CAD creation has two primary approaches: direct modeling and parametric modeling. These are useful for various aspects and stages of the CAD design process, making creating your 3D CAD model more straightforward. This piece delves into parametric and direct modeling services and their applications in design and engineering.
Table of contents
- What is parametric modeling?
- What are the advantages of parametric modeling?
- What are the disadvantages of parametric modeling?
- What are the best applications of parametric modeling?
- What is direct modeling?
- What are the advantages of direct modeling?
- What are the disadvantages of direct modeling?
- What are the best applications of direct modeling?
- Parametric vs. direct modeling: which is better?
- Factors to consider to determine the proper modeling method for you
- How Cad Crowd can help
What is parametric modeling?
The parametric modeling method refers to the structured engineering process, often called history-based modeling. This method retains a log of all model features; every new feature added to the model is cataloged in the list. This is known as a feature tree, which makes editing more easily accessible. Every feature is developed by manually inputting dimensions to ensure careful control of every angle and measurement.
Parameters also control the elements, and the design engineering expert who makes the CAD model defines these parameters. It allows the parametric modeling expert to retain design intent while developing and tweaking the model since every modification will abide by the set parameters instructing the model’s behavior.
RELATED: How the aerospace industry is using CAD design services: drafting, modeling, and prototyping
What are the advantages of parametric modeling?
Changes are automated
Each change is reflected immediately in the visual model whenever a feature’s dimensions are modified. Simultaneous editing of identical features is also possible in parametric modeling.
Design intent
With the help of the parameters, the CAD model doesn’t have to stray from the original intent of the design. These algorithms tell the features how to react to the changes made in the rest of the model.
Feature tree
The feature tree is the list that records every feature. You can always access it, and it maintains a linear creation log complete with steps.
Structure
Dimensions control every feature to allow precise modifications and movements.
RELATED: The best 3D modeling CAD software for designers
What are the disadvantages of parametric modeling?
Careful planning is required
Every time the parametric model changes, the program will update the model by addressing every feature based on the feature tree’s linear order. The parts are then connected while building upon one another in the list. Any lapse or carelessness on the parametric modeling professional’s part will result in some changes made earlier in the feature tree to break the model while trying to address the features much further down the tree. This is also why changing the design in later stages is challenging.
Concept design
While brainstorming the available design options, making iterations to the model through parametric modeling can be tedious and stifle the creative process.
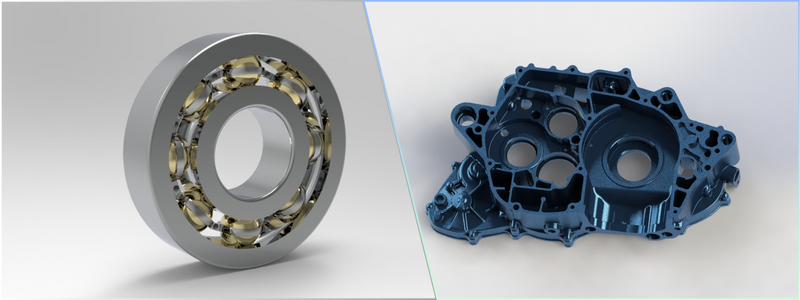
Size of the file
More features added means the longer the feature tree’s list goes. The computer may require additional power and time to resolve the model.
Sharing of parametric models
It’s not easy to share the parametric model in suite-specific CAD because of the numerous CAD programs available on the market. Converting the file to generic CAD makes it easier to share it among computers. However, doing this will wipe off the feature tree from the file, making it harder to make additional editing.
RELATED: The evolution of 3D CAD design and drafting
What are the best applications of parametric modeling?
Parametric modeling is highly recommended for tasks where it’s necessary to create or meet exact dimensions for the continuity of production. It is typically in the engineering phase after identifying the part’s concept design for production. It also comes in handy if there is a need for a comprehensive log of features, including 3D modeling services for machine parts that need frequent updates or a part of a family of products that should share several similarities.
What is direct modeling?
Freedom and flexibility are the main characteristics of the direct modeling method. These traits are all because direct modeling is a process free from history. It means that it doesn’t maintain any log of edits or features in the same way that parametric modeling does. Direct modeling doesn’t define parameters, so features aren’t tied together.
Instead, it’s possible to directly pull, push, or otherwise manipulate any particular geometrical piece of the model into the designer’s preferred spot. You can liken this model to how sculptors work with modeling clay. The intent of the CAD design is defined throughout the model’s progress.
RELATED: 3D modeling: an overview of history & industry applications
What are the advantages of direct modeling?
