During the concept phase of development, virtually nothing is off-limits. The single goal of development is to come up with product design, to stretch the limits of imagination, and to come up with an idea that stands out from the rest.
Once you have come up with a great idea that meets an urgent need—and more importantly, how to do it—getting it to be manufacturer friendly becomes the next challenge. At best, a product that isn’t manufacturer friendly will be more expensive to create, and at worst, it may not be possible at all. Planning your product to be manufacturer friendly from the first step will make the whole process smoother.
In recent years, proactively focusing on making product design services with ease of manufacturing in mind has become very popular. It’s so popular, in fact, it even has a name—DFM or “Design for Manufacturability.”
Before this concept, most designers did not take manufacturing into account before producing their designs. The viewpoint was simply that they would design it and find someone willing to manufacture it without any consideration of the difficulties presented by the design.
Now, making a product easier to manufacture is a significant consideration. Manufacturer friendly products are not only better for manufacturers and easier to produce, but they’re also significantly cheaper as well.
Engineering for Manufacturability
While there are plenty of individual things you can do to help make a product friendlier to manufacturers, it takes a true engineer to put them together in a way that both stays in keeping with the original product and is cheap and efficient as well.
Designing for manufacturability boils down to five basic parts:
- the process,
- design,
- the materials,
- the environment, and
- compliance.
All of these things have to be taken into account when creating a product that both meets the necessary requirements for the product while also making it as easy as possible to manufacture.
The Process
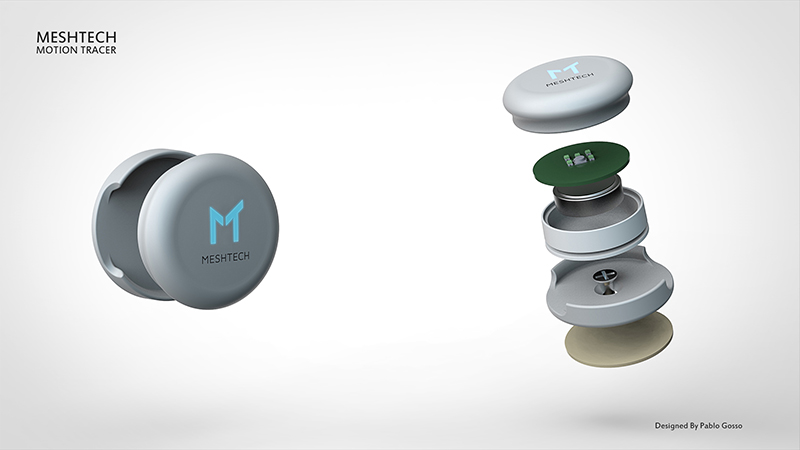
When designing your product, it is helpful to understand how the manufacturing process works. When you are focusing on making a product work, how it will look, and other factors, it’s easy to forget about manufacturing at all.
It’s worth understanding what processes are involved, what each type of manufacturing is needed for, and how they are used. When you understand how a product is manufactured, it becomes easier to design with that in mind. Here are a few common manufacturing concerns that involve the process itself.
1. Avoid Walls that Are Too Thin
Injection molding and casting services are amazing for mass production and allow you to make a significant quantity of a product very quickly. By its very nature, however, creating very thin walls is extremely difficult to pull off well.
When considering the thickness of the design, taking into account the thickness of the vertical walls is more important than the thickness of the horizontal walls.
Make your walls 0.0625” or thicker to avoid unpleasant feedback from the machines that may leave unwanted blemishes. You’ll get a higher quality finish, and it will be easier for your manufacturer to produce, which will make everyone happier.
If you do need an ultra-thin wall, ask your manufacturer beforehand if they have specialized presses that can handle extremely thin designs.
2. Avoid Drilling Long Holes
The longer the manufacturer has to spend drilling a hole, the longer the product will be using their machines. If the hole is long and deep or has complicated features at the inside of the hole, that means even more time and possible special equipment.
If the hole you’re drilling is deep and has a tight corner and more drilling, it’s going to be very difficult for your manufacturer to create it. Avoid asking for any drill holes that are more than a 6:1 tool length-to-diameter milling to make your product as manufacturer friendly as possible.
