In this article, we share CAE engineering costs, company consulting rates, and services pricing. CAE, or computer-aided engineering, focuses on improving product design and solving engineering problems using computer software. It applies to various engineering processes, from design to manufacturing. CAE utilizes digital simulation to perform design validation, ultimately leading to product optimization.
A massive advantage of hiring CAE experts is that it doesn’t require a physical product to conduct the tests. The procedure is a continuation of CAD, which models a product on a computer to see if the design meets the desired parameters. Simulation in a virtual environment saves considerable time and money, yet it still delivers accurate results.
Table of Contents
RELATED: What are CAM engineering costs, company fees, & consulting service rates?
Cost of CAE
In the United States, CAE engineers earn from $67,725 to $86,767 annually (or around $32 to $41 hourly); the median salary is $70,000 ($33 per hour). CAE may include many tests, including but not limited to thermal analysis, finite element analysis (FEA), and computational fluid dynamics (CFD). An exact project quote depends on the scope of the work and the professional’s qualifications. A CAE design engineers uses CAD and CAE tools during the early development phase to aid decision-making regarding product materials, shape, and overall design.
Cost of CAE services | Range | Median | Additional notes |
---|---|---|---|
Annual Salary | $67,725 – $86,767 | $70,000 | U.S. CAE Engineer’s Annual Salary |
Hourly Rate | $32 – $41 | $33 | U.S. CAE Engineer’s Hourly Rate |
Project Quote | Varies | N/A | Depends on scope, qualifications, and complexity |
Note: The cost of CAE services varies depending on the project’s complexity, the specific design aspect being analyzed, and the qualifications and expertise of the product engineering company. The table provides a general overview of the cost and types of CAE analysis. An exact project quote is determined based on the project’s scope and requirements. CAE simulations are conducted using 3D models, eliminating the need for physical prototypes and depicting real-life conditions for product testing.
RELATED: CAD Crowd marketplace for CAD, CAM and CAE drafting services
All the computer-based engineering techniques performed under the umbrella of CAD and CAM (computer-aided manufacturing services) fall into the CAE category. Each CAE analysis focuses on a specific design aspect. However, some products require additional research to ensure safety, efficiency, and performance. Relatively simple products such as sports equipment and bicycles may only need FEA simulation; complex electronics and piping infrastructures must undergo CFD and thermal analysis to validate the designs before production. Otherwise, a small mistake in design can lead to an expensive revision.
Types of CAE analysis | Examples of products | purpose |
---|---|---|
Finite Element Analysis (FEA) | Sports equipment, bicycles | Validate design and analyze stress distribution |
Computational Fluid Dynamics (CFD) | Electronics, piping infrastructures | Analyze fluid flow and thermal performance |
Wind Tunnel Simulation | Road cars | Test aerodynamics and air traction |
Stress Analysis | Buildings | Test structural stability under excessive load |
The simulation depicts real-life conditions or environments where the product is expected to be used. For example, to test the aerodynamics of a road car, CAE will turn to wind tunnel simulation to see how the air affects traction; to test how a building withstands excessive load, an engineer can run a stress analysis.
RELATED: Using Computer-Aided Engineering (CAE) and design services for product innovation
How it works
There are three stages of CAE:
- Pre-processing: engineers build a 3D model of the system (or product to be tested) and design the required physical effects.
- Analysis (solving): engineers run the simulation, and the model is exposed to the physical effects in a digital environment.
- Post-processing: the result of the analysis is presented for review.
CAE software can generate digital objects to represent real-world forces such as heat, vibration, electromagnetic, snow, flood, and storms depending on the type of analysis. The accuracy of the analysis result entirely depends on how precisely the engineers model the system and the virtual environment.
