Injection molding is the process of injecting molten material such as plastic or metal into a mold to make an item. It’s often used for creating prototypes or for mass-manufacturing products. Products like bottle tops, containers, tools, coverings for electronic parts, and many other items are often injection molded.
It is a particularly useful method of production when a person or company wants to quickly make large quantities of products. The molds can quickly be produced, as they can be reused over and over to make a great quantity of virtually identical items. This is incredibly useful in many industries where the fast mass-production of identical items is key to business success.
Injection molding and casting services can be used for both simple and complex items and ensures lower labor costs since fewer employees are needed in the manufacturing process. Additionally, injection molding, when properly done, can be very environmentally friendly. The plastic used in the molds can be used efficiently so that there is very little waste, and any waste that is produced can be recycled by the injection molding company. This saves money and helps to save the environment.
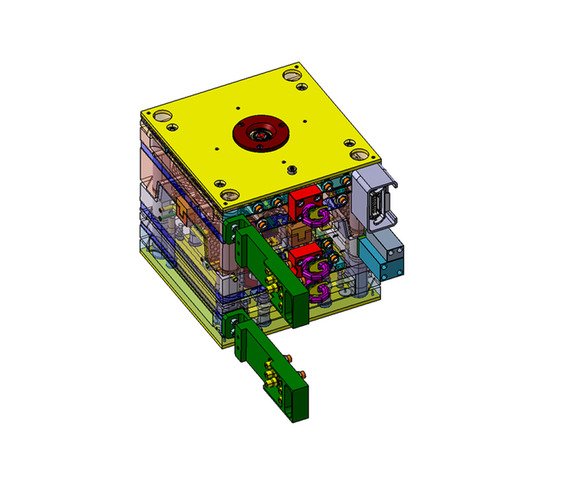
While this process has many benefits, it does take significant time and money to create a good mold. This means that a project must be planned well and that the freelance 3D CAD designer and engineer must collaborate on the project from day one to ensure that the project is being designed with injection molding friendly features from day one. If the planning stages of a project are done wrong, the benefits that injection molding offers will be lost.
A poorly planned injection molding project can quickly become an expensive nightmare if redesigning the mold is necessary, or it could just cost more because of unnecessary additional materials and added production time due to inefficient product design. To reap the benefits of creating injection molded items, a mold must be efficiently designed and the product must be carefully planned.
Six Tips for Planning an Injection Molding Project
When planning an injection molding project, there are several things to keep in mind as you work with your injection molding design service on your product’s design. One of the most important things is to consider the physical design of the product itself.
A poorly designed project, or just one that is not designed specifically with injection molding in mind, simply will not be a cost-effective project. RevPart’s Design Guidelines for Injection Molding gives great tips for how to design a project that can be injection molded, which I will reference in the following six tips.
Design and Test One or More Prototypes
A prototype is the first model of a project and is useful to help designers catch errors and fix problems before mass-producing a large number of items. Designing a prototype for your project is especially important in injection molding because it ensures that when the final mold is made for the project, it will work in the right ways. Molds are expensive and time-consuming to make so mistakes at this stage are costly.
RELATED: How to Save Money On Injection Molding: 10 Tips from an Engineering Design Firm
One or more prototypes should be made, tested, and changed as necessary to ensure product success. Once the design has been finalized, then the final molds for mass-producing the item can be designed. It costs money to make prototypes, but it’s cheaper to do this than to have to create multiple molds because of poor planning.
Prototypes can be 3D printed, made through CNC programming services, or made through prototype molding. They can also be made using CAD technology, which enables designers to send virtual prototypes to clients around the world. A downside is that there is no physical copy, but physical copies can be made from the design.
