Perhaps the first act for a company in developing a new product or solution is the creation of a prototype. Prototyping enables businesses to test their ideas, refine design flaws, and assess the functionality of their product before committing to mass production.
The two most common methods for prototyping are injection molding and 3D printing. Each has its own merits and demerits depending on what a company needs, the material or materials required, and the outcome desired. Knowing which one to use is essential to make a company operate efficiently and without excess costs when bringing a product into the market.
Choosing between injection molding and 3D printing services may be difficult at first. However, once you understand their respective benefits, you will find that both are a must-have for your prototype design. Cad Crowd can connect you with the best names in these two fields, and to help you understand your options, let’s take a deep dive into each method and how it fits your goals.
🚀 Table of contents
Injection molding and 3D printing: understanding the basics
Before elaborating on the applications of each technology, it is important to understand the fundamental difference between injection molding and 3D printing.
Injection molding: This process also involves the creation of a mold; often, it is made of metal, and molten plastic is injected at high pressure. After cooling and removal, a solid part is formed. Ideally, injection molding is suited to make large volumes of parts with consistent, repeatable quality. These types of operations are widely used in manufacturing industries that produce plastic components.
3D printing: This is just additive manufacturing. Basically, how this works is material that gets added in layers according to a digital description. Unlike injection molding, there is no mold, and the material does not get subtracted from a solid block in order to be manufactured. In 3D printing services, complex geometries and customized parts can be engineered at relative speed, and this is an attractive choice for prototyping and small production runs.
RELATED: Comprehensive guide to SLS 3D printing services for companies
When to use injection molding
Injection molding is a proven and robust process used for many decades. Its benefits materialize if the following conditions are fulfilled during the prototyping designing phase:
Complex geometries with low tolerances
This process suits prototypes with relatively simple to moderately complex geometries. While the produced parts can have very tight tolerance, and there are some precision limits of the process, which makes it hard to use advanced geometries with complex internal features or undercuts without the development of advanced tooling, the design and injection molding manufacturing services become expensive for complex parts, which is another reason why this technique is typically applied only for the products that will be mass-produced.
Cost-efficiency at scales
Although initial setup costs for injection molding can be high due to mold creation, the cost per part is much lower with high volumes. If a company plans on making a very large production, injection molding can be a very inexpensive way to mass-produce prototypes that will eventually become part of an entire production line.
High production volumes
If your company is likely to build a prototype that needs to be produced in high quantities, injection molding is usually your better choice. This is because injection molding is established for high-volume production. Once the mold has been created, building tens of thousands or even millions of parts with very little labor and very low cost is relatively easy. This allows per-unit costs to be kept relatively very low as the quantity of units grows.
Injection molding, on the other hand, is less suitable for the few units that most prototypes would require because producing the mold is relatively expensive and has a high initial setup. In such cases, the investments companies undertake may be ahead of schedule relative to the relatively smaller costs for 3D printing.
Number of iterations or refinements needed
In cases where a prototype would undergo multiple rounds of alteration and testing, injection molding is not the best option. The process of altering a mold can be time-consuming and costly. When a prototype changes quickly, 3D printing is usually the better method. However, once a design is locked in, and the company wants to start mass production, then injection molding is the way to go.
Parts durability and material properties
Injection molding is ideal for prototyping design services looking for better durability and material properties that closely resemble the final production version. The materials used in injection molding are mostly industrial-grade plastics, which can have different additives that not only strengthen and build up the material but also make it resistant to heat and chemicals.
Injection molding will most probably be your best option if your prototype is to be substantially tested or is expected to closely resemble the final product as far as its strength, elasticity, and other physical attributes are concerned. This would better approximate the material’s performance in the end product.
