity while improving ROI. An FEA simulation of consumer goods is often inseparable from life sciences, especially if the products involve direct human engagement during usage. The simulation might include comfort, stress distribution, support, and fatigue models.
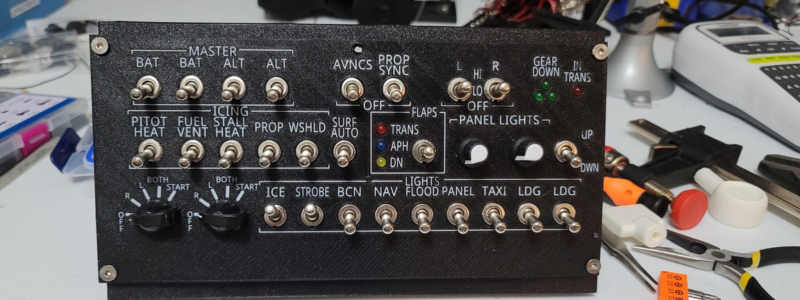
Example case: Foam Bed Optimization
A simulation of a foam bed in an FEA interface helps visualize how the product affects sleep quality. There are at least three variables to consider, including the user’s body measurement, foam material, and foam density. Detailed structural analysis is required to define the ideal thickness and firmness without diminishing comfort. The foam must support the body well enough but remain reasonably soft for a restful sleep. Because the body exerts pressure on the foam, the material must return to its original shape. Based on the design requirements, the manufacturer makes the necessary adjustments per FEA results.
RELATED: Product design guide for freelancers developing an invention
Athletic training
Based on the same user-product interaction principle, design engineering services use advanced FEA software can also simulate the human body to see the effects of specific training programs on muscles and bones. The analysis might also include simulations to measure the effects of repetitive movements—under certain conditions—on soft tissues and joints.
Example case: Elliptical Trainer Linkages Design
One of the main points of an elliptical trainer is to provide the same exercise routines as walking, running, and stair-climbing without the typical excessive pressure on the joints. That said, not every cross-trainer is created equal. Optimization in machine exercise should be based on how it impacts the human body during usage. Suppose a cross trainer is designed for people with knee injuries to stay fit. Unlike most machine exercises, the purpose-built training equipment must accommodate users’ disadvantages.
For instance, the engineering design services company may design better fluidity and lightweight rotational movement on the machine’s linkage. FEA helps determine the exact extent of pressure and force required to utilize the equipment properly without causing further harm to users.A similar method is possibly applied to applications like physiotherapy. FEA-based human body simulations might greatly assist doctors and physical trainers in planning an effective exercise routine to treat patients still recovering from injuries.
RELATED: How to hire a product design engineer: top 3 considerations for your business
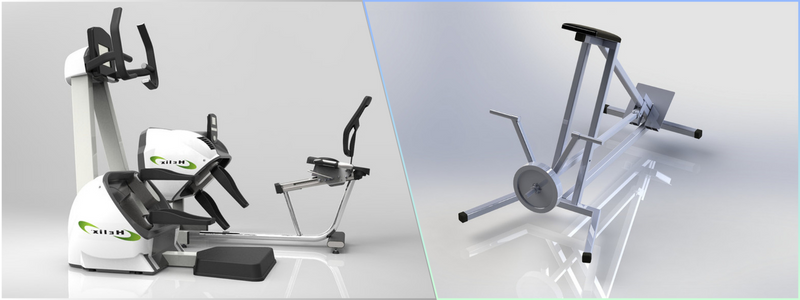
Medical research
Although the design process of training equipment might be listed under the medical research category, they are intended for devices or products outside the human body. On the other hand, the following applications highlight the practicality and usefulness of FEA for designing models meant to replicate actual organs.
Example case: Knee Biomechanics
Direct interoperability with CAD software used by medical device design & development services allows FEA tools to analyze objects of any source, including models generated from a CT scanning process. A three-dimensional reconstruction of a CT-scanned image makes for a comprehensive reference to study the prosthesis design. For example, a reconstructed scanned model of an injured knee clearly visualizes the organ’s musculoskeletal biomechanics.
Surgeons can use FEA simulation to determine the correct motion range of the femoral component. If TKA (Total Knee Arthroplasty) surgery is deemed necessary following the simulation, the prosthesis can be designed for individual patients based on their activity level, weight, age, and general health.
RELATED: Medical device design: a guide to service pricing, costs, and rates for companies
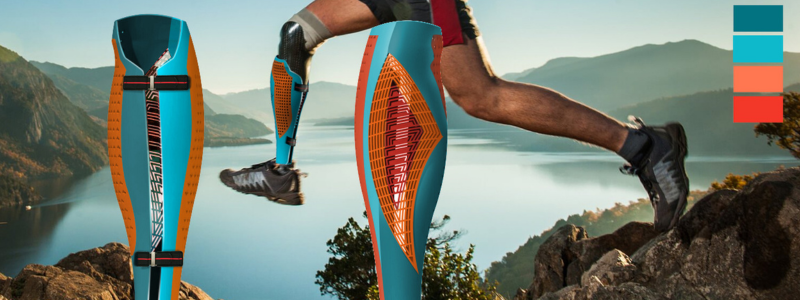
Example case: Dental Implants
In dentistry applications, FEA provides an in-depth look into dental implants’ surface structure and geometry. The simulation helps companies understand the material properties of an implant and how living bone tissues will respond to the applied mechanical force. Detailed geometrical analysis can predict adhesive strength and determine the optimum tightening torque to improve the success rate.