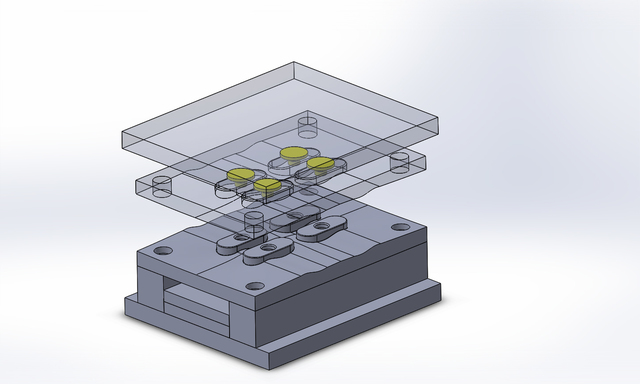
3D printing is the most cost-effective option to create a physical prototype, but a significant downside is that it’s not made using injection molding. Those working with injection molding usually do not use 3D printed prototypes for production, though they can give valuable information about how the product will work.
Two excellent options for injection molding prototyping are CNC machining and prototype molding. With CNC machining and prototype molding, actual molds are made of the project, which ensures that these prototypes realistically represent the items being planned. Prototypes are made using these molds, which helps catch design flaws and potentially costly mistakes.
CNC machining is a more basic, cost-effective option, while prototype molding costs more but can include more detailed features. Whichever a designer chooses, they must be certain that the prototype adequately represents their project to reduce the likelihood of having to throw away production molds that have flaws.
Plan for Wall Thickness
Wall thickness is important because it determines how much plastic you will ultimately use in a project. Generally, the thinner an engineer can make the walls the better because using less material cuts down on time. There is less material to inject into the mold, and since there is less material, the final product will take a shorter amount of time to cool. Additionally, the use of less material in each item adds up, which also reduces overall costs.
However, a designer must balance the cost versus the quality of the item to find the appropriate wall thickness for a project. If a wall must be thicker to ensure the structural strength of the item, this must be taken into consideration.
Changes in wall thickness are also important to consider and avoid when designing a project. In injection molding, it is generally inadvisable to change the thickness of the wall, as this can create warping or flaws in the material since the plastic will cool at different speeds due to the differences in thicknesses.
If it is necessary to change wall thickness. A designer should do this as gradually as possible to avoid sudden changes and also try to keep the changes in wall thickness as minimal as possible. This will help to avoid warping or dips in the final project.
Taper the Walls (Add Draft) to Streamline Production
Tapering walls of a project, or adding draft, is an important step in the design process. Adding draft is important because it allows the item to slip out of the mold easily. If a mold is not designed with an appropriate amount of draft, the item will not come out of the mold. This kind of mistake often means that the designer has to have a whole new mold created, which wastes time and money. Designing walls that have the right amount of angle is essential to creating an effective injection mold.
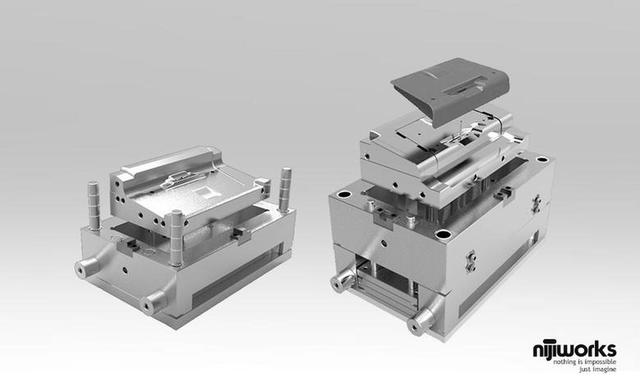
The amount of draft added needs to increase as the surface texture increases. Any ribs that reinforce the design also need to have draft added to them. Since adding draft requires calculations and can be difficult to do, it’s important to consult an expert who can help ensure that the design has the strength and the draft needed for the project.
A freelance prototype design engineering service can help calculate the amount of draft needed for your project to ensure it will easily be released from the mold. Getting the draft right the first time is important since adding to molds is practically impossible.
Know How to Avoid Difficult Mold Designs
Undercuts are portions of a design that prevent the product from pulling easily and cleanly out of the mold. When designing an item, it’s most efficient to eliminate undercuts from the design. Undercuts make it difficult for the item to be ejected from the mold, which increases production time.
Additionally, creating a mold that includes undercuts costs more as it is difficult to make. Where possible, a designer should eliminate undercuts and instead use other design techniques to create an item with the same functionality. This will cut down on costs by ensuring the mold is less expensive and will additionally lower the production time.
