This post defines engineering for manufacturing or EFM for new products at a prototype design services firm. Engineering for manufacturing or manufacturing engineering is how things are made efficiently, effectively, and economically.
Almost everything you interact with is the result of manufacturing — from the clothes you wear to the device you use to read this article. Everything around you is the product of a team of professionals such as designers, technicians, and engineers, and manufacturing engineers are essential members of these power teams.
Table of Contents
- What is engineering for manufacturing (EFM)?
- What makes engineering for manufacturing unique?
- History of engineering for manufacturing
- What’s involved in the engineering for the manufacturing process?
- Roles and responsibilities of a manufacturing engineer
- Why work with an engineering for manufacturing (EFM) company?
- Conclusion
- How Cad Crowd can help
What is engineering for manufacturing (EFM)?
Engineering for Manufacturing (EFM) involves designing processes to create high-quality products. Manufacturing engineers will design production facilities and suggest equipment like robotics, sorting equipment, welders, and lasers to get the task done.
Manufacturing engineers balance the manufacturing process and budget to develop a profit-generating product. They must stay knowledgeable of technological options while considering the long-term plan for manufacturing facilities to continue working flexibly and efficiently for the years to come.
A manufacturing engineer can be hired to improve or upgrade an existing facility and enhance quality control or operating efficiency through new procedures, equipment, or software. Depending on their specialty, manufacturing engineers may also oversee an existing facility, robots, or workers assembling parts. They may assess how upgrading the software of older equipment will affect the current production cycles.
Manufacturing engineering and industrial engineering are two fields that are frequently mistaken for one another. An industrial engineer mainly focuses on how machines and people work together and strive to streamline processes to boost efficiency. On the other hand, manufacturing engineers are more involved with identifying the best machinery and equipment required to develop a system or product.
RELATED: What Engineering for Manufacturing is and How it Helps Product Design Companies
What makes engineering for manufacturing unique?
Manufacturing engineers consider how equipment and the production staff can work together to develop the final product. These professionals can work in industries that create outcomes and can design a manufacturing facility that makes something as small as an eraser or even as large as a space rocket. They may also work in manufacturing parts used in other products, like a rear-view mirror for a car, or larger projects, such as assembling an entire vehicle.
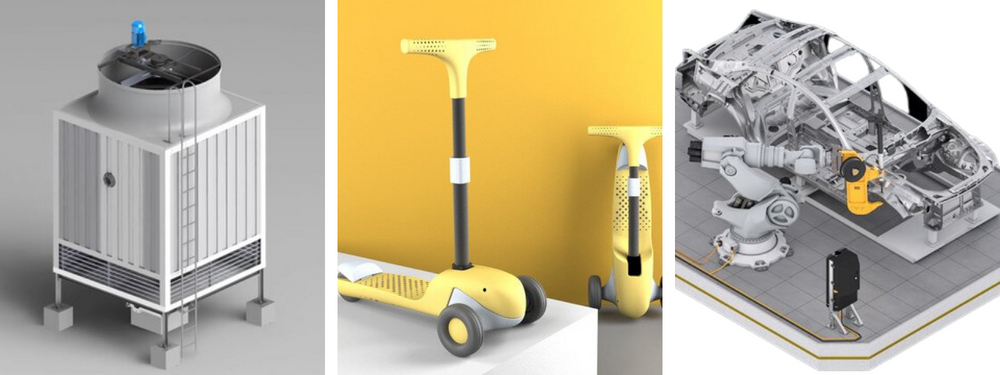
History of engineering for manufacturing
The engineering function for manufacturing traditionally plans factory layouts and organizes efficient assembly lines. Engineers design processes and source equipment to maximize efficiency within budgets and product requirements.
Before the Industrial Revolution, artisans handcrafted most products. This inefficient method struggled to meet large-scale production demands. Organized assembly lines transformed manufacturing by coordinating workers and machines, speeding production and increasing profits.
Portsmouth Block Mills provided an early UK example of continuous assembly processes, developing parts for Royal Navy rigging blocks. Ford Motor Company notably revolutionized automobile manufacturing in 1913 by introducing an assembly line that reduced Model T Ford production time to 93 minutes in 45 steps. This efficient process also created more jobs and reduced labor.
Over time, assembly lines evolved, incorporating sensors, automation, and robots to accelerate production further.
What’s involved in the engineering for the manufacturing process?
The example of Smartphone production detailed below is an excellent example of the EFM process.
1. Product design
The smartphone’s design is initially developed given customers’ needs using CAD drawings and models of assemblies, components, and subsystems. The manufacturing engineer takes part in the process almost right from the start, pointing out the different ways to improve the design further to make later fabrication faster, easier, and cheaper. Moreover, the manufacturing engineer can identify and correct severe issues in manufacturability before the start of production.
