AM, or additive layer manufacturing services, is the new evolution in industrial production methods. Indeed, commonly called 3D printing, it is a new technology that has the capability of producing three-dimensional objects through computer-controlled process with deposition of materials in layers. This paper takes readers deep into the world of additive manufacturing, discussing how it works, processes, advantages, materials, applications, and future prospects in different industries.
🚀 Table of contents
- How does additive manufacturing work?
- The process
- Additive manufacturing processes
- Additive manufacturing technologies
- Benefits of additive manufacturing
- Factors that affect processing time
- Materials used for additive manufacturing
- Applications of additive manufacturing
- Additive manufacturing for the future
- Wrapping it up
- How Cad Crowd can help
How does additive manufacturing work?
As simple as it gets, additive manufacturing uses CAD or 3D object scanning to create geometrically exact objects. Compared to conventional manufacturing, which is generally subtractive—the removal of material from a solid block—additive manufacturing adds material layer by layer. This not only saves material but also enables the creation of geometries that cannot be built using most traditional manufacturing methods.
The process
- Design creation: The journey begins with a digital model created with CAD software, which will be the base of the object to be printed.
- Slicing: The digital model is broken down into very thin horizontal layers by slicing software and is interpreted for the 3D printer.
- Printing: With the printer, the material is deposited layer by layer, which builds up to the eventual object. Each layer bonds with the previous one until forming a final shape.
- Post-processing: After printing, the printed object may need post-processing, which includes cleansing, curing, finishing, or other operations to attain the desired surface quality and characteristics.
This process depicts the openness of additive manufacturing; it allows for rapid prototyping services, designing, and economical runs.
RELATED: Unleashing potential: Complete comprehensive guide to SLS 3D printing services for companies
Additive manufacturing processes
There are a lot of additive manufacturing techniques, and each one has its own standards and application. Among all the techniques used, the following is the list of mostly used techniques:
1. Binder Jetting
In binder jetting, a 3D printing head follows paths along the X, Y, and Z axes to deposit alternating layers of powdered material and a liquid binder. With this process, a strong structure is formed because the adhesive sticks the powder particles together. Binder jetting is extremely rapid and allows for large parts with very little waste of material.
2. Directed energy deposition (DED)
Directed energy deposition has been accessed through a focused energy source such as the laser or electron beam that melts the material. Such a process is capable of handling a wide variety of materials, from metals to ceramics to polymers. Wire or powdered feedstock, which is delivered by a movable arm, is melted within the melting zone; this makes it accessible for creating intricate geometries.
3. Material extrusion
The most commonly used AM process is material extrusion. It involves spooled polymers that melt and then get pressed out through a nozzle, and the nozzle progresses horizontally as the build platform moves in a vertical motion, layering the molten material to create the desired shape. It’s very popular for home 3D printing, and it can have items with reasonable strength and detail. However, it is still a great choice for manufacturing services.
4. Powder bed fusion
Powder bed fusion encompasses a wide category of technologies, including DMLM, SLS, and EBM. In this process, the powdered material is melted selectively through laser or electron beams, thus allowing for the creation of complex parts of great accuracy. At the very end, the excessive powder is removed.
5. Sheet lamination
Sheet lamination can be further divided into laminated object manufacturing (LOM) and ultrasonic additive manufacturing (UAM). In LOM, sheets of paper or plastic are built up in layers with adhesives. In UAM, thin metal sheets are bonded using ultrasonic welding, which keeps temperature processes low and allows for multiple metals.
6. Vat polymerization
This process uses a vat of liquid photopolymer resin that is cured layer by layer with ultraviolet light. Mirrors steer the light to targeted areas, where the resin is hardened, and the object is built up incrementally. Vat polymerization is known for producing parts with high resolutions and surface finish.
7. Wire arc additive manufacturing
Named now as directed energy deposition-arc (DED-arc), this process uses arc welding power sources for the formation of three-dimensional shapes. The wire travels along a pre-programmed path that makes it feasible to deposit layer after layer uniformly and with very high accuracy. This technique often integrates robotic systems to enhance precision and speed.
