You’ve all heard about virtual prototyping services, where you use 3D CAD and simulation software to create a photorealistic visualization of a design or a product and see how it performs on screen. The simulations may include finite element analysis, structural mechanics, stress tests, and so on. Virtual prototyping is great and all, but it still lacks one important aspect of full design development: tangibility. As much as the software demonstrates how a product is supposed to look and work, there’s no way can touch and feel the product just by looking at it on the screen. As part of a design evaluation, you want to experience the ergonomics, touch the textures on the surface, feel the weight, press the buttons, etc. And that’s where physical prototypes come in.
Think of a physical prototype as an early pre-production version of a product. Assuming the design is entirely brand-new, you have to fabricate it from scratch with CNC machines, injection molding, 3D printing, or any other manufacturing method, depending on the design and materials used. As for the cost, the manufacturing may set you back from a few hundred dollars for a simple proof-of-concept made of paper or cardboard to north of $50,000 for a beta version electronic device. Here’s a general guidance on the estimated cost of prototypes in 2024 & 2025 based on materials, complexity, and estimated completion time.
🚀 Table of contents
General pricing
Prototype materials | Complexity | Estimated timeline | Price range |
Paper or cardboard | Low | 1 – 2 weeks | $200-$2,000 |
3D printed (plastic filament) | Low to Moderate | 1 – 4 weeks | $100-$5,000 |
Fabric | Low to Moderate | 2 – 4 weeks | $500-$5,000 |
Silicone rubber or plastic molded | Moderate | 2 – 6 weeks | $2,000-$15,000 |
Sheet metal | Moderate | 2 – 6 weeks | $2,000-$15,000 |
Machined metal | Moderate | 2 – 6 weeks | $2,000-$25,000 |
Mobile app prototype | Low to High | 2 – 6 weeks | $2,000-$30,000 |
Mechanical | Moderate | 4 – 8 weeks | $3,000-$30,000 |
Electronics (with a custom PCB) | High | 4 – 12 weeks | $10,000-$50,000 |
Actual numbers may vary, as they’re also affected by the experience levels, reputations, and locations of the prototype makers themselves.

RELATED: Designing prototypes: 3D design services for inventors and companies
Engineering and fabrication
The pricing of a prototype can be broken down into two major portions: the engineering fee to design the product in the first place, and the actual fabrication cost to make it. For most products, you’ll need at least a mechanical engineer and a designer to build the design. If the product uses custom PCB, make sure you have an expert electronics engineer in the team as well.
Engineering costs
In the United States, most engineers get paid on an hourly basis, especially if they’re working on relatively large projects, such as building a new product prototype. The glaring problem is that you can’t possibly determine – with good accuracy – how many hours it will take to get the project done, so it should serve you well to prepare a bigger budget than any sum you may expect.
According to the U.S. BLS, the hourly rates for the professionals you need are as follows:
Occupations | Estimated hourly rate |
Mechanical engineers | $31.04 – $75.71 |
Industrial designers | $22.37 – $60.58 |
Electrical engineers | $36.88 – $86.39 |
Note: the BLS data is based on a survey sample used for the May 2023 update, but it’s the latest available from the site.
There’s a big variance in the hourly pay, but like with all professional services, the engineers’ rates also vary depending on their educational backgrounds, location, track records (success rates with previous projects), areas of specialty, and experience. In general, you can expect an experienced engineering service to work twice as fast and produce a better quality result than the inexperienced one. Therefore, the higher pay rate might be balanced-out by the work efficiency and time-saving benefits. But the opposite is also true; hiring junior engineers saves money in the short run, but the project might end up costing you higher labor cost due to revisions and more work hours.
The engineering cost will likely dominate the entire project. Apart from the engineers’ credentials, another major factor that affects the cost is product design complexity. Mind that even a seemingly simple design decision, like changing the position of a button or the amount of metal parts in a product, can either increase or decrease the engineering cost a great deal. Some changes can make the design simpler, while others may unnecessarily complicate things.
