For the post today, you will learn about what to consider when developing the enclosure design of your company’s electronic products. When developing electronic products, the enclosure design plays a crucial role in ensuring the product’s success.
The enclosure is more than just a protective shell; it’s a critical component that influences the product’s durability, usability, aesthetics, and overall market appeal. A well-designed enclosure can make the difference between a product that thrives in the market and one that struggles to gain traction.
Cad Crowd is an industry leader in connecting engineering and design companies with the best designers and engineers. Here are key considerations when looking for the best electronic enclosure design service to develop your company’s electronic products to ensure that you will be getting the results you’re after.
🚀 Table of contents
Material selection
The choice of materials for the enclosure is foundational. The material must provide adequate protection for the internal components while also meeting aesthetic and ergonomic requirements. Common materials used by product design companies include:
- Plastics
Widely used for their versatility, plastics like ABS, polycarbonate, and polypropylene offer good impact resistance, flexibility in design, and cost-effectiveness. However, considerations around thermal management and electromagnetic interference (EMI) shielding must be addressed when using plastics.
- Metals
Aluminum and stainless steel are two major types of metals that are popular for their strength, durability, and superior heat dissipation properties. They are often used in products that require robust protection against external forces or that generate significant heat during operation.
- Composites
Composite materials combine the benefits of plastics and metals, offering strength, lightness, and thermal management properties. They are ideal for products that require a balance of strength and weight.
When selecting materials, engineering firms consider factors such as the product’s operating environment, regulatory requirements, and cost constraints. For example, a product intended for outdoor use may require UV-resistant materials, while a medical device may need to meet strict regulatory standards for biocompatibility.
RELATED: What are the costs for new hardware product design, PCB prototyping rates, and services pricing?
Thermal management
Effective thermal management is crucial to ensure the reliable operation of electronic components. Excessive heat can lead to component failure, reduced performance, and shortened product lifespan. The enclosure design must facilitate heat dissipation through natural or forced convection, conduction, or radiation.
- Heat sinks and vents
Incorporating heat sinks, vents, and fans into the enclosure can enhance airflow and heat dissipation. The placement of these features should be carefully planned to avoid dust ingress or moisture, which could compromise the product’s performance.
- Material conductivity
The material’s thermal conductivity plays a vital role in heat management. Metals like aluminum are excellent conductors of heat and can help in dissipating heat from internal components. Plastics, on the other hand, are poor conductors and may require additional thermal management solutions.
- Simulation and testing
Utilizing thermal simulation tools during the design phase can help predict how the enclosure will manage heat. This allows for the optimization of design features by design engineering professionals before moving into the prototyping stage, saving time and costs.
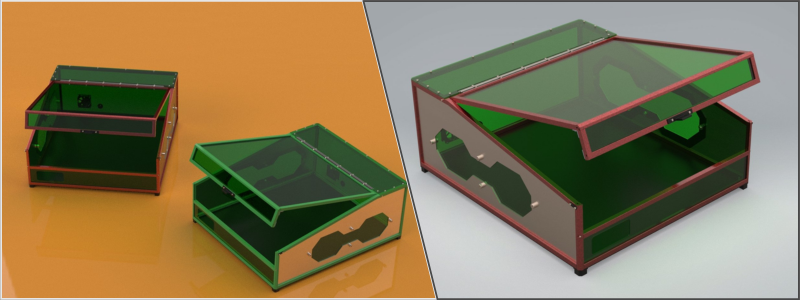
Ergonomics and usability
The enclosure design should enhance the product’s usability and user experience. Ergonomics is a critical consideration, especially for handheld or wearable devices. The concept design service should take into account how the product will be used, who will use it, and under what conditions.
- Form factor
The size, shape, and weight of the enclosure should be designed for comfort and ease of use. For example, a handheld device should have a form factor that fits comfortably in the user’s hand, with controls that are easy to reach and operate.
- Accessibility
Consider how the enclosure will be assembled and disassembled, particularly for products that require regular maintenance or battery replacement. Features like snap-fits, screws, and latches should be designed for easy access without compromising the enclosure’s integrity.
- User interface integration
If the product includes buttons, screens, or other interface elements, the enclosure must be designed to accommodate these components seamlessly. The placement and tactile feedback of buttons, as well as the visibility and durability of screens, should be carefully considered.
RELATED: Guide to new electronics prototyping for hardware startups & design companies
Aesthetics and branding
A well-designed enclosure contributes significantly to the product’s visual appeal and brand identity. The enclosure is often the first thing a customer notices, so it should reflect the brand’s values and target market.
- Design language
The enclosure design should align with the brand’s design language, whether that’s sleek and modern, rugged and industrial, or minimalist and elegant. Consistency in design across different products helps reinforce brand recognition and loyalty, as any consumer product expert designers would attest.
- Color and finish
The choice of color and finish can affect the product’s perception. Matte finishes, glossy surfaces, or textured coatings can all convey different messages about the product’s quality and intended use. Color choices should also consider the product’s use environment; for instance, bright colors might be preferred for safety equipment to enhance visibility.
- Custom branding
Incorporating logos, trademarks, or other branding elements into the enclosure design can enhance the product’s marketability. Techniques such as laser engraving, pad printing, or embossing can be used to add these elements to the enclosure.
