Have you ever wondered why most tools are easy to hold and grip? It’s all thanks to the introduction of processes, including injection molding and casting services, insert molding and overmolding. However, if you’re not part of the industry or haven’t heard of these terms, they can be confusing. It’s understandable because insert molding and overmolding are two types of injection molding. Continue reading below to learn more about injection molding, insert molding and overmolding processes.
Table of Contents
- What is injection molding?
- How does injection molding work?
- What is insert molding?
- What is overmolding?
- Advantages of injection molding
- Disadvantages of injection molding
- Advantages of insert molding
- Disadvantages of insert molding
- Advantages of overmolding
- Disadvantages of overmolding
- How Cad Crowd can help
What is injection molding?
Molten plastic is injected into a mold during injection molding. The mold will then cool down, and the plastic will become solid. Companies use injection molding to produce various products, such as consumer goods, automotive parts, and medical devices.
RELATED: How to design products for injection molding & prototyping firms
How does injection molding work?
A popular technique used by manufacturing design firms, injection molding is used to create parts by injecting molten materials into molds. This is a relatively common process for plastics, although it applies to glass, ceramics, and metals.During this process, the mold of the product is made first. A mold is a hollowed-out block that will give shape to the liquid or molten material. The mold will then be placed on the injection molding machine.
The plastic pellets will be heated until they melt. This molten plastic will go under high pressure into the mold. While the material hardens as it cools, it will take on the mold cavity’s shape. Once the plastic cools down and solidifies, the product or part will be ejected from the mold. Injection molding allows the creation of parts of all sizes and shapes. Molds can also be designed to produce more complex internal features. This ability to develop intricate designs is why injection molding is applicable in different industries.
What is insert molding?
The manufacturing process of insert molding involves adding parts, mainly metal, on top of the molded parts. Insert molding consists of the use of inserts in the injection molding process. This process is done before the product is cured and helps cut down the processes required during assembly following molding. After the parts that will be molded on top of the product are obtained, another layer will be accepted after the parts are inserted into the mold.
Insert molding can be carried out in two ways: automated and manual. Manual insert molding is relatively cheaper than automatic insert molding. But as far as consistency is concerned, automated insert molding is the ideal choice. It reduces human errors and increases efficiency. Introducing inserts onto the mold cores cast using the automated or manual process will result in plasticizing the plastic pellets after the mold halves are closed.
The pieces will be ejected from the mold after the plastic hardens. The inserts will then be encapsulated in the parts. An excellent example of insert molding is the addition of a plastic layer over the screwdriver’s metal part for the plastic handle to be produced.
RELATED: Which manufacturing technology is right for your new invention?
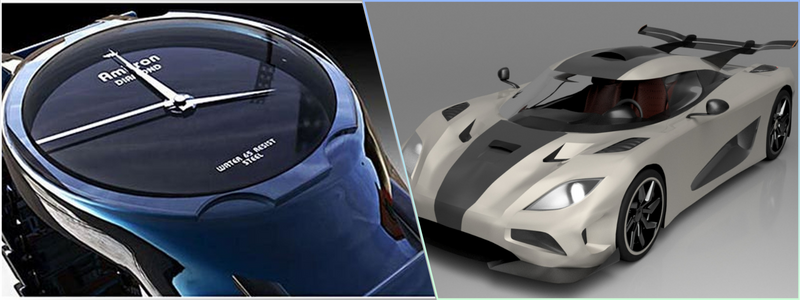
What is overmolding?
Overmolding is a manufacturing process involving a seamless combination of different materials into a single item or part. The overmolding process involves two essential steps. Molding and curing the substrate, typically plastic, is the first step. This is followed by direct molding the layer over the initial layer to produce a single product. Product design companies designing a toothbrush is a typical example of overmolding, where a basal layer is formed first, followed by a rubber layer.
Overmolding can significantly reduce production costs. Some of the critical components of the process include the rigid plastic base covered by a flexible, thin, rubber-like material. This manufacturing process has astounding versatility as it is helpful for different home items, including toothbrushes, hand tools, and razors.
Advantages of injection molding
1. High and efficient production
After the molds are developed, it speeds up the process, with cycle times only requiring 10 seconds. This ideal option for high- and medium-volume production runs from 10,000 parts to more than 100,000, depending on the molds used.
RELATED: An overview of injection mold materials and SPI standards for companies and firms
2. Intricate detail
High-pressure injection forces molten plastic into the mold, enabling the creation of intricate and detailed shapes.
3. More choices of materials
Choose from a diverse array of plastic materials tailored to meet the specific properties required for the final part.
4. Minimal to no post-production
Little to no post-production is required since the parts often have pleasing aesthetics.
