How can you reduce painful product development costs for your company? Even artisans and inventors from centuries ago understood the importance of prototyping in the product development process. They created rudimentary yet fully-working versions of their ideas before making the necessary refinements to build the primary artifacts in accordance with the plans. Features and functions must be defined as early and clearly into the project as possible. The prototyping phase is meant to analyze whether the would-be product carries all the predetermined characteristics and properties.
However, during this crucial phase, things can be further optimized beyond the initial plan. At the same time, it is possible for the designers to omit certain features due to various reasons such as manufacturing feasibility and budget limitations, among other restraints. The final version of a product may not be exactly the same as the original plan, but of course, it has to meet the needs of the intended users. In today’s hardware & research development, prototyping is made easier thanks to the proliferation of computer-aided design (CAD) tools used CAD services professionals, engineers, and manufacturing professionals.
Which prototyping technique and how much?
There is no single easy answer to that. Many factors determine the cost, among the most pertinent is the prototyping technique used. Various options are available, including:
- White model: simple non-functional visual representation of design made of modeling clay or solid builds. Prototyping may take less than 24 hours.
- 3D Printing: additive manufacturing technique to build prototypes of limited functionality, accurate details, and textures.
- Stereolithography (SLA): a more precise 3D printing method using UV laser and UV-curing resin. Precise prototyping thanks to the small focal width of laser in comparison to nozzle size in FDM (fused deposition modelling) counterpart.
- Selective Laser Sintering (SLS): on the higher-end of 3D printing equipment is the SLS machine, which utilizes powdered materials to be melted, fused, or sintered using lasers of varying power. The process can produce accurate prototypes with complex geometry and interlocking components.
- Micromachining: subtractive manufacturing technique using such machines as CNC (computer numerical control) and EDM (electrical discharge machining). Prototype is made from a single block of metal or other durable materials.
- Vacumm casting: silicone molds are made using prototypes. The molds are then used to create identical parts. The result is production quality hardware. Metal casting option is also available.
- Prototype tooling: urethane, soft, or full production tooling for injection molding. Prototype tooling produces hard-tooled plastic parts, soft is better for preliminary samples, whereas full production is suitable for final prototype with tighter tolerances.
Cost-per-unit examples
Any of those techniques is possibly done once the CAD file of the model is available. As an example a startup company designs a high-end digital clock radio; the prototyping options are:
Prototyping Method | Time | Cost/Unit | Typical quantity | Expected Result | Limitation |
White modeling | 24 hours | $1000 | 1 set | Appreciation of scale | No functionality |
3D Printing | 24 hours | $350 | 1 – 3 | Partially functional | Not precise |
SLA and SLS | 1 week | $2000 | 1 – 3 | Very accurate | Rigid |
Micromachining | 2 weeks | $2000 | 1 – 3 | Exact material | Restricted flexibility |
Vacuum casting | 3 weeks | $300* | 1 – 100 | Fully functional** | Short mold life |
Prototype tooling | 6 weeks | $10-15* | 50 – 3000 | Fully functional** | Tooling restrictions |
Soft tooling | 6 weeks | $10* | 500 – 10K | Full detail, functional | Expensive |
Full production tooling | 12 weeks | $8* | 5K – 1Mill | Full detail, functional | Expensive |
*Tooling cost not included **Fewer than 30 pieces |
Additive prototyping adds material during the process; subtractive takes away the material. Both can be used for production as well. There is also a hybrid approach, which takes advantage of both techniques, for example in the polishing process of a 3D printed part. Either additive or subtractive method comes with reasonable pricing, but only for low volume prototyping especially when the product uses certain components that cannot be easily fabricated or mass-produced.
Considering the rates per unit, large-scale prototyping using either method is not ideal. It costs too much, without the promise of full functionality. Casting and tooling are more appropriate for higher volume prototyping and production. When budgets become the biggest hurdle in the design process, even a partially functional prototype may help secure funding from investors.
Evaluation, testing, & development
Prototype, by definition, is the first working model of a design for evaluation, testing, and development. It will be subjected to quality assurance procedures in order to ensure that the manufactured products meet all the predefined requirements. Prototyping is just one part of the product development process. There can be a few different prototypes developed before a product is ready for manufacturing. The first prototype is most likely used only to validate the form and fit of the design.
Next is the preproduction, built on and improved over the first one. This second version is more expensive to make because it is essentially the final product itself, used as a sample. In fact, the cost to build this version is more expensive than the actual unit to be marketed because there is no large-scale bulk pricing benefit.