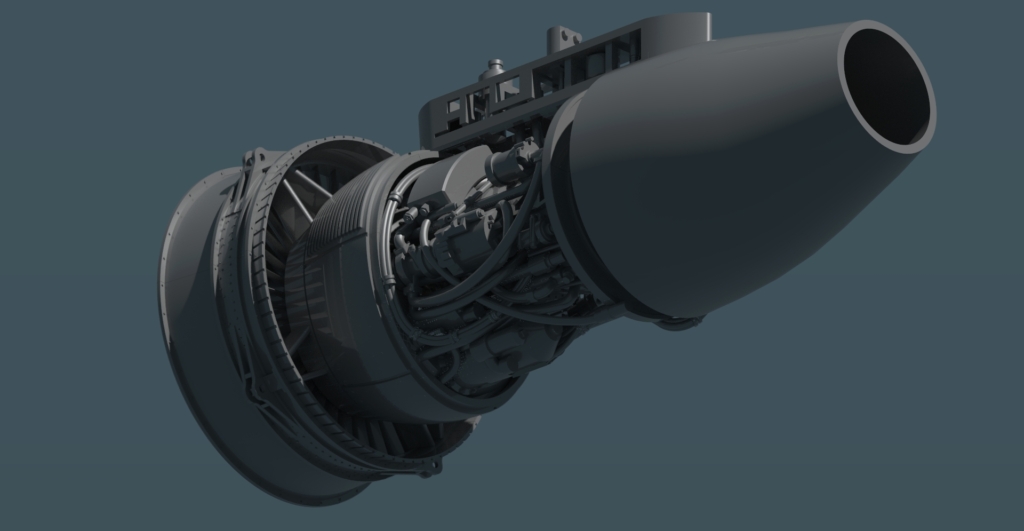
Durability and protection
The enclosure must protect the internal components from environmental factors such as dust, moisture, and physical impact. Durability is particularly important for products used in harsh environments, such as industrial or outdoor settings.
- Ingress protection (IP) rating
The IP rating system measures the enclosure’s ability to resist dust and water ingress. Products intended for outdoor or industrial use may require a high IP rating to ensure they are protected from environmental hazards.
- Shock and vibration resistance
The enclosure should be designed to absorb shock and vibration, which can damage sensitive electronic components. Materials like rubber or foam padding can be used inside the enclosure to cushion components and reduce the impact of shocks.
- Chemical resistance
In some applications, the enclosure may be exposed to chemicals or corrosive substances. In such cases, the engineering firm should determine the material chosen for its chemical resistance properties to prevent degradation over time.
RELATED: How to develop a new electronic hardware prototype & products for your company
Regulatory compliance
Electronic products are subject to various regulatory standards, depending on their intended use and market. The product design firm must comply with these regulations to ensure the product can be legally sold and used.
- EMI/EMC compliance
The enclosure should be designed to minimize electromagnetic interference or EMI and ensure electromagnetic compatibility or EMC. This often involves the use of shielding materials, grounding, and careful placement of components within the enclosure.
- Safety standards
Depending on the product’s application, it may need to comply with safety standards such as UL Underwriters Laboratories, CE, or Conformité Européenne. These standards often include requirements for the enclosure’s material, design, and labeling.
- Environmental regulations
Products sold in certain markets may need to comply with environmental regulations, such as RoHS or Restriction of Hazardous Substances or WEEE or Waste Electrical and Electronic Equipment. These regulations may limit the use of certain materials or require specific labeling and recycling instructions.
Manufacturability and cost efficiency
The enclosure design should be optimized for manufacturability to ensure it can be produced efficiently and cost-effectively. Consideration should be given to the manufacturing process, tooling costs, and material waste.
- Design for manufacturing (DFM)
DFM principles should be applied during the design phase to simplify the manufacturing process. This includes minimizing the number of parts, using standard components where possible, and designing for easy assembly.
- Tooling and production costs
The choice of materials and manufacturing processes will impact the tooling and production costs. For example, injection molding requires an upfront investment in tooling but is cost-effective for high-volume production. CNC machining, on the other hand, maybe more suitable for low-volume or custom production runs.
- Material waste
The enclosure design should aim to minimize material waste during production. This can be achieved by optimizing the design for the chosen manufacturing process, such as minimizing the number of cuts or using nesting techniques to reduce material waste in sheet metal fabrication.

Prototyping and testing
Before moving to full-scale production, it’s essential to prototype and test the enclosure design. Prototyping allows for the validation of design assumptions, identification of potential issues, and refinement of the design.
- 3D printing
3D printing services are excellent tools for rapid prototyping, allowing for the creation of physical models to test fit, form, and function. This can be done quickly and cost-effectively, enabling iterative design improvements.
- Functional testing
The prototype should undergo functional testing to ensure it meets all performance requirements. This includes testing for thermal management, durability, ingress protection, and user interface functionality.
- User testing
Involving end-users in the testing process can provide valuable feedback on the product’s usability and ergonomics. This feedback can be used to make design adjustments before finalizing the enclosure design.
The enclosure design of your company’s electronic products is a critical factor in determining their success. Through a proper and careful consideration of material selection, thermal management, ergonomics, aesthetics, durability, regulatory compliance, manufacturability, and prototyping, you can develop enclosures that not only protect and enhance your products but also contribute to their market appeal and user satisfaction. Investing time and resources in the enclosure design process will pay off in the form of a more robust, user-friendly, and competitive product.
How Cad Crowd can help
Do you want to take your enclosure design to a whole new level this time? Don’t hesitate to get in touch with Cad Crowd today to request a quote and find out how we can connect you with expert designers who can help you create the perfect enclosure for your electronic products. We have over 14 years of experience as an industry leader that can help you find the right talent for your project today. Contact us for a free quote.