Unless you have been hiding under a rock these past several years, you have probably heard the terms “3D modeling” and “3D rendering” thrown around. But why is this technology so important, especially for product manufacturing companies? In short, it reduces project times and costs. This gives manufacturers more room to experiment with designs. Companies that fail to utilize 3D modeling technology quickly fall behind the competition.
Over the years, consumers have grown more tech-savvy. As a result, they have become more demanding and selective in their product choices. Even the smallest mistake or confusion can turn off a potential customer and send them running to your competitors. That’s why manufacturing companies are starting to utilize 3D modeling to showcase their products. If you still aren’t convinced that 3D modeling can transform your business’s sales and marketing, read on for all the ways that 3D modeling has impacted companies.
Summary
There are a variety of advantages that 3D modeling brings to product manufacturing companies:
- 3D modeling allows you to create high-quality prototypes
- It is less expensive than traditional photography
- Displaying a model’s physical properties is easier and simpler than ever
- 3D rendered images can be used in a variety of marketing campaigns
- The 3D printing process is faster when using CAD designs rather than traditional 2D drawings
- The overall design process is more streamlined
- 3D modeling allows simple and efficient collaboration amongst team members
- Documentation is easier
As you can see here, the benefits that come from using 3D CAD modeling software are plentiful. Throughout the article, we will examine how these advantages ultimately help your bottom line.
1. 3D modeling is the perfect method for prototyping products
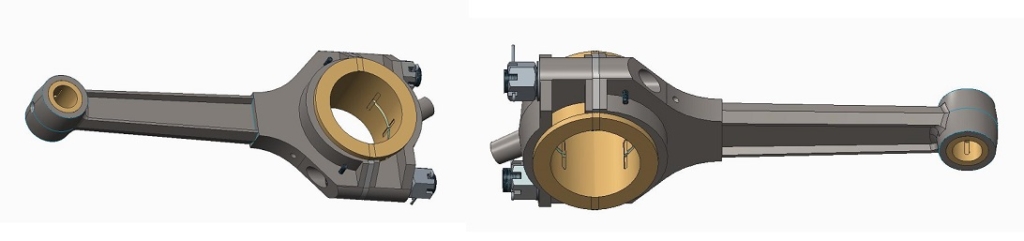
Designers can use 3D modeling technology to create photorealistic renditions of products. With their high-quality textures and strategic lighting, these images often turn out better than actual photographs taken by cameras. Viewers can examine every little detail of the model in high-quality resolution. 3D modeling design services often add lighting, texturing, and shadowing to enhance the realism of their digital renderings.
Everything from a light bouncing off a shiny surface to the soft texture of a chair is drawn precisely to enhance an image’s realism. It’s as if the viewers are looking at the object in real life. The only thing they can’t do is touch it. These images can then be placed anywhere from a print magazine to an online advertisement.
2. It’s easier on the budget than photography
While 3D modeling services can be pricey, they are still less expensive than hiring a professional photographer. After the long process of finding and hiring a photographer, you still have to schedule the photoshoot. Sometimes, you may even need to arrange for multiple shoots on different days, depending on the number of products that need to be captured. Once the photoshoots are scheduled, you will need to figure out how you will transport your products to and from the shoot. And when the photoshoot finally begins, it can take hours or even days to finish. Just typing all of this starts to feel exhausting.
3D artists, on the other hand, only need to be charged for the hours spent creating and rendering the product. There are no extra scheduling or transportation services required. Plus, most 3D CAD software comes equipped with over 700,000 standard templates for mechanical components. By using these existing templates, product design services save time while still creating accurate product renditions.