Why build hardware prototypes?
For electronic products (and any other type for that matter), constructing prototypes allow the design and engineering team to learn more about the product functionality before it is sent to the production line. Whether the prototype fails or is fully working as intended, the team gains valuable information and a better understanding of potential issues as well as the product’s strengths and weaknesses under normal usage. If necessary, the team can propose improvements to further reduce the risk of failures.
A product design may look pretty on a computer screen when drawn using CAD. Until the digital concept is transformed into a physical artifact, however, it is almost impossible to tell if the product will work in a real-life usage environment. Creating multiple prototypes, including the “looks-like” and “final product” versions adds to the product development budget, but this phase is not optional. It is better to recognize design flaws prior to production rather than having to go back to the drawing board after market launch.
Identifying design problems and solving them as early as possible during the development cycle is key to keeping the project within the estimated completion timeframe and budget. Fees associated with EVT (engineering validation test) and DVT (design validation test) would be a mere fraction compared to the potential loss due to late detection of issues.
EVT is done on the first prototype to ensure that the basic version of the product meets the functional requirement in the original specification. Tests may include powered-on simulation to detect electromagnetic and thermal problems if any. Connections between components and fit of parts in the assembly are covered too. DVT consists of a series of intensive tests including performance, reliability, environmental safety, and compliance with regulatory guidelines.
What are EVT and DVT prices?
For consumer hardware electronic products, validation tests generally run from about $1000 to $1500 and are done in a week or so, maybe quicker. It may take longer and cost more money for more complex heavily-regulated products such as medical devices. From POC (proof of concept) to EVT and DVT, several hundreds of product units are required for thorough analysis for the sake of reliable results. The total cost of material adds up as the product moves through its development phases. POC may only require 1 – 3 units, but DVT may use up to 200 units.
Cost for hardware prototyping
Again, it is a very broad question with many answers. Specific answers come when you have a specific product in mind. The good thing is that consumer electronics products categorically cost less and are quicker to prototype than medical-grade and industrial devices. Prototyping price variance can be enormous because each product presents challenges in terms of the production budget. To put it in a simple way, a professionally built hardware prototype of a consumer electronics product will cost anywhere from $300 to upwards of $100,000.
Selected Hardware Issues
- Requirements for custom-fabricated components, as opposed to readily-available ones
- Interactive user interface
- Sophisticated software requirements; many modern electronics run on proprietary software/firmware
- Connection with smartphone apps
- New features that have never been done in the product category
- Web connectivity
- Hardware materials
- Who you are hiring to get the job done
The price for prototyping also depends on what specific work is required for the process. In hardware product development, there are multiple stages of prototyping and each serves a different purpose. A combination of rapid prototyping (3D printing) for the hardware and Arduino for software developers to build and test a fully-functional product iteration can set you back a combined fee of a little less than $50,000; a good portion of that money goes into the software programming part.
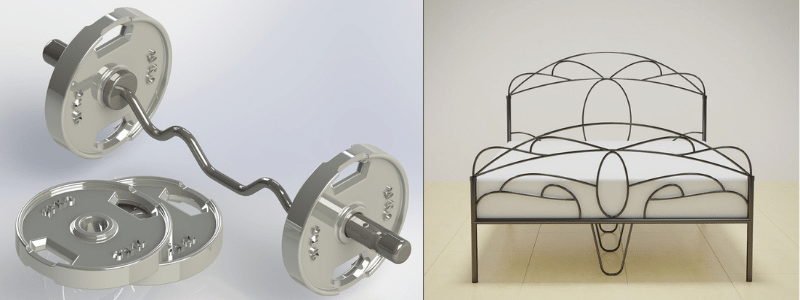
Product requirement document
Design and prototype are created in accordance with the set of non-negotiable constraints and specifications listed on the product requirement document (PRD). The specification covers not only the range of components required but also details like dimensions, power source, waterproofing, durability, safety hazards, and so forth. When connectivity is key functionality, the level of accuracy and compatibility with other products are taken into account as well.
Just like the prototyping phase itself, PRD is only part of the entire product development process. Assuming a startup only has a PRD without any meaningful analysis and market research, transforming the concept into a fully-working prototype can cost $200k – $300k. For a turnkey service to the point where the product actually gets to the production line takes more investment.
Other supply chain issues
Since it is highly unlikely that you can get through EVT and DVT with just a few working units, the supply chain affects the prototyping price a great deal. For example hardware companies in Shenzhen, China can probably iterate product designs at lower cost and quicker turnaround, thanks to the massive market for all sorts of electronics components, compared to those in the United States.