2. System and process design
After designing the smartphone’s parts, the manufacturing engineer will lead the development of the processes used for fabricating every product component. Experience with manufacturing processes like injection molding, casting, forming, welding, and machining enables manufacturing engineers to identify essential parameters and steps for producing quality parts efficiently.
In addition, the supply chain for outsourced components and raw materials is established as well. The manufacturing engineer determines the number of required workers and machines and plans the layout of the factory for efficient and orderly production.
3. Quality control to project management
Once the production starts, the manufacturing engineer will continue measuring and analyzing the manufacturing system and keep things running on schedule smoothly. The manufacturing engineer will also map out and implement enhancements that will cut costs and lead time while improving the quality with the help of tools such as robotics and automation, information systems, and computer simulations.
Principle-based philosophies such as Six Sigma, Total Quality Management, and Lean Manufacturing help the manufacturing engineer make tangible improvements to individual product lines, processes, factories, and entire companies. The work of a manufacturing engineer is never done, proving their essential role in the production process.
RELATED: Manufacturing Services and Tool Design Engineering
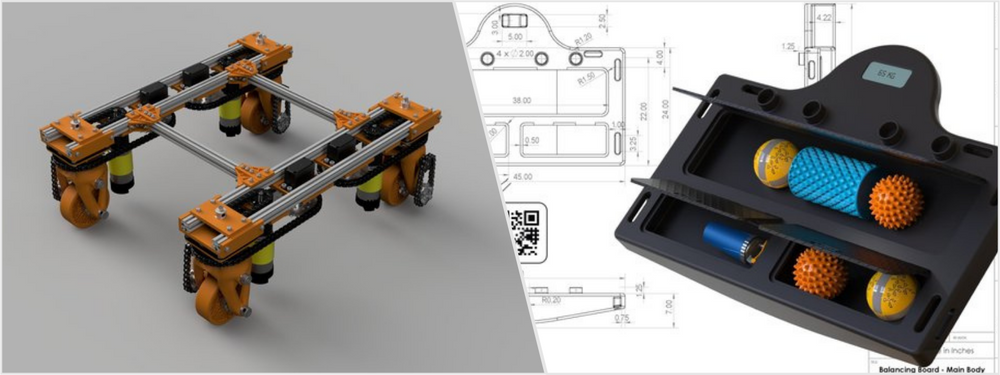
Roles and responsibilities of a manufacturing engineer
Engineering for manufacturing requires the ability to plan the manufacturing processes. These experts may spend a few hours researching new machines or processes or participate in meetings to discuss the best approach to build a particular product and project costs according to different systems.
A manufacturing engineer may also travel to observe the equipment used in other factories or approve progress at a developing manufacturing facility. They may also use technology to test suggested manufacturing layouts to make virtual changes before crafting the working version.
Manufacturing engineers also work with other teams and typically work 40 hours per week. However, they may need additional hours if a new product is under development or new equipment is being assessed. These extra hours are expected to solve an urgent concern if a breakdown occurs.
Other tasks of a manufacturing engineer include the following:
- Be involved in manufacturing, from planning to the finished product’s packaging.
- Examine flow and the manufacturing equipment’s process, searching for means to reduce costs, improve turnaround, and streamline production.
- Understand systems and methods to develop a product cost-effectively and efficiently to give the final product a marketing edge.
- Work with the prototypes often made electronically with computers to plan the final manufacturing
process.
- Different tools like numerical and programmable controllers, vision systems, and robots are utilized to fine-tune assembly, packaging, and shipping facilities.
Why work with an engineering for manufacturing (EFM) company?
Clients can look for the solutions they need with engineering for manufacturing companies that provide various services. Engineering for manufacturing (EFM) company can offer solutions, such as:
- Mechanical and electrical engineering
- Marketing
- All kinds of turnkey jobs
- Patent and product research
- Product analysis and simulation
- Product certification and testing
Corporations, partnerships, and individuals may discover that more profits await them if they outsource all or some of their production needs to engineering for manufacturing companies. Since the return on investment is critical for the management, they must always know when to replace or repair equipment. The cost analysis includes a return on outsourcing and even replacement or repair.
RELATED: An OEM’s Guide to Product Design and Manufacturing Prototypes
Conclusion
Engineering for manufacturing companies works to develop various products, from cup holders to Bluetooth headsets, car seats, boat seating systems, and so much more. Manufacturing engineers identify the best machinery and equipment to develop a plan or product. Furthermore, clients will discover potential savings when outsourcing production needs to engineering for a manufacturing company.
How Cad Crowd can help
Explore the benefits of Engineering for Manufacturing (EFM) for your new product prototypes with our design services. Seize the opportunity to transform your concepts into real solutions effectively.
Experience the expert assistance of our CAD Crowd team through the prototype design process. Begin your journey by requesting a free quote to try our services!