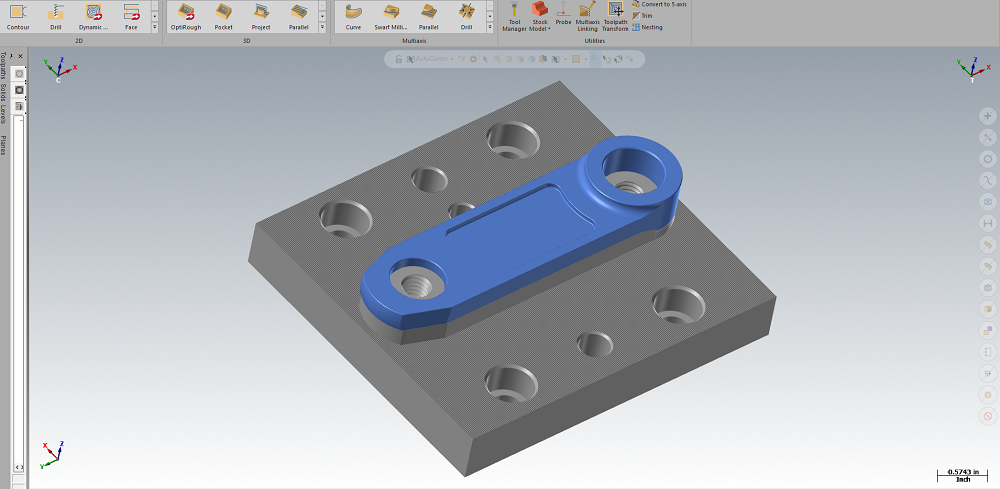
Some CG companies also offer free alterations up to a specific price point. This allows manufacturers to save money on any changes or corrections that need to be done on a model. Material rendering can also be applied to the 3D model to create a more accurate idea of how the end product will turn out. Anything from an aluminum finish to a metallic shine can be added to the model’s texture.
This makes it easier for sales and marketing personnel to give their input during the design process. Designers can continuously change the texture and color of the model until all team members are satisfied with the end product.
3. You can show off a product’s physical properties
3D modeling accurately depicts an object’s real-life proportions. This makes it easier for customers to compare the product to other objects in their households or to different versions of the same product. Within seconds, they can switch out different products within a virtual setting. If one object doesn’t fit, they can simply replace it with another. This method is, unsurprisingly, much easier than physically moving around bulky items oneself.
Some companies, such as IKEA, even have online programs where customers can set up their furniture within a sophisticated virtual setting. By trying out different furniture models within this virtual area, they have an easier time determining whether a particular product will fit well within their home, whether in size or in style.
4. 3D models provide multiple uses for marketing campaigns
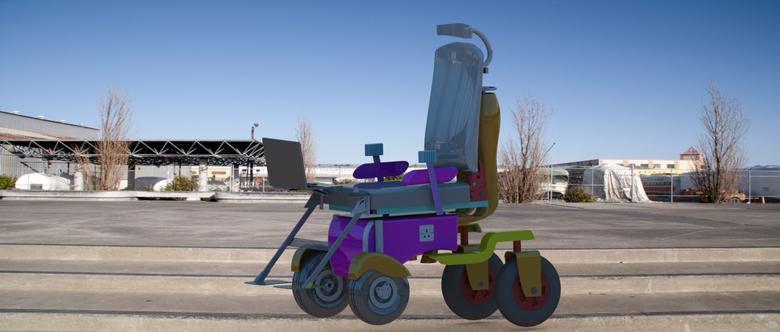
3D models can be used in a variety of different marketing materials. You can find them in everything from magazines to online ads and videos. Companies often use the same 3D model and place it in different mediums. The high-quality imagery that 3D CAD modeling creates looks good anywhere. Some businesses actually keep their 3D models inside a virtual library for future use. This allows marketing professionals to add existing products to new advertisements or even tweak their old models to make them more appealing to a different audience.
5. You can use 3D models rather than physical prototypes for advertisements
With 3D modeling technology, manufacturers can market products before they even create a physical product or prototype. By creating promotional materials early on, marketers can rest assured that their campaigns are started on time. If any changes occur to the product’s design, they can quickly change the images. The old method of waiting for the physical prototype to be made before launching a campaign was costly and inefficient. Plus, if there were problems with the prototype, the marketing campaign would be delayed until the manufacturers finished fixing it.