Creating molds of core cavities can also help lower production costs. For example, when designing molds for a structure like a box, a design for assembly service can, rather than machining a deep cavity into the metal to create the sides of the box, create a mold for the inside of the box and form a bigger part that goes around this to form the sides. Strategically planning molds and using molds for core cavities where possible cuts down the costs of creating the molds, which is a major expense in injection molding.
Properly Design Reinforcements and Fasteners
Reinforcements (ribs) and fasteners (bosses) that fasten one side of a project to the other are featured in many injection molded projects but must be designed appropriately to ensure that they easily come out of the molds and do not cause other issues.
Where reinforcement is necessary, a product design company should choose to use ribs rather than a solid piece of plastic to reinforce walls. A solid piece will not work well as it is of a significantly different thickness than the walls and could warp when it is cooling.
Walls are not the only things that need to have draft. Ribs must have draft in order to come out of the mold freely and should be thinner than the walls. Bosses must also have draft, and when designing bosses, a mechanical engineer service must take into consideration both the placement and size in relation to the thickness of the walls.
Plan the Surface Texture of a Project from Day One
An injection molded project will take on the texture of the mold. That means that if a specific texture is required on the project, it must be added to the mold. It can be added by hand or by chemical etching. Adding a texture means extra cost, but this can be worth it for the aesthetic appeal.
However, the texture of the finished project plays a part in the draft of the mold, so the texture desired in the final outcome must be planned for from the beginning stages of the project. Failing to plan for this means that the item may not come out of the mold well.
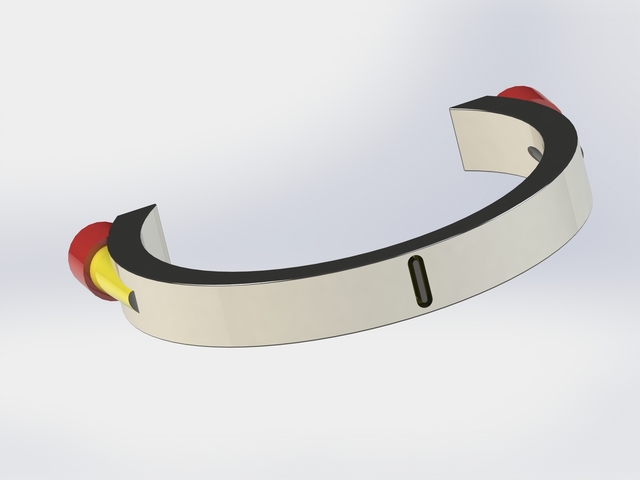
Any other embellishments, symbols, or text desired on the project should also be planned for from the beginning and should be at least 1.5mm high. Additionally, there should be a 0.5mm width between any text or features.
When planning to use text, a designer should use a simple sans-serif font with letters that are not significantly depressed into or embossed onto the item. Following these rules when designing additional features for the surface of an injection-molded item will ensure cost-efficiency when mass-manufacturing an item.
Other Tips for Reducing Costs When Planning Injection Molding Projects
Design is vital in reducing the costs of an injection molding project, but design alone is not the only factor to think about when creating a well-planned and cost-effective injection molded project. The following tips focus on other factors that influence the cost of a project and provide ideas on what can be changed or altered for the sake of producing a streamlined project with a lower cost of production.
Consider Design Material
In injection molding, a variety of kinds of metals and polymers or plastics can be used in projects. The different metals and polymers available share similarities but are also very different from one another and can be used differently within injection molding. Many materials available are blends or alloys. There is a vast amount of choices available and each choice is slightly different from the next, not only in physical properties but also in cost.
When choosing a material for a project, a designer needs to take into account what the product will be used for, the strength or flexibility that the project needs to have, and the cost to mass-produce items using this material. Some materials are much more expensive than others, and depending on the product, it may not matter if the highest quality material is used in the project.
For example, a concept design service might be designing something small and sturdy, such as a plastic figurine. In this case, the designer can save money by thinking carefully about what material they will use. Since it does not need to be flexible or excessively strong or made out of a plastic that is especially resistant to flame, oil, or harsh chemicals, the designer can help their client save money by choosing a lower-quality plastic such as polyethylene.