If your product needs to have a hole longer than this or will have a lot of turns or other complications at the end of the hole, you may want to design it so that it can be done in a different way.
3. Avoid Sharp Corners on the Inside of Your Product
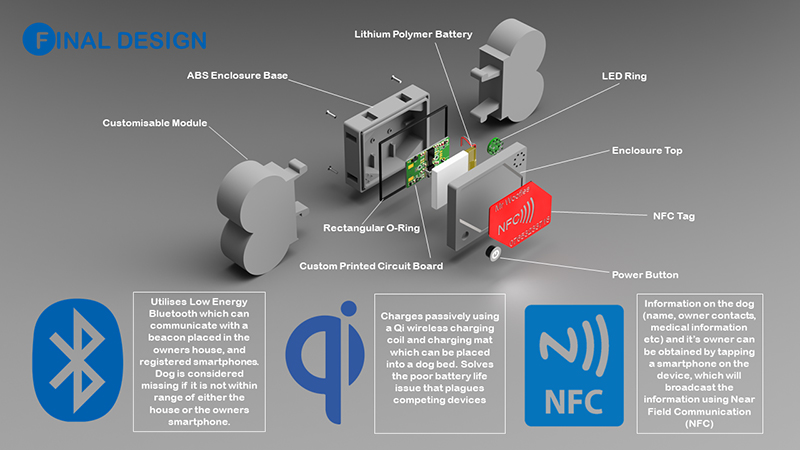
Just as it is tough to change directions while milling internally, it is also hard to make sharp corners internally. You can use other methods to make it easier to manufacture, such as mouse-earing the corners so they are not sharp and difficult to maneuver a machine through.
How your manufacturer will handle internal parts of your product is something you should take into serious consideration throughout the design process. It might be easy enough to see how to drill a hole or where a corner should be, but how your manufacturer should access the inside of the product also needs to be addressed.
4. Specify Cone Bottom Holes
There are two ways for a manufacturer to create a hole in your product. The first way is to drill it, and the second way is to mill it. Drilling creates a cone bottomed hole and is much easier and faster for the manufacturer. Milled holes create the flat look at the bottom but take up more machine time to produce.
Unless you have a specific reason for the bottom of a drilled hole to be flat, plan for cone bottom holes, so your manufacturer knows it’s okay to drill instead of mill.
5. Avoid Lots of Parts
The more parts needed for a product, the more time the product will have to be on the machine. More run time means it will cost more money for your product to be made, and if it also has to be assembled, it will be even more time-consuming.
Time, of course, isn’t the only consideration. A lot of parts that need to be assembled means a higher chance for error. No one wants to get an awesome 800-piece LEGO set with a critical part missing, and a component in any other product is no different. Have a reason for every part that you use, and if you can simplify the product without losing the usability of the product, do so.
Striking a Balance between Cost and Manufacturability
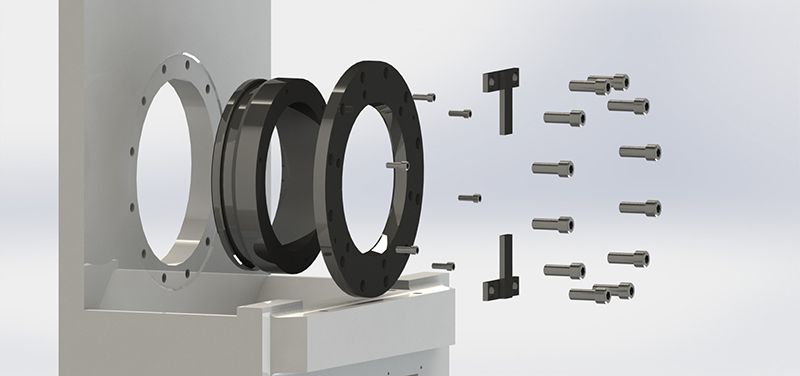
It costs money to have a product made by a lot of different parts. While sometimes that is essential (after all, we pay a premium for those LEGO sets because the vast amount of parts is part of the allure), sometimes they’re just plain unnecessary. If you can simplify a product so that it doesn’t require so many parts, it will save money over time, since one-piece molds are less expensive than multiple pieces.