6. You can create animations showcasing your products
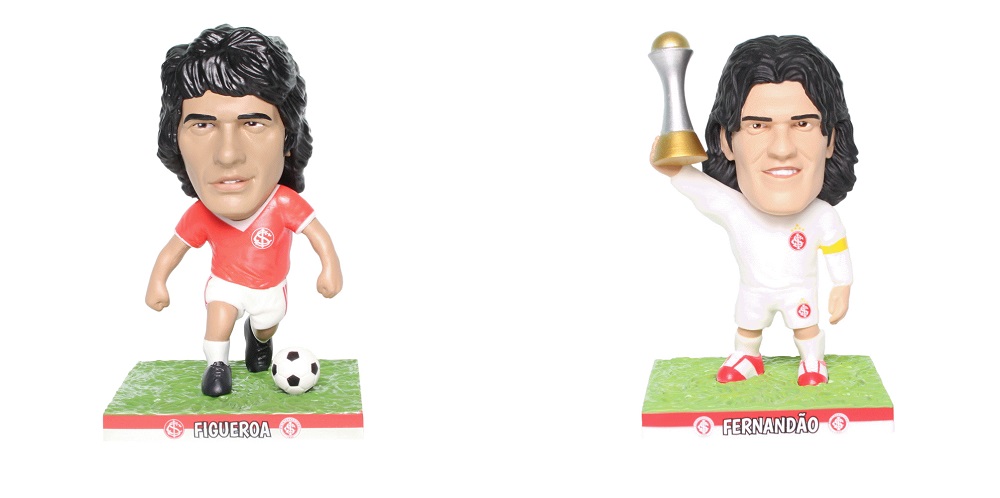
For people who want to go further, they can also create short 3D animations of the product being assembled and disassembled. Customers then have an easier time learning how to properly build and use their new product. Of course, you aren’t limited to creating assembly animations alone. Depending on the product, you can create animations displaying it in motion or demonstrating the various ways it can be used. The possibilities are endless. With a tool as helpful as this, customers are sure to come back to your company for future purchases.
7. Companies can present their products with 360-degree views
Single views are boring. They don’t show off all of the amazing components of a product. Customers don’t like any hidden surprises either. They usually want to see everything that a product has to offer. Manufacturers will often create 360-degree views of products so that customers can obtain a full understanding of all they have to offer. Packaging, color tones, and dimensions are all easier to examine from a 360-degree view. This method for engaging customers keeps them looking at a product for a longer time, which increases the chances of making a sale.
8. Designers can make quick changes to their renditions
Manufacturers can also make quick adjustments and variations to multiple products. With traditional techniques, designers have to manually redraw any incorrect or missing components. 3D CAD technology automatically redraws any missing or hidden parts of a design. Should you need to make changes to particular aspects of a design, the software will automatically redraw any connecting lines within it to prevent the chance of any errors.
They can even create different versions of an object. For instance, if a certain table comes in different lengths, the designer can adjust the structure without losing or compromising the original design. He or she can also try different color options and textures for the design. If something isn’t working, they can remove it and add something else.
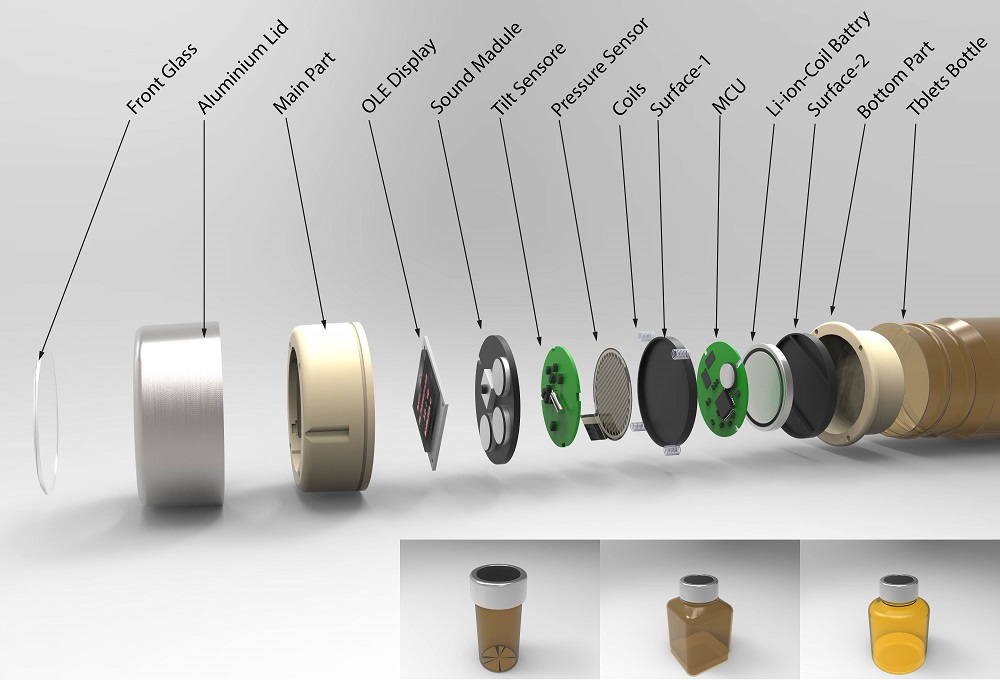
As the 3D modeling services edit or add new features, the object’s bill of materials is automatically kept up to date. This effectively decreases engineering costs. This feature is especially useful for projects involving the design of assemblies with multiple parts and fasteners.