This is the same plastic many items such as grocery bags, cosmetics containers, and children’s toys are made of. Using this kind of plastic ensures that a designer will be saving money when mass producing a vast quantity of items rather than spending money on a more expensive plastic when it is unnecessary in this situation.
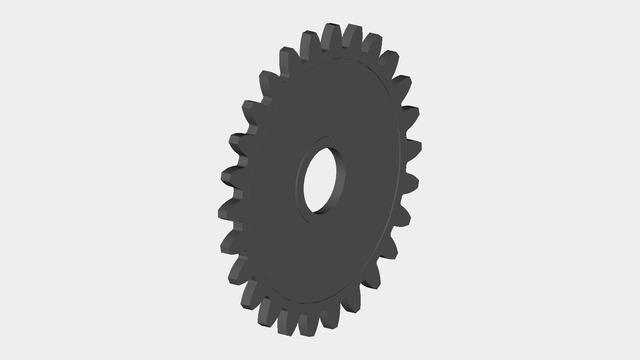
A designer should also take into account the color of the final project and whether they want a consistently exact color or if a generic color will do. For example, if a designer is creating a flower pot and would like the final product to be a specific color of blue, they can choose a pre-colored resin, which will guarantee color consistency across a wide range of batches.
However, when choosing a color for a plastic item, masterbatches, which are highly concentrated resins in liquid form that are added to the plastic being injection molded, are typically the most cost-effective. Though masterbatches cannot be used in rotational molding, they can be vital in decreasing the cost of production in other injection molded projects.
Consider Design Strength and Durability
Knowing exactly what kind of material is necessary for a project from day one can cut down on costs. When choosing the material for a project, keeping the needs for strength and/or flexibility at the forefront is important. If a design needs to be flexible, a rigid plastic will simply not work.
Similarly, if a design needs to firmly hold its shape, a flexible plastic would not work. Some projects may need to be rigid but still have the ability to flex under stress. Additionally, different plastics react differently when they are being injection molded. An injection molding and casting service must choose the kind of plastic they want used in the project early to avoid having to change the design later.
RELATED: How to Design Products for Injection Molding & Prototyping Firms
Different kinds of plastics also have different durability in terms of breakdown under UV light and strength when exposed to extreme weather, such as freezing or extremely hot temperatures. Some are flame resistant or resistant to harsh chemicals. The type of plastic used on a cooking utensil, where the material will come into contact with extreme heat, should be chosen to handle high temperatures while remaining safe to use around food.
The plastic used in a hospital environment where it may come into contact with harsh cleaning solutions several times a day should be designed to not break down even though it is exposed to chemicals. Carefully considering how the item will be used will keep a designer from choosing a more expensive plastic that unnecessarily goes above and beyond the needs of the project. At the same time, if the item needs to have specific qualities, a designer should choose the appropriate material.
Decide on Necessary Features
When attempting to cut costs on an injection molded design, a designer should consider the decorative details of the design and question if they are necessary. Injection molding can be used to create extremely complex designs with intricate details. However, fine details inevitably mean that the cost of a project will be higher since the time spent creating a mold with fine details will be greater.
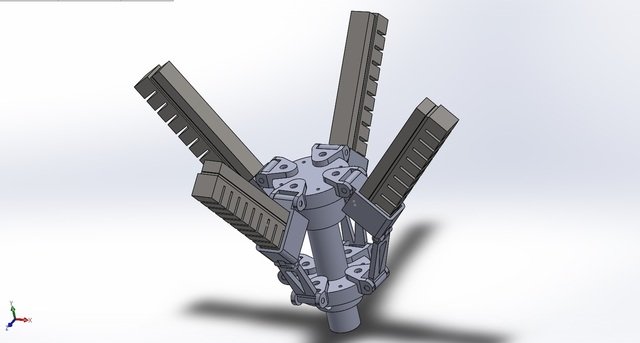
It is not always the best choice to include this kind of complexity when budgeting for a cost-effective project or the beginning stages of prototyping. A CAD designer should consider if finer details are necessary at all, and if so, if they are designed to be injection mold friendly or if they present a costly and unnecessary challenge for those creating the mold.