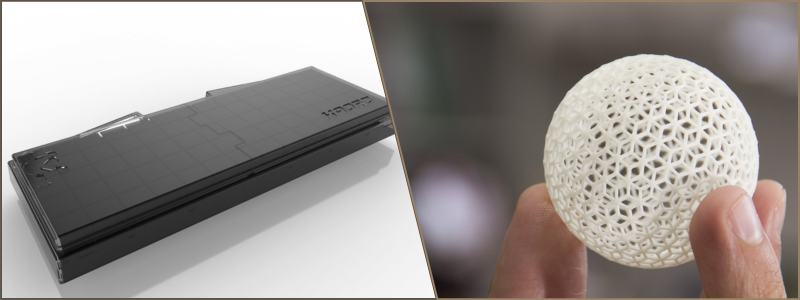
RELATED: Smart manufacturing using CAD design is the future for OEM’s
Additive manufacturing technologies
Depending upon the ways additive manufacturing design firms produce objects, there are three chief types classified as follows:
1. Sintering
This involves heating materials to near but below their melting points, causing particles to fuse together and make an overall solid structure. The most common ones in this category are Direct Metal Laser Sintering and Selective Laser Sintering, which use metal powder for DMLS, whereas SLS always uses thermoplastic powders.
2. Melting
This class melts all materials completely for the production of solid, dense parts. Examples here include direct laser metal sintering and electron beam melting. Both use laser beams and electron beams in melting layers of powder to create full-scale, solid objects.
3. Stereolithography
Stereolithography applies photopolymerization to create an object using an ultraviolet laser. It is perfect for various complex designs and high-resolution parts. The ceramic parts produced can endure extreme temperatures, which makes them fit for specific applications.
Benefits of additive manufacturing
Additive manufacturing provides a number of benefits over conventional manufacturing, and it appears to be gaining more ground across industries:
1. Least amount of material waste
AM produces much less waste compared to subtractive manufacturing techniques. Since materials are deposited layer by layer, only that which is required is used, which is particularly advantageous for expensive materials.
2. Design flexibility
One of the major advantages of additive manufacturing is the ability to produce complex geometries and bespoke parts. Designs can be altered quickly; quick prototyping is possible during the manufacturing process, and it goes without saying that rapid prototyping services use additive manufacturing a lot.
3. Shorter lead times
Additive manufacturing can bring the lead time down dramatically, meaning companies can get products to market sooner. This is particularly useful in markets where the ability to get a product to market is vital.
4. Merger of parts
AM allows for the building of parts that otherwise would be an assembly of a number of parts. It enables the production of stronger and more robust final products by minimizing assembly stages and reducing possible failure points at the same time.
5. Customization
Additive manufacturing will particularly be good at manufacturing customized products for precisely designed user needs. Perhaps no area represents this, as well as the healthcare sector, in which unique medical implants can make a significant difference in how patients recover.
RELATED: 6 ways 3D printing will change the world
Factors that affect processing time
The time required to print a part can depend on several factors:
- Part size: The more enormous the object, the longer it takes to print
- Quality settings: Generally, higher quality will take longer processing time because of increased layer resolution and detail.
- Volume of the material: The amount of material to be laid down also sets the overall time.
- Complexity: Designs that carry a lot of complexity take more time to allow proper bonding and layering.
The overall AM time might lie in the range of some minutes to days or even hours, depending on the factors stated above.
Materials used for additive manufacturing
There are various materials that can be used in additive manufacturing and differ in their properties and areas of usage for expert engineers:
1. Biochemicals
Biochemicals are also gaining acceptance, especially for health care applications comprising silicon and, calcium phosphate,e and zinc. Bio-inks based on stem cells are also of interest for potential application in tissue engineering and regenerative medicine.
2. Ceramics
Some of the common ceramics used in AM include alumina, tricalcium phosphate, and zirconia; they are suitable for those applications with a requirement for high strength and temperature resistance.
3. Metals
A wide variety of metals and metal alloys, including stainless steel, titanium, gold, and silver, are used in additive manufacturing. This diversity allows making parts from the most complex jewelry to structural aerospace components.
4. Thermoplastics
The most common materials used in additive manufacturing are thermoplastics. Examples include but are not limited to, acrylonitrile butadiene styrene (ABS), polylactic acid (PLA), and polycarbonate (PC). It can also utilize water-soluble materials for the temporary support structure, polyvinyl alcohol (PVA) being one of them, which will dissolve after printing has been completed.