9. It makes 3D printing faster and easier
Manufacturers can also obtain physical prototypes quicker with 3D printing than through traditional methods. Since they already have a 3D model, manufacturers can quickly convert it into a print-ready file. This allows manufacturers to inspect and evaluate them in a fast and efficient manner.
10. It allows for easy documentation
The traditional method for CAD design and drafting services involved the manual documentation of different aspects of the mechanical component being drawn. It was a tedious process that required high levels of accuracy and precision. Luckily, this method is starting to become a thing of the past. 3D CAD software is preloaded with flexible documentation options, such as product dimensions and material specifications, for designers to use at their disposal. As a result, the documentation process is faster and simpler.
11. Communication among team members is easier
By using a 3D representation of a product as a reference point, team members have an easier time communicating with each other. Sometimes non-engineering personnel, such as product marketers or even customers, are needed to give input into a product’s concept and features. But with traditional 2D drawings, it can be difficult for non-technical personnel to properly visualize the end product drafted on paper. With a virtual 3D model, they have a much easier time visualizing and adding their critiques to designs.
12. The design’s integrity can be preserved during edits and changes
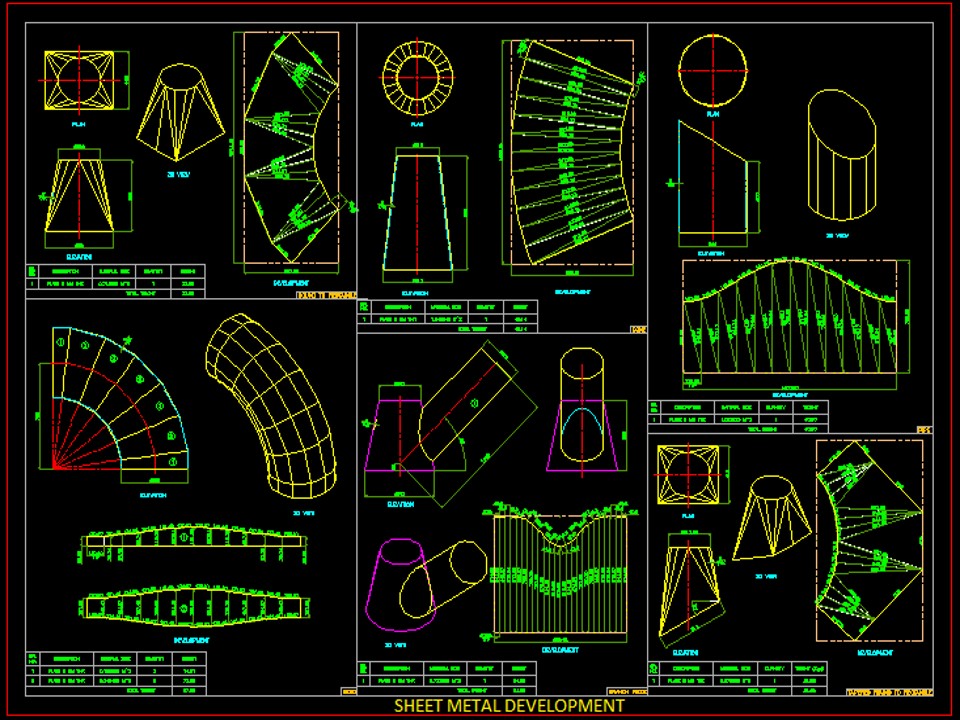
By keeping a product’s geometric measurements within your design software’s algorithm, this will automatically prevent certain features from being accidentally modified. For instance, if two holes must be 2” apart at all times, then 3D modeling software will ensure that the product can be redesigned over and over again without breaking this rule. As a result, the integrity of the component is preserved throughout the entire design process.
13. You can test your product under various stressors
By gathering an object’s surface geometry and material data, designers can predict how it will react to thermal, impact, fluid flow, and other physical stresses. They can also slice a cross-section into the object to view the complex components that make up its interior. Imagine being able to test a building’s ability to withstand a Category 3 hurricane. Or seeing how well a car can fare against a snowstorm. Both of these things can be done through the click of a button. Testing a product’s strength through virtual means is much cheaper and safer than doing so physically.