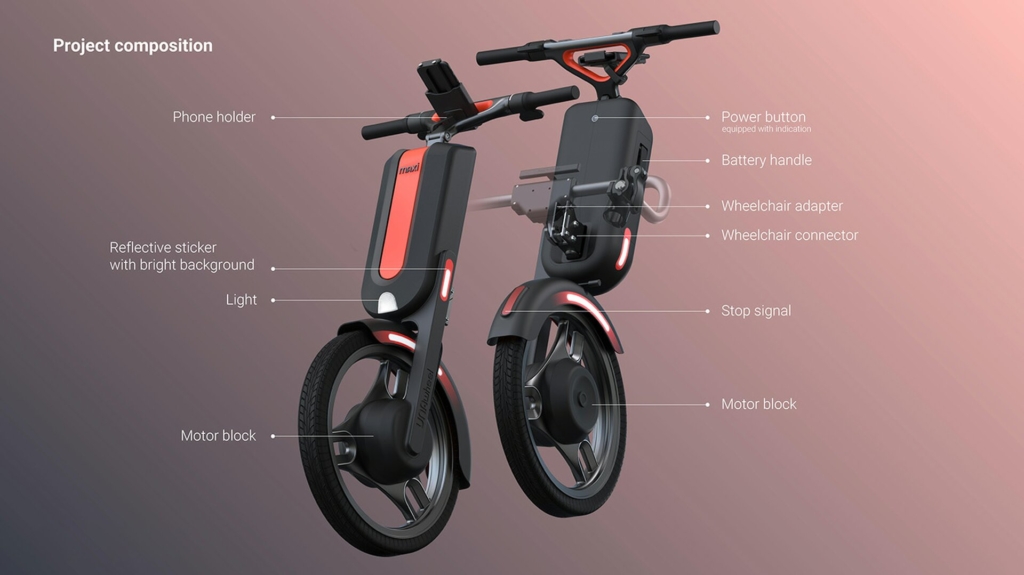
RELATED: What are the main prototypes used by companies in industrial design prototyping?
Fabrication cost
With the exception of electronic devices with custom PCBs, the fabrication process of most product prototypes is pretty straightforward. For instance, a moderately sized pencil holder might be easier to prototype than a small mechanical toy with a lot of moving parts in it. Depending on the materials used, you can use either 3D printing (mostly for plastics) or CNC machines (for metals/wood). Unless the product is complex enough that it needs to be assembled from multiple tiny metal parts, 3D printing is probably the best way to go. It’s quick, accurate, and getting even more affordable these days.
Complex electronics
An electronic product is quite tricky. It needs a custom PCB, firmware development, enclosures, and in some cases, connectivity features like IR for remote-controlled operation and Bluetooth technology. The prototype cost is affected not only by the enclosure fabrication process, but also the PCB design and firmware programming. The cost ranges from $10,000 to $50,000, and that’s for simple devices, such as flashlights, electric kettles, alarm clocks, calculators, and so on. On the high-end of the range, where you find products like digital cameras and audiophile headphones, the prototyping cost may reach hundreds of thousands of dollars for electronic product companies. Not only are those products equipped with complex electronics, but they’re likely made of high-quality materials as well.
3D printed prototypes
It’s quite difficult to pinpoint the exact cost of 3D printing, and that’s why you see a massive gap in pricing between $100 and $5,000. The actual cost is affected by quite a lot of factors, including but not limited to types of filaments, size, details, colors, and completion time. If the prototype is around 20 cm across and made of plastic-based filaments, such as ABS or PLA, the cost is probably $50 or less; as the size and level of detail increase, the cost gets higher accordingly. A large object with a lot of different textures on the surface and intricate details may set you back thousands of dollars, including the post-processing (cleaning and polishing).
Machined metal
You want the prototype fabricated with CNC machining if it has metal parts or perhaps made entirely of metal. The average cost for 3-axis CNC machining is around $80 per hour, including labor, whereas 5-axis CNC machining costs about $200 per hour. Keep in mind that you still have to pay for the material, too. The prices for some of the most common metal materials are as follows:
- Stainless Steel 304: $90
- Aluminum 7075: $80
- Aluminum 6061: $25
Note: all prices are for standard sheet sizes (15.24 x 15.24 x 2.54 cm). You can also have the materials cut to specific dimensions. When the product is supposed to have plastic and metal materials, the most practical way to build the prototype is to use both 3D printing and CNC machining.