On the flip side, if it will be extremely difficult to make a product out of one piece (such as when you’ll need to drill a hole and change angles, as mentioned before), splitting it into a few easy to assemble parts may actually be cheaper, and certainly easier on the manufacturing company.
1. Avoid Mirror Image Parts
This detail may not be something you think about in your everyday design, but they will make a difference to the manufacturer. During the manufacturing product, parts can be stacked together and machine drilled for holes all at once. If you need a part with holes on the left side, and another with holes a little different on the opposite side, creating one part that has all the holes and using them differently will save time and money for the manufacturer.
This way, instead of having to run a small batch of both of your parts, all the products can be made at once. If you can make parts that can be used both left side and right side, you’ll save a lot of money and make your manufacturer much happier.
2. Tolerance Matters
In manufacturing, there will always be slight variations in how each product comes out. How much a product can vary is called its tolerance. Most engineers create a product with tolerances that are far more restrictive than is necessary to get the job done.
Set your tolerances as unrestrictive as possible to make it as easy as possible for your manufacturer to finish the product. Save tight tolerances for times when it matters, not for every single part.
The price of extremely tight tolerances tends to go up exponentially past a certain point, so it benefits you as well to have wider margins where possible.
What Type of Manufacturing is Needed?
Different types of manufacturing are easier than others. Injection molding is more difficult for manufacturers to tool compared to thermoforming. The cost per piece may be more expensive overall, however, so this may be something you need to take into consideration if you plan to have large runs of products.
If your product will be a small run, ask yourself whether it really needs to be injection molded, such as something with relatively thin walls, or if some or all of it can be thermoformed.
Design
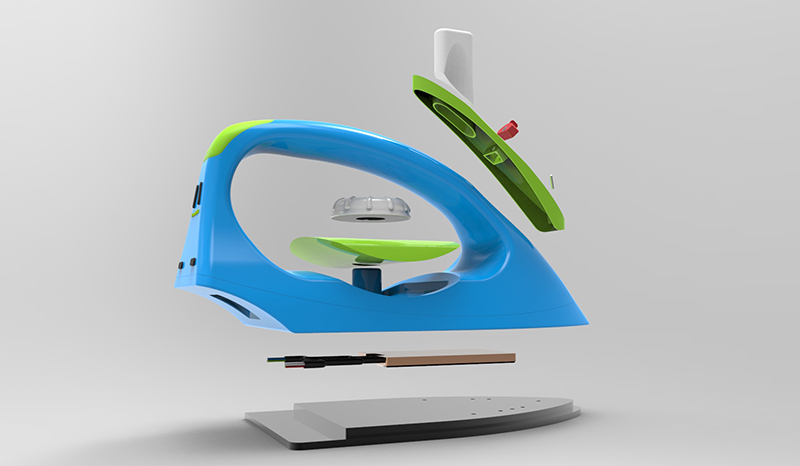
Much of the specifics of designing for DFM are discussed above, but it’s worth discussing design on its own as well. How you design a product matters, from choosing how the parts go together to where every bolt and screw goes on the product as a whole.
One other thing to consider is that your manufacturer may not necessarily have control over whether they can use your design or not. Certain types of products are subject to GMP, or Good Manufacturing Practice, which has certain requirements that need to be met. These practices are usually meant to keep everyone safe and healthy and to protect customers from buying a potentially dangerous product without being aware.
When designing, you should keep GPM in mind and also a few other things.
1. Can You Buy a Part? Then Don’t Design It
One way to reduce the number of parts your manufacturer needs to create is to take a hard look at the parts going into your design. You don’t need to design and manufacture your screws unless there is an excellent reason to do so. (A lighter product, for example.)
If a part already comes readymade and just needs to be ordered from a catalog, purchasing them is easier than manufacturing them. When you consider the cost of design and manufacturing, determine whether it’s overall cheaper.
