This post explains more about 3D meshing in CAD and how it benefits companies and firms. 3D modeling technology has evolved, and using traditional pen and paper is almost a rare and even obsolete practice. Aside from how neat it is compared to others, digital modeling, specifically 3D modeling services, allows users to practice and take advantage of different methods. But despite their differences, 3D modeling still shares the same goal: to simulate things to make them as realistic as possible.
Using essential tools and resources, what was once a blank screen can now showcase fully modeled terrains inspired by actual sceneries. From video games to animated films, learning to develop 3D models plays an important part in entertainment. As expected, these are only some areas where 3D excels because even new car models and technological blueprints are presented as 3D models. 3D modeling services involve many types, and one of these is mesh modeling.
Table of Contents
RELATED: 3D Modeling techniques used in video games
What is meshing in CAD?
Mesh modeling, or polygonal modeling, is under 3D modeling and takes shapes as multidimensional figures. Unfortunately, meshing in CAD doesn’t get as much spotlight because of its simplistic details. Mesh models can be converted into surface or solid models. Since the mesh works as the outline of the 3D model, 3D modeling design artists can easily manipulate it to assume various forms. It makes the mesh look like a blank linework waiting to be filled in with color later.
Parts of mesh 3D modeling
Meshes are among the most crucial aspects of 3D modeling. A mesh 3D model is any object that an artist can manipulate to form various forms and shapes. When developing a mesh, the first step is usually to create the shape. You can consider it as devising a wireframe or an outline that you can fill in later with texture and color. It will make sense if you consider it a way to fill something in on paper by drawing around it. 3D mesh comprises three dimensions, so you can expect its components to differ from the basic 2D shapes.
Today’s software can use character models for recreating expressive facial characteristics. On the other hand, three-sided models have been found to excel better in modern gaming models. 3D mesh models are essentially made up of three primary elements: edges, faces, and vertices. You will only notice the level of detail in your model in modeling mesh after you have realized how low the polycount is.
RELATED: How to evaluate the quality of a 3D model for parts & products
If you haven’t guessed yet, the polycount is connected directly to the faces of the 3D model since it indicates the number of polycounts accumulated in the figure. The 3D mesh model details will be vaguer if the polycount is lower. As far as the edges are concerned, these are the connected points forming a figure. Points or vertices promote mobility to allow the user to manipulate the shape.
Different types of meshes in CAD
Meshes are the collection of interconnected edges, faces, and points. Meshes in CAD and 3D modeling come in many types, namely NURBS, polygonal mesh, and subdivision surface mesh, called “subd.”
NURBS mesh
Non-Uniform Rational B-Splines or NURBS are typically used to form curves that are impossible to express as other types of curves. It is also possible to convert NURBS into polygons if and as needed. NURBS meshes are meshes containing curves. These meshes can be made using 3D modeling software instead of basic hard surface modeling software.
RELATED: What is 3D rigging and how is it used for 3D character animation?
Polygonal mesh
A polygonal mesh in 3D modeling consists of faces in polygon form. These are often triangles or four-sided shapes known as quads. However, these faces can also be in the form of hexagons. A polygonal mesh made up of the most basic form of a mesh, a triangle, is said to take on a triangular topology. If squares make up a polygonal mesh rather than triangles, it is referred to as something with a square topology. If the polygonal mesh consists of polygons with more than four sides, it takes on an angular topology.
There are some instances when quads or square topology is better than triangles or triangular topology. If quads make up a polygonal mesh, its number of edges will be even. It means the surface must be flat when used for 3D printing services for any given plane to retain quality and accuracy. If quads make up a mesh, animating will be a better option. Square topology is your best option for 3D model characters.
RELATED: 5 3D modeling techniques for freelance CAD designers
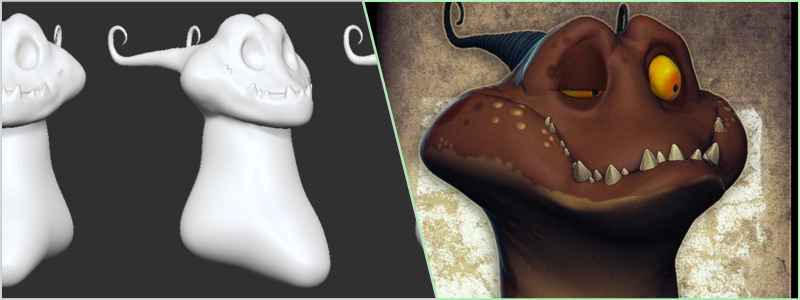
Subdivision surface mesh
Subdivision surface mesh is composed of polygons on the object’s surface. The only difference from polygonal mesh is that the polygons are not flat and are composed of several quads. A particular amount of curving or distortion on the surface plane makes achieving high-quality and accurate 3D prints more difficult. You may wonder if your 3D model should use subdivision surface mesh or polygonal mesh, there are several factors you must consider:
Can your 3D printer print the details on the polygonal mesh, like the corners or curves? If not, is it best to stick to quads? How detailed do you need or want your model to be? If your model must be highly detailed and polycount is the least of your worries, you might consider opting for a triangular typology. What is the primary purpose of your modeling project? If it is for printing purposes, a subdivision surface mesh is your better option? Alternatively, you might want to go with quads if they will be used for animation.
RELATED: 12 Must-know 3D modeling terms
How are mesh models made?
Now that you know what meshing in CAD is centered around, it is time to learn how mesh models are designed and created.
1. Begin with the base
You have to take note of the connected parts before you begin your calculations, and failure to do so might result in a deformed model. Rather than diving straight into making your mold, you must start with mold details first. You must take your time and ensure it doesn’t lose shape. It is also a must that you don’t smooth your mesh model right after you make it, or else you will only prevent the decent performance of the model. Note that if the polycount is higher, it will more likely impact its performance. It will also add further to the complexity, slowing it down. You can start adding details after you are finished modeling the mesh.
2. Pay attention to one face at a time
It is not your goal to make your mesh turn out flawlessly smooth. Aside from making it more complex than it already is, just a single wrong move can quickly ruin any progress you make. Always take your time in refining every face of your mesh. Alternatively, if you are not keen on refining every component of the mesh model, you can also opt to refine only the individual faces requiring more focus on detailed modeling.
RELATED: 3D Hard surface modeling versus organic modeling
3. Take advantage of gizmos
Artists will only survive in the field with their tools and medium; this rule applies to 3D character modeling professionals. Even if 3D models are in a virtual setting, it doesn’t make their modifications less challenging. This is why you will need gizmos or tools specially designed to cater to specific demands and apply these to your model, like giving it a scale, rotating, or moving.
4. Look at every angle
3D mesh models have several dimensions, so it only makes sense to look at and check your creations from different angles to appreciate them. But more than appreciation alone, you should also use this chance to inspect if the faces of the model have any abnormalities. This way, you won’t have a hard time doing the necessary refining later.
RELATED: How much does a 3D character modeling service cost for 3D artists & firms?
The bottom line
Art is an enduring and integral aspect of life; sometimes, you might find it in the most unexpected places. But similar to other art processes, it often takes some time to identify the right method for you, and it even takes longer to perfect the craft. The best way to embark on your 3D modeling journey is to be familiar with mesh modeling. Or better yet, you can follow the footsteps of other companies and firms and take advantage of the expertise and knowledge of meshing freelancers who can gather your ideas and form something solid and visible out of them.
How Cad Crowd can help
At Cad Crowd, we have an expert collection of top-tier 3D modeling services available to help you with your project. Whatever you need modeled, rest assured that we can help. Get a free quote today.