Budgeting for iterations
Here’s another thing you should remember: the cost mentioned above is only for a single prototype. Regardless of the product, chances are you need to make at least three physical prototypes; the alpha, beta, and pre-production version – each with either minor or major changes from the previous design.
Prototyping affects the cost of product development services a great deal, which means you cannot put enough emphasis on the importance of budgeting. Make sure each iteration serves a good purpose and is made only after rigorous design review to avoid overspending. Let’s say the first physical prototype is a simple proof-of-concept; following a design evaluation by the engineering team (and maybe a small number of potential users), refine the design as best as you can before rushing to the next prototype. Only proceed to fabricate the second (beta) iteration when you’re confident that all issues have been identified and properly addressed.
The beta prototype needs to have all the features and functionalities of the final version. It’s not yet production-ready, because you have to run it once again with the factory partner/manufacturer to prepare for the mass-production process. The final iteration is the pre-production version, ready for manufacturing.
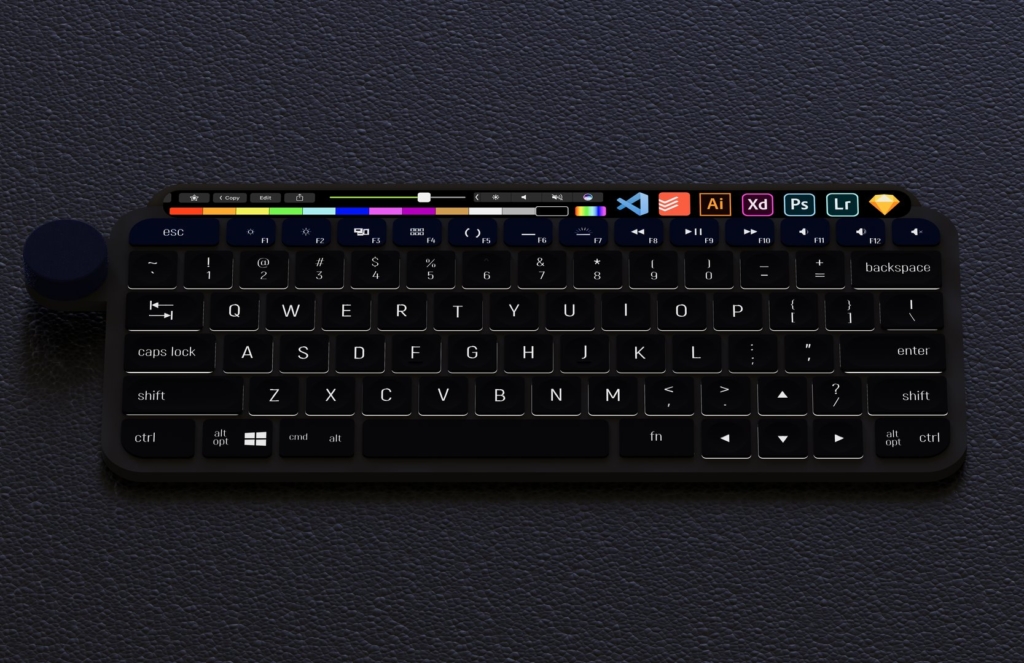
Once again on virtual prototype
Most mechanical engineers and industrial design firms work using 3D CAD and simulation software. They can build an entire design from scratch on a computer screen and implement various modifications without costing you a dime. With advanced software, every product can be modeled in 3D with accurate dimensions and material properties. In essence, there’s already a prototype, albeit virtual, sitting on the screen for them to experiment with. They can try different materials or geometries and run an analysis to see how well the design is. CAD software helps you save money from having to build physical prototypes too many times throughout the development process.
How Cad Crowd can help
With the help of professional engineers, designers, and 3D modelers from Cad Crowd, you can make sure that every physical prototype you build serves its intended purpose and is indeed effective to propel the product development process. Cad Crowd has also worked together with hundreds of custom fabricators and prototype makers all across the country to help you build quality and accurate prototypes regardless of the product type.