Language barriers and reputation for a lower standard of quality, however, can present their own challenges to product development. Talent pool and contract manufacturers in the US are much more promising, experienced, and likely easier to work with on these kinds of projects. Even when the US-based prototype maker you hire actually gets their parts from elsewhere, the workflow is easier on your part.
Consider the technologies that you can access. For the first hardware prototype, a 3D printing machine is good enough to build a “looks-like” or visual sample of the product. A rapid prototyping service charges around $100, maybe less if the design is not that intricate with details and textures. It can be more than several hundred of dollars, but the rate is still a bargain considering the alternatives. For example, the fee for creating an injection mold for a prototype in the US can cost thousands of dollars. Save the budget for injection molding later when your product is ready for large volume manufacturing.
What is the hourly rate for prototyping?
Very few prototype makers use an hourly rate to determine the total cost; most would consider the difficulty level then charge on a per-project basis. That said, the hourly rate remains a factor to calculate the labor cost. An hourly rate of $50 to $200 is just about right for a design firm in the United States. The firm typically consists of engineers in software, electronics, and mechanical fields in addition to employees in administrative support. As an example, an hourly rate of $150 will be used to determine the hardware prototyping cost.
Alarm clock on wheels
The specific type of product will be a digital clock radio. The main goal is to build a prototype into a fully-functional clock radio with an alarm as well as a feature that forces the owner to wake up from bed to stop the alarm. Since it is an alarm clock on wheels, the product has a battery-powered motor to move the wheels, a tilt sensor, an LCD for the clock and radio, and a microcontroller board. There are also FM modules along with an audio system. Amplifiers and speakers add to the complexity of the design as well as the lighting system, external power supply, and software.
Should you hire individuals or a design firm?
There can be a massive difference in completion time, budget, and quality depending on who you are hiring to build the prototype.
Hire a hardware development firm:
- When you are not yet familiar with product development. You don’t have a network of professionals in the product category, and assembling a team would take a long time.
- When budget is not an issue. A single prototype of a consumer electronics product can cost five figures. You may need multiple iterations throughout the process.
- When wuick completion time is non-negotiable. A team of professionals in a design firm usually can get the job done faster. In addition to in-house talent pool, an experienced firm most likely has established relationships with reputable component suppliers.
- When software is the main focus. Sometimes hardware prototype only means the outer enclosure of a product. When your main business concerns the development of software, it is best to hire a design firm to build the physical prototype so you can focus on your core business.
To get a good idea of how much a hardware development firm charges for prototyping services, here are some companies in the United States and Canada, listed by Clutch, a market research firm based in Washington, DC.
Company Name | Location | Main Services | Rates per hour |
DiveDesign, LLC | Boonton, New Jersey | Hardware design, development, and rapid prototyping | $150 – $199 |
Kickstart Design | Milwaukee, Wisconsin | Product design, prototyping, CAD | $100 – $149 |
Mako Design + Invent | San Francisco, California | Hardware product development for small businesses | $100 – $149 |
GloberDesign | North Miami Beach, Florida | Product design, CAD, prototype | $100 – $149 |
Concepto Studios Inc. | Fort Lauderdale, FL Santa Clara, CA | Product and prototype design, contract manufacturing | $150 – $199 |
nAO (not another one) | San Francisco, California | Hardware and software concepts, early prototyping | $50 – $99 |
Verify Inc. | Edmonton, Alberta, Canada | Product and prototype design, CAD, contract manufacturing | $100 – $14 |
Design1st | Ottawa, Canada | Full-service product design and engineering firm | $150 – $199 |
Hire individuals:
- When you know some experienced prototype makers or someone who can introduce you to those people.
- When your budget is tight. A design firm will charge a premium rate for the same prototype done by individual prototype makers. Think of it as hiring a group of freelancers instead of an agency.
- When the project is not done in a hurry. Since you are doing all the recruitment on your own, it may take a while until you find just the right people to join the team.
- When hardware design is the most important part of the project. Retaining the creative control over the hardware is easier if the development is kept close to your chest.
How Cad Crowd can help
Cad Crowd’s freelance specialists carry the knowledge and experience to help you with 3D modeling and help you connect with the 3D printing, rapid prototyping, and manufacturing services you need to bring your product to market. Save time by reaching out to us! to take to your preferred manufacture. Check out how it works or get a quote.