Patrick Hanratty was credited as the father of CAD/CAM and wrote and deployed computer software known as “Pronto” in 1957 while working at the General Motors Research Laboratories. About 70% of the current CAD/CAM systems are directly related to his original code. In 1962, Ivan Sutherland invented the “Sketchpad” as part of his Ph.D. thesis at the Massachusetts Institute of Technology. Sketchpad is often regarded as the first CAD software, thanks to its interactive interface.
It was a groundbreaking technology back then and is still developing and affecting many industries today. The technology was expensive then; most users were designers and engineers working at big companies. As personal computers became affordable, CAD drafting services gradually became popular among professionals and home users. By 2007, Autodesk had sold about eight million copies, establishing its position as an industry leader.
RELATED: Top 101 engineering and mechanical design firms in the United States
1995 was a proving ground for the prevalence of CAD in the transportation industry, specifically commercial airliners. It marked the launch of the Boeing 777, the first passenger aircraft designed entirely by computer. By then, Boeing had already been incorporating CAD into their design practices but had never fully computerized its aircraft development process; all that changed with the Triple Seven. CAD allowed the aerospace engineers at Boeing to do more complex calculations quicker and more accurately than ever before.
Automated systems also opened the possibility of merging design and aerospace engineering services into a single process, resulting in more significant cost-saving benefits and time efficiency. The technology has fundamentally transformed the aircraft development process thanks to digital modeling and simulation. During the early design phase, computer modeling of multiple potential designs enabled aerospace engineers to conduct a quick yet thorough examination of various configurations.
RELATED: 3D Modeling software or CAD programs: what should my designer use?
Part of the examination scrutinizes the aerodynamic properties of the aircraft, reducing the need for expensive wind tunnel testing to a significant degree. It does not entirely replace an actual wind tunnel, but at least the aerospace engineers knew what to expect before testing the flight vehicle.
Table of Contents
Production
Boeing 777 also marked a departure from a conventional industry practice where a company developed a passenger aircraft without external input from customers. The in-house development and aerospace engineering team controlled nearly every aspect of the vehicle, including the shape and features. Things were different with the 777. For the first time, eight major airlines, including United Airlines, Delta, American Airlines, British Airways, Qantas, Cathay Pacific, Japan Airlines, and All Nippon Airways, took part in the development process. Such a global subcontracting venture was, at the time, unprecedented.
RELATED: How 3D CAD & CAM have changed new product design
Technology companies other than airlines also had significant roles in production. For example, Mitsubishi Heavy Industries and Kawasaki Heavy Industries built the fuselage panels, whereas Subaru Corporation (formerly Fuji Heavy Industries) made the center wing section. The rudder was contracted to the Government Aircraft Factories (formerly Aerospace Technologies of Australia), and the elevators were developed by Hawker de Havilland (before it became a subsidiary of Boeing).
It was the same thing with the propulsion systems. General Electric, Rolls-Royce, and Pratt & Whitney developed the engine options. The first engine to be fitted was the PW4084. Assembly began in January 1993. Due to the size of the aircraft, Boeing expanded its Everett Factory in Washington to double its original dimension at around $1.5 billion, including adding new assembly lines. Boeing also fitted a turning machine that could rotate the fuselage to 180 degrees, giving easy access to workers.
RELATED: How much do mechanical engineer services typically charge for rates & firms?
Maiden flight
After more than four years of development, the final prototype of the Boeing 777 came out of the assembly facility in April 1994. The airliner took its maiden flight in June, and its first commercial flight was with United Airlines in June 1995 from Heathrow to Dulles. Multiple variations of the aircraft came along over the years. Yet, the original is still in service today as a testament to the power and value of CAD in the aerospace industry. The latest version, the Boeing 777X, is currently the world’s largest twin-engine jet.
How the aerospace industry is using CAD design services
CAD indeed plays a significant role, but real-world testing (as opposed to simulation) remains indispensable for evaluations by a test pilot. Aerodynamics, passenger capacity, power, and fuel efficiency can be tested on simulation with accurate results using finite element analysis services, but the onboard system and maneuverability are for the test pilot to evaluate.
RELATED: Product simulation and analysis: why it’s worthwhile
Once again, Boeing 777 set the precedent of using CAD design to develop commercial aircraft. The generic steps of development remain the same across the aerospace industry. In almost all scenarios, aerospace engineering builds several preliminary digital designs. Following a refinement and selection phase, they focus on the most technically feasible model to develop further.