2. Make Different Parts Look Very Different
Whenever you can, it’s best to use as many of the same parts as possible to cut down on costs and make the output as easy as possible. If there isn’t a good reason for two bolts to be of different lengths, there’s no reason to have them that way.
If there is a good reason to have two parts that look similar but are different, use colors, labels, or other methods to help manufacturers discern the difference between the two. This is especially important in fast-paced assembly environments, where a crew of workers may only have a few seconds to discern the difference between the two parts.
This benefit may also extend to your customers if your product is sold with some assembly required. It’s easier for customers to see which bolt goes where if they are color-coded, and if they can assemble it faster, they’ll be happier as well.
3. Discuss the Design with the Manufacturer
If you already know who your manufacturer will be with the product, reaching out at the design phase of development to ask how you can modify a design to make it easier for them can save everyone a lot of time.
The design phase is the easiest part of the product to change. Taking advantage of this to get changes your manufacturer might like before prototype design services or any testing has been done can save a lot of money in the long run as well. If you know something will be difficult to manufacture and have the time to figure out ways to fix it, the whole process will be sped up down the road. A few extra days or even weeks at the beginning could save months of time at the end.
Most manufacturers are happy to point out areas that need work, helping save time for everyone.
4. Reusable Designs
Another more indirect way of making a design more manufacturer friendly is to design with the future in mind. If your design can be later reused, such as for updated versions of the product or similar items, your manufacturer will already know how it goes together and will have molds already available.
Even if you never plan on updating that particular product or will be making something very different in the future, if you can use some of the same parts to make something new, you’ll still be saving on project costs because those molds and dyes are still available.
Materials
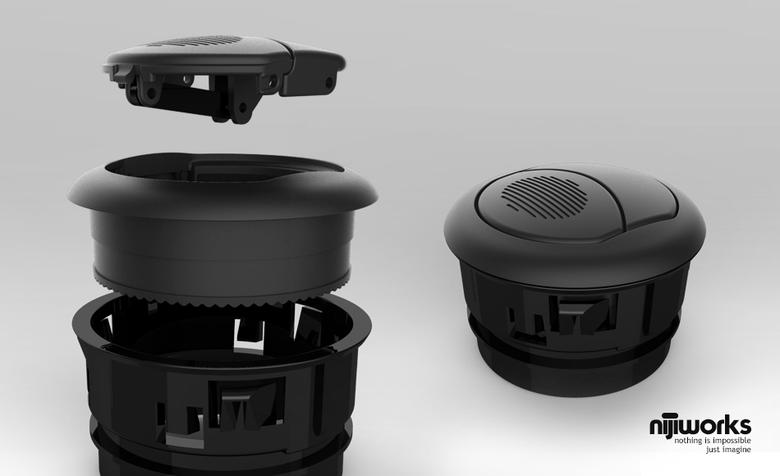
It’s not just what parts you use or how they are put together that defines a product. As you probably know, what a product is made of can make it vastly different from similar products. A jacket might be put together the same way as another jacket, but whether it is made of cotton, denim, or leather will change it in big ways.
Considering the material for how friendly it is to manufacturers can also make a difference in your price, the speed it can be made, and how easy it is to manufacture.
1. Weaker Materials Are More Manufacturer Friendly
You may have a very good reason for choosing the materials that you have. If your marketing is based around the sturdiness of the materials you have chosen, then you’ll want to use the best materials possible. If there’s no reason not to choose a weaker material, however, choosing them can help make your product easier to manufacture.
Weaker materials usually have higher machinability, which means it’ll be easier for the manufacturer to drill through a bit of plastic than, say, a bit of steel. If there’s no reason to use a stronger material for your product, don’t.
2. Other Factors
What material you choose depends entirely on what it needs to do. If it needs to be reflective, that will narrow down your choices of what is available. If it needs to be made from non-flammable materials, or be a certain strength, this will also change what your decision will be for the materials.
If you have specifications that need to be met, reach out to your manufacturer and find out what materials they have in their portfolio. If there is a material needed that they already have access to and you can use that one, it will help make the product easier for the manufacturer to make.
Environment
Your product won’t be useful if it doesn’t stand up to the environment it’s designed to handle. A poker for a fireplace won’t be any good if it’s made out of flammable materials, just as matches would be useless if they’re made out of inflammable materials.