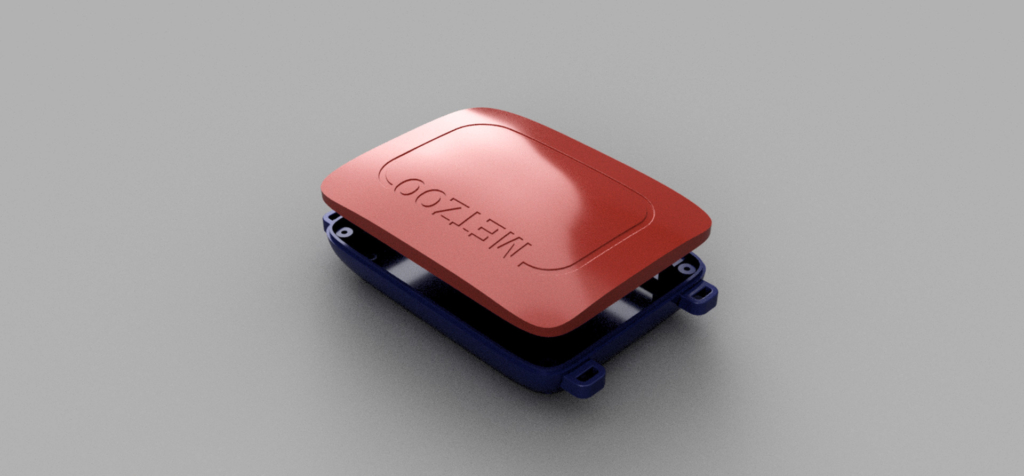
RELATED: A brief history of 3D printing
Applications of additive manufacturing
Additive manufacturing is increasingly applied in many areas: drafting and design firms can exploit its unique capabilities for a wide range of products such as:
1. Aerospace
Advantages of additive manufacturing in the aerospace industry include weight savings and the capability of producing complex geometries, such as blisks and bladed disks. The ability to generate lightweight yet powerful components contributes to higher fuel efficiency and aircraft performance.
2. Automotive
The significant benefit to the auto industry has been from rapid prototyping allied with the material flexibility of additive manufacturing: manufacturers can test designs rapidly while reducing weight and costs inherent in traditional production approaches.
3. Medical
AM changes the face of medicine because it allows for the production of customized implants and medical devices to address specific patient needs. Technology can now produce customized parts that enhance patient comfort as well as outcomes from dental implants to orthopedic devices.
Additive manufacturing for the future
Additive manufacturing is bound to experience rapid growth in the era of Industry 4.0. The demand globally for AM is going to surge high, thus reaching an essential figure of $76.16 billion by the end of 2030 in various sectors.
1. Prototyping and low-volume production
Among the biggest attractions of additive manufacturing is still the rapid prototype fabrication. Technology keeps improving, and more firms are increasingly using 3D printing for low-run volume production, thus enabling them to manufacture customized products at minimum costs that may be associated with traditional mass production. It is also easy to acquire 3D modeling services to help you speed things up in the pre-prototyping phase.
2. Sophistication and accessibility
As the technology of 3D printing advances, machines get more sophisticated and yet cost-effective. Accessibility to such AM by small businesses, even startups, allows businesses to tap the potential of AM for all manufacturing works, stimulating innovation and creativity in most industries.
3. Rapid production of new components
Turnaround time for new components or prototype parts is usually very fast in industries such as automotive and aerospace. Additive manufacturing facilitates a streamlined process that is geared to meet their needs better by allowing fast product development with quick market time.
4. Scalability
The other critical factor driving the adoption of additive manufacturing is scalability. The same technology can be used for a whole spectrum of products, ranging from tiny components to large structures, thus making it possible for companies to respond correctly to varied customer demands.
RELATED: Top applications of thermoplastic polyurethane (TPU) for 3D printing companies
Wrapping it up
Additive manufacturing revolutionizes the landscape of manufacturing and product development. Its capacity to create complex shapes, minimize waste, and offer customization has changed the approach toward design and production on the part of industries.
Because technology is very prolific and its applications in the field of AM are broadening day by day, it is promising to revolutionize manufacturing in the future with unmatched efficiency, innovation, and sustainability. Business enterprises that utilize the power of additive manufacturing will not only save time and costs but will also be able to develop excellent quality products to meet their evolving customers’ needs.
How Cad Crowd can help
Additive manufacturing- the future of CAD and 3D modeling services for engineering firms: on its way. Need a model for a new product? Or perhaps you’re just shopping around? Cad Crowd has worked with the best engineering firms to find the best fit for their projects quickly. Learn more about how to take advantage of our network with a free quote today.