Work Toward Mold Efficiency
A competent designer needs to ensure that not only is a finished item ejected easily from a mold, but that the molds are efficient enough to mass-produce items. For example, if a designer wants 10,000 of a small object, it would be extremely inefficient to use the same mold for all 10,000 objects. Rather than creating one mold and using it 10,000 times, a designer can make a mold that produces many more of the item at one time.
Since both making a mold and production time are expensive, a competent designer can do the math to find the cheapest possible maximum mold size for the minimum production time, which will help more items be produced in less time. This will ensure that the needed number of items are created in the shortest amount of time possible with the lowest cost.
A competent CATIA design and engineering service can also design molds that have inner parts that have space within them for smaller molds. These are called multi-cavity molds and are useful in cases where one piece is small enough to fit inside a bigger piece. A family mold can be used when three or more pieces can fit inside of each other. If all the pieces are made of the same plastic and will take roughly the same amount of production time, creating a multi-cavity mold can help make the mass production of items more cost-effective.
For example, a lamp base may have injection-molded pieces that fit together over the electrical components. The space inside the mold for one of the sides of the lamp base can have another mold inside it for another component of the lamp, like the light’s switch box. If an even smaller piece of the lamp fits inside the light switch box, this space can be utilized as well.
Taking full advantage of the cavities inside the mold ensures that the molds are being used to their full potential, and also saves money since the CAD designer has avoided having to create another mold for each other component of the lamp.
A professional CAD designer can ensure that their clients have an efficient mold that will cut down on production time and the expenses associated with creating molds. Since molds are costly parts of mass-producing items using injection molding, it is well worth it to hire a qualified professional to design a mold that will work for your project.
Design Molds That Can Be Modified and Reused
Molds are expensive to make. They use high-quality materials that are time-consuming to machine into the right shape. One-way designers can reduce costs is by reusing prototype molds as they develop their projects. It is possible to remove metal from a mold, but it is almost impossible to build a mold back up. This means that the prototype can be altered, as long as these alterations only involve taking metal away from the mold or making the prototype bigger in some way.
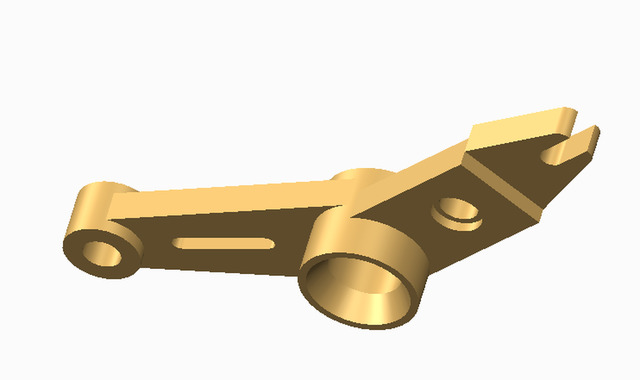
A designer can use this knowledge to their advantage by planning the simplest, smallest prototypes first, and then changing it as they continue to develop the project to be bigger or more complex. This works especially well on projects with pieces that might be made longer or changed to be larger as the project progresses.
A designer can plan to make molds this way in order to cut costs as they develop their design and test it out through the creation of new prototypes. An excellent designer can help a client to save money by planning to create prototypes that allow the mold to be reused.
Choose the Right Professionals for the Job
Designing injection molds and designing the product to be molded often requires the collaboration of two different people: the designer and the civil engineer. An engineer knows what kinds of design elements will work best with injection molding and knows the various problems that can come up when products are poorly designed.
Choosing to work with a reputable company that has both designers and engineers who know how injection molding works and how to design items with injection molding in mind will ensure that project costs are kept down. Cad Crowd has both skilled professional designers and engineers that can collaborate on injection molded projects to create the highest quality cost-effective outcome.
If you are looking for a designer or engineer for your injection molded project, Cad Crowd can help efficiently design and engineer your products. Get a free quote or to request more information about how our professional designers and engineers can help you to create the ideal product at the ideal price.