RELATED: 6 ways 3D printing will change the world
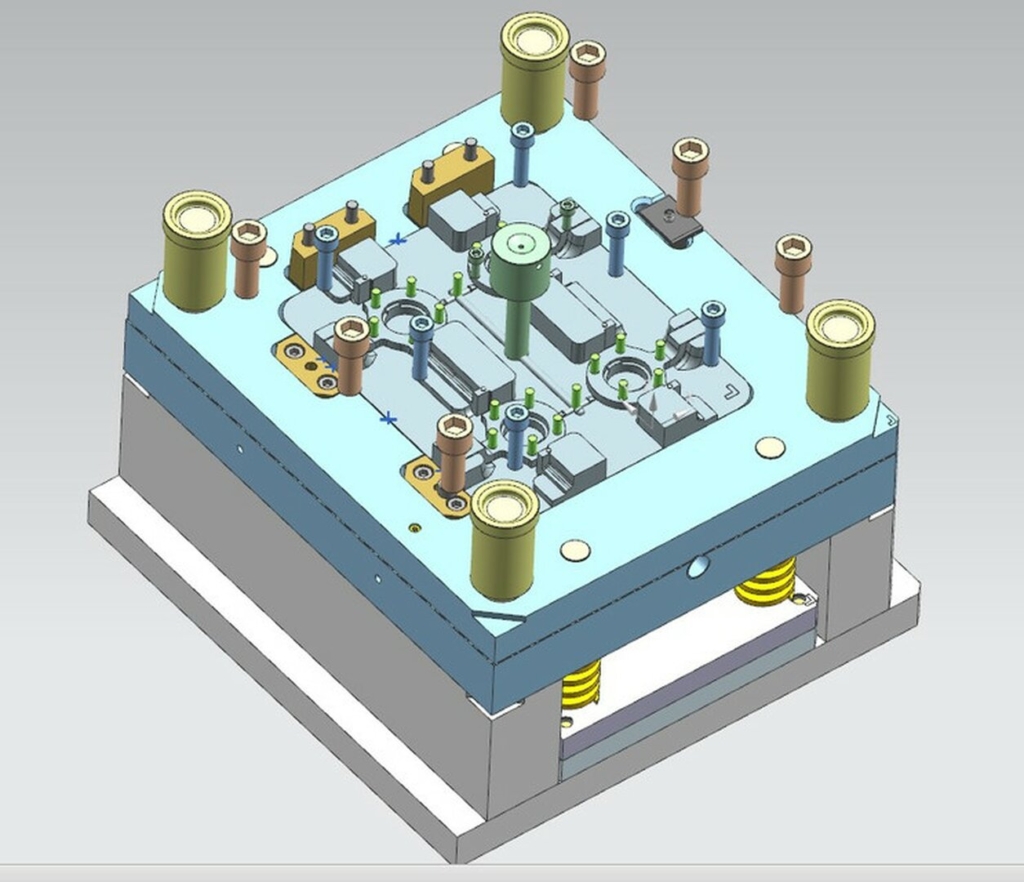
When to use 3D printing
3D printing or additive manufacturing is changing prototype betterment because this technology offers maximum flexibility at low costs and quick production of highly detailed parts. It is especially valuable at the early stages of prototype models, design iterations, or testing.
- Complex Geometries and Customization
One of the major advantages of 3D printing services is that it can easily create parts of highly complex geometries, especially parts with deep internal features, lattices, or overhanging structures that cannot be easily or successfully done through injection molding. It more often requires additional tooling and adjustments to such intricate designs.
Whether you design with intricate part shape or complex internal cavities or unique material combinations, 3D printing can produce prototypes that would be impossible or too expensive to make with injection molding. - Iterative Design Process
But 3D printing really shines in environments where rapid iteration is required. If a company is not yet finalized its product and needs to test features or materials in different configurations, this is the way to go. Changes can easily be made in the digital model and a new prototype printed right away. Changing an injection mold is an enormously more expensive and time-consuming process.
Third, for concepts that are in the early phases of design or for evaluating several design ideas, 3D printing facilitates teams to rapidly shift between iterations based on testing the designs in the real world. - Lower Setup Costs and Flexibility
One of the strong points of 3D printing is that setup costs are incomparably lower than those for injection molding. With no molds or other specialized tooling required, one would save money and remain flexible. It is perfect for a small business, startup, or any venture testing a few different ideas without committing a large budget upfront.
Easy changes to the digital model without a premium being charged for retooling or mold alteration: this is also one of the strengths with 3D printing in that changes are made continually during design cycles. - Low Production Volumes
When the quantity to be tested or validated is small, it is very much less costly than injection molding. This is because it will take a lot of money to get the mold using injection molding. Besides, injection molding may not even be appropriate for producing little quantities. 3D printing will eliminate the presence of the molds and will require a very much lesser amount as an initial investment.