Combining 3D modeling and CAD
CAD software has been around since the early 1980s. Since then, it has become the standard tool for drafting and designing mechanical parts and assemblies. For a quicker, more cost-effective approach to manufacturing products, companies are starting to combine 3D modeling and CAD design services. Some companies even outsource their 3D CAD modeling in order to focus more on their product manufacturing.
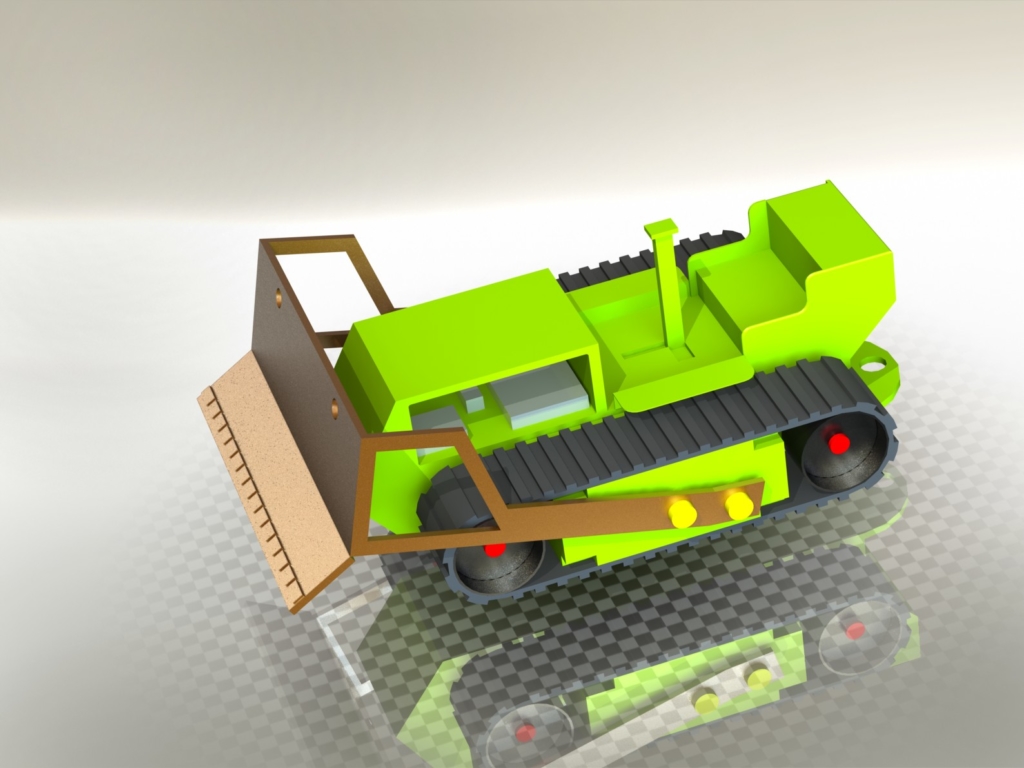
With CAD software, companies go through their concept to prototype phases in no time at all. Thanks to the software’s flexible product design feature, engineers can make changes to a component’s design without negatively affecting other parts of the assembly. This saves the company both time and money by helping them avoid costly mistakes with the designs. The technology also allows engineers to visualize complex technical elements that would be difficult to view in a traditional two-dimensional form. But exactly what part does CAD design play in the overall process?
How designers use CAD in their design process
Because consumer needs are continually changing, manufacturers need a method for successfully keeping up with them. Nowadays, product life cycles are growing shorter while the demand for new models and customizations increases. That is why designers rely on computer-aided design (CAD) to create photorealistic 3D models. It can be used throughout the engineering process, from the initial conceptual design to the full product layout. Designers also rely on CAD to analyze assemblies and determine manufacturing methods for different products.
By utilizing 3D CAD modeling, most of the guesswork involving complex geometries and assembly interference that results in scrapped component designs are taken out. Companies who are ahead of the game are starting to use concurrent engineering too. This involves engineering and manufacturing a product from shared 3D CAD data. Rather than continually creating physical prototypes until the product engineering is determined to be correct, manufacturers can use 3D CAD models to test as virtual prototypes.