This is another great time to ask about materials from your manufacturer. The more you can use materials they have easy access to, the faster and better the production will be.
Why Making a Product Manufacturer Friendly Benefits You
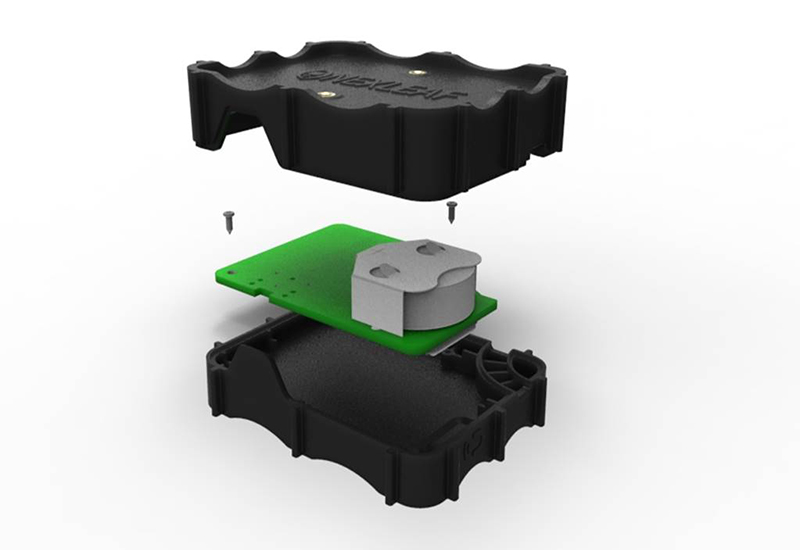
There are dozens of different ways CAD designers can make their product easier to manufacture. With so many manufacturers available both overseas and at home, it may not seem like it matters whether or not your product is easy for a product to manufacture or not.
As we have seen before, the easier it is for a product to be manufactured, the lower the price will be. Every second a machine is running to make your product, it’s a second that’s not being used on a project belonging to someone else. If a product takes more time to make, that extra time will be reflected in the price. If it is complex or requires special tools, this will also have an effect on pricing.
A product that is easy to manufacture will always have a lower price than a product that is not easy. A lower price means more profits for the company, happier customers who can buy a product with lower pricing, and a stronger outlook for the company. If you can figure out how to make your product less expensive than other products through clever design, but it can still perform the same function, you may be able to edge out competition that way.
The price incentive isn’t the only reason a manufacturer friendly product is beneficial to you. A product that is made with the manufacturer in mind will help you reduce the chances of a data file being sent back because the design isn’t manufacturer ready.
Many times, the designs get sent back because they aren’t ready to manufacture. Instructions for manufacturing are fairly complicated, with a data file that includes where every last piece should be placed, how thick the plastic should be, and several other details. Having the design manufacturer friendly makes it faster and easier to get something made, and made right.
Getting the product made to your specifications isn’t the only important part, however. If you don’t design the product with thought to how it is manufactured, you may find that your product is broken easily or doesn’t stand up well to the test of time. This will result in disappointed customers, or worse, a manufacturer that would rather not handle your products anymore.
Making your product manufacturer friendly is a lot of work. It takes thoughtful design to figure out how to make products using the same parts you have used before, designing symmetrical parts, and thinking about every detail individually. The result, however, is worth the effort. A product that is easy to manufacture will be produced faster, have fewer delays, and cost less than a product that was thoughtlessly designed. It may take more work, but the benefits outweigh the costs in many ways.
Cad Crowd’s Product Design Freelancers Can Help You Save Costs
Entrusting product design to skilled professionals can make a dramatic impact on how easy and fast it will be to manufacture it.
At Cad Crowd, we know that and, therefore, aim to connect business owners and entrepreneurs with the best talent that can help them develop manufacturing friendly products. We have a wide database of freelancers from all over the world. They are skilled, experienced, pre-vetted, and confidential.
If you’d like to get started, take a look at how it works. You can also launch a design contest and have the best talent find you.