Injection molds and prototypes, usually made using materials like steel and aluminum, can be outputted with the help of CNC programming services. It is highly recommended, and designers tend to lean towards using it when it comes to designing injection molds because of its precision, accuracy, and exceptional suitability for different mold designs. Sadly, this option is far from ideal if you want to launch your new products faster or if you have a limited budget.
It is good that 3D printing is now here to improve manufacturing injection molds and prototypes. 3D-printed injection molds are made using plastic polymers like polyethylene, and ABS using any of the various types of modern 3D printing technologies. The choice to use 3D printing technology mainly depends on the properties, intended mold sophistication, and material makeup of the mold.
3D printing injection molds is an affordable process that suits different designs, not to mention that it is also faster to manufacture the mold. The overall process that prototype design professionals use for part and prototype production that involves injection molding is also quicker.
Table of contents
- Benefits of using 3D printed injection molds and prototyping
- A more straightforward and more flexible mold design process
- Lower cost
- Recommended for low-volume production runs
- Less industrial expertise is required
- Important considerations before using 3D printed injection molds
- Draft angle
- Shape and size
- Smooth finishing
- Number of prints
- Design tips for 3D printed injection molds
- Materials
- Mold design
- Part design
- The bottom line
- How Cad Crowd can help
Benefits of using 3D printed injection molds and prototyping
3D printed injection molds are critical in part manufacturing and prototyping thanks to their flexibility, low cost, and other benefits. Here are more reasons to convince you to use these technologies for your following projects:
A more straightforward and more flexible mold design process
3D printing offers better skills when it comes to mold design. This helps mold manufacturers and designers to design and produce molds more easily. Aside from this, correcting mistakes after a mold has been 3D printed is so much easier and cheaper, thanks to the use of plastic.
Lower cost
Injection molds are produced using plastics that are much more affordable compared to metals like steel and aluminum used in the traditional process of injection molding. 3D printers used by 3D printing experts are also cheaper than CNC machines. There is also the fact that the printing process consumes considerably less time. Thanks to this cheaper price, the 3D-printed injection molds can be considered the most cost-effective choice for production runs that only require low volumes. Enthusiasts even claim that the use of one can already save around 80% of the total costs of mold manufacturing.
RELATED: How to design products for injection molding & prototyping firms
Recommended for low-volume production runs
As mentioned earlier, 3D-printed molds are better for low-volume production runs than CNC-machined molds. For starters, the initial investment required to make them is much lower than that required for CNC machining. In addition to this, the materials used for manufacturing, specifically plastics, are way more affordable. This means that mold designers no longer have to worry about augmenting the number of injection molded parts just to cover the production cost.
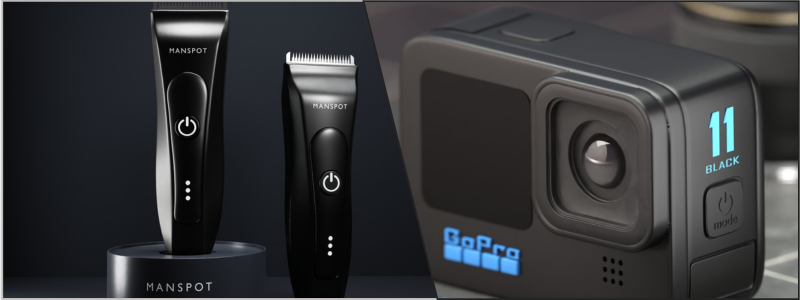
Less industrial expertise is required
Anyone who has good knowledge and familiarity with 3D printing can easily print injection molds, This eliminates the need for specialized industrial design services, which will only increase the cost of labor of traditional processes of mold manufacturing such as CNC machining.
Important considerations before using 3D printed injection molds
The process of injection molding will only be successful depending on the 3D-printed mold. Thus, it is essential to consider several critical factors, including the draft angle, number of prints, and others, as listed below:
RELATED: Understanding injection molding, insert molding, and overmolding for companies
Draft angle
The draft angle helps in the correct ejection of the part that has undergone injection molding after the process is completed. It means that you have to make sure that you properly integrate the correct draft angle while designing the mold. The suggested draft angle of 20 can make it easier to remove the molded part.
Shape and size
It is essential to determine the size of the part that will undergo injection molding and select the corresponding shape and size for it. Among the key differences between a CNC-machined and a 3D-printed mold from injection molding and casting experts is none other than its size. In general, 3D-printed molds are smaller. The result is that it cuts down the size of the parts that have been injection molded that you can work with, unlike CNC-machined molds.
Smooth finishing
The surface integrity of 3D-printed molds is often lesser than that of metallic injection molds because of the high temperature used in injection molding, which can cause degradation of the mold. This is why these molds might not be the best choice for projects that require smooth finishing. Instead, it makes more sense to opt for steel or aluminum injection molds.