Types of 3D models
Designers typically use 3D CAD models as virtual prototypes to eliminate time that would have been spent attempting to edit and change physical prototypes. Below are three types of 3D models that are often utilized for this task.
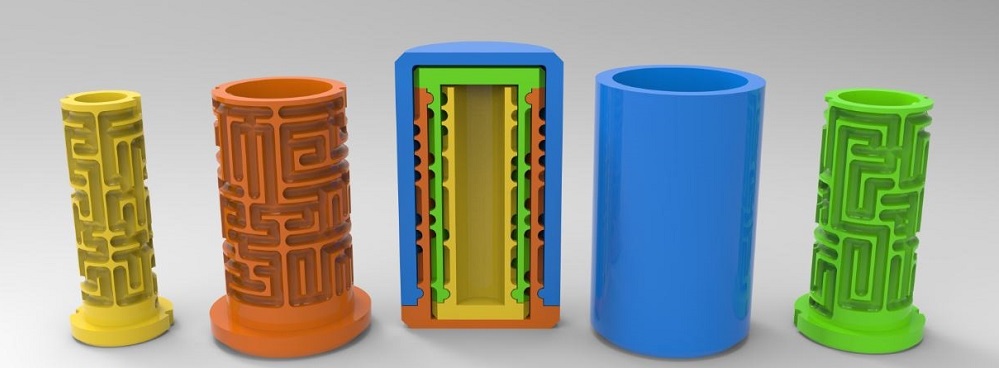
3D wireframes: A 3D wireframe model is a skeletal representation of a real-world object. Different curves, points, and lines are assembled together to define the object’s edges. 3D wireframes are typically used to make the final engineering drawings of a product. While they aren’t used often nowadays, they are sometimes utilized for many of the same things that 2D CAD systems are employed for.
3D “dumb” solids: A 3D “dumb” solid is a three-dimensional geometric form, such as a cylinder or prism, that is manipulated via a computer program. Designers can add or subtract volumes from them in the same way that someone would assemble or cut a real-world object. This technique makes it easier for designers to create two-dimensional views of their models. Manipulating a 3D “dumb” solid is much easier than physically cutting an actual object. However, most 3D solid programs are limited in their range of motion.
3D parametric solid modeling: This type of modeling requires operators to use “design intent.” This term refers to the ability of a designer to consider the object’s purpose when creating the model. By using design intent, the modeler must take the relationship between product features and the various parts that allow them to come to fruition into account. He or she must carefully consider the consequences of their actions. If a feature needs to be located in the center of a part, then the CAD technician needs to place it in the model’s center just as it will come out in real life. If they move a feature by even a fraction of an inch, this could negatively affect the other features of that object.
The product design process
The product design process is typically composed of three distinct stages:
- Conceptualization
- Prototyping
- The Production of the End Product
Let’s explore each stage closely.
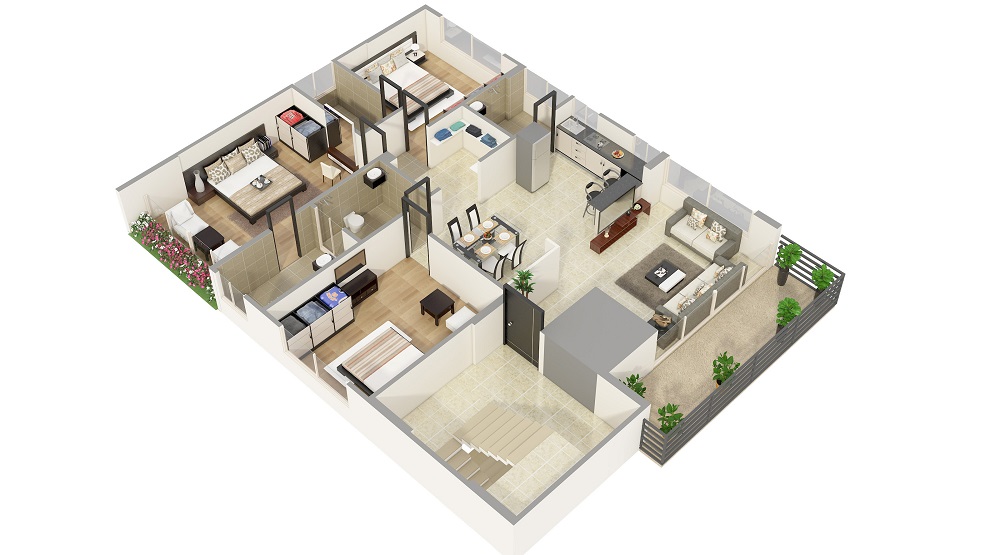
Step 1: Conceptualization
A CAD freelancer typically starts the design process by analyzing their client’s product concept. They also focus on the client’s goals, budget, and production schedule when drafting their initial ideas. The designer will also conduct in-depth market research to learn more about the client’s position among its competitors. They will then draft 2D concept renderings of their design to help them create detailed 3D models of the product and, if necessary, a 3D printed conceptual prototype.