5. Lower cost per part
The cost per part is meager for high-output production runs.
6. Reduced waste
Unlike most manufacturing methods, very little waste is produced during molding.
RELATED: Injection molding tips for cost-effective prototypes and mass-manufacturing by a mold design firm
7. Repeatability
Identical products can be manufactured repeatedly. It’s a good choice for parts with high reliability and tolerances across high volumes.
Disadvantages of injection molding
1. Design limitations
There are several design elements a product designer need to consider during injection molding. These include controlling the thickness of the wall, preventing sharp edges and undercuts, and using radii and drafts to eject the parts.
2. High initial cost
A substantial capital cost might be required for higher volumes of production that require a great deal of machining and time to produce.
3. Longer initial lead times
Some tools may take several weeks to be produced, so consider using other technologies like CNC machining services or 3D printing, especially for lower production runs.
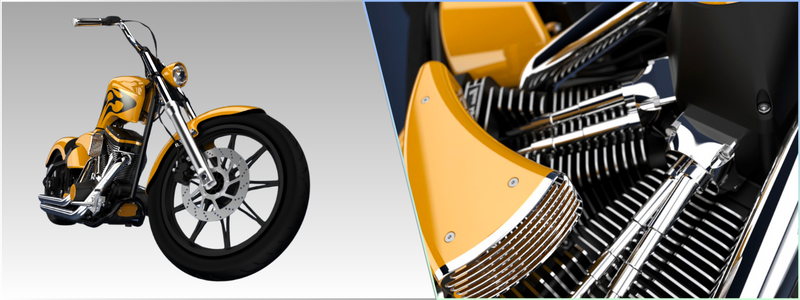
4. Not cost-effective for small production runs
Injection molding might be unsuitable for smaller production runs when other manufacturing processes are more suitable.
RELATED: How to save money on injection molding: 10 tips from an engineering design firm
Advantages of insert molding
1. Lower cost
Insert molding makes it possible to create thousands of parts of products in just one day. Its economic significance leads to reduced costs for the entire molding production process.
2. Faster assembly time
The assembly of products needed in CNC machining is often challenging. However, insert molding can do away with the need for assembly. The overall production cost is reduced because no assembly time is involved.
3. Multipurpose parts
The parts produced by 3D modeling design services for machine parts using insert molding can serve various purposes depending on the specific function that the product is intended to serve. The combination of metal and plastic parts will benefit not only the end users of the product but even the manufacturers. The use of plastic parts can also improve the design’s flexibility and make it lighter than metal.
RELATED: 3D printing technologies for modeling and prototyping
Disadvantages of insert molding
1. Multiple technologies for manufacturing
Machining processes such as die casting are required for custom-designed inserts. This is made before the start of the actual process of insert molding. This results in a higher cost per part.
2. The complexity of part design
The injection molding designers must be familiar with the design of the technology’s manufacturing principles for them to produce custom-made metal inserts in insert molding. This is the only time when it becomes practical to integrate the involved technologies.
Advantages of overmolding
1. Eliminate the need for adhesives
Adhesives are no longer required in overmolding since the different parts get the chance to fuse during the process. This will increase the durability of the parts or products produced. It also results in an overall reduction in production costs.
RELATED: A product designer’s guide to design for manufacturability
2. Better product performance
Adding other suitable quality materials to a product can significantly improve its performance. Those products that go through overmolding have two edges in terms of materials over the traditional products used in most industries. This will, therefore, enhance the performance of the products made using overmolding.
3. Improved flexibility of materials
Combining several parts is required in overmolding, increasing the part’s flexibility because it leverages each of the benefits of the involved materials. Design for manufacturing and assembly firms can also use an overmolding design guide to enhance flexibility further.
Disadvantages of overmolding
1. De-bonding
The risk of delamination may occur if two different parts are bonded together in an injection mold. Delamination may take place if there is a change in the range of optimal temperatures. Mechanical interlocks will be required when the available heat fails to bond the two materials successfully.
2. Multiple processes of production
Two steps are involved during manufacturing using overmolding, which can increase the cycle time of each part. The production cost may also be higher than just molding one part in one process. Overmolding also needs more tools compared to single molding because the process involves two steps.
How Cad Crowd can help
Injection molding and its two specific types, insert molding and overmolding, are efficient and helpful processes. These techniques help produce different parts with various uses and applications. Before embarking on your project, it’s vital to assess these methods to make a well-informed decision. Knowing what type of finished part you plan to make and its specific application will help you identify the proper process. Cad Crowd offers injection molding and casting services and can help you find specialists to guide you through every step to ensure successful production. Contact us for a free quote.