Example case: The Living Heart Project
In collaboration with the FDA, Dassault Systèmes and a massive group of leading cardiovascular researchers are on a shared mission to develop a simulated 3D heart model. The project is at the cutting edge of medical research, with a massive potential to deliver a groundbreaking study in developing new cardiovascular treatments and devices. A highly accurate simulation of a living heart aims to reduce the number of risky real-world clinical trials when designing a cardiovascular device while still ensuring efficacy and safety.
RELATED: Product simulation and analysis: why it’s worthwhile
External medical devices
External medical devices’ design and manufacturing processes also benefit significantly from FEA. Such devices are much less sophisticated than implants or pacemakers but equally applicable to improve patients’ comfort during treatments and recoveries. Among the common examples include:
Wheelchairs
As simple as a wheelchair may seem, the equipment should be an over engineered design piece. The engineering design expert must keep in mind that it needs to be durable and comfortable, but also practical and easily maneuverable. Throughout its helpful lifetime, a hospital wheelchair is quite possibly used by hundreds of people with varying weights, heights, and health conditions. An FEA analysis of the material and mechanism will lead to a versatile and heavy-duty design.
RELATED: Exploring medical prototype design factors for companies: costs, rates, and pricing
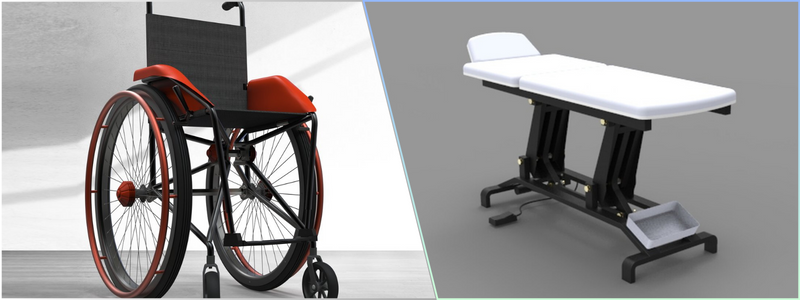
Transfusion machines
FEA simulation of blood flow through a pipe assembly is used as the basis for the design of platelet separators or transfusion machines of all sorts. In a typical simulated analysis, engineers perform an A/B study to examine the mechanism of two pipe assemblies and determine the most effective configurations to prevent blood clots, undesired flow rates, and turbulence. In addition to structural analysis, the simulation involves the computation of fluid dynamics.
EMS cots
The primary design considerations for an emergency service cot are load-carrying capability and lightweight components. While materials like carbon fiber and titanium are known to have the two characteristics, they are still too expensive for most emergency services. A cot is not designed by finite element analysis experts to be carried or lifted but is intended to help transport patients from one point to another; apart from material considerations, the locking mechanism should also be easily deployed and released. FEA simulation is expected to lead to the development of a reliable, affordable solution.
RELATED: Product testing and validation: the role of CAD simulation services for companies
In each case, virtual prototyping and simulated performance/usability tests open the doors for medical device manufacturers to design products that improve patients’ comfort and health. Thanks to CAD and FEA, minimum development costs may translate to affordable yet quality devices in the future.
Automotive industry
Automotive design & engineering services design a modern car to be equipped with numerous advanced electronics and moving components. It is also made of many materials constantly exerting forces on each other. Since every assembly requires a thorough assessment for reliability, performance, and quality in a cost-efficient fashion, FEA finds it one of the most significant applications in the automotive industry.
Solid and rigid materials deliver a durable design, whereas lightweight assembly can improve speed and performance. At the same time, the higher-performance engine often generates noise and vibration that might compromise comfort. Modern combustion engines rely heavily on liquid coolant and air to keep the temperatures within a safe range and maintain ideal working conditions. Nearly everything about FEA, from structural and thermal analysis to buckling and computational fluid dynamics, is fundamental in the development of a car design.
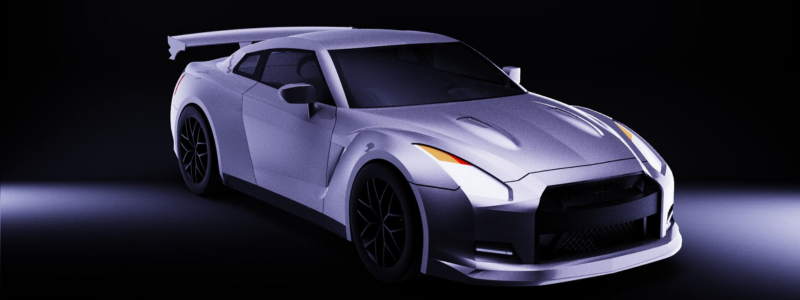
RELATED: Automotive design & engineering services, costs, rates pricing for companies
FEA also plays a vital role in determining a vehicle’s crashworthiness. A simulation of a crash—or impacts from multiple directions—can help engineers build a dependable safety system, including harnesses and airbags, to minimize the risk of injuries to occupants in the event of accidents.
Civil and architectural industries
Commercial & residential architects and engineers utilize 3D CAD modeling and FEA analysis to create building plans. In addition to ensuring a safe construction process, the simulation tells the architects and engineers whether the finished project can withstand various environmental conditions and topographical issues in the future. Detailed analysis can predict deterioration and the extent of damages to a building’s components under given conditions; based on the information, the building owner or management should be able to set a maintenance schedule to prevent expensive repairs.
RELATED: Civil engineering services rates, budget breakdown & costs for companies
How Cad Crowd can assist
Discover the intricacies and potential of Finite Element Analysis (FEA) as it redefines project management and outcomes in the industry. Delve deep into the transformative capabilities of FEA, reshaping how companies tackle complex projects and ensuring optimal results. Equip yourself for the future now and gain an edge over your competitors. Contact us for a free quote, and let Cad Crowd assist you in mastering FEA for your industry ventures.