RELATED: The benefits of using design simulation at your company
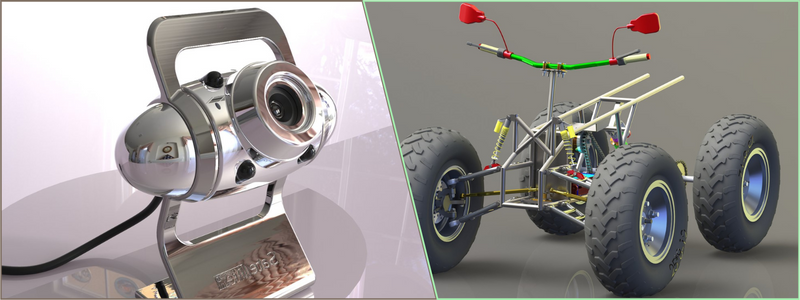
Running a CAE simulation for complex geometries is hardware-demanding, and this means CAE requires an extensive amount of computational power, which is a big hurdle for small companies. The good thing is that sophisticated IT infrastructure like cloud computing makes it easier and more affordable for startups to access CAE without heavy financial investment. Freelance engineering design services also specialize in CAE analysis, offering their services at competitive rates.
Advantages of CAE engineering services
The most significant advantage of CAE is that everything is done on screen. CAE is more efficient and requires fewer resources (i.e., time and money) than building and testing a physical prototype. Physical manufacturing prototyping design services are necessary within the design process of any product, but the digital version reduces the urgency for a rapid prototype. The advantage subsequently lowers the production and development costs.
Another massive benefit is identifying design mistakes early in product development. Just because a product looks great as a 3D model in CAD does not always mean the product will perform and function as intended. You need CAE to detect potential flaws and make revisions before product development advances. The revised model can be tested and analyzed repeatedly using different parameters to see if the product still has room for improvement.
RELATED: CAD vs. CAE: What stage of product development is your business in
The simulation is a string of computer codes that can test multiple products of the same category. For example, a company can use the same wind tunnel simulation to analyze the aerodynamics of different cars regardless of design; since the engine components are subjected to extreme temperatures, the company may also take advantage of a similar thermal analysis.
Regardless of the analysis, CAE affects how a company designs a product. Product designers and engineers use CAE to verify that the final product meets durability, performance, energy usage, and functionality requirements. The analysis demonstrates that a product, assembly, or components will fail to function. The company will then improve the design to prevent the same failures from happening in a real-life scenario.
RELATED: Finite element analysis costs, consulting company rates & engineering services pricing
Applications
CAE has been around for years and has undergone significant advances since it first emerged. Over the last decade, CAE has established a strong reputation as a reliable design verification tool in many industries, including automotive, infrastructure, consumer products, and electronics. Despite the modernization and rapid development of computing hardware to increase accuracy, CAE still is not a complete replacement for physical prototype testing. The analysis results are, in essence, an educated guess at how a product performs under stress. A physical prototype is still necessary to define the actual boundary conditions and level of exposure to the elements.
CAE simulation is considered wasteful for sophisticated products like aircraft and smart systems (e.g., smart homes or smart cars). First, the products are made of composite materials, making it difficult to define the correct parameters for setting accurate boundary conditions. Second, a complex product will require advanced analyses (including each system and component). With CAE, the cost and the computational power requirements are equally high. However, CAE is a dependable tool to explore how a product will perform before production begins.
RELATED: Product simulation and analysis: why it’s worthwhile
Summary
Computer-aided engineering (CAE) is a transformative technology that enhances product design and addresses engineering challenges through digital simulation. By enabling virtual testing and design validation, CAE eliminates the need for physical prototypes, leading to significant time and cost savings. CAE engineers in the United States earn a median salary of $70,000 annually and oversee various simulations, including thermal analysis, finite element analysis (FEA), and computational fluid dynamics (CFD). Project costs vary based on complexity and engineer qualifications.
RELATED: Engineering and product design advice for mass manufacturing services
The CAE process involves three stages: pre-processing, where a detailed 3D model is created; analysis, where the model undergoes virtual simulation; and post-processing, where the results are reviewed and interpreted. With advancements in cloud computing, CAE has become increasingly accessible and affordable. Its benefits include early detection of design flaws and reduced production costs. Though not a replacement for physical testing, CAE provides valuable insights and is widely used across automotive, consumer products, and electronics industries.
How Cad Crowd can assist
Cad Crowd provides expert CAE services for businesses seeking design optimization and engineering solutions. Our experienced engineers utilize CAE to deliver high-quality results tailored to your project’s needs. To get started and receive a project quote, request a free quote for CAE services from Cad Crowd today!