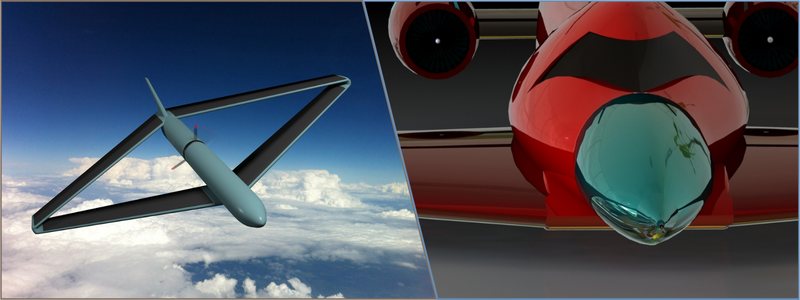
Drafting
The point of drafting is to create a virtual representation of what the aircraft will be. Aerospace engineers use CAD software to build a three-dimensional model based on vehicle data sets. The process eliminates the need for physical models or mock-ups. Aerospace engineers then improve and verify design layouts on the virtual model.
At this point of development, the model still needs more details, such as electric subsystems and engine schematics. The aerospace industry primarily uses CAD/CAM packages like CATIA from Dassault Systèmes, CADDS and Pro/Engineer from Parametric Technology Corporation, and NX from Siemens Digital Industries, among others. Boeing 777 was developed using the CATIA package.
RELATED: The evolution of 3D CAD design and drafting
Modeling
The real work begins with modeling an aircraft. Many 3D modeling design companies use parametric modeling to draw the vehicle’s parts and subsystems. It may sound simple in a small mechanical vehicle, but an aircraft presents enormous complexity. In the case of the Boeing 777, there are around three million individual parts and miles of wiring for the onboard computer system.
Parametric modeling doesn’t just draw the parts to resemble their physical shapes but gives them real-world behaviors. Apart from the parts’ dimensions, the data set includes weight, material characteristics, and tensile strength. Both surface and solid modeling techniques are utilized to give the parts their attributes. Since the model is the foundation on which an actual aircraft will be built, maintaining a near-obsessive level of accuracy is non-negotiable. Accuracy to the tiniest details ensures precise design modifications and improvements at every step.
RELATED: 3D modeling: an overview of history & industry applications
Accuracy means enhanced communication and efficient collaboration if the development and aerospace engineering teams comprise multiple companies working at different locations. The design cycle can be reduced, and the team can move forward to reach the next milestone confidently. The finished model is run through countless simulation procedures to evaluate performance, stability, and maneuverability. Aerospace engineers use different simulation parameters, such as load capacity and speed, depending on the type of analysis performed.
Prototyping
In the aerospace industry, a prototype almost always means a fully-working product. Developing an aircraft is costly, so building multiple test models makes little financial sense. Thanks to CAD, physical mock-ups and expensive prototypes are optional. However, some parts of an aircraft may require the assistance of a prototype design engineering expert.
RELATED: Find the best prototype engineering firm services
Additive manufacturing, much like CAD, has proven to be a significant player in the development of flight vehicles in the aerospace industry. The demand for additive manufacturing or 3D printing in the aerospace industry is projected to grow to $3 billion in 2022. The increasing demand for lightweight engine parts triggers a large portion of the growth. The aerospace industry is not merely about commercial aircraft or massive jet airliners but includes every aerial vehicle, such as smaller jets and drones. Smaller companies that develop and sell drones will find 3D printing cost-saving equipment in the prototyping phase. Theoretically, they could build a fully-working version of a UAV using only a 3D printer.
Like in other industries, a 3D printing design company is used to prototype intricate parts. Additive manufacturing can only create objects from plastic materials, so the prototype is not likely functional. That said, the printed object enables manufacturing companies to examine intricate details and dimensions accurately. 3D printed parts are mock-ups manufactured without using various specialized tooling.
CAD and additive manufacturing services are inseparable. While the former can stand independently as design software, the latter needs 3D models to print. CAD software creates the object for the 3D printer to manufacture. In the aerospace industry, the key areas where there is high demand for 3D printers include mounting brackets, fixtures and jigs, and surrogate parts. The need for a detailed prototype is rare, but it exists, mainly for commercially-sold drones because it usually is light and requires minimum heavy-duty materials.
RELATED: Different kinds of prototypes and how to use them for your design project
For an industry that operates within an immeasurable margin of error, accuracy – even in the prototyped parts – is of the utmost importance. However, the printed object is only as accurate as the CAD model. When the traditional prototyping process is no longer capable of keeping with the required speed of development, 3D printing is, at the moment, the most viable solution.
How Cad Crowd can assist
Cad Crowd Services provide rendering services and has been an expert for many years. We assist architects, contractors, construction companies, aerospace, manufacturing, technology users of 3D CAD, and other defense industries. Innovative companies worldwide rely on us for their models, 3D CAD Perfect works. We are Thankful to all the customers we have – no matter if someone is among the premier CAD organization or if you’re a consumer. Size does not matter, but your order is our prime concern at 3D CAD services. Every 3D order is important to us. Contact us for a free quote.