Freedom and flexibility
Due to the lack of connection of features among each other, it’s possible to make changes with no need to worry that the model will break. It also allows making radical changes at any stage of the process.
Speed
The process can speed up since it’s possible to make direct edits instead of inputting the individual dimensions. It allows the 3D design firm to rapidly and easily explore different design variations.
Versatility
Since this modeling process doesn’t keep a feature tree, it allows direct working with the generic CAD models in the form of IGES or STEP files.
What are the disadvantages of direct modeling?
Design intent
Since parameters are not used for defining the design intent and making the model react due to the changes, there is always the risk of straying from the design intent.
RELATED: 3D modeling vs. 3D rendering services
Dimensions
Even though dimensions might be shown every time the geometry is manipulated in a direct model, these dimensions don’t have a history. It makes editing and tracking them more challenging if you need exact measurements rather than concepts.
Identical features
It’s possible to modify identical features like holes with parametric modeling simultaneously. However, direct modeling doesn’t draw relationships between the items. It means that if there are exact features similar to this, individually editing them is necessary.
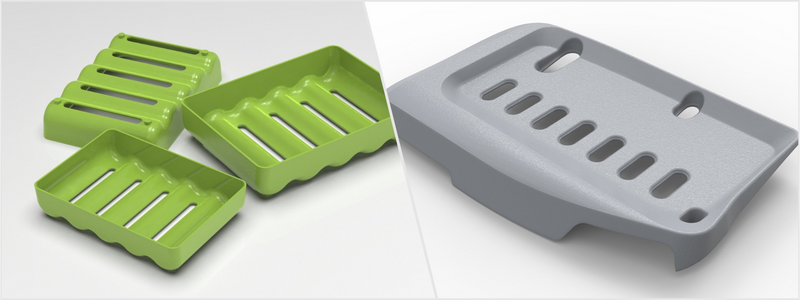
What are the best applications of direct modeling?
Direct modeling is an approach best recommended for tasks where there is a need for speed and flexibility, such as with rapid prototyping and concept design. It also helps if creating a part that is a one-off design will have a short life cycle or if it is expected to undergo numerous design iterations. Speed is also more beneficial than parameter control in most of these instances and, in turn, will save resources spent on the model’s production.
RELATED: 3D modeling & CAD design recap
Parametric vs. direct modeling: which is better?
The specific modeling that will suit you best depends on the current phase and the intended purpose of your model. However, a good combination of both is recommended since each will help you in the different stages of the modeling process.
The two 3D modeling service types can lead to a similar CAD result, making the exchange between direct and parametric modeling programs. However, the feature tree from parametric modeling will get lost in the data exchange. It’s important to remember that direct modeling and parametric modeling often exist in different programs. Although several modeling programs have started incorporating tools from the two approaches, both are still in their early stages and must provide all the perks of either method.
RELATED: Do you know the three major types of 3D models?
Factors to consider to determine the proper modeling method for you
If you’re a 3D design professional wondering about the modeling method that suits you, there are several vital factors you need to consider.
- Specific needs for collaboration
Do you have a team where every 3D modeler expert uses their preferred software, but you still need to collaborate through tweaking the models’ aspects? In cases like this, your go-to paradigm should be direct modeling. The paradigm encourages interoperability because it doesn’t involve using history trees to capture the design intent. It means importing and modifying the model developed using software X to software Y while maintaining the crucial details possible.
- Sophistication and complexity of design
Parametric modeling is the preferred approach when developing complex models. Alternatively, direct modeling is recommended for one-off simple designs. But note that the former needs significant effort and planning to develop a parametric model.
RELATED: How to evaluate the quality of a 3D model for parts & products
- Easy workflow and usage
If you’re looking for a design paradigm that doesn’t require lots of planning and is a tad simplistic and straightforward, the direct modeling paradigm is the better option. But if you want to dedicate more effort to understanding the model before starting the 3D modeling process, you’re better off with parametric modeling. It allows you to capture the design intent and define relationships between the dimensions and the rest of the parameters.
- Learning curve
It’s recommended to choose direct modeling if you’re a beginner or hire 3D modeling design services for assistance. Direct modeling is easy to learn and use, is flexible, and requires little planning or effort to achieve the preferred solid model. Direct modeling is ideal for workflows that don’t require 3D modelers to dedicate lots of resources, such as money and time.
How Cad Crowd can help
Cad Crowd is a platform where you can find parametric and direct modeling services experts for your 3D modeling needs. Freelance parametric modeling experts can help your company transform your design and engineering projects into sophisticated CAD models. Contact us for a free quote.