Step 2: Prototyping
After the concept designs are approved by the client, the prototype design engineer will pick out preliminary manufacturing technologies and materials to use for developing the product. To improve efficiency and reduce costs, they will also outline an optimized manufacturing process for the client to follow. During this stage, they will start creating semi-functional prototypes to test and refine their design.
Step 3: The end product
For the final stage of development, the designer will create fully functional prototypes and 3D models for the client to evaluate. Designers will also gather vendors for any hardware or other off-the-shelf parts needed to build the actual product. Once the product design process is complete, the client will begin the manufacturing process.
Case study: SolidWorks world 2018 showcase
SolidWorks is a community filled with millions of talented, award-winning CAD designers. Users share their knowledge with each other every day in order to improve CAD software and to help make the world a better place. At SOLIDWORKS World 2018, designers, engineers, entrepreneurs, and business leaders unite to collaborate and innovate with each other. The power of design and fabrication, a cornerstone to the company’s motto, is showcased at this world expo every year.
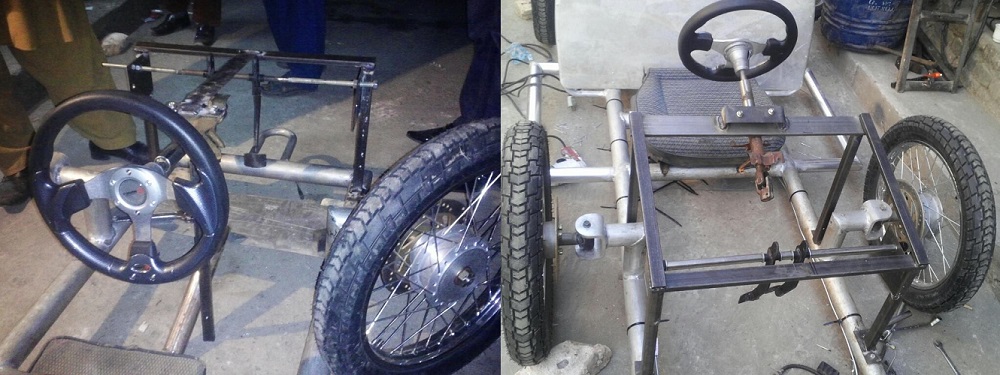
Each year, the expo introduces new tools to machinists and manufacturers to ensure they have accurate production parts for their projects. In one of its product showcases, SOLIDWORKS setup a mini machine shop that created shifter arms for a vehicle. A shifter arm, also known as a gear lever or gear shift, is used to change gears in a vehicle. The showcase highlighted the ways in which a designer can use SOLIDWORKS CAM to take their part from the mill all the way to inspection and engraving.
How the process starts
The engineer begins by creating a 3D model of the shifter arm. Included within this model are all the features, tolerances, and product information needed to send it out to various milling processes. Detail is essential for this step. The more detailed an engineer is with the model, the easier it will be for them to produce it.
Zone 1: 2D Cutting
Before they can begin milling, the engineer must cut out the model’s 2D profile. He or she will need to use the OMAX protoMAX waterjet cutter to cut out the profile on the arm component of the shifter arm assembly. Once the part is programmed, the engineer can send it to the mill and remove the piece from the blank metal.
Zone 2: 3+2 Milling
The engineer then mills the arm component of the shifter arm assembly with the Haas UMC 750. By programming the part into the UMC 750, they will be able to begin the milling process. To make the machining process easy and smooth, the mill uses water to shave off the metal. Once the milling is finished, the part is ready to be inspected.