Customized or single-copy prototyping is also made easier by 3D printing. With your product needing bespoke changes, 3D printing can easily adapt to those needs without expensive tooling. - Rapid Prototyping
If the company feels it needs a rapid prototype, then 3D printing is the answer. While a traditional injection molding process does indeed require lead times to create molds and manufacture, 3D printing turns everything around on its head with quicker turnaround time. Using an overnight machine, prototypes can be completed overnight, meaning quick feedback and iterative improvements.
Early stage development or when prototyping multiple iterations of a design, the fastest path from concept to a physical prototype is 3D printing. This speed is really valuable to startups or business working within tight timelines.
RELATED: Top applications of thermoplastic polyurethane (TPU) for 3D printing companies
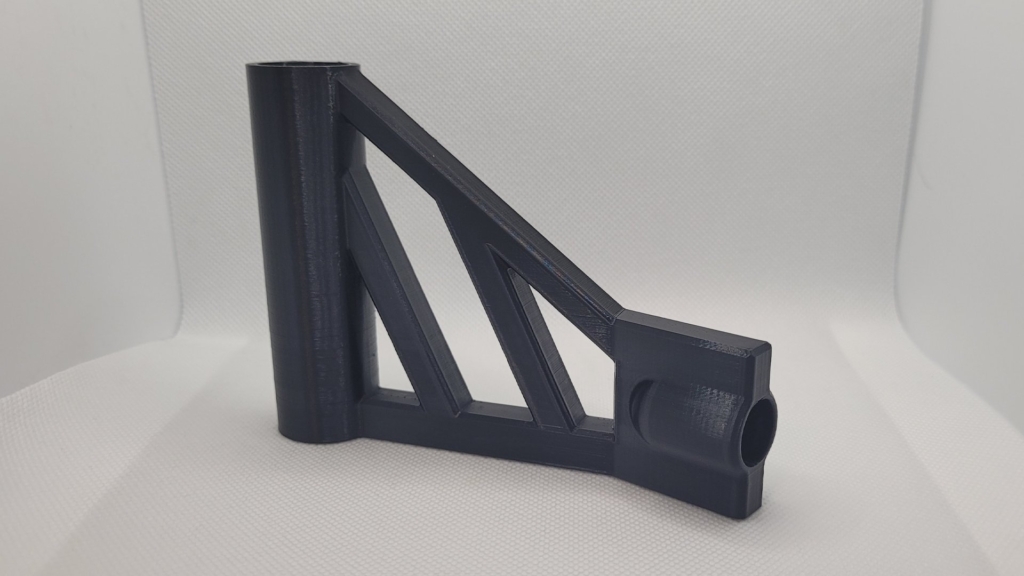
Injection molding vs. 3D printing for prototyping
Finally, the choice between injection molding services and 3D printing is determined by your specific prototype requirements and how advanced you are in product development. To recap:
Injection Moulding should be chosen if: You need high volume production. You require heavy-duty materials. Your product design calls for high accuracy. Your design is nearly finalized, and you now want to produce in high quantity.
Choose 3D Printing if: Rapid prototyping, low-volume production, and complex geometries or flexible iterations are necessary when having the lowest initial costs.
Each of these techniques has specific benefits that can be asserted at various stages of the product life cycle. It is also worthwhile to note that some organizations would be interested in using a hybrid approach—that is, applying 3D printing in early stage prototyping and design evolution and subsequently switching to injection molding for mass production once the design is ready.
The right choice would depend upon understanding what your company really needs, would budget, and actually wants in terms of timeline for the prototype. With this, the appropriate prototyping method will help you streamline your product development process while avoiding unnecessary costs. Thus, your company will be well-positioned for success and will be ready for mass production.
How Cad Crowd can help
Now that you understand how both services differ, you can look no further than Cad Crowd to help you find the professional that fits your project. Our experience and network gained from working with firms that used both services can help make you plan a strategy that’ll have someone you can trust working on your team in no time. Request a free quote today.