RELATED: Prototype injection molding: 7 materials commonly used by design firms
One more possible solution here is to take advantage of a protective coating crafted on the printed mold from materials like ceramic to cut down heat degradation and create a smooth finish. Take note that the cost of the 3D printing technology, material, and general service will have a direct effect on the kind of 3D-printed mold selected.
Number of prints
A 3D-printed injection mold has weaker structural integrity compared to its counterparts made in metal. This is why they are more recommended for low-volume manufacturing. Many 3D-printed molds, in general, only apply to just 30 to 100 runs. This makes them the ideal choice for rapid prototyping services. On the other hand, opt for a traditional mold made from steel or aluminum if you need something higher.
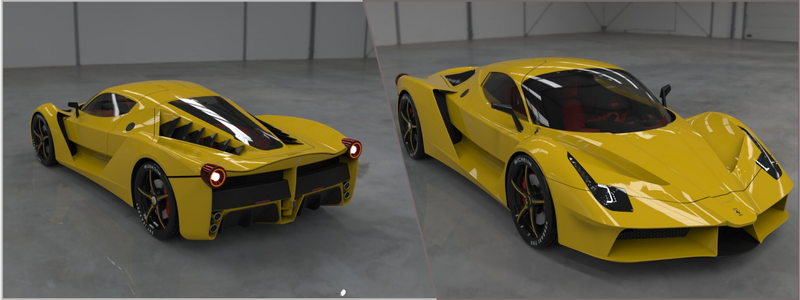
Design tips for 3D printed injection molds
It would be best if you considered essential factors like materials, injection molding defects, parts, and others when designing a mold with the help of 3D printing. Here are some helpful tips for cutting down the challenges and difficulties often associated with using 3D printing when using injection molds:
RELATED: An overview of injection mold materials and SPI standards for companies and firms
Materials
Most materials can be used to make 3D-printed injection molds, including acetal, PP, Nylon, ABS, and PETG. There are two primary things that you should consider before you choose a material to use to 3D print plastic molds: stiffness or strength and temperature resistance. The suitable plastic polymer for 3D-printed injection molds must be stiff and robust after printing. Stiffness and strength will help the mold endure the pressure produced during the process of injection.
Injection molding takes place at a high temperature to make sure that the molten plastic will have maximum flow. Thus, the melting point of the plastic material that will be selected to make the mold must be higher compared to the injection molding material.
Mold design
The mold design is the foundation of mold manufacturing design services. Inner face orientation, layer height, shallow air vent, and channel are some of the critical factors to consider when evaluating a 3D-printed mold’s mold design. The orientation of the inner face of the mold must not allow any contact with support. The surface quality of the printed parts will increase because of the total avoidance or reduction of support marks. It also cuts down the need for post-processing.
RELATED: Overmolding design success: strategic considerations for company prototype designs
Printing at a lower layer height also improves the printed mold’s smoothness. It reduces the visibility of print lines. Meanwhile, adding an air vent to the mold design can help expel any air trapped during the process of injection molding. The recommended shallow air vent of around 0.5mm can help decrease the risk of defects like injection molding flash.
Channels can also be incorporated into the design of those molds intended to be used for over 20 runs. It will let you embed metal tubes and rods and lessen defects in the injection molded parts like warping. The use of a channel also reduces cooling times.
Part design
Just like the mold, you might also want to add some of the design tips stated below to the injection mold part you plan to make:
RELATED: Guide to surface finishing for 3D printed parts
Include a draft angle
The draft angle part design experts use will make it easier to remove the injection molded part from the mold used for the printed injection process. The suggested draft angle is 20, which depends on the specific part in question. Stay away from sharp corners. You can prevent sharp corners if you include radii on the corners and edges of the mold. Observe uniform thickness. A uniform wall thickness is expected across the entire injection mold part to reduce potential defects like warping after and during injection. However, in instances where the walls must be thin, gussets and thin ribs can be included to improve the wall strength.
Get rid of flash
Flashing is a widespread flaw in injection molding, where the molten plastic ends up spilling from the mold throughout the injection process and then solidifies afterward. This happens because of the high injection pressure, an overfilled mold, or an imperfect mating of mold halves.
Using runner systems in the mold design and guaranteeing tolerance in the part line can help get rid of flashing with 3D-printed injection molds. But if these fail to work, post-design tweaks can also be done, such as cutting down the injection pressure and enhancing the clamping force.
RELATED: Injection molding tips for cost-effective prototypes and mass-manufacturing by a mold design firm
The bottom line
3D-printed injection molds are different from traditionally designed molds. These are applicable in various industries that need low-volume production for complex and simple product designs. Taking advantage of this modern technology can help bring your ideas to life.
How Cad Crowd can help
Contact Cad Crowd today and let us connect you with the best providers of 3D-printed injecting molding services that can turn your company’s product design ideas into reality. Get a free quote today.