Zone 3: Turning
In the turning zone, the engineer uses the Haas ST20 to create the knob component of the shifter arm. Like the UMC 750, the process starts with a piece of round stock that is cut to a specific length. After the part is programmed into the ST20, the engineer can begin to create the knob. The ST20 mills the entire knob and leaves only the engraving step untouched for a step further down the production line.
Zone 4: Inspection
Once all the parts are finished with their machining processes, they need to be inspected. The SOLIDWORKS Inspection and Origin Checkmate software both are used to verify the parts. The inspection equipment is programmed to check tolerances, clearances, fits, and the overall build of the part. Inspectors must measure the manufactured components and compare them to the original SOLIDWORKS model.
Zone 5: Engraving
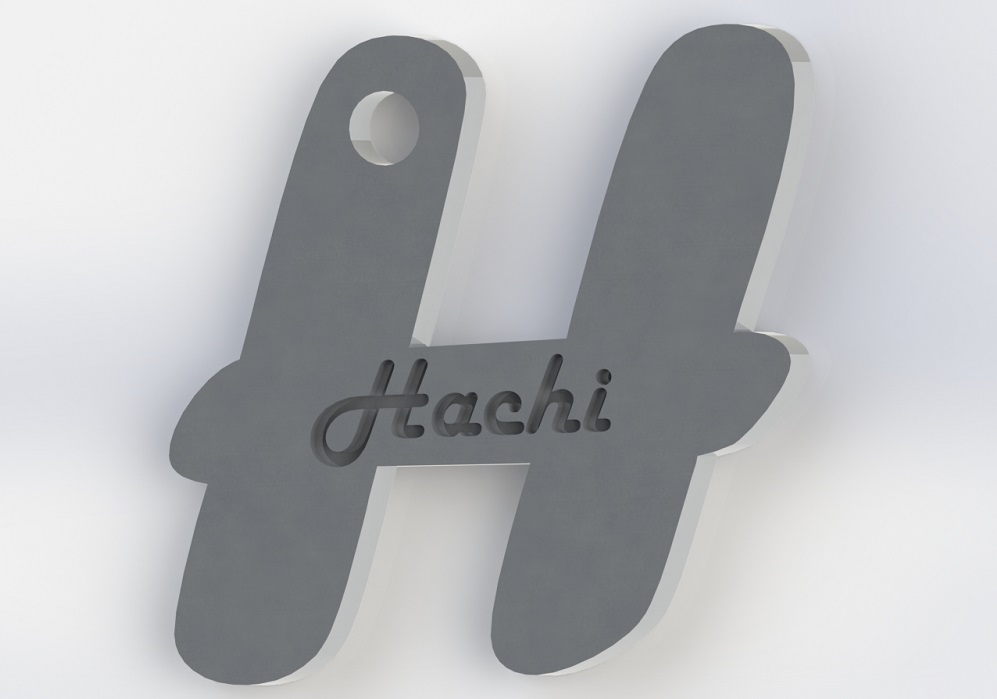
During this last step, the knob of the shifter arm, which was milled in zone 3, is engraved using the Tormach 440. After it is engraved, the knob will be ready for quality inspection and final assembly.
The Finished product
After it passes the quality inspection, the shifter arm is ready to ship. Thanks to the SOLIDWORKS CAM and Inspection software, translating the computer design model into the machining process is fast and easy. This showcase is just one example of how SOLIDWORKS empowers its users by providing a straightforward process for creating their designs.
How Cad Crowd can help you
If your company needs a boost in its marketing strategy or is struggling with its manufacturing process, 3D modeling may be the solution to your problems. Customers want high-quality images, fast service, and reliable information in one cohesive package. All of this and more can be provided by 3D modeling and CAD services.
But searching and finding the right designer for your company can be challenging. It is a long process that takes a significant amount of time and energy from you. That’s where Cad Crowd comes in. Cad Crowd connects companies with top-rated designers that are pre-screened and vetted by their own team. Through this rigorous process, they will match you with the top 1% of design talent for your project.
If you require confidential 3D modeling services for a private project, Cad Crowd can work with you. After you send the team your project brief, they will provide a private quote from a pre-qualified designer for your project. Cad Crowd also hosts design contests for companies interested in choosing from multiple design concepts. Contests are perfect for smaller projects, and often garner dozens of entries.
Whether your company needs a CAD designer, 3D modeler, or industrial designer, Cad Crowd will match you with a top-tier freelancer. Ready to hire your next freelance CAD designer? Contact us now to get a quote or start your own design contest today.